“As the R&D of a CV manufacturer, we have all the solutions, and once the market is there, we are ready. We need the business heads to tell us which market requires what and the solutions to most of the same are available either as a prototype or at a mature level,” reveals Dr. Seshu Bhagavathula, Chief Technology Officer, Ashok Leyland (AL) Technical Centre.
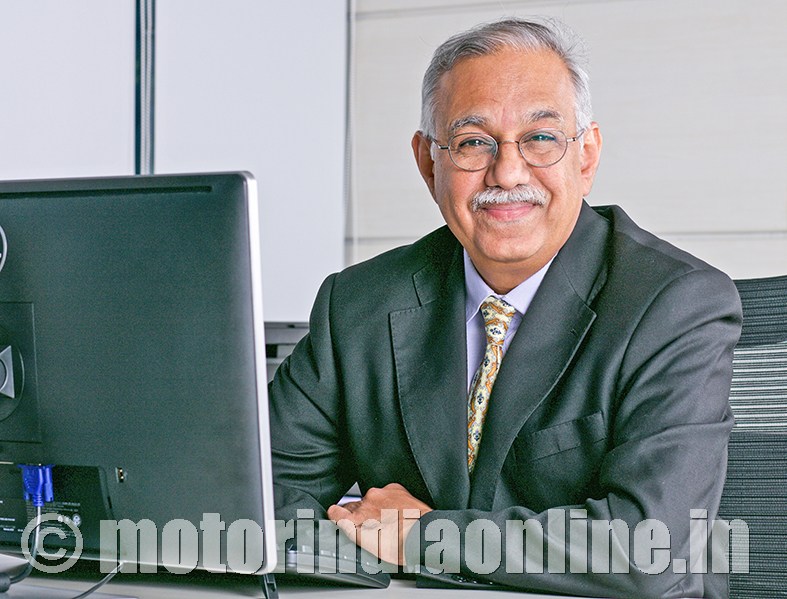
Excerpts:
Kindly reflect on the crucial role played by technology in the 70-year journey of AL, and your operational set-up to support the company operations.
The 70 years in CV space and development of the country during that period are invariably intertwined, and one can readily relate the role played by the CV manufacturer AL in the developments. Take the typical examples of the first double-decker in India for the transport sector or the AL trucks carrying cement for the first bridge constructed in Assam.
In all the projects and infrastructure works, the contribution of AL directly or indirectly can be easily deciphored. During the initial period, technology came from others, and after AL became an Indian company, we had to build resources and develop R&D here. Starting initially with a few hundred people, today we have about 1,800 engineers working on various aspects of product development and advanced engineering assignments.
This campus is spread over an area of 180 acres, with test tracks and work centres located amidst greenery and environment-friendly ambience.
Though AL briefly forayed at some points of time into other mobility solutions, it realized its core competence in trucks and buses and started focussing on it. Buses are invariably younger brothers of trucks in the sense that they are always built on a chassis; and truck and bus manufacturing invariably go together and rarely does one come across a standalone bus company.
AL is the only CV manufacturer having their own engine brand covering the range from 60 to 380 hp. This gives us the advantage of fine-tuning the marriage between the engine and truck and providing higher/lower torque for an application demanding a certain hp. We have chief engineers to take care of bus, MCV and high-end trucks, supported by heads of aggregates like the engine, driveline, suspension, gearbox, etc.
The group is involved for 60% of the time in advanced engineering assignments. For example, consider the push axle where we believe the market will be there because we see a space there. If the same gets approved, it is taken up for further processing. Almost 40% of the time on projects we work on are triggered by business unit inputs.
Tell us about the technology inputs, impact and product development cycle, and the current and future projects to address the imminent disruptions ahead.
Aggregates team members are always meeting the worldwide top suppliers and keep looking at their roadmaps. The suppliers play a key role and we have a fantastic ecosystem with them. They are not only the suppliers for the local but also global markets and their observations give us an indication where technology is heading.
We also attend international conferences that give us lot of data, and work with the universities on new ideas. All of above drive the aggregates members towards new development work and the operations are coordinated at the CTO level.
Apart from support to trucks and buses, the Tech centre also supports Defence & Power solutions divisions. Tech support is also provided for sister companies, Optare, Albonair and Hinduja Tech, based on their needs.
After the BS-IV launch, 1,400 engineers involved with it started working on the BS-VI, so critical a legislation. Taking into account the suppliers working on the project along with our team, about 12,000 man-years are going to be spent for BS-VI vehicles coming out of this campus, and this should amply illustrate the magnitude of development efforts needed.
Any product development cycle comprises of prototype, pre-series and series stages and vis-à-vis BS-VI, we are currently in the middle of the pre-series stage. This involves testing the first batch of vehicles to varied site conditions. Series stage means vehicle testing is over and ready for assembly and other related operations.
We are also spending lot of time on EVs, driver assist systems and AI, data acquisition & algorithms for reliability predictions.
Comment on the various technologies, systems and products positioned for performance and safety aspects, as well as the trends in the chassis and driveline systems.
ABS and telematics are already present. Driver assist systems will become a reality in the near future. Over 70% of the accidents happen on the frontal and side sections, especially while taking turns. If we can have the systems in place to warn the driver to take corrective measures, it will mean a lot in saving precious lives and associated other losses.
This is our priority focus area, viz., to develop the assist system for market introduction. However, we need legislation in this regard to make it a reality. The ESC (Electronic stability control) will take some more time, the reason being the prevailing legislation on overloading. The trucks come with proper balancing and there are lesser chances of overloading the truck and shifting the CG of the loaded truck to cause stability issues.
However, at the R&D level we already have the prototype solution for the issue. With BS-VI shift, AMT will become a default offering in trucks, the reason being incorrect manual gear shifting significantly affects the fuel efficiency and performance. With the electric engine, AMT will take over the finer issues of shifting gears.
Airbags solution is readily available at our end and we have already done the crash tests with these safety features. However, the market is not ready and we will enter it when the same is mandated. I see big changes happening in the braking systems, especially in the high-end vehicles. Reducing the braking distance means significant reduction in the number of accidents.
Chassis will become lighter with new materials, and load carrying capacities increase leading to enhanced performance and better fuel efficiency.
Noting that diesel power has fallen out of favour, share your observations vis-à-vis hybrid technology and the increasingly popular electric route for mobility solutions.
I would consider hybrids as the logical step to address environmental issues before the move to fully depending on electric vehicles. This is the trend in Europe, and I feel that the Government has also realized this and is re-examining the proposed shift to fully electric vehicles by 2030. Pollution is a serious issue in urban areas and not on the rural side.
With BS-VI, trucks can operate with diesel/CNG on the rural front/highways, have geofencing to switch over to electric in urban areas. Battery cannot give you the 300 km range with a 20-30 ton payload, and hybrid is the only answer till the electric route meets such long range demands. There are issues with lithium-ion batteries regarding size reduction, and it’s impossible beyond a certain point.
New battery systems are evolving, and I see solid-state battery becoming a reality in future.
What is the impact of technology disruption and the direction in which the CV domain is likely to shape up in future?
Intra-city buses and LCV trucks will move over to electric first to meet the pollution issues in urban centres. We have already got an order from Ahmedabad to operate electric buses as turnkey services project. We are also looking at various business models right from total service package to sale of bus and leasing of batteries and combinations thereof and solutions vis-à-vis swapping and charging methodologies.
As regards fuel cell (FC) as an alternative to plug-in electric battery, it definitely has a future. It is compact and gives wider range. Beyond 200 km with about 30 ton, FC is the answer and a combination of battery and will exist to meet the demand. FC is ideal for constant torque and battery for varying torques.
Hence you will see FC powering the battery and battery powering the vehicle, a hybridization of a different class in force.
Autonomous driving will not happen in the near future, but platooning is a real possibility. In mining and other restricted hazardous areas pollution problems are acute. The vehicle traverse paths however are well defined, and in such cases the first truck and driver can act as GPS for the following, say, 4 or 5 trucks in the platoon formation.