ANSYS, Inc. is an engineering simulation software (computer-aided engineering, or CAE) developer headquartered south of Pittsburgh in the Southpointe business park in Cecil Township, Pennsylvania. ANSYS was listed on the NASDAQ stock exchange in 1996. In late 2011, it received the highest possible score on its SmartSelect Composite Ratings according to Investor’s Business Daily.
The organization reinvests more than 15 per cent of its revenues each year into research to continually refine the software. Some of its solutions under Simulation Technology comprise in the areas of Structural Mechanics, Fluid Dynamics, Electromagnetics and Multiphysics. It also offers solutions in the form of ANSYS Workbench Platform, High-Performance Computing, Geometry Interfaces, Simulation Process & Data Management.
In India, the company, formally registered as ANSYS Software Private Ltd., operates as a wholly-owned subsidiary of ANSYS, Inc., USA. It has offices in Bangalore, Pune, Kolkata, Chennai, Hyderabad and Noida.
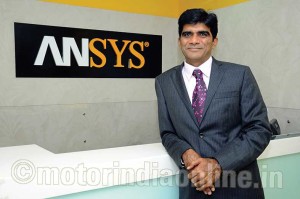
Mr. Rafiq Somani, Country Manager – India, South East Asia and Australia, New Zealand at ANSYS, spoke to MOTORINDIA about the company’s contribution to the domestic automotive industry. Edited excerpts:
It’s a known fact that ANSYS is a provider of reliable simulation software. Could you elaborate further on this?
Yes. One of the themes ANSYS talks about is ‘Realize Your Product Promise’. The ultimate test of the product is when it gets completed, eventually hits the market and is in the hands of the consumer. ANSYS plays a very crucial role, particularly in the early part of this product development cycle and in several cases later as well. Just to elucidate this, we are supporting our clients from the concept stage of product development to its virtual testing, validation, prototype and production-stages. We are also involved in field failures and other challenges involved in product development. Additionally, backward loop mechanism is a domain where ANSYS adds value to the product development.
What is the automotive market share of ANSYS globally as well as in India?
ANSYS is the dominant player in the engineering simulation space worldwide. Globally we command a substantial market share in the automotive space. All the leading automotive OEMs clients in India and worldwide rely on our solutions to streamline their product development. Some of them are Volvo (both trucks and buses), Eicher, Ashok Leyland, TAFE, VW, Bajaj Auto, Tata Motors (both PVs and CVs), Scania, MAN, Navistar, Cummins, etc. In the automotive space, we are already the number one CAE company in the world. Additionally, 23 out of 25 Tier-1 auto component firms are using our solutions. Globally, we work with some of the leading auto parts makers like Dana, Valeo, Bosch, Continental, Delphi, Denso, Yazaki, Bharat Forge, etc. In India, the automotive segment is our biggest growth driver accounting for 30 per cent of our business.
So, what kind of customized solutions do you offer to the global and domestic automotive industry?
I can talk about the series of challenges that the industry is grappling with and areas where we are supporting (with our solutions). Talking about the Indian context, one of the key parameters on which various OEMs develop their products is fuel efficiency. Furthermore, the vehicle emission norms are also getting stringent as time passes. The forthcoming legislation in CO2 emission is compelling most of the vehiclemakers to develop engines which are compatible with BS-IV/V norms. Moreover, the Indian customers are becoming smarter to get value-for-money products. They are demanding many high-end features like infotainment system, GPS, onboard telematics, ergonomic interiors, better cabin comfort, etc. Moreover, the other aspects like warranty, safety, security and reliability, are there on the vehicle buyers’ wishlist. As time rolls on, Indian customers are also very discerning when it comes to next-generation products and are not accepting obsolete products. So, to develop this next-generation commercial or passenger vehicle, there are three physics involved (in the product development phase).
The first one is the structural aspects of physics which has to do with the strength, durability, payload capacity, crashworthiness, impact, etc. The second one is the flow physics comprising engine emissions, air drag, water sealing, aerodynamics, etc., which affect fuel efficiency. The third one is the electronics because there is a lot of action happening when it comes to actuators, circuit boards, and embedded software.
So these three physics are what need to be considered in developing any commercial or passenger vehicle. Today, you cannot rely on a single physics (out of the three that we offer) in a vehicle because there is a complete process involved from ground-up phase to the commercial roll-out. So by offering virtual prototyping to our clients (like CAE, CAD) ANSYS software eliminates a large part of physical prototyping of the vehicle, which is a costly exercise.
So what do you have specifically for trucks and buses in India and overseas?
One classic example is engine development which is a very complex process. Very recently we have acquired a company called Reaction Design which offers simulation and modelling products specifically created to support the development of modern internal combustion engines. Reaction Design’s solutions enable transportation manufacturers and energy companies to rapidly achieve their clean technology goals by automating the analysis of chemical processes via computer simulation and modeling solutions. Reaction Design also provides best-in-class engineering services in its fields of expertise.
We have got some amazing response from automotive OEMs and engine suppliers not only worldwide but also in India. Understanding and predicting the effects of chemistry in a combustion system is key to developing competitive products that meet ever-tightening fuel efficiency and greenhouse gas emissions norms in transportation, energy and materials processing applications. Effective simulation of the detailed chemistry underlying a combustion system is critical to advancements in engine and fuel technology.
How does combustion simulation fit into ANSYS’ long-term strategy?
The reduction of greenhouse gases and improvement of fuel efficiency is a central initiative for major engineering sectors, such as the automotive, aerospace, turbomachinery and industrial machinery industries. Providing simulation tools that enable customers to bring new innovations to life in the areas of fuel economy and emissions reduction is a key focus of ANSYS’ long-term strategy. Various combustion systems such as automotive engines, aircraft engines, industrial burners, thermal power plants and chemical reactors are central to the topic of fuel economy and emissions. The key to improving fuel economy and reducing pollutant emissions is in improving the combustion processes in these devices. Adding Reaction Design’s proven simulation software for combustion gives manufacturers insight into making those improvements. Combined with other ANSYS fluid dynamics solutions, companies will have an unparalleled view into the performance of their existing products and how to create even more energy-efficient ones in the future.
So can we assume that all these simulation systems will replace physical testing of vehicles over time?
I would say ‘Yes’ and ‘No’ to your question. No because we cannot completely eliminate actual testing of vehicles. The OEMs at least need to build a one physical prototype to meet crash-testing and other safety norms. But some companies which make hi-end vehicles cannot afford to develop multiple physical prototypes of a vehicle. And, yes because the number of physical prototypes can be eliminated from, say, five to one or two. In the automotive industry, an increasing number of virtual prototyping is happening. Rather than elimination of (actual) prototyping, I would call it the first time right prototyping for which we handhold.
Could you brief us on your R&D activities in the country?
We have three development centers across India, with Pune being the major one followed by Bangalore (dedicated for electronics and electromagnetics) and Noida. India is the second biggest development hub after the US, and there are around 200 people engaged in various activities (across the three centres). The Bangalore unit is working on an application called ‘Apache’ which is more of embedded software. There is a dedicated wing at Noida having strength of 40 engineers dedicated for electromagnetic vertical. Our Pune facility is not just into application engineering but also into hardcore product development activities including testing and validation. We work hand-in-glove with our development centre in the US. Because of the time zone, the development work gets complemented with each other.
Lastly, what is the roadmap that you have laid for the company for the coming years?
Out of all the major markets in the world, we have taken a challenge to make India one of Asia’s biggest markets. India will be one of the growth engines for the company worldwide. With the kind of customer base that we have in the automotive domain, we have outlined some robust strategies to enhance our business. We are aspiring to make the Indian automotive industry very competitive by coming out with some benchmarked products at a global level. We will be assisting OEMs and suppliers to develop world-class products on a sustainable basis.