For the Coimbatore-based ELGi Equipments Ltd., the manufacturing sector is indeed the key driver of growth. As a leading air compressor manufacturer, the company products have different industry applications, including in the automotive sector. Though a well-accepted brand in the textile industry, the company products have also become a preferred choice among industries, including foundry, automotive, plastics, etc. The company has sold over two million ELGi compressors worldwide powering business in 70 countries. In energy conservation and cost savings, the compressors are considered the best in the world.
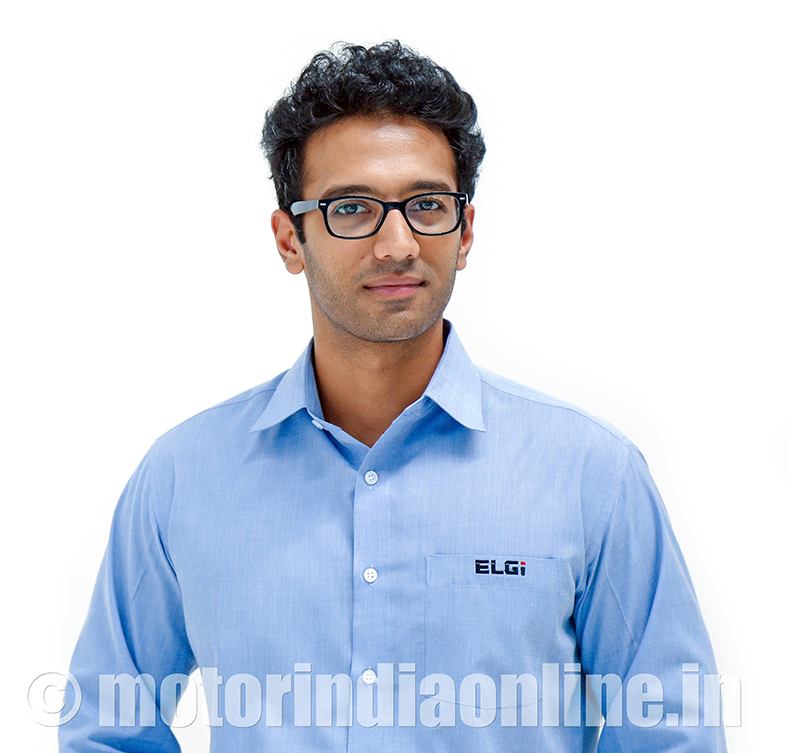
Recently ELGi Equipments showcased “Air Alert”, its Industry 4.0 initiative. This is a SIM card-based communication system that tracks multiple parameters within a compressor, such as operating temperature, pressure, the volume of air delivered and energy efficiency. As a standard, free of cost service, ELGi will aim to have 500 Air Alert devices for its screw compressor range in the field by the end of this current calendar year. The data will be transmitted to ELGi’s servers, where ELGi engineers will review the data and provide meaningful insights to the customer on service intervals, energy efficiency, changes in air consumption and general compressor health. The initiative will elevate ELGi’s customer service by effectively eliminating service delays and compressor failures, which can result in expensive downtime for the company customers.
Air Alert will also provide meaningful field data for the ELGi engineers to address quality concerns real time and integrate relevant changes into ELGi’s product development process.
Earlier in the year, Mr. Jairam Varadaraj, CEO, declared ELGi’s aspiration to emerge the No.2 player in the world by stating that the company growth would be driven with its investments in technology and innovation such as in the Air Alert system.
Commenting on the launch, Mr. Anvar Jay Varadaraj, Head of Marketing and Corporate Communications, ELGi Equipments, observed: “The showcase of our Air Alert system is a significant step in our efforts to be more customer centric and data driven as we seek to provide the most efficient compressed air solutions. Gathering data is easy, but analyzing the data and providing meaningful insights to customers will set us apart. As a quality and innovation centric system, Air Alert will play a key role in our product development processes. The system will provide us objective data on our products’ performance in the field, making it a valuable tool for our quality and product development processes. Fundamentally, Air Alert is about elevating our customer service, and by providing it free of cost, we will emphasize our Always Better brand promise to our customers. We aim to have the 500 Air Alert equipped machines by the end of the calendar year 2017”.
Mr. Anvar Jay Varadaraj, the son of Mr. Jairam Varadaraj, has joined the family business two years back after completing his academic course in the US.