Novel products underway for passenger safety, comfort
Busworld India 2016 witnessed enthusiastic participation from several ancillary suppliers who presented new developments and futuristic solutions across a range of product categories such as AC systems, lightings, seat fabrics, wiper systems, tooling and fabrication, harness and connectivity, etc. We bring you some of the most interesting ones in this exclusive report.
Efficiency through power saving
Bustec, a Czech company, showcased an innovative surface mounting device (SMD) LED signs. This latest technology, according to Mr. Arun Kumar H.C., Director, Bustec, “has low power consumption but provides high illumination of 1300 MCD (mili candles) with a long life of one lakh hours.”
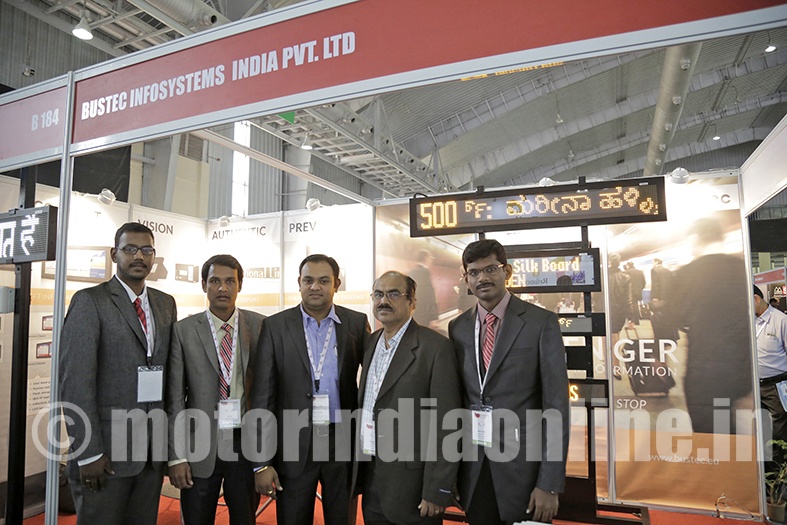
Considering Busworld India as the best launching pad, the company that functions from Bengaluru for its India operation, has completed all the mandatory certification from ARAI two months prior to the show.
He said: “Globally recognized as a market leader in SMD LED signs with a long history of more than 20 years, “we have supplied around 60,000 LED signs across the world. While we have been able to localize most of the mechanicals in Bengaluru, PCB boards come from the Czech Republic. We are confident that within two years we will be able to manufacture even PCB boards in India and look at exporting from India.”
Bustec aims to achieve 1,250 vehicles in a year, and going forward as India moves towards accepting electric buses the number of vehicles can grow upto 5,000. “Our product with new technology offers low power consumption of 3 amps for all the set against the standard 8.5 amp which can save up to 65 per cent of power,” he added.
The Indian bus AC market has witnessed exponential growth in the school bus, staff transport and tourist segments in the last three to four years. There has always been very good acceptance for new technologies with customers demanding hi-tech products. In order to offer affordable AC units and grow rapidly, PKN Moulders started manufacturing bus AC units for its tourist customers using Tempo Travellers. Having established them as a brand to go for in North Indian market due to the Korean technology, copper tubes for condensers, aluminum fits for condensors and blowers from SPAL, Italy, PKN now looks to expand in South India. “We encourage our customers to visit us to see our operation as well as the product. In this way, they could know us better. This is important for long-term business relationship. They can also understand that our reputation is only as good as the reputation of the materials that go into our products and thus we work closely with customer’s requirement,” explains Mr. B.S. Arora, General Manager, PKN Moulders Pvt. Ltd.
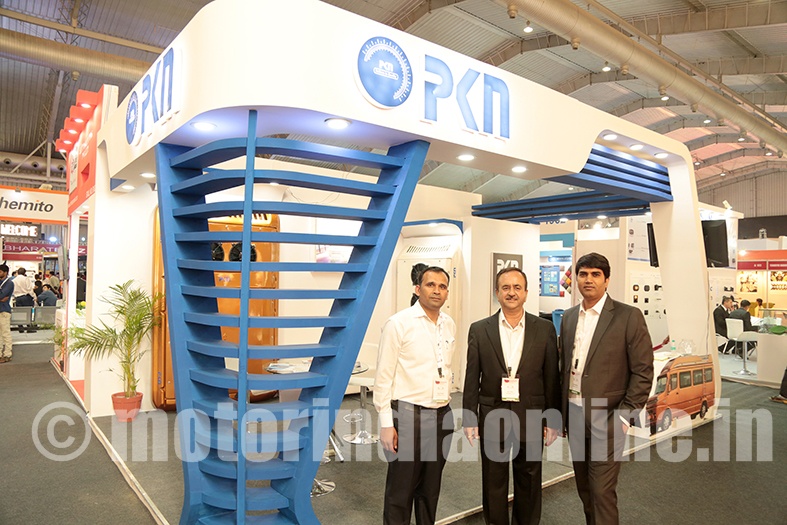
The company, located in Bhiwadi in Alwar district of Rajasthan, has the capacity to produce around 150 bus AC units per month and did around 800 units last year. “We plan to grow by 30 per cent CAGR as we have done around 3,000 vehicles in the last five years,” states Mr. Satish Sharma, Managing Director, PKN Moulders Pvt. Ltd.
Upholstery fabric
Reliance’s textile division debuted at the show and impressed one and all with its finest fabrics. Although Reliance has been a pioneer in the field of branded upholstery and textiles since 1988, it started supplying for buses only since 2007. “We have technology to make different fabrics and produce a variety of woven and knitted fabrics with moisture control, fire-retardant, water-repellant and anti-microbial properties with fragrance, which are popular among some of the leading automotive and sportswear manufacturers. The best part is that we believe in innovation. We also have stain release, self-cleaning fabrics, and any dust or impurity will not get into the fabric. If it is on the surface you can just wipe it off,” reveals Mr. Sambit S. Satpathy, General Manager – Auto Textile Division, Reliance Industries Ltd.
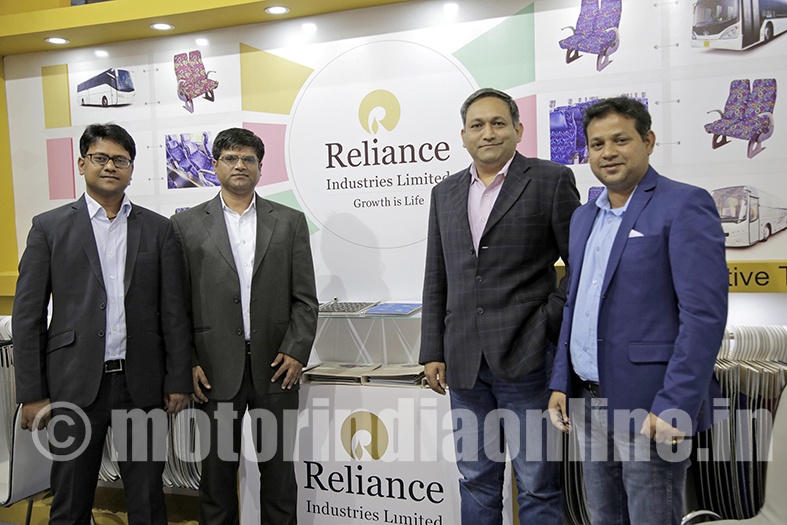
Just in nine years the company’s auto textile division has penetrated around 30-32 per cent in the Indian bus segment. “At present we have the capacity to produce around 3 lakh metres of fabric a month, and in the next two years we should be able to achieve 60 per cent of marketshare in the bus segment,” beams Mr. Satpathy.
Another company that caught attention was Turkey’s Epengle that supplies luxury fabrics to both German and Swedish bus manufacturers. “Last year we did fabrics for around 10,000 seats in India and are targeting around 50,000 seats in the next two years. However, we believe that Indian has a total industry volume of over 2 lakhs seats and hence we have a good opportunity to tap the requirement,” informs Ahmet URKUT, Sales and Marketing Manager, Epengle.
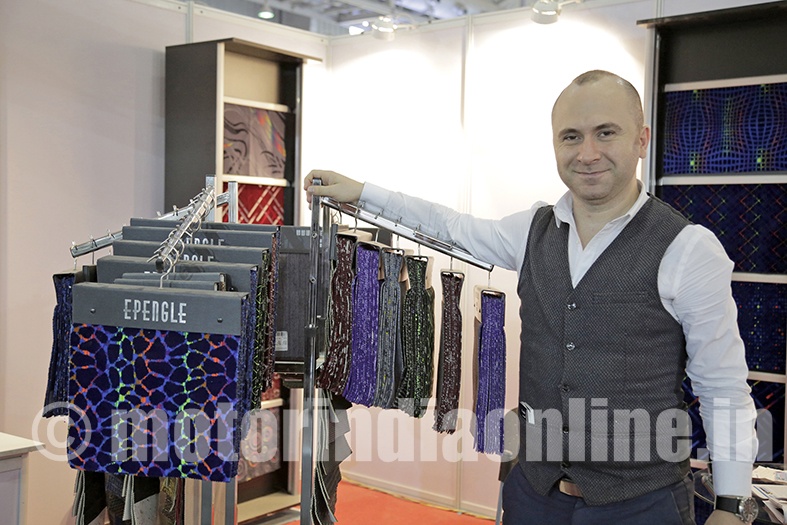
The Haryana-based Niemla too showcased its variety of fabrics at the show. The young CEO, Mr. Armaan Mehra, says: “For bus seatings, our range of jacquards and dobby are available in a variety of designs and colours. We have got two plants, one in Haryana and the other in Gaziabad. The former can produce one lakh metres and the later around 25,000 metres a month.”
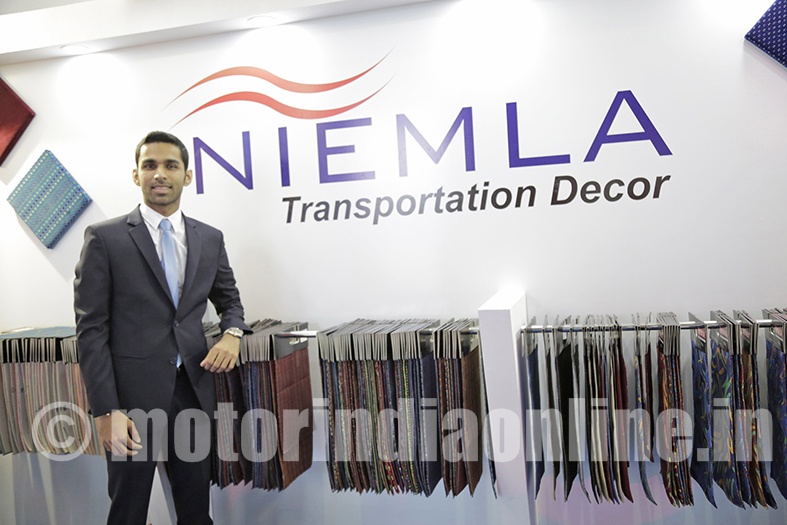
Rubber, components and fabrication
ALP Overseas Private Ltd., along with Nishikawa Rubber Company, Japan, provides sealing solutions to major automobile manufactures in India. ANCO, as the JV is known, is the market leader for supplying EDPM, PVC, TPE and TPO sealing to OEs. “We help the OEMs bring out better products for front and rear windshield, glass run, bonnet seal, door seal, etc., and have approximately 50 per cent marketshare in India and contribute to 30 per cent globally,” says N.K. Gauda, DGM – Sales, ALP Overseas Pvt. Ltd.
The show even hosted suppliers like Basant Overseas offering aluminum doors, roof hatches, head lamps, tail lamps, rear view mirrors, wiper systems and almost all auto components used in a bus. “We also have stop signs for school buses and will soon be introducing day running LED lamps like you see in Mercedes cars or BMW cars to our portfolio of products,” said Mr. G.S. Anand, Director, Basant Overseas.
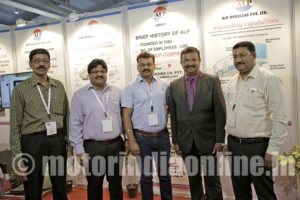
RG Fibrotech provides fibre reinforced plastic (FRP) components in almost any shape and size, tailored to the requirement of the bus industry. Mr. Ajith V, Manager, RG Fibrotech, the Belagavi, revealed: “We have an entire manual production process that starts from gel coating, laminating, trimming, heating and finishing to creating best designed products. We make around 500 pieces of front and rear face of the bus and around 180-200 dashboards at present for one of India’s leading bus manufacturers.”
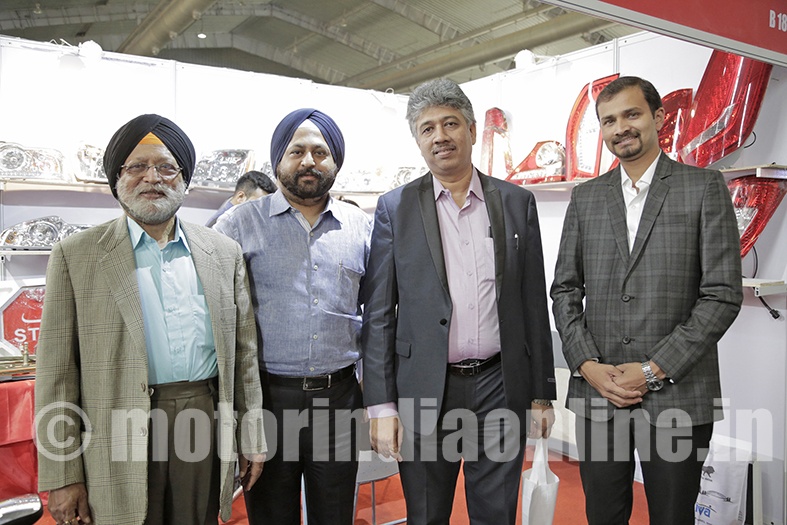
In their endeavor to take the bus industry forward and help it grow, the new innovative products and technologies developed by these ancillary suppliers will undoubtedly play a major role in the future of the country’s bus sector. By exhibiting at Busworld, the companies displayed precisely how close they can get to contribute to the performance, efficiency, safety and comfort of buses in India.
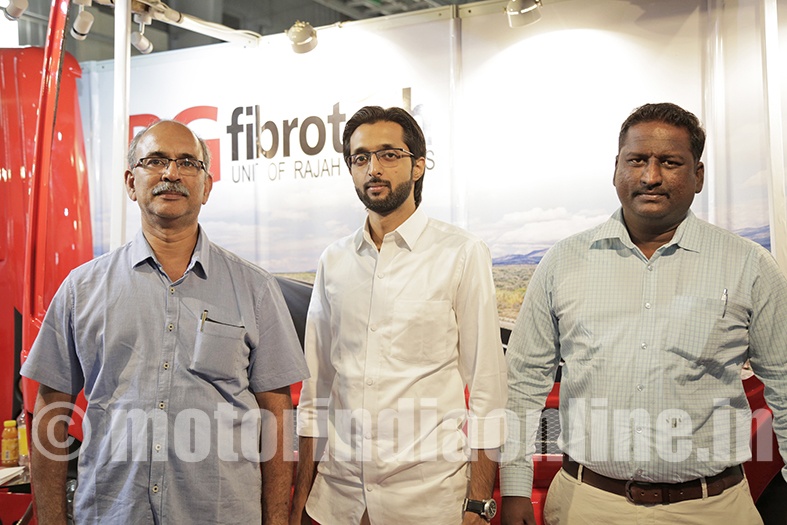