Cummins operates its businesses under four major segments – Engine, Power Generation, Components and Distribution. The components segment comprises Emission Solutions, Filtration, Fuel Systems and Turbo Technologies. In India, Cummins Filtration operates as a joint venture by name Fleetguard Filters Pvt. Ltd. All the Cummins business segments work together in creating a whole that is greater than the sum of its parts. Separately, each is a strong and independent business with many of its own customers. Together, integrating innovative technologies with customer demands, they unleash the power of Cummins.
The businesses that make up the Components Segment started globally in the 1950s and in India it was the 1980s. Today this segment in India is a team of over 2,000 employees with eight world-class manufacturing facilities that operate domestically and globally. Almost 50 per cent of the manufacturing carried out by the Components Segment in India is exported. The team is supported by the Cummins Technical Center India, where 30 per cent of the companies worldwide engineering support is based. This center provides critical research and development delivering next-generation solutions to meet global challenges customers are facing, such as rising fuel costs and total cost of ownership.
The Four Businesses
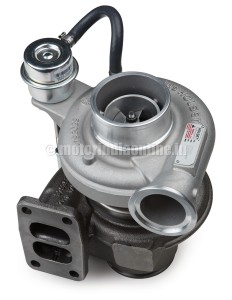
In 1987, Cummins Filtration began its operations in India as a JV, Fleetguard Filters Pvt. Ltd. (FFPL). FFPL is India’s leading manufacturer of light, medium and heavy duty air, fuel, lube, hydraulic filters, air intake systems, coolants and chemical products for all commercial engines with a wide variety of applications in markets, including automotive, industrial equipment for construction, mining, agriculture, marine application and power generation. FFPL has the distinction of being ISO/TS 16949:2009 certified. Its filter performance testing lab bagged the ISO/IEC 17025:2005 accreditation and it became one of the first filter testing facilities to receive ISO/IEC 17025:2005 accreditation in India.
Fleetguard provides a total “value package” of products and services to meet customers’ requirements for extended uptime, increased operator comfort, lower operating costs and reduced environmental impact. Fleetguard India has its manufacturing facility at Pune (Maharashtra), Hosur (Tamil Nadu), Jamshedpur (Jharkhand) and Sitarganj (Uttarakhand).
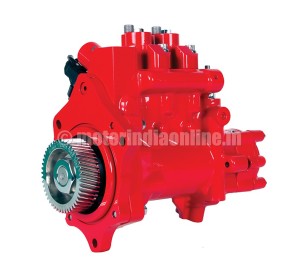
In 1994, Cummins Turbo Technologies (CTT) began its manufacturing operations in India. CTT is at the forefront of engineering design and produces some of the most durable and innovative turbo-chargers to meet global challenges of emission reduction, fuel efficiency and total cost of ownership for engine systems from 2.8 to 120 litres. The company operates under its product brand name of Holset in the aftermarket. The Holset brand is synonymous with turbo-charger and airflow management excellence, relied upon for engineering excellence, precision manufacturing and the reassurance of comprehensive aftermarket support for OEMs and end-users across the globe.
CTT India supplies turbo-chargers to all major OEMs in the automotive, industrial and farm tractor segments. In India, it has its manufacturing facilities in Dewas, Pithampur and Rudrapur. The Pithampur plant exclusively manufactures turbo-chargers and parts for exports. CTT works on a range of technologies including variable geometry (Holset VGTTM), power turbines and two-stage systems. The latest addition to the range is the newly launched Series 200 and 250 that gives high performance while occupying a smaller space.
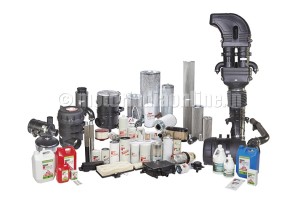
Cummins Emission Solutions (CES) – India was formed in 2008 and launched its first product in India in 2010. CES is a global leader in designing, developing, manufacturing and integrating exhaust, after-treatment solutions with a strong global presence in both on– and off– highway markets, across light, medium-, heavy-duty and high horsepower engine platforms. The business was globally established in 2002 to support the first product for EPA 2007 regulations in North America, and has recently introduced next generation technology for EPA 2017.
CES India, with a team of around 200, works extensively with major OEMs to develop fit-for-market solutions for the domestic market by tackling challenges in fuel quality, duty cycles, driving conditions and after sales service. It develops and integrates complete after treatment solutions, thus serving as a single supply source to OEM’s and taking system ownership. CES is geared up to provide solutions to meet the current and future emission norms for local and global markets.
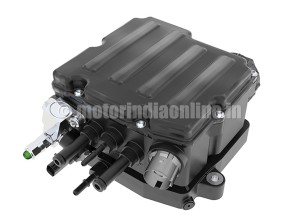
CES India established its manufacturing facility at Pune in 2013 to manufacture EcoFit Selective Catalytic Reduction (SCR) system along with EcoFit Air-Assisted Urea Dosing System for NOx reduction, EcoFit Diesel Oxidation Catalyst (DOC) and EcoFit Partial Flow Filter (PFF) for particulate matter (PM) reduction.
The EcoFit Air-Assisted Urea Dosing System is specially designed for emerging markets, considering OEMs’ performance and durability requirements, while providing best-in-class cost of ownership and ease of integration. It consists of a urea metering module and an injection nozzle, which delivers accurate quantities of atomized air-urea mixture upstream of SCR catalyst where it reacts with the engine exhaust to convert NOx. The system offers better fuel economy, reduced space claim while minimizing urea deposit issues.
Cummins Fuel Systems (CFS) – India began its operations in 2011 through its technical center. The fuel systems business research and development organization is a fully integrated technology team responsible for the design, development, test and support of new, current and remanufactured Fuel Systems products. CFS India has proven capabilities to carry on the complete fuel system development work in India, while ensuring partnership with customer’s engine design team to provide best-in-class solution. It offers products for precise injection of highly pressurized fuel for efficient combustion in mid-range, heavy and high horsepower engine markets.
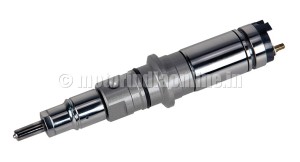
The Cummins Components Segment is a technology and market leader in the commercial engine and related technology components business. It has developed in-house expertise on the critical sub-systems that drive engine performance, emissions and fuel efficiency through combustion optimization, fuel systems, air handling, emissions control equipment, and filtration. By developing these capabilities in-house and with the expertise of their own technical people working closely together, they integrate these technologies more effectively.