The Indian automotive industry is going through a lot of changes. Apart from the legislative shift in fuel from BS-IV to BS-VI and building the eco-system for electric vehicles, the industry is also consciously speaking about energy efficiency, carbon footprint and light-weighting of vehicles. The concerns regarding these have opened up discussions and alternatives of metal to plastics and composites. Here is where the solutions offered by Covestro India come into play. Covestro, globally, has been providing extremely high-performance insulating material that can withstand extreme temperature fluctuations to its clients in the field of automotive, electrical and electronics, construction and the sports and leisure industries.
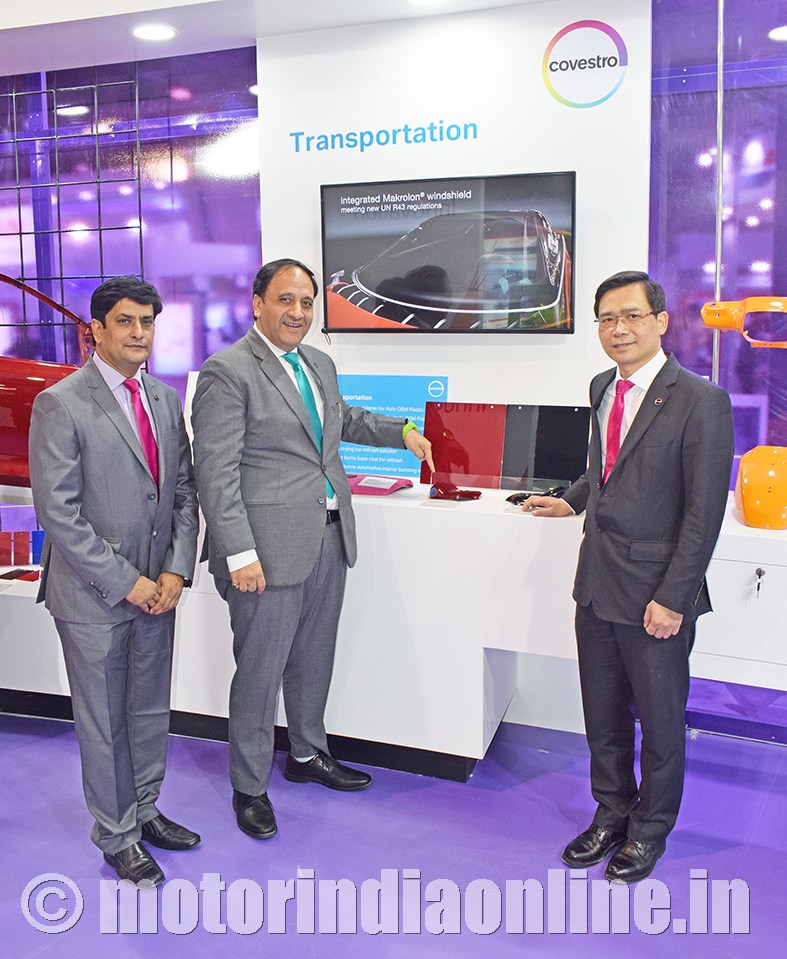
An exhibition conducted by Paint India, where Covestro India was present with one of the largest booths on the theme, ‘Smart City with Covestro Material’, highlighted its portfolio for various industries. Motorindia had an exclusive chance to engage with the experts from Covestro India as well as the global team. “At Covestro, we not only have a long-standing and profound experience in polyurethane, but we can also offer an extraordinary and leading range of proven polyurethane systems from bonding foam for construction to molded foam systems for upholstery to high-performance elastomers for industrial and automotive application,” informed Mr. Ajay Durrani, Managing Director, Covestro (India) Pvt. Ltd.
The German materials giant’s booth had Smart Building & Infrastructure solutions such as PASQUICK™, PU Insulation and PC Sheets on display. Under the Smart Mobility theme, 2K PU coating for composites, Solutions for light weight, efficiency, design freedom and comfort were demonstrated.
Polyurethane was a massive invention years ago. The invention has its significant contribution to the world. The second biggest invention in molecules after it was polycarbonate. These are the two major molecules that are used in so many diverse industries. “These two adhesives have bought so much to the world as on date, and India has to capture the potential of these two polymers. Tailor-made modifications of our broad polyurethanes portfolio are part of our day-to-day business. Our customers get precisely what they need to be successful, namely, customized polyurethanes,” added Durani.
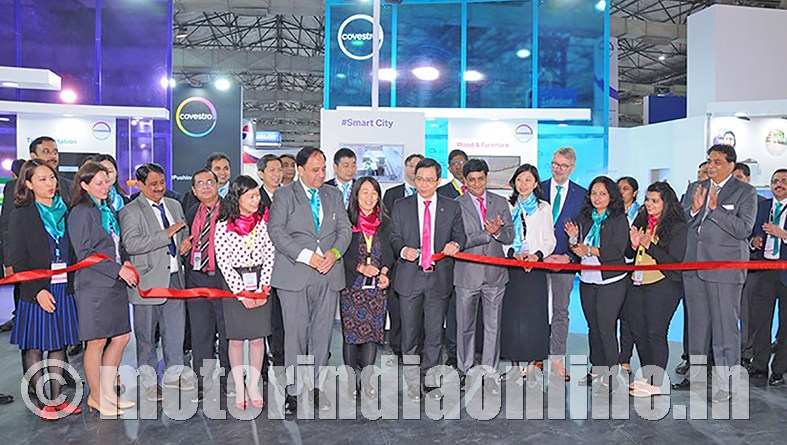
Tapping the potential in India
Speaking about the company’s interest and potential in India, particularly in automotive industry, Mr. Xiaobin Zhong, Sr. Vice President, Coatings, Adhesive & Specialties, APAC, Covestro (Shanghai) Management Co. Ltd., said: “The auto market in India is really big. In 2017 the light vehicle market was around 4 million and, including 2-wheelers & 3-wheelers, it was about 20 million. However, the Polyurethane (PU) penetration is low compared to China, the US and Europe. In the US and Europe, PU penetration is above 40 per cent and in China it is close to 100 per cent, while in India it is close to 10 per cent. There is thus a lot of potential in terms of the size of the market and technological perspective in India. That’s why we are committed for India and have invested in people and technology to bring the latest products and innovative solution to the Indian market.”
The penetration of these products is still low in the country. With application industries such as automobile, wood furniture, construction, etc, upgrading to new technology, the demand for PU-based material will increase, opening up huge opportunity for Covestro. “Increasing thrust on sustainable solutions and government initiatives and schemes such as ‘Make in India’, Smart Cities, Ujaala and Digital India, etc., will provide further boost to the market, and hence we believe this is the right time to highlight our core strengths innovation and sustainability to the Indian market,” said Mr. Durrani.
Explaining the nuances of the solutions Covestro India offers, Dr. Kumar Iyer, Head – Commercial Operations, CAS, India Sub-Continent, Covestro India Pvt. Ltd., said: “When one brings in more composite material into the system or a structure, the best material that is suited for coating is polyurethane and that’s exactly where we come in play. The advantage of using polyurethane is that it can be cured and can be done at a much lower temperature than what other normal technology would need. When you are reducing the temperature from 150 to around 80 you are saving a lot of energy. That’s the reason we see a lot of opportunity for us in India.”
What is exciting is that these coatings do not just enhance the aesthetics but also give functional properties and results into enormous efficiency in the system. “As we reduce temperatures in the production line, we bring in faster turnaround time and also enable the OEMs with the liberty to experiment with different metals, composites and getting in plastics, without worrying about the coating,” added Mr. Iyer.
Covestro made final product is found everywhere, be it on table, wall, vehicles, air crafts, cell phone, refrigerator etc. To tap in the Indian potential the company has manufacturing set-up here in India along with research and development centers.
Manufacturing base
The first facility for Covestro that was acquired in Cuddalore, Tamil Nadu, is dedicated to the production of Polyol with a capacity of 840 tons per annum while manufacturing over 30 different products. In June 2015, it further increased the production capacity of thermoplastic polyurethanes (TPU) to 6,000 metric tons from 2,500 metric tons. The second site at Ankleshwar, Gujarat, caters to coating and adhesives. The third site in Greater Noida comprises of the System House, Eco Commercial Building and the Color Competence & Design Center. The facility is raised over a total area of 77,880 sq. meters with the built-up area being 13,700 sq. m.
Asked about synergies between global production sites and R&D for high quality materials, Mr. Iyer revealed: “Almost 60 per cent of the coating business that we do in India is served by our local plant in Ankleshwar. In terms of what is needed in the market we are adequately equipped and it is fully complemented with R&D. We are a raw material supplier and usually come at the back-end of the value chain. We forward integrate and try and possibly work on solution because we have a lab and development centers.”
Clearly the facilities are set up to understand the requirement of India. “These labs are designed to understand the desires of local customers and show them the advantages of using our products. We are actively working on solutions to participate in the electric mobility space where the question of light weighting, energy efficiency will become even more critical. Our varied solutions in the field of fiber reinforced composites can easily replace metals with much less weight,” added the M.D.
Looking at the current megatrends in the Indian automotive industry, especially towards light-weighting and energy efficiency, Covestro is poised to actively engage with leading OEMs and their partners as part of its innovation and sustainability drive.