“Our conscience does not allow us to use low quality material”, and this policy approach has ensured the sustained growth of Shree Damodar Coach Crafts (SDCC).
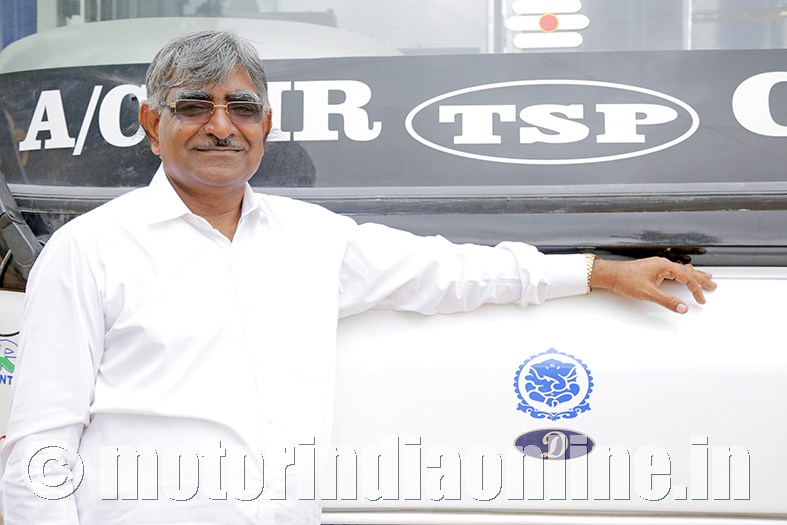
Mr. G.L. Sharma, Director – SDCC, founded the company with a partner in Goa in 1993. Originally hailing from Jaipur, Mr. Sharma dived headline into bus body building and built SDCC from the scratch with the help of this partner.
He reminisces: “In 1997, we registered it as a private limited company. Later, in 2007, we set up a unit in the KIADB, and in 2011 we opened another one in Dabaspet. Currently we are constructing the KIADB unit where we will build special-purpose vehicles like caravans, mobile hospitals, mobile banks and reefers and also pursue regular bus body building.”
SDCC builds bus bodies for a range of customers, from major Indian OEMs and STUs to private fleet owners. Since the time they rolled out their first bus out of SDCC’s workshop, they have been flooded with orders. Mr. Sharma says: “In the initial days, our clients were from Karnataka, Maharashtra and Goa. Since the beginning we have earned goodwill because of the product quality.”
The specialists
SDCC built its first sleeper coach in 1989 for a private fleet owner. Mr. Sharma shares: “In fact, you can call us the pioneers of sleeper coaches in India. In 1989 there was no provision in the MV Act to register the sleeper coach. One fleet owner saw it abroad and wanted us to make it for them. Though they initially had difficulty in getting the vehicle registered, they eventually did it and the coach went on to the roads. People saw it and we started receiving enquiries from Gujarat, Maharashtra, Tamil Nadu and Kerala. One particular large fleet owner wanted to inspect our premises. Once he became satisfied with our technology and our professional team, he ordered 200 sleeper coaches. And this owner from Gadag now swears by the SDCC sleeper coaches.”
Success on wheels is an advertisement for the product quality. Mr. Sharma adds: “In 2004, a traveller was going to Goa with his family by a sleeper coach built by us. Sometime later, we heard from his operator friend from Kolkata who visited us and ordered for a few units of the same. Initially he plied them from Siliguri to Dhaka, but when the route to Dhaka was cancelled he ran the sleeper coaches from Siliguri to Kolkata. In turn, the WBSRTC got us to build for them too. So, our business has always run on customer recommendation because the customer watches everything – from quality, delivery schedule to comfort.”
Mr. Sharma prides himself on the fact that he and his team always strive to be in direct touch with the fleet owners to know the tyre and diesel mileage, among other things. He shares: “Our customers generally say that on every trip they save about 20 litres of diesel. And that’s why we take daily feedback from our end customers.”
Uniqueness of SDCC
Mr. Sharma further observes: “Our conscience does not allow us to use low quality material. We will even stop production till the time we get the right quality material. We use high strength steel of 2mm thickness which offers high capacity for corrosion and is stronger but lightweight. This translates into saving diesel and tyre life. We believe that the structure and the flooring need to be of quality because these vehicles are supposed to run for at least a decade and our quality complements it.”
Currently the Dabaspet unit of SDCC has a capacity of building 20 sleeper coaches a month, and the Goa unit produces 10 sleeper coaches. He shares: “Once our KIADB plant gets operational, we will have a monthly capacity of 80 buses.”
SDCC also relies on its own in-house design team which keeps working on upgrading the design based on the daily feedback received from clients.
Lightweighting in the EV era
In the slow yet steady run-up to the EV launch, SDCC has been receiving orders to make EV bodies. Mr. Sharma adds: “We are making two prototypes for an STU. Since their main focus is metro city buses, they are planning to have a battery that can run upto 200 km. So they need the body to be lighter so that the battery can last longer. Now there are two options to make it lightweight. One is carbon fiber and the other is aluminum. Carbon fiber is highly expensive. We are going to use aluminium.”
India may leapfrog from BS IV to VI or launch EVs in the near future, but it is true that certain ground problems still exist. Mr. Sharma says: “Overheads for a large, medium or a roadside body maker are different. The roadside one does business without billing and the Government loses out on the revenue unlike us who go through the system, pay taxes and have relevant bills for material, among other things. Another problem is that there are two kinds of certification – one is self-certification and the other is ARAI certification. SDCC has spent a huge amount on ARAI certification, but there are others who have not. Another problem is that if the chassis manufacturer installs an engine of a certain horsepower other than the one recommended, then we are unable to get the registration done. But as a body builder, I bear the brunt of it and pay the difference for certification when it is the responsibility of the chassis manufacturer. I seek better clarity on this issue.”
On its part, SDCC has presented its recommendations to CIRT urging it to make amendments in order to reduce the loss to body builders. Also, as a front-runner in sleeper coach manufacturing, the company has set a high standard for quality and reliability in this segment. In a nutshell, the name SDCC is synonymous with quality.