Company’s major role in bringing ABS technology to India
By N. Balasubramanian
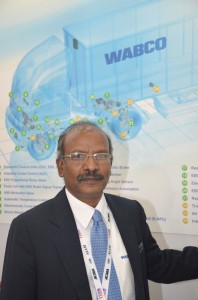
WABCO INDIA LTD., a majority-owned subsidiary of WABCO Holdings Inc, has pioneered manufacture of air-assisted and air brake systems for commercial vehicles in India. The braking expert has been instrumental in bringing the ABS technology to India and has plans to further its efforts to raise the safety standards of commercial vehicles on Indian roads.
Mr. Kaniappan gives us an insight on how WABCO INDIA has developed expertise in the ABS segment and the company’s plans to drive growth into adopting new technology.
WABCO INDIA offers a wide range of products with its focus on the commercial vehicle segment. Apart from conventional products, it also has advanced braking systems, including anti-lock braking system (ABS) and electronic braking system (EBS). The company is vigorously working on advanced braking systems with its aim to bridge the gap in technology between India and other developed markets, such as Europe. Its efforts with respect to ABS have been quite successful with many vehicle manufacturers and fleet operators switching over to ABS over the last decade or so.
ABS technology came into the limelight in the Indian market around 2002 when an ABS-fitted vehicle was considered a premium one. Since then WABCO has been consistently working with OEMs, fleet owners, tanker operators and bus operators, to highlight the advantages and importance of using ABS. A big breakthrough came in 2006 when it was made mandatory for all vehicles carrying hazardous goods, tractor-trailers and long buses to be fitted with ABS. Despite initial resistance, customers have realized the importance of the technology and have gradually started switching over to it. It is encouraging to note that 100 per cent of the vehicles of renowned fleet operators in India like Ranganathan Travels and Neeta Travels are fitted with WABCO ABS.
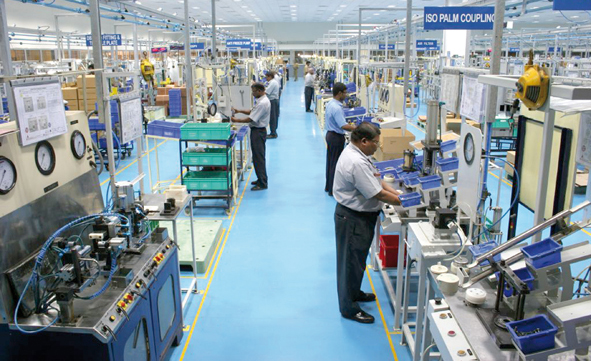
WABCO which is working with all major commercial vehicle manufacturers in the country has 85 per cent market share for ABS systems in the segment. At present, around 10 per cent of its brake systems supplied to OEMs are with ABS, though the figure is expected to go up with increasing awareness and impending safety regulations. Last year, the company made a turnover of Rs. 1,045 crores and expects to maintain its good run in the coming year.
In the aftermarket segment, the company has fitted ABS on nearly 20,000 vehicles, mainly those carrying hazardous goods such as petroleum products. Says Mr. Kaniappan: “We are working with petroleum companies such as HPCL that recommend transporters to go for ABS-fitted vehicles. Every month 500 to 600 trucks are made safer with our ABS. The vehicles are homologated by OEMs and the ABS is given as an option. Retrofitting is done in most of the petroleum transport customers while the trend is also growing in the passenger car segment.”

The company has developed around 140 centres across India to facilitate easy and quick retrofitting of ABS. In the ABS system, the company imports the ECU and some sensors while the valves and wiring harnesses are made locally. It currently makes 20,000 ABS systems annually in the country and has set an annual target of 100,000 systems to consider localisation of the complete system.
WABCO has been actively involved in STU driver trainings and also conducts its own training sessions throughout the country. Over 500 training sessions are conducted in various locations in a year, with a total spend of Rs. 1 crore. Motor-Vehicle Inspectors (MVIs) are also trained to check and inspect vehicles for safety. Apart from the training sessions, a group of drivers, engineers, bus operators, fleet owners, tanker operators are taken to the company’s site and demonstrated the importance and advantages of ABS periodically.

WABCO has four plants in the country, with the unit at Ambattur, Chennai, operating as its mother plant. Another plant in Chennai, mainly catering to exports, contributes about 14 per cent to its total turnover. It has a facility in Jamshedpur which caters mainly to Tata Motors and Tata Cummins and another assembly plant in Pantnagar for supply to Ashok Leyland. The company is setting up a new plant in Lucknow which is expected to be ready by the first quarter of 2013. With an investment of Rs. 15 crore, the new facility will meet the requirements of WABCO’s customers in north India, which contributes around 35 per cent to the company’s production capacity of 100,000 brake systems annually.
WABCO is known for its efforts in research and new product development. The company’s R&D headquarters is located in Hannover, with two additional centres, one each in Chennai and Poland. It is planning to set up two more R&D centres, one each in China and the US. It has a strong R&D set-up in India with around 150 R&D engineers working in its mother plant, apart from another 150 engineers who operate from the company’s software development centre, also located in Chennai. The Indian R&D centre is being further strengthened to function as an extended arm of the German R&D department and will cater to the company’s global plans as well.
World-class test track
WABCO INDIA’s focus is on safety, for which the company has setup a 200-acre test track in Chennai. The facility was established with a vision of bringing ABS into the country and it has certainly played a big role in instituting the technology in the Indian market. The test track is the only such facility in the country and is used by testing agencies such as ARAI and CIRT for certification and homologation of vehicles for safety.
Says Mr. Kaniappan: “The test track can simulate roads of different friction levels based on the requirement during product development. At WABCO INDIA, we design the brake system indigenously, develop, produce and validate it and finally demonstrate it to our customers.”
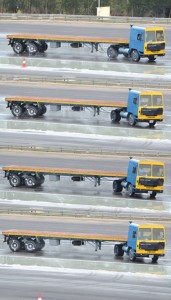
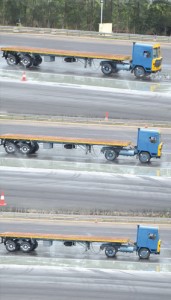
The test track includes a 1.5 km straight track with different surfaces of varying friction, simulating different road conditions for testing. The dry asphalt surface has a friction of 0.8 u while the wet asphalt surface has a friction of 0.5 to 0.6 u. There is a blue basalt surface which has a friction of less than or equal to 0.3 u, to simulate oil patches and slurry on roads and also a wet ceramic surface with 0.1 u friction to model the highways. The facility also has a circular track which will come into full use when regulations on Electronic Stability Control (ESC) and Roll Stability Control (RSC) are implemented, which in turn depends on how and when the relevant products enter the India market.
With a state-of-the-art, perhaps even futuristic, test track, strong technical know-how, global technological expertise, dedicated and experienced workforce, and, very importantly, an aggressive drive to transform the safety standards of the country, WABCO INDIA promises delivery of world-class product and solutions in the years to come. With the commercial vehicle industry in India maturing at a fast pace following the entry of global heavy-weights and the rapid technological strides of home-grown players, WABCO is ready to cater to the entire segment by delivering globally reputed solutions, the Indian way.