With the introduction of the manual, economical and simple EcoDry X as a new filter system and counterpart to the established fully automatic EcoDryScrubber, Dürr Systems has completed its portfolio for dry paint overspray separation. The product family now facilitates differentiated technical solutions for the series painting of vehicle bodies ranging from fully automatic to semi-automatic.
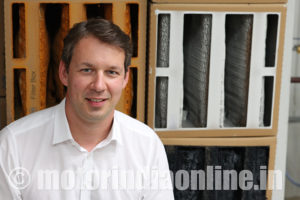
In this interview to MOTORINDIA, Mr. Jens Reiner, Product Manager for Ecopaint Booth at Dürr Systems GmbH, analyses the functionalities of the different systems and reports on the initial practical experiences using EcoDry X.
Excerpts:
Mr. Reiner, what advantages does the new EcoDry X technology offer?
EcoDry X is a multi-stage filter system, consisting of a filter trolley equipped with six filter boxes and pocket filters connected downstream as a secondary stage of filtering. The disposable cardboard filter boxes can be swiftly replaced with minimum effort using the filter trolleys, even during production if necessary. Once the cardboard filters are saturated, the interchangeable trolley is manually undocked and replaced by a filter trolley prepared with new filters. At a ventilated preparation workplace the saturated cardboard filters can then conveniently be disposed of in containers. The system, which can easily be operated by even unskilled personnel, is ideal for both green-field and brown-field plants with a low to medium volume of overspray.
As a pioneer in dry separation, Dürr started with the fully automated EcoDryScrubber solution. Can you describe the application scenario for this?
With the EcoDryScrubber we revolutionized paint overspray separation in 2010. This alternative to conventional wet scrubbing represents energy savings of up to 60% in the spray booth, a reduction of up to 80% in water consumption for the supply air conditioning, and completely does away with the need for chemicals. These convincing arguments led to the EcoDryScrubber proving extremely successful on more than 75 automotive painting lines worldwide. Together with the new EcoDry X, these systems form the dry section of our paint overspray separation range, which suits a wide variety of needs and budgets.
‘One size fits all’ is frequently the claim to technical solutions. Are you adopting a different approach by assembling a family of products?
In our experience, efficient painting processes are both individual and customer-specific. For this reason there cannot be one product that fits all applications – also because requirements are changing all the time. When we were developing the EcoDryScrubber, the market was anticipating a fully automated system which regulates itself and operates independently. This demand still exists as before. But, in addition, today there is also an interest in technologically simpler and more economical plants. We are still primarily focused on providing benefits for customers that are derived from their individual requirements. With the conscious decision in favor of a separation family, we are offering our customers expertise for the future.
When planning a paint shop, the number of units per hour is a relevant variable. Is the choice as between the EcoDry X and the EcoDryScrubber also made on this basis?
The throughput is not the decisive factor, but rather the quantity of paint overspray that is generated in the painting process. This depends on the size of the vehicles, the method of application and the type of paint used in each case. As the separation systems differ in their capacity and in the consumption of the filter medium, the volume of overspray is decisive. This makes it clear how important the precise analysis of the parameters is in each individual case, in order to meet expectations exactly.
How does EcoDry X stand out in comparison with other semi-automatic separation systems?
The filter boxes of the EcoDry X set a benchmark in paint separation capacity and filter costs. This efficiency is based on the principle of our technology: not impact separation but filtering is the order of the day. In this way, we also overcome the challenge presented by every paint displaying individual separation behavior. Another unique feature of EcoDry X is the independence and control of costs that our customers have when buying the consumable cardboard filters. This is because the trolleys are standardized, enabling filter boxes from any third-party supplier to be used. We assume that the number of suppliers offering the corresponding filter boxes will rise along with the number of EcoDry X systems sold. This will then lead to continuous development in respect of performance and lower costs.
The EcoDry X has only become available recently. Has any practical experience been gained yet?
The first plant, designed for car body painting in three-shift operation with a primer, base coat, and clear coat process, is located in a plant operated by the Indian car manufacturer Mahindra, south-east of Mumbai. The performance of the beta site production test has exceeded all expectations, above all in respect of its ease of operation. The separation, filter replacement and stocking of supplies each have their own areas, all of which are easily accessible on one level. The optimized sequences make the work safe for the personnel and at the same time ensure stable processes. The operation runs very smoothly. The system automatically shows when a replacement is necessary by means of a signal lamp and visualization on the control monitor. An operator then unlocks the unit, removes the filter trolley with the saturated filter boxes and replaces them with fresh filters, locks the new trolley, and pushes the saturated filters to the changeover location in the offline mode. The replacement is completed within minutes and without any impact on the production that continues to run in parallel.
As one of the early adopters of the new system, what advantages does Mahindra hope to gain from EcoDry X? Are there more success stories?
Mahindra has consciously switched from wet to dry scrubbing. Apart from the simple operability, this change focused on safety at work, the saving of water and energy, and the complete elimination of chemicals from the process. The German manufacturer MAN has also opted for an EcoDry X, partly because of the excellent ratio of replacement costs to investment costs. For our customers it is important that we always regard dry scrubbing as an overall concept. This means that we consider aspects such as the complete delivery and disposal chain of the filter boxes, the fire protection, safety, cleaning, and the air flow behavior in the separation process from the very start and integrate it into the system.