GGB helps create a world of motion with minimal frictional loss through plain bearing and surface engineering technologies. With R&D, testing and production facilities in the United States, Germany, France, Brazil, Slovakia and China, GGB partners with customers worldwide on customized tribological design solutions that are efficient and environmentally sustainable. GGB’s engineers bring their expertise and passion for tribology to a wide range of industries, including automotive, aerospace and industrial manufacturing.
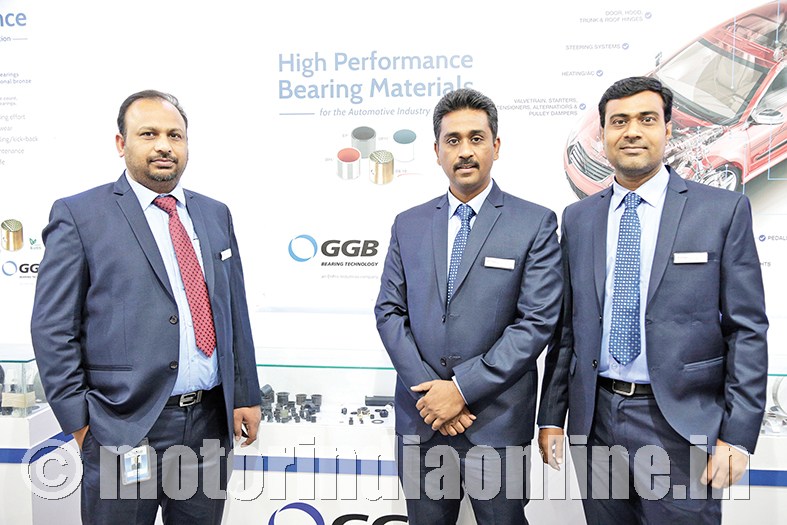
GGB’s self-lubricating bearing solutions have been enabling trucks, passenger cars and two-wheelers to run smoothly for a long time. This century-old company began its operations in India in 2004 and is importing the plain bearings and supplying to their Indian customer base. GGB’s world-class manufacturing facilities across the globe are certified to the industry’s highest quality and excellence standards and boast of global network of sales offices and distributors.
Mr. Mahesh Thangamani, India Sales Manager, said: “We manufacture specialized bearings which are used by every OEM. As a solution provider, we study the application and then offer complete solution to our clients and work with our customers already in the design phase. We help those customers who use conventional roller and plain bearings to re-engineer and then use specialized polymer bush bearings by giving them cost benefits as well as performance advantage.”
The tough Indian customer
Initially, GGB found that the acceptance in India was difficult since many customers follow designs given by their global partners or parent companies. He admitted: “Quite honestly, it’s only after repeated attempts that the Indian clients understand the unique package of technical expertise, tribology and application expertise we are offering, especially when they have cost pressure and are looking for alternatives. It is then that they accept our proposals. For example, the transmission shifter fork is an application where people conventionally use linear bearings but customers have now shifted to our DP4 bearings and have benefited from cost savings and better life of their vehicle transmission.”
The unique advantage that GGB offers is that their bearings use PTFE polymer with proprietary fillers which offers low friction values and gives good operating performance in lubricated as well as dry conditions.
Talking about the new range of bearings, Mr. Thangamani explained: “We have a machinable version of metal polymer bearings – DTS10 which can be machined to tight assembled ID tolerances. GGB provides complete PTFE tape lined machinable version, free of metal contact in sliding area which is unique and provides extremely low friction. We are currently importing these from our global manufacturing plants and catering to our customers.”
Cost – the big challenge
Success means challenges need to be overcome. GGB finds cost-sensitive Indian market as one of the key challenges. Mr. Thangamani shared: “When we approach Indian OEMs, our focus is the application that they have in mind and how our clients can work with their parameters using our bearings and thereby improve or upgrade to the next level. We suggest changes and recommend using relevant parts, and we always work towards bringing value to them. Some percentage of customers prefer local references, and are not readily open to experiment but try to follow which is already available in the market. There are some other OEMs who are more open to experiment, are responsive and have improved their system performance using GGB tribological solutions. They understand that Indian customers are now more conscious of comfort as well.”
The great EV impact
With EVs on the horizon in India, the impact is real for GGB and they have adopted proactive response approach. Mr. Thangamani observed: “We are studying the global impact and evaluating, and we have found that it is different in different countries. For example, China is jumping straight to electric mode, Europe is mix of hybrid and electric, while in India though the vision is there, progress is yet to be visible. GGB has experience of working with many Tier-1 customers who develop components for e-mobility such as electric pumps and cooling pumps. In India, like around the world, we are ready and capable with products for EVs. For example, take planetary gear mechanism in transmission which we are already working on and supplying, because for us the products will remain the same while only the application will differ. So, for GGB, hybrid means more opportunities while battery-operated translates into relatively fewer opportunities. Everything depends on how the market evolves.”
Not to forget the transition to BS-VI, which again is considered a good stage to achieve by GGB because the BS VI-compliant vehicles will bear parts and have functions for which GGB will have bearings ready to use.
In a nutshell, the market may evolve and bring forth many a challenge, but GGB will be ready to cater to any need with its range of products that are a class apart.