In this exclusive interview with Farrokh Cooper, Chairman and Managing Director, Cooper Corporation, Rajesh Rajgor gets details about the company’s operational plan to unlocking, including measures taken on the shop floor, dealing with supply-chain disruptions and actions taken to mitigate the business and virus-driven risks
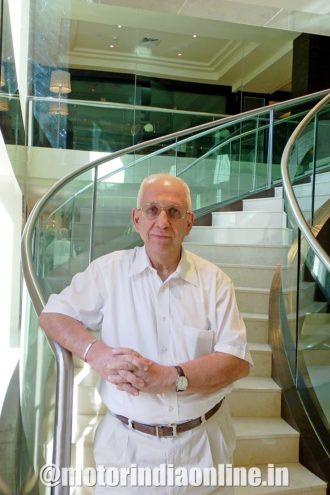
The current situation in India and internationally is acutely uncertain. Even as the corona virus continues to spread across countries, it is likely to lead to production and supply problems for many months. And the economic impact on most industrial enterprises will be significant. “Through our deep understanding of the supply chain, we are helping many in the sector to quickly identify areas where response plans are warranted. By acting early, generating forecasts quickly and accurately, and bridging data gaps, we can manage this crisis through forecasting and stay ahead of the curve,” says Farrokh Cooper, Chairman and Managing Director, Cooper Corporation (P) Ltd.
For the uninitiated, the Satara-based Cooper Corporation, one of India’s leading engine manufacturers, employs majority of locals in their plants and hence is less impacted by the reverse migration happening across Maharashtra and rest of the country. “We are the only company in Satara that has been employing locals for the past 40 years. Hence, we were able to resume earlier than many others. We also paid them salaries despite the shutdown and, in fact, also pay more than others to get the benefit of them returning to work happily,” informs Cooper. The legacy of Cooper Corporation dates back to 1922 when Sir D B Cooper established Cooper Engineering in Satara. The company has the unique distinction of making India’s first diesel engine and iron mould ploughs.
Safety in Revival
It goes without saying that safety is of paramount importance for all the employees and involves strong commitment from the management and line staff. “We believe safety starts at one’s home. All our employees coming to work on bikes have to compulsorily wear safety helmets and they will not be allowed to enter company premises without them. We, at Cooper Corporation, believe that safety starts from the top to bottom and has to reflect in our day-to-day manufacturing practices on the shop floor. I have always believed that human life is invaluable and hence ‘safety first and quality production must’ is the philosophy we abide by,” he states.
The pandemic has given a new dimension to safety systems. Social distancing, usage of the mask and sanitizing hands frequently have become the new additional requirements. “Just like the use of PPE at the workplace, these three requirements are now embedded in our safety behaviour through extensive training and awareness sessions by the training staff and our company physiotherapist and factory medical officer. We have leveraged the IT technology to extensively sensitize on virus-related precautions at all levels of the workforce, including the blue collar workers,” highlights Cooper.
The top-down approach about following safety norms sends a clear message to shop floor people. It helps Cooper Corporation in developing a safe work culture in the organisation. “A safe work culture improves the morale of employees,” Cooper reiterates. However, it will take more than just safety to revive the business. “Business needs continuity. Our overseas and domestic customers need our products just in time. While the domestic demand is slow, our exports have shot up. The economic revival will be a long haul,” he adds. Currently, Cooper Corporation is exporting engines from 8 kW to 228 kW in diesel and gas versions for various applications. In the engine division, Cooper Corporation manufactures an entire range of 2, 3, 4 and 6-cylinder diesel engines from 3.5 KVA to 1,000 KVA.
These engines power applications for diverse sectors including automotive, gensets, marine, defence, construction equipment and agriculture. These engines are designed to meet all the future emission norms. “We have also been working on expanding the engines’ portfolio in terms of power and fuel technologies. The work on CNG has, in the meantime, slowed down and hit due to the extended lockdown periods,” informs Cooper. With a strong focus on automotive components, Cooper Corporation is India’s largest supplier of critical automotive spares like crankshafts, cylinder liners, cylinder heads and blocks, flywheels, etc. Having an extensive client portfolio in Indian and overseas markets, the automotive component business currently contributes to nearly 80% of the company’s overall revenue.
Tackling Pandemic with Technology
Farrokh Cooper is a qualified agriculturist and has led Cooper Corporation in making engines and components. He quotes a saying from the book ‘Principles’: “If you don’t know something, you should find somebody who knows it and obey him.” The tone and quality of an organisation is even more important during the crisis. The automation technology at Cooper Corporation does provide strong multiple safety levels. Interlocked gates, biometric authorisation and mechanical fail-safe safety devices in robotic production lines ensure human safety. Industrial automation provides safety interlocking.
The safety gates using PILZ-type dynamically conditioned monitoring emergency devices and magnetic locking arrangements, IR beam detectors and light barriers well-engineered with automation systems provide strong safety features on the shop floor. Surveillance cameras monitoring plant operations from a single control station provide a means to study unsafe conditions and operations to create safety alerts. It also provides more insights for planning engineering control. There are restrictions on the movement of workers after the corona virus impact, but the severity of this varies from region to region, resulting in different impacts on suppliers and part categories depending on the location of the factory. It has had an impact on the ability of road, rail and marine logistics networks to transfer work in progress between production centres.
“As this continues to be interrupted, finished goods with significant precision components have already begun to signal delays, and it will take time to restart the production chain once logistics begins again. The government now needs to allow people to get back to work for incomes to flow and bring back the economy on track,” Cooper states. Ask him about prioritizing when things are so critical and intertwined – be it supply chain disruptions, troubles in schedules and forecast of business requirements – he concludes: “Rather than prioritizing based on the consequence of supply gaps, it is more constructive to assign a proportionate response based on the ability for the supply to be substituted, either through alternative supply, renewal or fabrication – and all this with discipline and determination.”