“Even though the plant is 70 years old, we use the latest technology, state-of-the-art machines and equipment for various production operations. We have benchmarked the world’s best standards in manufacturing and are now on par with them. The average experience of employees is 25 years, and we have been able to produce a wide range of vehicles through their experience, knowledge and skill levels,” affirms Mr. K.V. Natarajan, Plant Head – Ennore, Ashok Leyland Ltd. (AL).
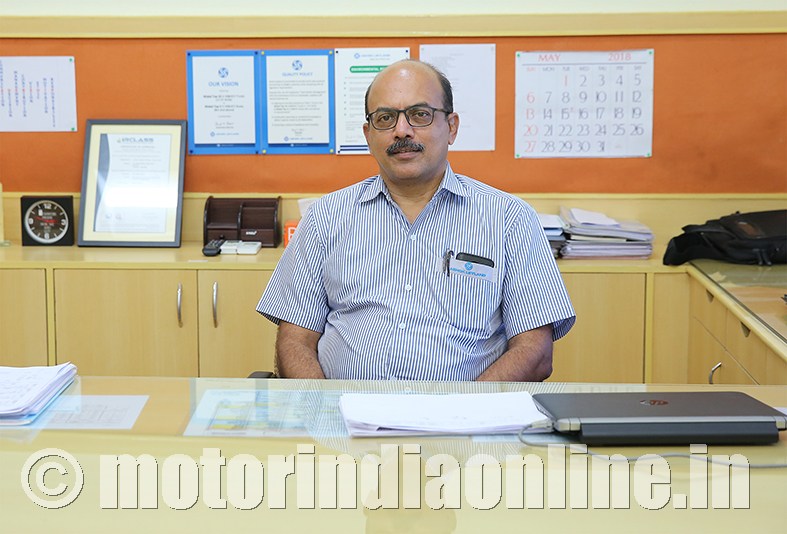
Excerpts:
The Ennore plant has been the starting point for AL’s exciting 70 years CV journey and the key unit continuing to play an important role. In this regard, can you brief us the important milestones crossed?
One of the main turning points has been the Hinduja Group taking over AL, and there have been several others too. Manufacturing tie-ups with Hino Motors of Japan for engines, Iveco of Italy for vehicles and engines, getting self-certification for Defence engines and vehicles and supply of about 70,000 vehicles to the Indian Army are some other important milestones.
We have been constantly upgrading technology and changing the face of the plant to take on competition.
In such cases where quality is of prime importance, we have removed the human element through robots and machines, and inspections carried out by machines for the benefit of the customer. We had partnered with Hino Motors 10 years for engines manufacturing and the same renamed as H-series have been upgraded to meet the BS-IV emission norms. On the technology front vis-à-vis mistake proofing and assembly, we are on par with the Japanese and European manufacturers.
We have an assembly line flexible to take up an ICV, bus or a truck and produce 120 vehicles per day, apart from the daily production of 220 engines H-series in a different assembly line to meet the domestic, Defence and export requirements.
Give us an overview of the operations, flexibility to ramp up production and methodology to address the critical activities in the assembly line.
We have 2200 associates (reference to workers in AL) and 800 executives at this location. The Ennore plant manufactures all the engines for captive requirement as well as the Power solutions group of AL. Besides the H-series engines, we have started producing the Neptune series engines, about 20 per day, and will gradually scale it up to 40 per day – the same in the nascent stage.
The comprehensive assembly line having many production stages/stations has a takt time (average stage time between the start of production activity in one unit and the start of the next unit) of 6.8 min per vehicle, and it’s the lowest amongst all the AL plants. This means more vehicles are manufactured on the conveyor line, and similarly the engines line has a takt time of 3.8 min per engine.
As regards the critical activities of assembly line, we provide additional equipment to keep the takt time under control. For example, in the wheel nut runner tightening torque stage, instead of one we give two of that equipment on the same side of the conveyor. Similarly, time controlling is done at the turnaround crane station.
First, the chassis assembly operations are done in the upside down position. Then it’s turned around for the next operation, and the time for it is dependent on the weight and length of the chassis. By adjusting the motor control and turning speed for various models, the turnaround time is achieved to meet the 6.8 min takt time.
To scale up production on the conveyor, we are looking at reducing the takt time to 6.3 min. To achieve the same we need to cut the activities into smaller elements and give it to the associates. There are two options in doing it, viz., increase the associates or machines. Also wherever we feel the activities can be done outside instead on the conveyor line, the same will also be considered.
Comment on the approach towards automation and the manufacturing practices at AL vis-à-vis that worldwide in similar industries.
We do not take up automation blindly for the sake of automation. In places where quality cannot be compromised, very strenuous labour content is there, safety or health hazard risks are high and hot working conditions prevalent, automation is considered. We want our associates to be involved with value-added production activities.
For example, in the axle beam machining where quality is prime, we have introduced machines in conjunction with robots; and with three machines and eight associates able to finish the same work output accomplished earlier through about thrice the above number of machines and associates. Herein the kingpin bore operations are done.
This involves face milling, drilling, boring, tapping, etc., the component checked for accuracy and specs conformity and comes out only after it passes the same. The axle beam of the front axle is a critical part that takes about 30% of the vehicle load and hence demands accuracy of the highest order.
As for the technology comparisons I would like to cite two areas, viz., engine assembly & machining and chassis assembly. In the engine machining area, we use state-of-the-art machines. During machining, the size is being checked and only if OK the part comes out.
Similarly, in the engine assembly area, after every stage, there is mistake proofing activity. For example where torquing is done, it’s automatically recorded in the computer system, and if the requisite torque has not been applied, the conveyor stops and the engines don’t move to the next stage. Similarly, in the chassis assembly line, if necessary torquing is not done, the conveyor line stops for the necessary remedial action.
Can you share with us details of the supply chain management and process control planning to meet the production of varied vehicles in the assembly line?
We follow the typical just-in-time approach to get the parts delivered to the assembly line. We do not hold inside the plant the bulky parts in the ‘A’ category that need to come only every 4 hours. We give the login ID to our suppliers, and they can see the production plans and supply parts every 4 hours on a sequential basis.
We have vendor managed inventory here and in nearby locations for the timely supplies. To ensure the quality, we certify the vendor and our team will be at their works to monitor the same. We rank the suppliers, educate and train them to meet our requirements.
When we design the process, we benchmark the best in the industry, viz., in which way it can be done the best and decide on the customer requirements, variety of products going on the conveyor line and then take the best decision. We have a separate department for doing it, and they work on the details to balance the activities.
What has been AL’s approach towards introducing new products for production, quality control measures and standards?
New products are designed in our R&D at VVC. They come here with a new vehicle model, and we do it on the assembly line to decide the operations and activities at the various stages. After the same, we sign off the model for bulk production and align the equipment and activities stage-wise for commencing commercial production.
The first batch of a few vehicles are done at this plant and later taken up at other plants for the eventual scaling up to attain the target.
As regards QC, wherever quality is critical, we have done mistake-proofing at all those locations. This means quality is ensured at that stage, and if not that part will not move for the next operation. We also have online process capability checks. For instance, the process capability quality index is checked as and when we produce parts.
The concerned executive/manager gets an SMS on his mobile about the quality index for monitoring and implementing corrective actions. We also invite everyday, about 25 customers, inside the plant to go around all areas. They pose questions and get convinced about the quality aspects. We take their feedback and depute our associates to customer fronts to understand their pain points.
This enables them to come back and discuss the issues with their colleagues for taking corrective actions. We have been continuously upgrading ourselves to the best of the worldwide quality systems. We have the ISO/TS 16949 and are now moving towards winning the Deming Award for all our operations.