When one thinks of adhesives, Henkel is probably one of the first names that comes to mind. In general, the name is more synonymous with beauty, laundry and home care. In the industrial arena, Henkel’s adhesive business is divided into four strategic business units (SBUs), of which one major vertical is that of transport and metal business. Henkel set foot in India in 1997, and now it caters to automotive, aircraft and aerospace and metal processing industries at the global level.
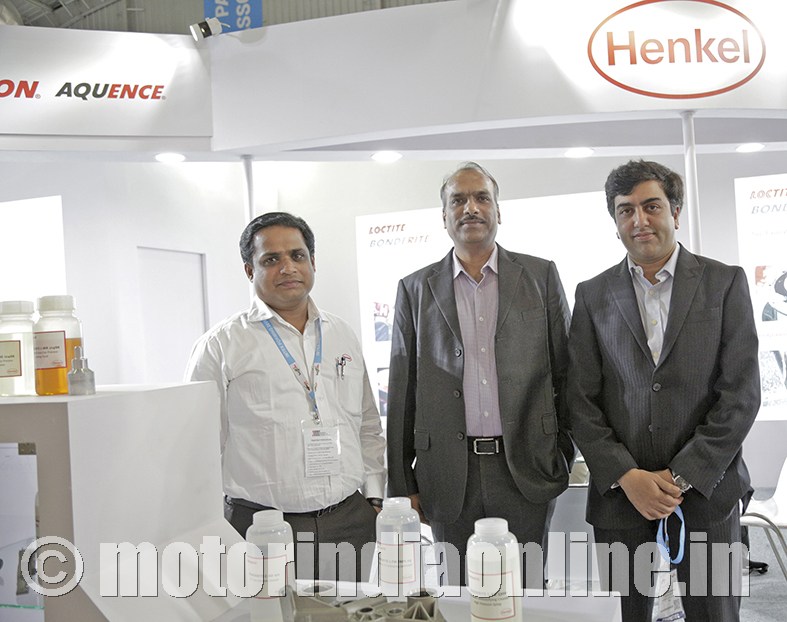
Mr. Kumar Venkataraman, Market Development Manager, Transport & Metal SBU, shares: “Globally we have on offer adhesive products for surface and functional coatings, besides surface treatment of the parts. We cater to all the OEMs and their auto component suppliers both in India and overseas along with Tier-1 companies.”
Sticking right
Henkel has an innovation center in Pune, inaugurated in 2013 with roughly 100 R&D engineers working on new technology constantly. Its most popular adhesive brands, Loctite and Bonderite, are built to provide high crash durability and offer fast curing, making them sustainable products suitable in automated applications in automotive production.
He says: “We supply to all customers from the power train technology, surface treatment of the body to the lubrication of the parts within a vehicle. When we come to the NVH or the body part of a vehicle, we have structural technology solutions which can help our OEMs to achieve the NVH levels that they want. We have sprayable acoustic solutions known as liquid applied sound deadeners (LASDs) which eliminate the bitumen part that is high on volatile organic compounds that reduce the NVH levels. The performance of the vehicle also improves in terms of crash resistance, making the body sturdy and helping achieve light weighting.”
If Loctite bonds different substrates, including steel, aluminum and thermoplastics composites to provide high shear strength that is sought after in the automotive segments, Bonderite presents a unique concept in machining and in-process cleaning for the metalworking market.
Mr. Venkataraman adds: “We have an innovative technology that was launched in 2017 known as the Bonderite dualCys process which is a combination of two processes – that of a cleaner and a lubricant. This solution offers high-lubricity, efficient part cleanliness and corrosion protection.”
Storming the EV Castle
Globally, Henkel Adhesives is supporting major EV brands successfully and is excited about India’s push to the EVs. He says: “Since the main mechanism in EVs will be battery operated, we have the capability to cater encapsulation adhesives, spotting application and any adhesive application required in batteries. As and when the OEMs start working on EVs in India, we can work with them from the design stage and offer products specific to their requirements in batteries. As for the body, light weighting and the sturdiness of the vehicle are going to be the major criteria for the OEMs, we have structural solutions such as HDF or High Damping Foam which can help achieve higher performance and strength of the vehicle while simultaneously reducing the weight of the vehicle.”
Henkel Adhesives looks at the overall solution that it is able to offer its customers rather than specific products or solutions. It is helped by global technology that is developed and applied in other markets across the world and then calibrated and used for Indian customers.
Mr. Ashok Konduskar, Regional Business Development Manager, Automotive Component Solutions, says: “Sharing of knowledge helps us address our customers’ requirements while adapting global technology to the Indian market. One such best practice would be in Automotive Transportation or the AT unit where the market segment is divided into power train and chassis comfort segments. Our unique technology for the AT unit would offer synergy between the cutting fluid and cleaner. After much research, we have a combination where the cleaner acts as a topping which means it is not disposed of as a cleaner every couple of months. We are here recycling the cleaner fluid as a topping fluid which saves the overall cost of the cutting fluid. Since it is used at the room temperature, it translates into energy saving unlike other cleaners which need to be heated.”
Henkel Adhesives is poised to open a state-of-the-art facility in Kurkum in Pune dedicated to metal treatment plant. Though ‘small’, the facility will boast of using the Industry 4.0 concept.
For a company which is present in the entire value chain, traditional technology and the customers’ affinity to it is a major challenge. According to Mr. Venkataraman, there is no better option than to make one-on-one connection with their customers at their locations to create awareness about their products coupled with demonstrations.
With the automotive sector, specially the commercial vehicle segment, always on the look-out for better sealants while building bodies, Henkel Adhesives is always in demand with its global high-end solutions.
With its eye on the automotive aftermarket and a total growth in double digits, Henkel Adhesives is keen to firmly establish itself in the Indian market as a ‘total solution provider’ in the automotive sector, be it CV or the passenger car segments.