Faced with the challenges of supporting a buoyant and growing Indian market, Accurate Technologies Inc. (ATI), the US-based powertrain software and hardware specialist, opened an office in Bangalore in 2013. The new team has grown rapidly in the last two years to provide higher levels of on-site technical and sales support, as well as training and engineering services for clients in the region such as Volvo Eicher Commercial Vehicles (VECV) and Ford India. Having listened attentively to its customer base, the ATI India regional office has contributed to product design and development specifically designed for the needs of the Indian market.
ATI India has been closely involved with Ford India throughout the implementation of the global ‘One Ford’ strategy which saw Ford India provide crucial input for the development of products such as the EcoSport, the highly popular sport utility vehicle manufactured in India. Volvo Eicher, another major user of ATI products, values the enhanced scope for flexible engineering support and user training that is possible via the ATI India office.
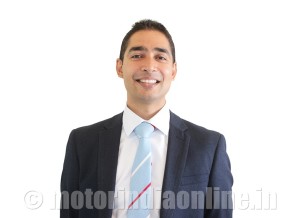
Just as ATI’s customers tailor their global products to suit regional preferences, ATI India is responsible for ensuring that its product features and priorities are closely aligned with the specific needs of the Indian market. This can influence both the product specification and the type of training and support provided.
As an independent supplier of control system development tools, ATI offers a portfolio of hardware and software products for Electronic Control Unit (ECU) and control system design, such as rapid prototyping, in-vehicle calibration, network analysis and interfacing to the ECU. The ATI India office is dedicated to providing tools that allow Indian vehicle makers to compete more effectively with established US and European manufacturers. For example, ATI’s ECU Rapid Prototyping Solution can help the Indian automotive industry enhance its skills in independent algorithm development, currently at a nascent stage in many Indian OEMs.
Meeting off-highway market needs
ATI India’s focus on providing clients with flexibility and independence through local support is especially valuable for the commercial vehicle and off-highway market in India. These vehicle types have a broader range of requirements. So ATI’s ability to support bespoke developments to meet special requirements minimises the involvement and cost of outside suppliers. This provides unprecedented flexibility and autonomy for the clients, and helps to improve their competitiveness against established overseas producers.
In practice, ATI is able to support the development of systems comprising multiple ECUs, communicate via different on- and off-highway protocols, collect and time-align all data into one tool from all systems, and create an autonomous and flexible development environment. The benefits for the customer include reduced development time, maintenance of a single tool chain, avoidance of incompatibility issues, increased flexibility and lower costs.
Indian off-highway manufacturers are not alone in facing global challenges such as increasingly restrictive emissions legislation. JCB, the world-renowned off-highway equipment producer, used ATI’s VISION calibration and data acquisition software to keep their award winning EcoMAX engine family ahead of the latest emissions standards while delivering robust performance under arduous conditions and satisfying the demands of the most critical customers. VISION provided a single, comprehensive, calibration, data-acquisition and rapid-prototyping solution that not only accommodated JCB’s engine ECU but also supported its after-treatment ECU, allowing significant time saving during system development.
JCB also uses ATI’s No-Hooks rapid prototyping software to carry out rapid prototyping directly on engine and after-treatment production ECUs without the need to access the ECU source code, using only the readily available description and memory image files for both ECU types. Though these ECUs use different protocols, JCB was able to reprogram both the controllers through the same, versatile ATI software.
JCB’s controls and calibration engineers believe they are saving weeks on each software iteration by using No-Hooks, because they can carry out rapid prototyping directly on the production-intent ECUs by themselves, without the need to access ECU source code, ensuring any new strategies work fully before involving the ECU manufacturers.
Keeping pace with evolution of Automotive Electronics
Electronic devices in general are constantly evolving, running at faster speeds and able to handle exponentially increasing amounts of data, and automotive electronics is no exception. In many ways, micro-processors for vehicle and transmission ECUs and body controllers have lagged behind those used in computers in some ways, yet in other respects they are more advanced.
Automotive ECUs must remain current over a much longer product life cycle. Their operating environment is harsher than a domestic environment, and the consequences of malfunction can be much more severe, dictating greater emphasis on robustness and exhaustive validation. However, micro-processors used in commercial vehicles are only now moving towards a multi-core architecture, compared to today’s PCs that typically have six or seven 64-bit micro-processors.
In order to keep ahead of these changes, ATI works with the major semi-conductor suppliers such as Infineon, Freescale and others to understand what will be happening in 10 years’ time and ensure that ATI tools can be future-proofed for the next generation of automotive ECU interfaces.
The advances in ECU specifications are necessary to accommodate higher safety, comfort and emissions control standards, which require more sophisticated features and result in more complicated algorithms. In turn, increasing amounts of data are generated from the growing number of sensors required for these algorithms to make the necessary decisions. ATI tools, such as its EMX data acquisition modules, must be able to capture this increased data and communicate it at the higher speeds that will be required in the future.
Business philosophy
ATI has discovered that the most effective way to compete in the long term with larger rivals is to combine product excellence, strategic independence and operational flexibility, and strives to offer the same benefits to its customers through its products. Experience gained working with a wide range of customers and technical advances, from all over the world, has enabled the development of cutting-edge tools that are independent of the ECU manufacturer and do not require the purchase of custom hardware.
ATI has taken positive steps to help even its smaller customers remain competitive as the pace of change accelerates. The open compatibility of ATI’s VISION software allows customers to use it with their existing equipment, avoiding additional expenditure. ATI has also created toolkits with tailored packages of capabilities to provide customers on a restricted budget with the opportunity to use sophisticated tools to gain a competitive advantage by purchasing only the functionality they need.
Regional commitment
ATI believes that establishing a centre of expert technical support and sales locally provides Indian clients with more than just the necessary tools to excel in the development of their products; it acts as an advocate, within ATI, for the particular needs and priorities of the Indian region. This ensures that future global developments in hardware and software are matched to local customer requirements. It also encourages regional participation in development, thereby strengthening local domain knowledge in the longer term, which is significantly more valuable than only utilising the traditional coding expertise of the region. This progressive approach of meeting higher criteria has already been successfully demonstrated at other regional ATI offices.
The most recent example of ATI’s commitment to the Indian market is the introduction of the new DLX data logger which was designed specifically for the priorities of Indian customers, namely, a targeted feature set, top quality and high value. The DLX’s efficient design integrates ECU CAN interfaces, data acquisition channels and stand-alone logging functionality in one pocket-sized device, protected by a tough, splash-proof nylon case. Further value has been achieved by specifying the unit with only those features required by the market, instead of charging for unnecessary functionality that is unlikely to be used. Identifying those features was easier, thanks to the close communication between ATI and its clients in the region through the ATI India office.