Carrier Transicold has been an industry leader, providing customers around the world with the most advanced, energy efficient and environmentally sound transport refrigeration solutions, including equipment for vans, trucks and trailers for transportation of fresh and frozen food, pharmaceuticals and other perishables both for long range transport and for urban distribution. Mr. Pankaj Mehta, Managing Director, Carrier Transicold, India and South Asia, provides his perception of domain developments.
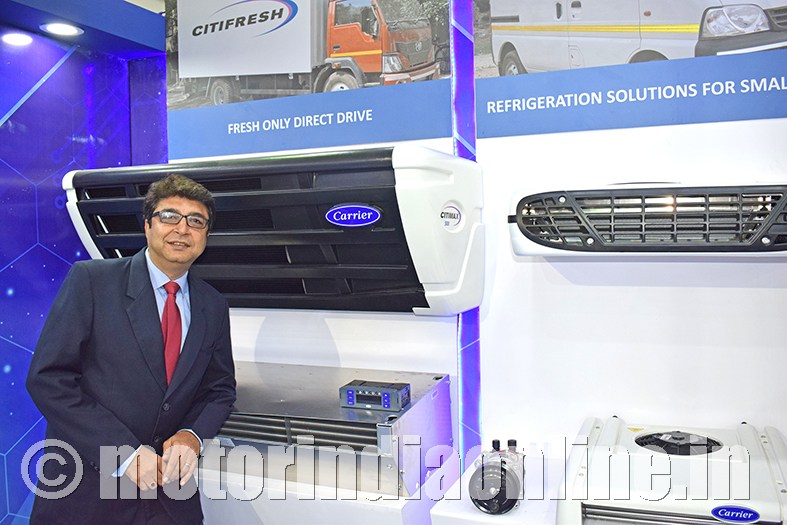
Excerpts:
Brief us your manufacturing program, salient product features & the recent developments.
Carrier Transicold has manufacturing operations in Athens, USA; Rouen, France; Shanghai, China; and Singapore. Global sourcing through a strict quality control ensures that consistent, high quality equipment is produced at all of our factories.
Based on Indian requirements of an affordable and simple solution for transporting chilled products like fruits and vegetables on medium- to large- commercial vehicles, we have recently developed and introduced the Citifresh range of direct drive truck units. The Citifresh range’s robust design and stainless steel evaporator are easy to install and maintain, as well as being ideally suited for demanding applications including high ambient conditions up to 50 degrees Celsius. The range delivers exceptional value by virtue of its low initial cost and lower maintenance and operational costs, while a dashboard-mounted DIN controller offers ease of use.
Inform us the input drive power modes (electric/diesel/PTO) for the unit & the popular models.
Transport refrigeration encompasses several technologies, which broadly fall under Direct Drive or Diesel Drive categories. Direct Drive units are those where the refrigeration compressor is powered by the main engine of the truck/van. Whereas, in case of Diesel Drive, a separate diesel or CNG engine is available for driving the compressor and other accessories. The Diesel Drive units are more popular in India since they are used on medium to large trucks and give flexibility to cover the entire spectrum of temperatures. On the other hand, Direct Drive units are more common for specific loads/temperatures and are installed on small to medium vans catering to local movement or last mile deliveries.
Carrier Transicold has also recently introduced a new generation of engineless transport refrigeration technology, following its 2016 acquisition of TRS Transportkoeling b.v. (TRS). The hydro-electric power generated by a truck’s engine can be harnessed to cut emissions, maintenance costs and help to improve fuel efficiency. These units add a new dimension to Carrier’s range of products and help fleet operators meet their efficiency and sustainability goals, and achieve a sustainable cold chain.
When mounted to a commercial vehicle, the TRS ECO-DRIVE GenSet is driven by a hydro pump connected to the truck’s power take-off (PTO) motor. The hydraulic system drives a generator that delivers electrical power to the host Carrier Transicold unit, without any requirement for the refrigeration unit to use its own diesel engine. Integrated into the hydraulic system is a control unit that ensures the generator consistently runs the same number of revolutions. This maintains constant power, even when the truck is idling in heavy traffic, eliminating any need for the driver to rev the truck’s engine to provide sufficient cooling power.
Highlight product USPs, after sales service & technical support to body builders/end customers.
Cargo safety, efficiency and reliability of temperatures are key to anything that is transported in reefer trucks, Carrier products offer superior technology, advance controls, remote monitoring through telematics, safety devices and automation. For example a driver on a long trip can set the desired temperature and take a break without worrying about any temperature changes. The Carrier unit, when running on standby (electric) mode, is designed to automatically switch to run on diesel engine, in case the electricity fails. The various cooling, heating and defrost cycles are controlled through an advance microprocessor-based controller with other features like sleek design, self-diagnosis, error alarms, high customization managed through an easy to handle cab command.
All Carrier Transicold products come with the security and peace-of-mind of an extensive aftermarket service network. A highly-skilled team of certified technicians, regularly trained in the installation, maintenance and repair of Carrier Transicold refrigeration products, are ready to support the container and box manufacturers and customer fleets across a well-established pan-India network.
Carrier Transicold India works with all stakeholders – including the leading truck manufacturers, insulated box manufacturers and end users – at every stage to integrate the reefer equipment with the vehicle and to install and commission the equipment.
All major OEM’s have chosen Carrier Transicold as their preferred refrigeration partner and our unmatched support is well acknowledged by the industry. We ensure that appropriate refrigeration unit is selected per the desired application requirements. We also work closely with the box manufacturers to ensure proper insulation is done and ensure complete peace of mind for our customers.
With the BS-IV and GST behind, how do you see the demand for reefer vehicles shaping up?
We see all these developments as good moves which will bring more opportunities and positively impact our business. As the cold chain matures we see the demand for larger size reefer trucks and trailer growing along with smaller trucks for the secondary distribution using a hub and spoke model.
What are the growth drivers for cold chain transport and more specifically the reefer vehicles?
Changing customer consumption patterns towards more ready to eat food, higher disposable income and urbanisation are among the key drivers for the cold chain in India.
India is the second largest producer of fruits and vegetables in the world, however a large part of this produce is wasted. One of the reasons for this high wastage could be the lack of robust cold chain infrastructure.
A study by the National Center for Cold Chain Development (NCCD) highlights that Indian cold-chain development is incomplete due to a large gap in form of farm gate pack-houses along with the associated refrigerated transportation. Without these preconditioning centres, the produce cannot be readied for the cold-chain and without refrigerated transportation, there are breaches in integrating the movement in the cold-chain.
To clear the perception that cold chain is complicated and too expensive for business, we recently conducted a pilot study on the impact of the Cold Chain on the kinnow fruit from Punjab.
The study measured the effects of cold storage and refrigerated transport from Abohar, in northern India to Bangalore, in southern India, a roughly 2,500 km (1,600 mi) overland journey that is a four- to five-day drive by truck.
The study demonstrated that investment in refrigeration equipment & refrigerated trucks can reduce food loss by 76 per cent while increasing profit margins up to 23 per cent. As a result, the kinnow selling season was extended by one month, the selling region was expanded 2,500 km, from Punjab to Bangalore, CO2 equivalent emissions from wasted food were reduced by 16 per cent. The impact of the pilot has been in the second year more than 80 refrigerated ocean containers of the fruit were shipped during the year’s selling season, and around 350 refrigerated truck trips were made – up from zero, just two years ago.