In the Spotlight – Basil Mohamed Siddeeqi, Managing Director and M H Zakkir Hussain, CEO, Alkraft
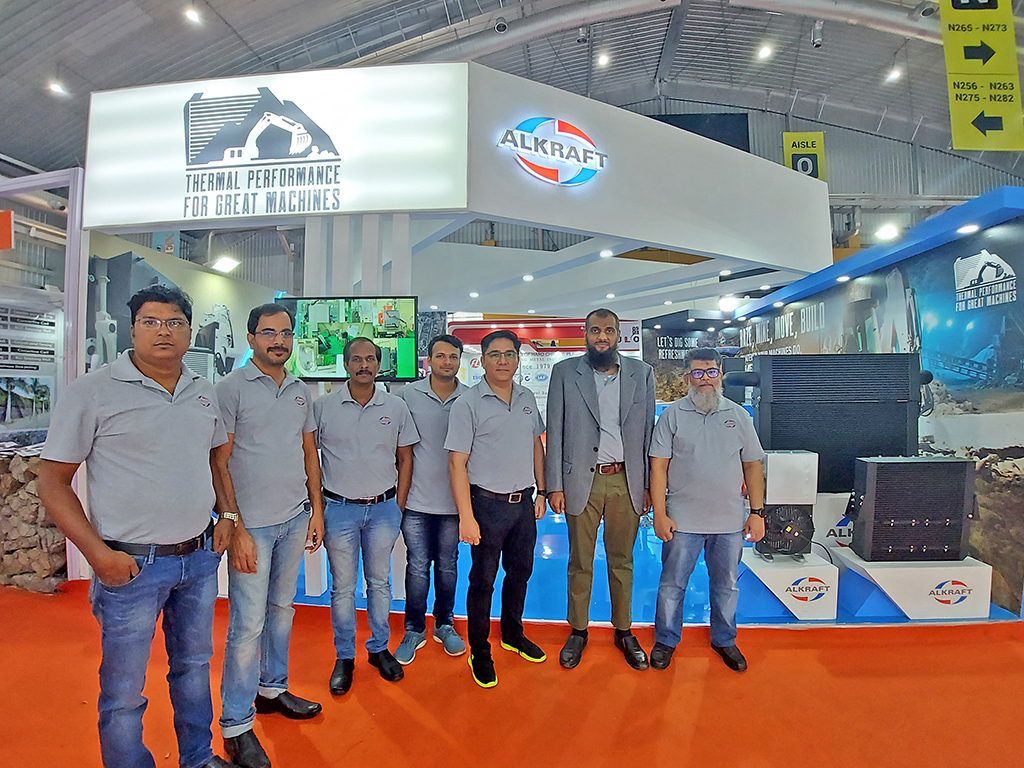
Rajesh Rajgor spoke to Basil Mohamed Siddeeqi, Managing Director, and M H Zakkir Hussain, CEO to understand their innovative and robust solutions for construction equipment and off-highway industries, and the expertise they offer in the space of thermal management
EXCON 2022 Special
Alkraft showcased a number of cutting-edge thermal management systems at the recent Excon in Bengaluru. New generation radiators, transmission oil and hydraulic oil coolers, and an oil cooler for vacuum pumps with a uniquely shaped seamless L-shaped core were among the heat transfer systems on display at Alkraft’s pavilion for construction equipment. The exhibits were visited by a number of dignitaries and VIPs from Indian and international OEMs. Industry veterans welcomed the new products on display, as well as Alkraft’s product strategy, which is centred on technological leadership.
During our conversation, it became evident that Alkraft’s construction equipment heat exchangers were designed from the ground-up to endure and even thrive in the extreme operating environments seen on construction and mining sites, where heavy dust and high vibration levels are commonplace. “To achieve superior thermal performance with lower pressure drop, we use proprietary fin and tube geometries in our radiators, charge air coolers, oil coolers, and cooling system modules,” Siddeeqi explains. The best-in-class performance-to-weight ratio of Alkraft’s heat exchanger cores are due to the design and process advances that enable remarkable thermal performance and durability without over-engineering the product”.
Alkraft heat exchangers are available in a variety of configurations including tube and fin, bar and plate, and drawn cup. This provides optimal versatility and performance in a variety of applications. “High-performance fin designs prevent clogging even in applications like truck-mounted concrete mixers and earthmoving equipment, making our products compact and lighter.” MH Zakkir Hussain, CEO of Alkraft, says, “Our heat transfer solutions stand out in the construction and mining equipment sector because of their ability to achieve optimal performance in high vibration and high dust scenarios while maintaining industry-leading reliability and lifespan.”
Advantage Alkraft
Construction and mining equipment applications require an increasing number of heat exchangers as they get more complex. In order to ensure that all of the heat exchangers perform individually and as a complete module, it is critical to design, test and simulate their performance as a system under various operating environments. “Apart from empirical designs, we genuinely model the actual performance of the product using computational tools,” Hussain explains. The thermal performance of the entire system can be clearly evaluated using design simulation. Prototyping and validation are the next steps. Our CAE & CFD analysis scenarios closely mirror the conditions under which the equipment will operate as we have optimized our systems to better emulate real-world conditions.”
Such detailed testing enables Alkraft to experiment and design for optimal material combinations for a particular environment and application. It is worthwhile noting that Alkraft pioneered the introduction of aluminium in automotive heat exchangers in India while copper brass was the widely used standard. “Some copper brass systems are still used in very demanding environments and we are now working with customers to convert them to aluminium. We have new materials in the form of ‘super long-life’ alloys that can work as an alternative to copper in terms of quality as well as price,” shares Basil Siddeeqi.
Alkraft works closely with customer development teams right from the beginning of the design process. “Some customers are unsure about a number of factors that can affect the final result. On paper, it’s impossible to get a perfect set of specifications. As a result, customers rely on professionals to assist them in producing precise product specification sheets. It can involve a variety of criteria such as replacing copper with aluminium, using the proper coolant management with water, coolant mixture ratios, and so on,” Hussain explains.
Says Hussain, “Being a system supply partner to global defence and armoured vehicle OEMs, Alkraft has in-house expertise in designing and manufacturing for extreme stress applications with very high reliability and durability. The requirement from the heat transfer system, both in terms of thermal performance and reliability, in defence applications are greater than any other given the extreme weather and terrain conditions involved. The expertise of designing for those conditions, design capabilities for conformance with BSVI emission norms, and three decades of auto industry pedigree of efficiency and operational excellence makes Alkraft the ideal partner for construction and industrial equipment OEMs. Because our products are exposed to difficult terrains and weather conditions in the defence sector, we see it as a training ground for construction equipment, CVs, and off-highway vehicles, similar to how Formula One is a testing ground for passenger cars. We do unique things there, and the learning is carried over to other areas”.
Putting Customers’ Interest First
While custom design and build of heat transfer systems is Alkraft’s core competence, Siddeeqi says the company has noticed an increase in demand for standardised products as well, the advantage being lower lead times and lower development costs. “In high-volume businesses like trucks, using the modular platform for commercial vehicles, OEMs see the importance of standardisation to achieve economies of scale,” he explains. “Although standardisation is less of a concept in construction equipment, we have had some customers asking for systems based on our standard product platforms too. We work according to our customers’ priorities, and hence we do both standardised and custom designs”.
“When we are able to customise, we have the option to bring some distinctiveness, but we must balance the technological aspects with the business needs. Our continuous brazing method enables us to meet both high and low volume requirements while maintaining quality standards,” he adds.
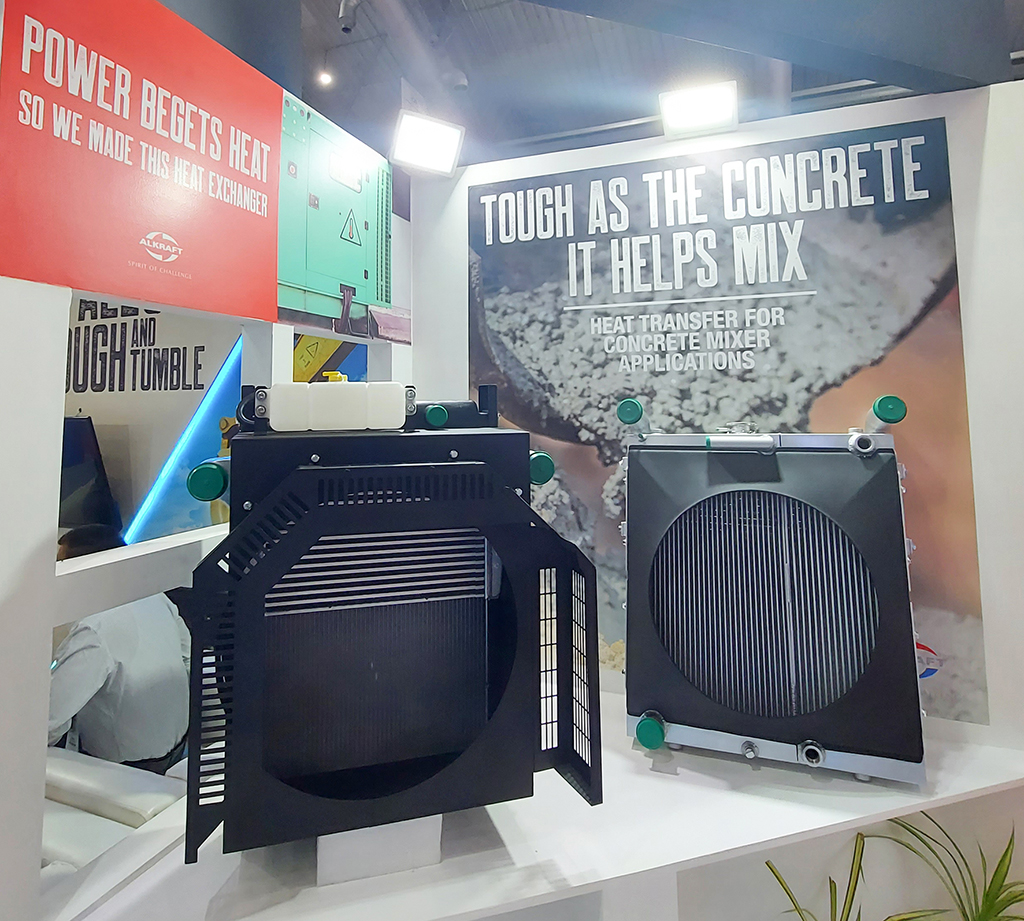
Zakkir Hussain adds that product lifespan is tied to proper service and maintenance of related parts. Alkraft advises operators and end users on when periodic cleaning is required, when a component must be changed, and so on. “Connecting hoses, rubber, and other exposed materials have a lifespan,” he explains. “Deterioration in mountings can also cause vibration levels to fluctuate. This has an impact on the product’s lifespan. For proper material servicing, we require customers to follow the directions in our repair and maintenance handbook. The heat exchangers interact nicely with the connected systems if they are in good working order.”
He signs off with the point that Alkraft has always been at the forefront helping the industry address its most complex challenges, whether they involve more power and performance, more stringent emission and fuel efficiency regulations, or product weight and life expectations. Alkraft’s growth from a small research and development unit that designed and developed India’s first aluminium heat exchanger to a well-integrated system supply partner for the automotive, industrial, power generation, agri-equipment, and defence product industries, demonstrates its innovative spirit and core engineering strength. These are the tenets that the company, its customers, and the industry as a whole value the most.