Meritor is a market leader in China and expanding in India. In India they already have a leadership position in wheel loaders and are working to increase it further. Meritor is planning to launch new products and expand the product range to provide a complete range of cost effective, new generation solutions for the construction equipment industry. Mr. Kamaljeet Nandkeolyar, Director – Defense & Speciality Business, talks about the segment developments.
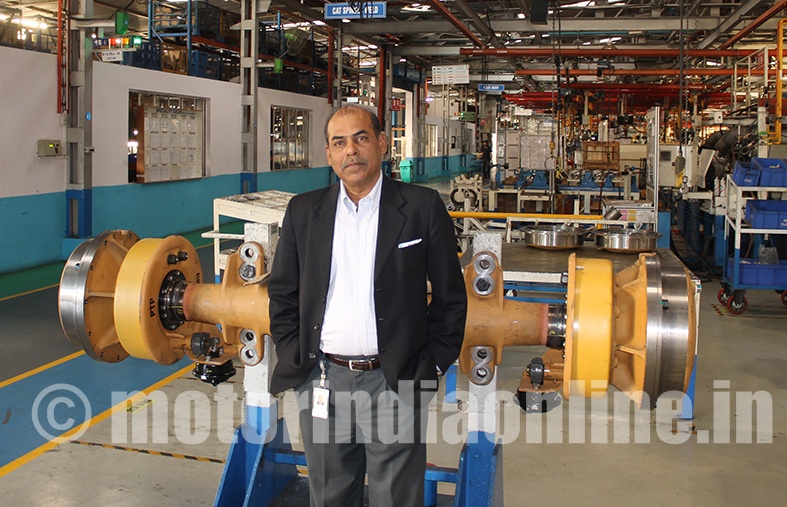
Excerpts:
Indicate the earthmoving segment focus areas & the axles/transmission assemblies supplied for the applications. What are the USPs and your plans to increase the market share in a competitive market?
The segment focus areas vary from country /region to region. The way in which a country has moved towards mechanization plays important role – very specific being the material handling market of the industrialized world vis a vis India. Similarly backhoe loader is dominant in India & wheel loader in China. Focus areas for Meritor India is backhoe loader, wheel loaders, motor graders, cranes, dump trucks.
Talking about USPs, we are market leader in axles for commercial vehicles in the world. We can bring real value product which are not only robust but also cost efficient. We have a well-established organisation with strong capabilities in design, manufacturing and servicing of axles & brakes. We have a wide bandwidth to handle and manage variations and that helps in supporting every customer with their specific requirements.
Brief us the type of co-operation and working arrangement with OEMs in developing or positioning the component/sub-assembly for their application. Also indicate your design strategy and focus areas.
Concept to market – product development process includes application specific – road load data acquisition, target reliability definition, voice of customer -OEM key requirement gathering, product concept evaluation, design, development and testing. We do have a global team focused on CE segment products. In certain case, we involve our global off highway & specialty team to select an existing product and tweak the product to meet the customer specific requirement. The product specifications are frozen jointly with the OEMs and the field testing of the prototype is monitored together. Generally, it takes one to 2 years from concept to commissioning.
Focus areas of product design strategy are modular design, high reliability, shock resistant components, lightweighting, longer maintenance intervals, reduction in oil quantity, high efficiency gearing and lower cost.
What are the special requirements for the mobile equipment applications in general and earthmoving equipment in particular?; and the service support demands / challenges in keeping the machine downtime to the minimum?
The mobile equipment works in a very challenging environment of extreme high & low temperatures, high humidity, high vibrations and dusty atmosphere. Besides this, they work in different terrain conditions and are subjected to a wide range of loads & torque.
We believe the key is to lower the total cost of ownership, this mean superior efficiency, high reliability, minimum downtime, Ease of serviceability & longer service maintenance.
We have a strong aftermarket network across the country and around the world. Part availability is another key for these equipment and we have invested in our channel to support the same. India – aftermarket operations managed centrally from Pune, we have more than 100 authorized dealers, we also partner with the service mechanics and provide them training and tools to service our products. We have specialist service engineers and product specialists, who can provide support too.
Can you comment on impact of rapid advancements in technology, viz., design, materials & process, electrical/electronics, automation etc., on your products?
With rapid advancements in technology, a lot of improvements have been achieved. To begin with the very first stage of product development – In the field of design, a lot of improvement has been observed, notably, among them being increased accuracy of design verification tools & high correlation between real world and simulations. This has resulted in shorter product development cycle time besides lesser validation costs and time. The product introduction is faster since number of iterations & failures are considerably reduced. In many cases, we do not have to repeat the expensive tool development between prototype and production components.
Better material grades are able to enhance performance and lower the costs. Higher strength material and material with better processing capability results in lower weight & results in lower costs as well. Better materials & their processing enhances the component performance and their manufacturing costs. Electrical / electronics and the latest IoT is leading to smarter products within built logic to optimize operation, improves safety and reliability of products. It prevents catastrophic & human error failures.