In a move to consolidate its core competency of offering services and solutions, Bosch Automotive Aftermarket (AA) acquired SPX Service Solutions three years ago. The move has broad-based its product and service range. Bosch AA is now ready to offer connected services to its entire customer base the world over, with India as its key market, under three brands – Bosch, RobinAir and OTC.
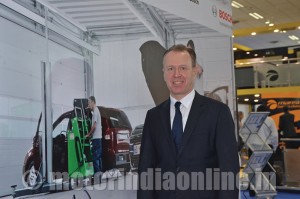
This has pegged Bosch as a one-stop comprehensive service solution provider catering to the requirements of all of its stakeholders like OEMs, OES, IAM and educational institutes.
The Indian automotive market, with its changing consumer trend, customers seeking value for money and advanced technology, and the dynamic mobility concept, is ripe for absorbing intelligent and connected services and solutions. Mr. Guenter Weber, Regional President – Bosch Automotive Aftermarket, says: “Upto the year 2005, we had power tools and conventional systems. Then, it was a little computer in our cars to replace the electronics and make it easier. Today, we are talking about hybrids and connectivity of all of that. We are driving a computer on wheels, so we have to deal with that in a suitable way. If, say, 100 new vehicle models are being added every year in India, imagine what it means for service, for workshop and technician who has to service that.”
Today’s technologically advanced cars and heavy commercial vehicles, equipped with multiple tiny computers requiring maintenance and servicing quicker than before, need the competitive edge of the garages and mechanics who have kept themselves updated with the upcoming technological trends. Bosch Automotive Service Solutions has helped this by coming up with tools to help them with diagnostics, servicing and repairing.
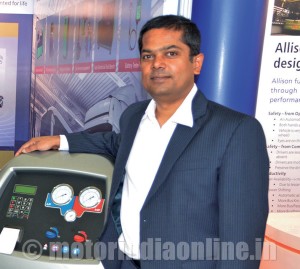
With growing fleets and vehicle population in India, proactive services and solutions are sought by fleet operators to manage their vehicles better. Mr. Abhijit Kallianpur, Senior General Manager, Bosch Automotive Service Solutions, shares: “We enable any proactive maintenance that is required like the kind of mileage a car is giving, emergency calls, accident notification, vehicle diagnostics, and all. It helps the end-user predict when a certain part is going to fail. Car theft, fleet management and integration of all this data helps us serve the stakeholders better.”
Explaining the need for a broad-based knowhow involving connected service solutions to the AA market, Mr. Weber says: “I need software, I have to understand what the car is doing, I have to understand how the software is talking and everyone wants information available to be able to service vehicles. Vehicle maintenance is important if we are talking about total cost of ownership. Service complexity is increasing, and the number of parts is increasing dramatically for distributors and workshops.”
He adds: “Managing all this is a prerequisite to service the end-consumer, but more importantly it requires someone to organize it in the face of increasing amount of technology. Growing electronic content in the vehicles and then the upgradation and growing preference for connected services will drive the next stage.”
Bosch has roughly 24 patents registered for the products and equipment manufactured in-house. Most of them boast of local innovations and are developed in India, right from software, electronics, hydraulics and mechanical construction – which enables them to manage the entire value chain. Bosch exports its hardware and products to more than 60 countries around the world. Its services are largely focused on Australia, the UK and the US. They cater to both the independent aftermarket and OE dealerships.
Mr. Abhijit Kallianpur, Business Unit Head – Bosch AA, throws light on this: “We provide comprehensive solutions towards workshops and technicians from one company. We have diagnostic technical information, special service tools, workshop equipment and services which help the entire business division in its strategy of parts bites and solutions. We also supply diagnostic solutions directly to OEs, so they are single branded and they are supplied with the OE diagnostics content route to OEMs. With this we are able to go in the direction of preventive, predictive and even remote diagnostics.”
Take, for instance, EasyScan 200 or ES200, a diagnostic tool for the independent aftermarket meant to be used by technicians. This comes in handy, replacing a variety of OE diagnostic tools to validate different makes of cars and diagnose faults. Mr. Weber points out: “We have software called Guided Trouble Shooter which informs the technician in a step-by-step approach to diagnose and fix the vehicle. Then we have a helpline and a consultancy for the workshops for the technicians.”
Bosch AS has three segments of doing business with the OEMs in India and the world over – special service tools, diagnostic and equipment and help auto workshops in gearing up to service its end users. Mr. Kallianpur adds: “We have over 10 training centers across the country and we are training roughly 25,000 technicians in various courses. For us, this is the key element that will support training for the technicians to work on latest technology, and one of the examples is how we use latest technology like augmented reality to help in this cause to improve skill levels of the technicians.”
In diagnostics, according to the Bosch officials, they have the capability to communicate with 28,000 vehicle models around the world using the ESI software. This holds good for its reverse engineering process. Mr. Kallianpur says: “Assume there is a new car launched today. If you merely connect it up to the diagnostic tool it will not be able to read, so we have to reverse engineer the protocol. Then once that is created, it will be put into this tool. So, over a period of time, there are about 28,000 such systems that it can communicate with. It is about how we use connected technology to integrate all of these strengths. Platforms and apps, depending on the stakeholder, provide information using a portal and an app. Call centers are also available.”
To process the entire information gathered from all concerned areas using the Internet-Of-Things or IOT requires data analytics. And Bosch officials claim it to be the corner-stone of their Parts, Bites and Services strategy.
Training the future generation to keep them updated to the dynamic technological trends is a challenge that Bosch takes seriously. Mr. Kallianpur shares: “We work with universities, engineering colleges, polytechnics, ITIs and the like to help them train their students. We have joint certification centres with educational institutions where we have Bosch equipment. We create the curriculum that goes more or less in tandem with what the students are already being taught. This includes specific on-the-job training that increases their skill levels and employability, and they have a certificate authorized by Bosch and their institutes as well.”
Bosch is establishing an engineering laboratory for the connected cloud services team in Bengaluru. Mr. Kallianpur says: “There are two offices like these in Pune. We do not manufacture anything but offer engineering services.” The main training center in Pune has its commercial IT office and technical information services office.
Bosch Automotive Service Solutions is top-of-the-line all the way.