Delux Bearings has made significant headway by gaining market share in the LCV and HCV space with existing as well as new customers. The company’s new expansion facility in Surendranagar has been praised by several OEMs and by mid-2017 it should be up and running with a 5,000 sq. ft. testing facility, automated assembly and machining lines and a dedicated tool room. “We have expanded our business development team and now have a battery of dedicated application engineers focused on developments for the post 2020 trucking sector. We are posting 14 per cent revenue growth over last year despite the macro economic turbulence of GST speculation and demonetization,” revealed Mr. Rohan Rathod, CEO, Delux Bearings.
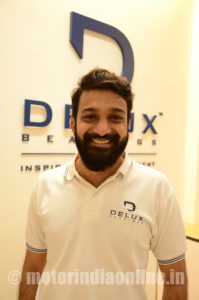
Transformation is the name of the game
Over the years, considerable evolution has happened in the design and manufacturing of bearings and Delux Bearing is not untouched from it. “We are working with 5 OEMs in the CV and PV space on the development of hydraulically actuated clutch bearing technology. This technology is extremely sensitive and delicate that reduces pedal efforts by up to 30 per cent. In India, we would be the first privately owned bearing company to commercialize this technology and there are a only a handful of companies in this space globally”, beamed Rathod. Quite understandable as to even convince OEMs to start developments takes a lot of effort and Delux saw it all. “It took us a good part of the year to convince OEMs, however, with a dedicated application team, road map of investment into testing, CAE, digital simulations and the passion to innovate, we will be commercializing this product 18 months from now,” expressed the CEO.
There is a lot of technological transformation happening in the business, and particularly about the new generation clutch bearings. “These bearings come with engineered grease, layered sealing technology and high-performance plastic hybrid components that outperform their predecessors. We have just recently commercialized an extremely value engineered mechanically actuated withdrawal bearing for the 380 dia. Clutch application for HCV. Although we have been manufacturing this technology for quite some time, market forces drove us to develop the part at almost 20 per cent of the cost whilst improving reliability and performance drastically. Recent field tests of pilot lots reveal that the product compares with a part that is fresh off the assembly line!”, he exclaimed.
Testing and validation
We understand that several problems can occur in the bearings and in the entire drive-line when the temperature increases. Delux Bearings undertakes a whole lot of testing before the bearings are packaged. The test includes, H.A.L.T. (Highly Accelerated Lift Testing) for 2.2 million cycles, Mud and Salt spray tests, Fatigue Tests (for specific failure modes, e.g., Brinelling), Temperature rise tests, etc. Similarly, coatings are also reported to play a significant role in enhancing bearing life. Although Delux Bearings is not too much into specialized coatings, it does use them in its products in a small way. “We utilize dry lubricated molybdenum sulfide coatings (mos2) to reduce metal to metal contact on some of our clutch bearings. Tests are conducted to ensure the thickness layer of coating is maintained within limit (up to 10 – 15 microns) and adheres uniformly to the surface,” he informed.
Since the commercial vehicle sector has start adopting light-weighting and hybrid technologies, to come up with more sustainable and greener technology. Delux Bearings is leaving no stone unturned in this area. “For the LCV segment, we are working with sheet metal bearing raceways (as opposed to solid steel forged or rolled raceways). In doing so, a weight reduction up to 35 per cent is possible without compromising on the load requirements of the bearings. There are further tempering and hardening techniques that can be utilized to eliminate pre-machining process altogether and that’s where we are headed. Historically, most clutch bearings for commercial vehicles are quite bulky as they come from a very western design sensibility – borollic, massive, heavy and tough. However, the eastern sensibility when it comes to these parts (and probably all other parts) leans more towards agility, elegance and lightness. We have developed more than 450 types of clutch bearings for the East and West so this comes to us naturally. We are using a lot of cold rolled sheet steel to substitute castings and forgings in the bearing housings as well. Highly neutral engineering plastics of course are also being explored for housings, retainers and even raceway contact pads,” explained Rathod.
Being attentive to growth and acknowledging it, the CEO added: “Most growth will come from the aftermarket as we scale distribution from 100 dedicated distributors to 200 pan India. We are looking to boost manufacturing by another 50 per cent to achieve certain economies of scale whereby unit rates come down, making us more competitive. But the growth will also include new products such as the CSC, Engine bearings and Transmission bearings.” Notably, the company’s share from aftermarket is 40 per cent, OEM (Domestic) is 30 per cent and that from exports is 30 per cent. Such a share has helped the company grow each year.