Smart solutions are defining new paths in bridging EV gaps right from design stage, all the way to manufacturing, says Bhavaneesh Athikary, Automotive Lead – Indo-Pacific, Hexagon | MSC Software
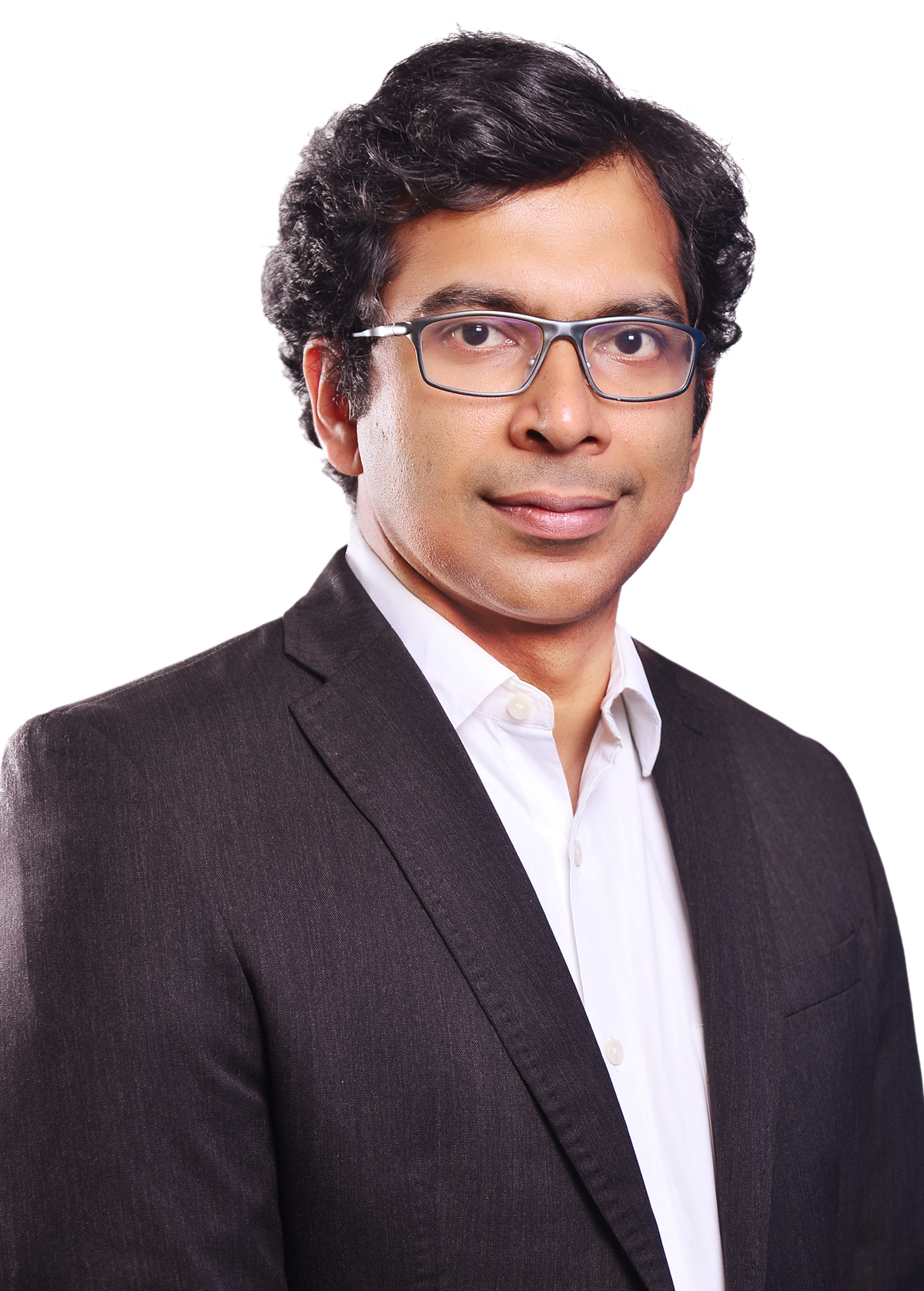
India is the world’s second most populous place on earth with a domestic consumer market that dwarfs entire nations. Today, it offers perhaps one of the worlds’ biggest untapped prospects for electric vehicles (EVs) with a market valued at USD 5 billion. It is expected to reach USD 47 billion by 2026, registering a CAGR of above 44% during the forecast period. Various reports, in fact, suggest that the only way for India’s EV market is up. The south-western State of Kerala, for example, aims to put one million EV units on the road by 2022 and 6,000 e-buses in public transport by 2025.
Meanwhile, the southern state Telangana aims to have EV sales achieve 80% for two and three-wheelers (motorcycles, scooters, auto-rickshaws), 70% commercial cars (ride-hailing companies, such as Ola and Uber), 40% buses, 30% private cars, and an overall 15% electrification of all vehicles by this same period. Experiments with e-mobility for public transport have also led to the deployment of electric intercity buses across several other major cities. While data from the Society of Manufacturers of Electric Vehicles (SMEV) indicates that 2021 EV sales in India are down by 20%, this has been attributed largely to the pandemic. Still, the momentum is growing.
In February 2021, India’s first intelligent EV manufacturer, Ather Energy, moved its USD 86.5 million factory from Bengaluru to Hosur. Ather Energy’s factory is said to have an annual production capacity of over 1,00,000 electric two-wheelers, up from its previous capacity of 25,000. Furthermore, Ola Electric, the subsidiary of Indian ride-hailing start-up, Ola, also announced that it would be setting up the world’s largest electric scooter plant in Hosur at a cost of USD 330 million. It aims to produce two million units a year, and in fact, by next year, wants to scale up production to 10 million vehicles a year – or 15% of the worlds’ total number of e-scooters.
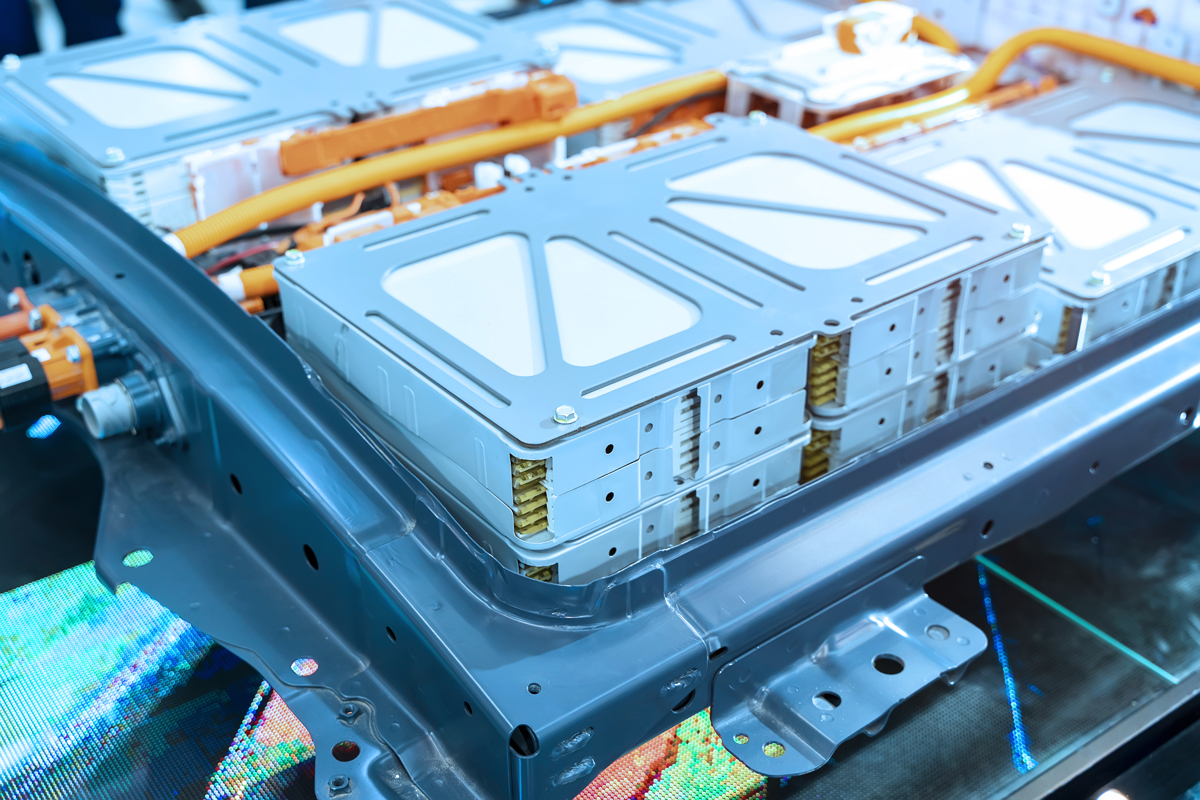
The uptake has also been bolstered by government initiatives such as the Faster Adoption and Manufacturing of Hybrid and Electric Vehicles (FAME), and more players are joining the market mix. Charging stations, likewise, have also been on an upward trajectory. In January 2020, the Department of Heavy Industries (DHI) of India approved 2,636 electric vehicle charging stations in 62 cities across 24 Indian states and union territories (UTs) under the second phase of the FAME program to promote e-mobility. However, there are a few bumps in the road ahead before EVs can go full throttle.
Powering On: The Shape and Size of EVs
When it comes to EVs, the challenge is transforming from demand to supply. A major concern for manufacturers lies in the batteries where there is a need to balance the desire for high charging capacity, low charge times and long service life against the production cost and the impact of battery size and weight on vehicle performance. There are serious considerations for EV providers as well in areas like material selection to thermal performance of the battery system; from protecting the battery units from damage in an accident to providing safe as well as sustainable battery-powered mobility solutions.
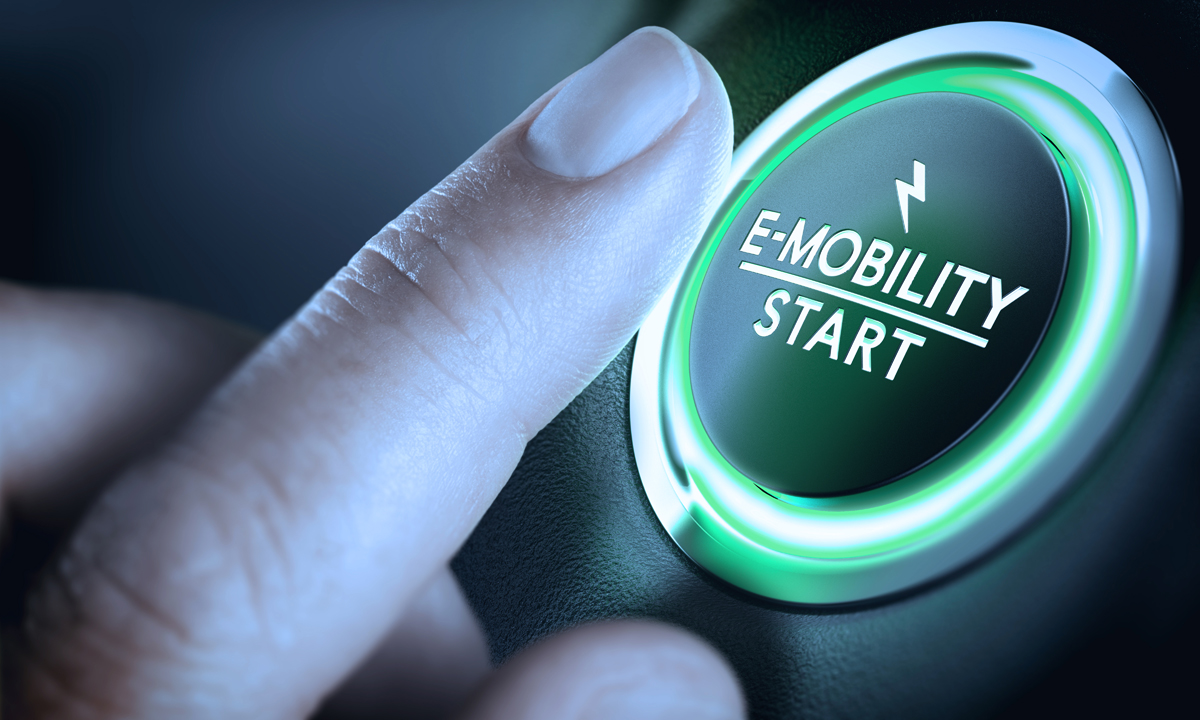
Here, Hexagon’s smart manufacturing technologies provide a number of solutions for e-mobility providers to optimise and validate battery designs using computer-aided engineering (CAE) simulation, ensure robust battery manufacturing processes with process simulation and execution tools, and verify components and battery systems through non-contact inspection and non-destructive testing techniques. The future of sustainable transportation is also seen in the development of hydrogen fuel cell vehicles, or fuel cell electric vehicles (FCEVs), which generate energy through the electrochemical reaction of hydrogen and oxygen with only water as a by-product.
According to Allied Market Research, the hydrogen fuel cell vehicle market size was valued at USD 651.9 million in 2018, and is projected to reach USD 42,038.9 million by 2026. Some analysts expect FCEVs to dominate vehicle sales by 2030, and their use in military vehicles, mass transit and aircraft is already increasing. Yet, the development of fuel cell technology into a viable mainstream alternative to petrol and diesel combustion engines remains challenging for manufacturers; not least the fact that manufacturing FCEVs requires a number of unique parts and production technologies including bipolar plates, membrane electrodes, catalytic electrodes, hydrogen injectors and carbon-fibre hydrogen tanks.
Manufacturers also need to adapt other more typical automotive parts to fit a fuel cell powertrain – for example, the cooling systems. Hexagon’s simulation, production and inspection solutions are therefore supporting manufacturers working to develop the next generation of fuel cells and FCEVs. From thermal modelling to help modify cooling systems for effective operation with fuel cells to case production to ensure safety of this new technology in the event of an accident, its technology provides data to help accelerate innovation. Meanwhile, e-motors are also emerging as an exciting game-changer.
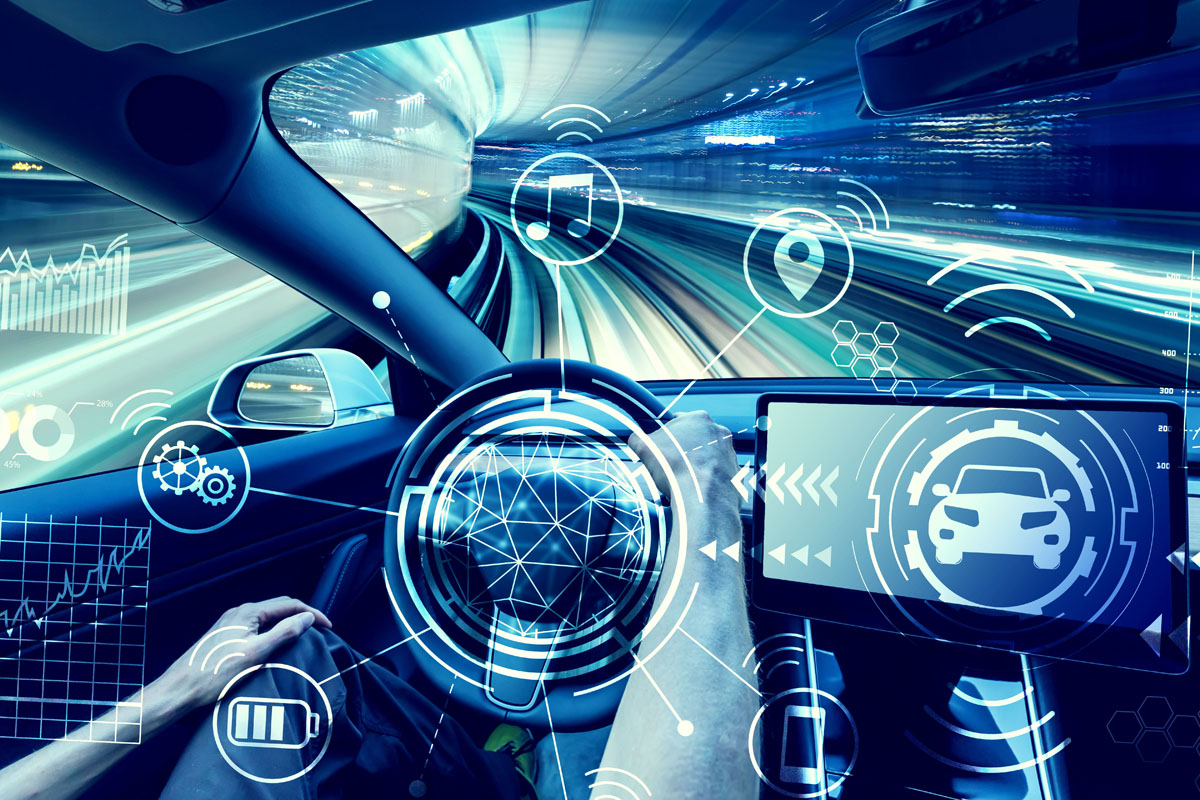
Public awareness and acceptance of electric motor vehicles has never been higher, but concerns over range, coupled with relatively high prices compared with combustion engine vehicles, has so far limited the adoption of electric motor technology for e-mobility. The operating principles of electric motors are relatively simple, yet designing and manufacturing electric motors brings a new set of challenges for automotive manufacturers. Electric motors have fewer mechanical components than combustion engines, but still contain a number of intricate parts like stators, rotors and hairpins that require very accurate production specifications.
These parts will need to withstand significant thermal stresses through their lifetime. Design engineers working on electric vehicle motors must also consider new challenges, such as the different noise emissions of the vehicle and how they will impact driver and passenger experience. In this regard, Hexagon’s extensive automotive industry experience provides CAE simulation, production and quality assurance technologies to OEMs and others in the supply chain. Our understanding of the dynamics of new vehicle development and manufacturing ramp-up uniquely positions us to support the industry in developing the electric motor to its full potential. As such, production of electric vehicles is made easier, increasing manufacturing productivity, lowering costs and reducing time to market.
Gearing Up for Safety and Sustainability
Rapid urbanisation, growing awareness about climate change and electrification together are trends driving a future where clean fuel and smart features will be at the forefront of automotive innovation. Therefore, manufacturers require efficient ways to develop EVs, but without prohibitive cost while factoring in environmental-friendly designs. This has led to a race to build better and more tailored models – pushing the envelope beyond contemporary practices. Such a rapid pivot can only be addressed through smart manufacturing technologies that support design and development from concept to customer.
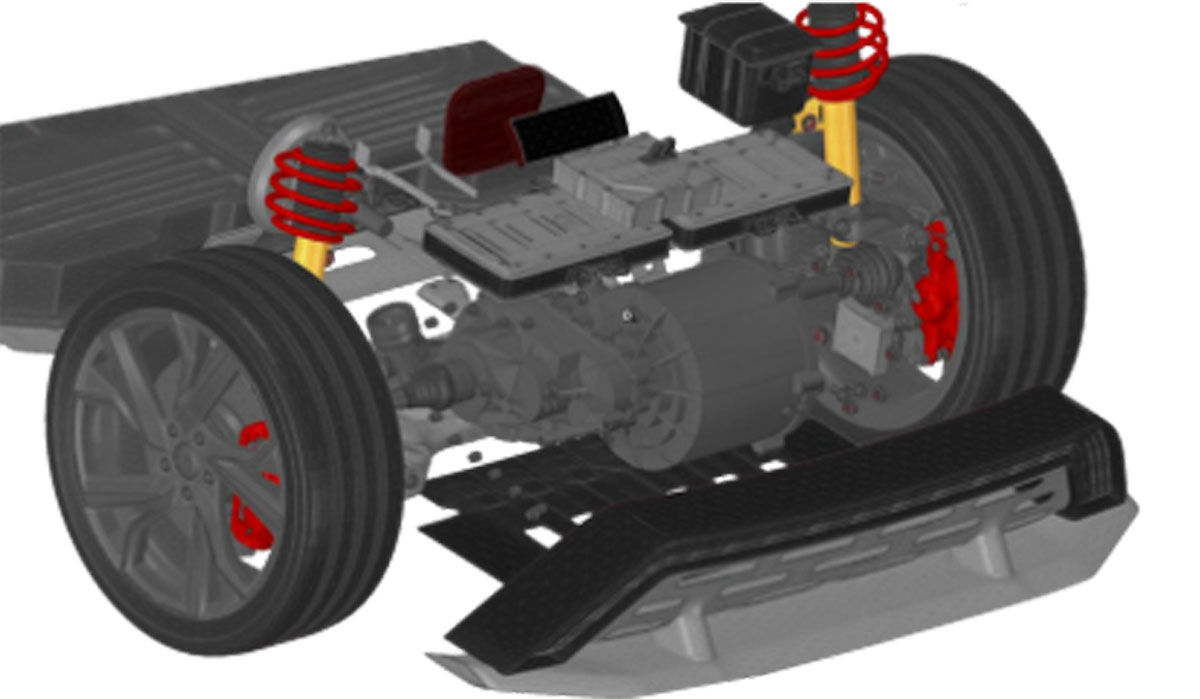
Smart manufacturing technologies can help solve the twin problems of automotive modelling – which now requires more integration than ever before – and safety concerns. In automotive modelling, which now requires the integration of mechanical, electrical, electronics and communications systems to come together, it is further complicated by the need to balance greater comfort, easy handling, better in-car experience with the need for safety and lesser fuel and material consumption.
At the same time, the rapid rise of e-mobility increases the conversation surrounding the safety of EVs. Today, road testing forms a critical part of the vehicle build process. However, a driving system that can function safely in practice needs at least a billion miles of testing according to industry estimates. This makes physical testing impossible and unviable. Therefore, simulation technology is the only way to test for the thousands or even millions of possible conditions that might arise during a drive.
CAE simulation can help address these situations since it allows us to not only design the vehicle, but also design and develop the entire ecosystem, including other cars, pedestrians, bad roads, buildings, traffic systems, and so on. Hexagon technology such as Virtual Test Drive (VTD) enables users to create, configure, visualise complete virtual environments, in which vehicle models can be thoroughly evaluated and validated in nearly any conceivable condition of operation. While physical testing won’t go away completely, the role of simulation is front and centre.
Advancing Together
As we move into the first chapter of a whole new story of energy and mobility across the planet, we believe the race for 100% clean, safe, cost-effective electric vehicles can be accelerated and it can reach a higher bar as industry and government work together. Our goal is to help manufacturers make the transition more effective. From OEMs to suppliers and mobility providers to industrial engineers, Hexagon is supporting the industry in designing and producing this next automotive evolution. With other industry leaders, we continue to set pace in the race for a more intelligent, integrated approach for a sustainable future – helping product manufacturers to advance their engineering methods with smart simulation software and services to tackle the challenges of ramping up and commercialising EVs.
—
About the author
Bhavaneesh Athikary, Automotive Lead – Indo-Pacific
Bhavaneesh has over 16 years of experience in the automotive domain, most of which is focused in the field on engineering simulations for automotive OEMs. Currently he heads Automotive, Business Development for automotive industry in Indo-pacific region. As a part of this job, he works closely with all major automotive OEMs and suppliers in Indo-Pacific region, helping them solve their engineering challenges.