Amongst the many companies at the SIAT Expo, Gestamp was one brand that caught a lot of attention. Gestamp is a Spanish multinational company offering a wide range of forming technologies, in addition to the full range of cold forming processes and advanced assembly technologies such as remote-control laser welding. It showcased its hot stamping prowess. We caught up with Mr. Raman Nanda, Country Head and President – Gestamp Services India Pvt. Ltd., for an exclusive interaction.
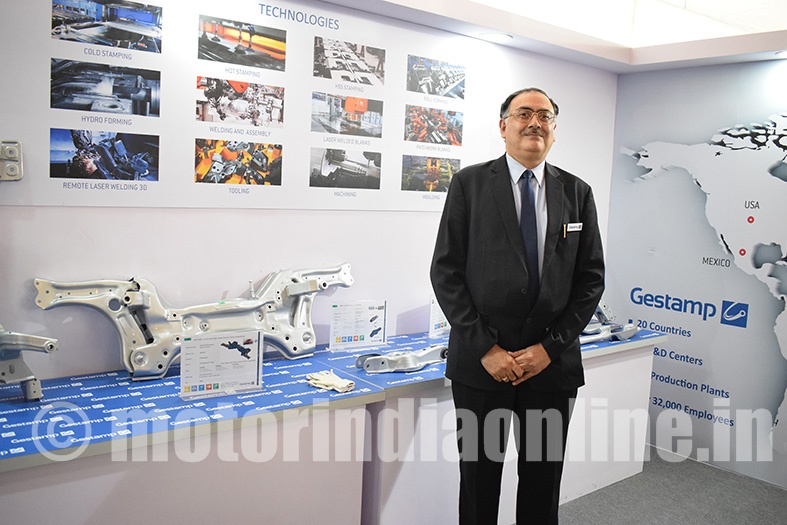
Excerpts:
It is Gestamp’s first participation in SIAT. What is your motive behind being present here?
The automotive industry has always been on an exciting technology development path, as we keep hearing about newer technology innovation such as driverless car, and hybrids engines. What better technology platform can one have than the 15th edition of SIAT organized by ARAI which is completing 50 years. It is a privilege to be here and showcase our technology to Indian OEMs. Since the government has changed a lot of laws and regulations, even OEMs are looking for safer, lighter vehicles; crash law has changed, fuel efficiency norms have come in, emission norms are announced and Bharat NCAP is coming; so suddenly there is more emphasis than ever on body. We being a high technology metal part producer thought this is the right time and platform to showcase our potential. Many of our meetings with visitors have resulted in companies showing interest to visit our plant.
What advantages do you bring to the table with your know-how and solutions?
Our motto and tagline say, ‘For a safer and lighter car’. Our technology focus therefore also moves in that direction, especially in material. Hot stamping is our very big focus. That’s a game changer for us as well as the industry. With hot forming, steel at 500 mpa, after a process of hot forming, becomes 1500 mpa in terms of hardness. So, where 1.6 mm thickness steel is used, we can easily replace with 1.3 mm steel which is a clear 20 per cent reduction in weight of the same part. Besides, it gives a lot of design flexibility that one can’t even think of in cold stamping because in hot stamping the material is like in a plastic stage.
We offer our clients an extensive product range, primarily produced from steel, which are integrated into vehicle bodies, thus defining their structure. On the show is the bumper, which typically is made in seven parts by an OEM but we have made it in one part – an 86 per cent reduction in the number of parts.
Hot stamping involves the heating of the steel blanks until they are malleable, followed by formation and then rapid cooling in specially designed dies, creating in the process a transformed and hardened material. Because of this ability to efficiently combine strength and complexity, press hardened parts accomplish in one relatively light-weight piece what would typically require thicker, heavier parts welded together in more than one process under cold stamping.