Contributing more than 6% to the nation’s GDP as per reports in April 2021, the Indian automotive industry in its entirety provides employment to about ‘37 million people’. In the continuing turmoil triggered by the COVID-19 pandemic, the industry is trying to step on solid ground where if stakeholders are introspecting, and some looking up to the industry leaders for directions, others are strengthening their manufacturing capabilities. In that context, it is timely to have Vinnie Mehta, Director General, ACMA, share his opinions in an exclusive interview with MOTORINDIA’s N. Balasubramanian about how the market sentiment is slowly yet steadily lifting up with cautious optimism
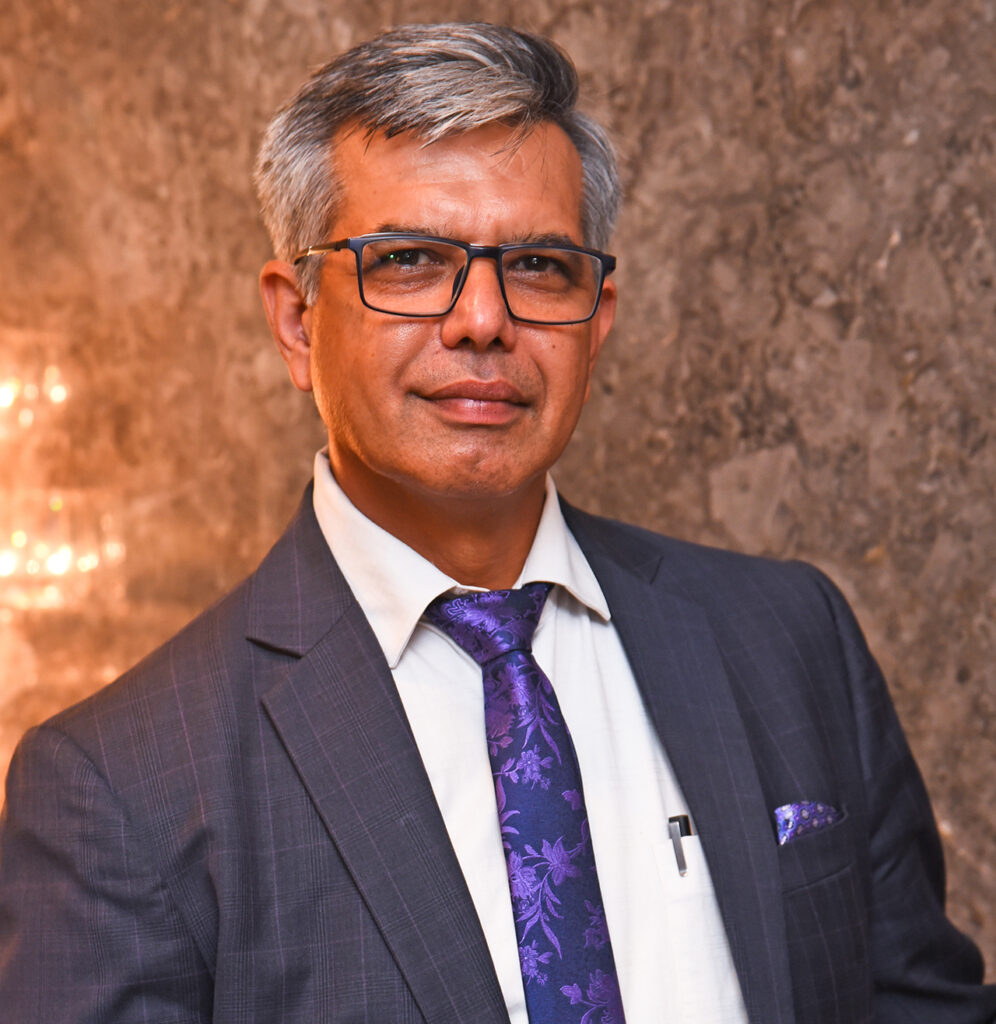
According to research organizations, the Indian auto industry, including component manufacturing, is poised to grow beyond US $ 251 billion by 2026. And, a study by the Centre for Energy Finance states that the Indian EV segment has the potential to touch US $ 206 billion worth of opportunities by 2030.
Vinnie Mehta, Director General, ACMA assures the industry stakeholders that though there are challenges, the Indian automotive industry as a whole is focusing on strong growing business avenues like exports and the aftermarket segment. He is hopeful that notwithstanding the potential negative impact of the 3rd wave of COVID-19 pandemic, the industry is set to grow at the same pace as last year if not marginally better.
Excerpts from the interview:
What, according to you, is the current market sentiment in the continuing COVID pandemic coupled with lockdown challenges?
At the outset, we are proud that the entire automotive industry – be it the OEMs, or the component manufacturers – rose up to the occasion and helped divert industrial oxygen to the hospitals, set up oxygen camps and even hospitals. It is true that the industry as a whole is facing an adverse impact. In the last couple of months, we have witnessed partial lockdown with activities somewhat resuming. There are challenges such as companies going on maintenance shutdowns and there are issues pertaining to supply chain and logistics. This has been the case in both May and June and I believe that the same will continue to an extent.
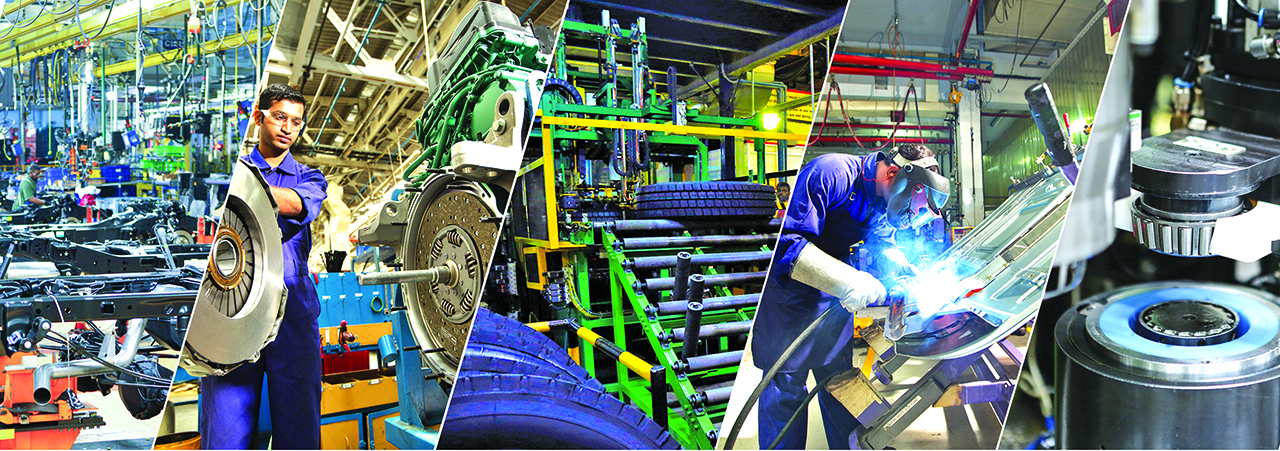
In May, the auto industry was operating at 30-40% capacity which increased to 40–60% in June. It really depends upon which part of the country one is operating in and how adversely the business there has been impacted. On the one hand, the industry sentiment seems to be at a low because the 2nd wave is proving to be more devastating than the previous one, while on the other, people are cautiously optimistic that there will be recovery from the 2nd quarter onwards notwithstanding the next wave. The challenges may take the entire financial year to be overcome. Post the 1st wave, there was an improvement in business sentiments, and footfalls in the auto showrooms had increased. Going by the OEMs, the demand could be a little bit tougher but it will continue. The industry may not exactly be on target but the vaccination drive will bring in confidence in the people for across every single sector. Also, the 1st wave did not impact the rural market at all but the current wave has, though we do not have sufficient data on it. The extent of it will pan out in the next few months and it could be a potential red flag. But there is hope in the market.
Lastly, the best part is that this time around the workforce migration has not been much when compared to the 1st wave.
From the component industry perspective, what are the learnings from both the pandemic waves?
There are two key learnings. The first is financial prudence and better preparation. There was no panic this time around like in the 1st wave. The second is that the companies have understood that people are the most critical resource. When we look at the financial programs, people have gone asset light because they have realized the value of work from home where it is relevant. People have better understanding now of the value of deploying sophisticated tools for managing the entire supply chain and operations including industry 4.0 parameters, besides office automation, as they enable efficiency and sustainability.
What are the industry expectations from the government and how well are they being met with?
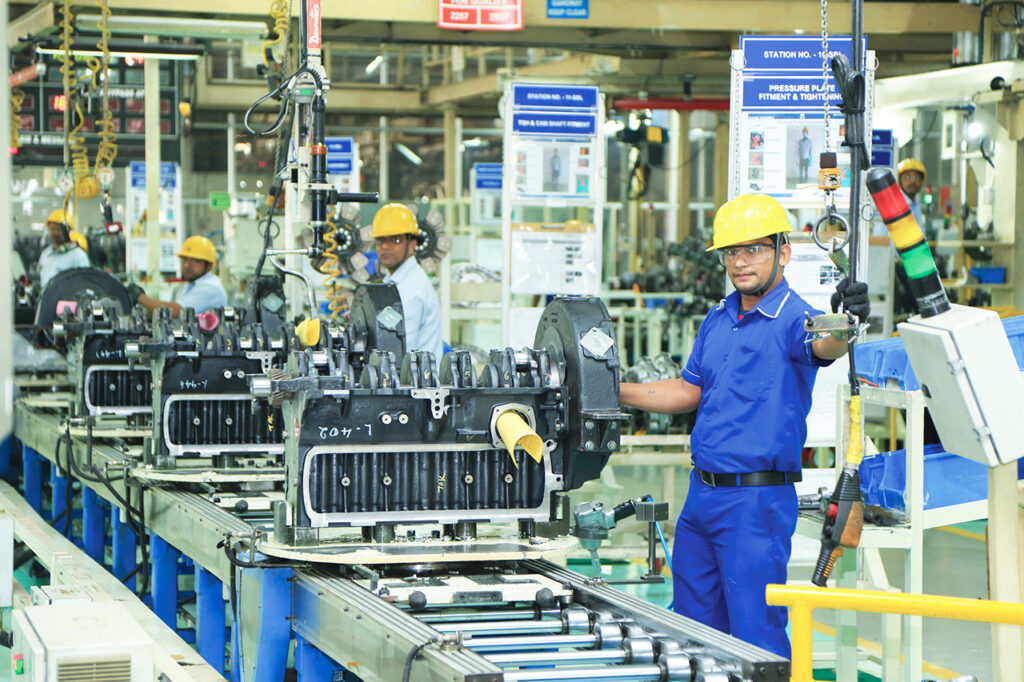
What needs to be realized is that on the financial front, the government is extremely stretched at this point in time. Yet, the government continues to deliver what it had promised. We are happy that the government has recently come up with the National Programme on Advanced Chemistry Cell (ACC) Battery Storage which has an outlay of Rs. 18100 crores towards establishing local manufacturing capacity of 50 GWh of ACC and 5 GWh of Niche ACC capacity.
Soon, we are expecting another big shot in the arm in the form of a sizable outlay of Rs. 57,000 crores over a five-year period. This will bring in much needed boost in confidence and improvement in the market sentiments. The objective is to make the industry globally competitive.
It is interesting to note that in the 2nd wave while the domestic supplies suffered, the exports continued to grow strong, even though the segment accounts for 25-30% only, which may not really offset the challenge in the domestic market. But great export performance sends a strong message in terms of de-risking, making it possibly one big element of our recovery strategy. And major markets like Europe and North America are fully open to be continued to tap into.
Besides, we hope that the central government’s PLI scheme would give our economy a further thrust. Competitive rates on the RoDTEP, coupled with a generous auto PLI, will encourage the manufacturing industry which, in turn, will help the industry recover faster than what we are currently thinking of.
How are the MSMEs in the auto sector faring?
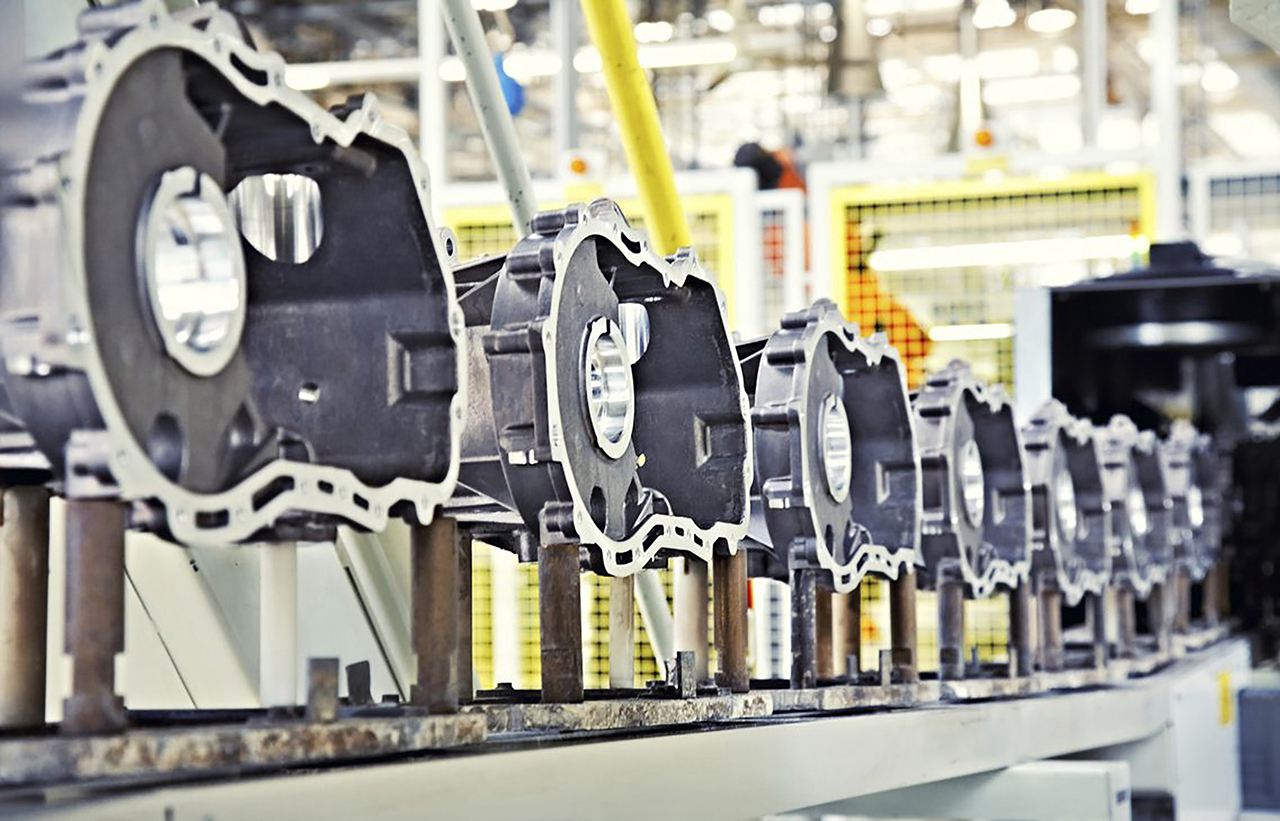
Over 65% of our members today are MSMEs. There is no denying that they were stressed out because they were operating under sub-optimal capacities. Yet not a single ACMA member shut down. We give credit to the OEMs because having learned a lesson in the 1st wave, everybody is now focused on a robust supply chain to minimize disruption. And in some ways, they have ensured that the tier 2 and 3 companies are also taken care of. In the 1st wave, ACMA had urged all the OEMs to ensure payment clearance. Also in the 2nd wave, the SIAM Sourcing Group worked closely with ACMA in terms of mapping and seeing how we can increase localization in the tier 1 companies to begin with. The Group as such works on procurement of raw materials and components besides other issues.
In the last couple of years, many Indian companies have found global partners, entered joint ventures, and have signed technology agreements. Can you throw some light on this?
The industry realizes that it has to continuously add value to its offerings to stay relevant to its customers. And that can come only with using better technologies, and products that meet the operational boundaries set up by the regulatory environment. India is a price sensitive market. And if we continue to import, we will not be able to meet the price expectations of the consumers. Hence, localization is imperative to keep costs down. India is known for its frugal engineering which is what delivers better cost. On our part, ACMA is supporting engagement with startups in component manufacturing.
If COVID pandemic has inevitably turned a number of companies introspecting and working on improving their capabilities, what other opportunities do you think the pandemic has brought about for, say, suppliers?
Definitely the pandemic has forced a hiatus on us but the time gap has enabled people to focus on what they wish to be in future and work on value propositions that can be offered. This, in turn, has enabled them to look deeper at resources – be it people, infrastructure, future investments or sourcing technologies. This has encouraged us to be more AatmaNirbhar and to train our focus more on localization.
Do you think the anti-China sentiment that can be seen globally has played in India’s favour and opened a slightly larger window of opportunity for our suppliers?
The size of the Chinese auto component industry is 11 times bigger than ours. They are US $ 550 billion worth industry whereas we are US $ 50 billion. China has many lessons for us. We are practically similar in terms of our population but we are not able to scale up and create a huge dynamic market like them. India must primarily look at how to scale up because only then we can benefit from the huge economies of scale.
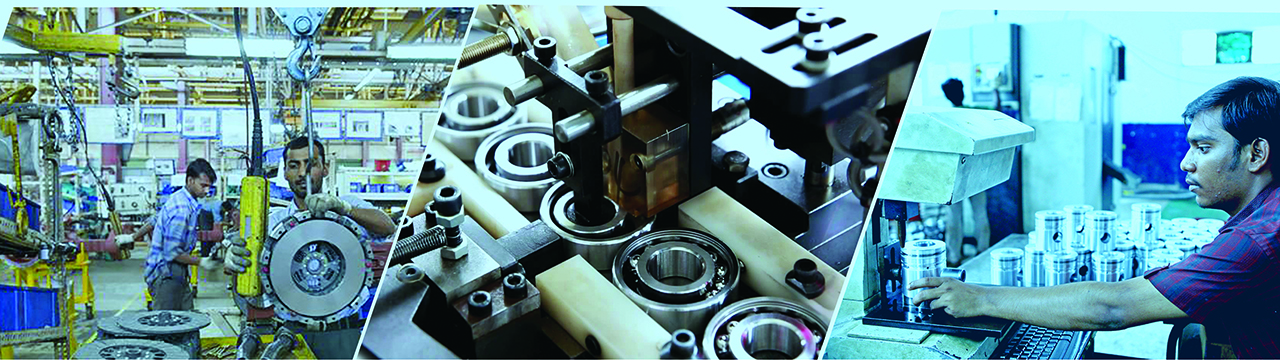
What is ACMA doing towards skilling workforce?
The mandate to upskill the industrial workforce is with ASDC. Our industrial competitiveness lies solely on learning newer skills along with the digitization of factories, upskilling for manufacturing technologies that are the outcome of the regulatory changes, and those which are futuristic in nature like the electromobility. Besides the manufacturing industry, there is the aftermarket which needs to be able to deliver and sustain the new age industry. ACMA conducts cluster programmes for its member companies. Today, we have 18 to 19 variants of these programs and about 250 companies are engaged with us. Similarly, we subsidize the skilling initiatives for smaller companies under UNIDO-ACMA-DHI Partnership Programme.
How do you see the rest of the financial year panning out?
Things are rather fluid at this time in the market. We do have challenges – be it on the domestic front, international, commodity prices, or that of the current global shortage of semiconductors. But the OEMs are hopeful that the current fiscal year may be as good as last year or even marginally better, notwithstanding the 3rd wave of the pandemic. Therefore, I would say that the component sector will perform similarly because the silver lining could be the aftermarket, with exports continuing to grow strongly, even if the domestic market may still remain under a bit of pressure.