A rise in demand from industries such as meat, seafood, fruits & vegetables, and pharmaceuticals, and the growing presence of organized quick service restaurants and retail are expected to increase the penetration of cold chain transportation in the coming years. According to expert sources, the cold chain industry is expected to grow at a robust pace of 13-15 per cent annually, owing to a huge demand-supply gap in the availability of such specialized vehicles. The temperature-controlled vehicles are equipped with active refrigeration and are skillfully designed reefer boxes that take care of this special transportation need.
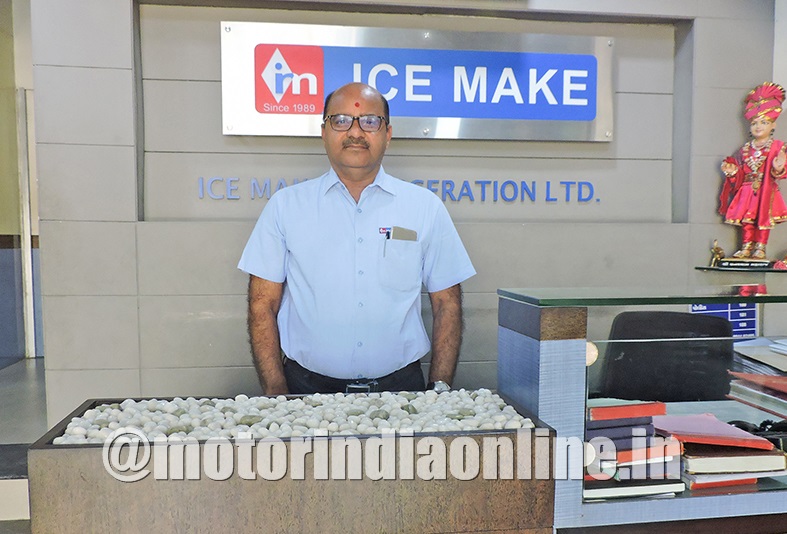
We recently got in touch with Mr. Rajendra Patel, Joint Managing Director, Ice Make Refrigeration Ltd., engaged in the business of providing customized cooling solutions to a diverse set of clients across a wide range of industries by manufacturing and supplying high quality refrigeration products & equipment, to understand the dynamics of the refrigerated containers, their technical prowess and market reach.
During the interview we realized that through its various offers, the company caters to a wide range of industries like dairy, ice cream, food processing, agriculture, pharmaceuticals, cold chain, logistics, hospitals, hospitality, retail, etc. They have made a name for themselves in areas such as the cold room (walk in cooler) with PUF panels, cold room doors, glass door display chiller, condensing units, evaporating units, blast freezer/chillers, industrial chillers, incubation chambers for curd, ripening chambers, pre-cooling chambers, air- & water-cooled chilling plants, ice building tank (IBT), ice cream plant, ice candy plant, hardener, and commercial freezers.
Under Transport Refrigeration, the company provides cost-efficient, value-added solutions for transport of perishable foods with wide range of containers. Mr. Patel elaborates, “We generally have refrigeration-based products designed with HCFCs / HFCs and Ammonia refrigerants for industrial and commercial use. One of our major verticals is to offer total cooling solutions for refrigerated transportation (reefer) reefer vans for milk, fruits, vegetables as well as for ice cream and other frozen products. This includes refrigerated containers, ‘Eutectic’ mobile containers, insulated containers and bunk houses for various applications such as dairy, ice cream, food processing, sea foods, bakery & confectionaries, pharmaceuticals, horticulture/floriculture, hotel-restaurant, retails outlet for dairy – ice cream, logistics, plastic, chemical and biological & research.”
Cutting-edge quality
To deliver quality products for such large variety of sectors the manufacturing capacity of a company has to be cutting-edge. Not only the products manufactured by Ice Make are at ISO certified plants, they are aided by well-developed infrastructure and process to ensure highest quality. “Our manufacturing facilities established on a total 2,96,000 square feet area at Dantali, Gujarat, is equipped with the requisite infrastructure, including CNC, PUF dispensing machine, PUF panel press, fabrication line, laser cutting machine, vacuum table for refrigerated van panel and many others that ensure high quality output in a cost-efficient manner. Our transport refrigeration vertical offers the refrigerated container with size ranging from 8 feet to 40 feet and temperature requirements varying from -25°C to +15°C. We have production capacity of 1000 + refrigerated containers per annum. Our structure of manufacturing is such that we can easily scale up the production capacity based on future requirements,” shares Mr. Patel.
In 2012 when the company started manufacturing refrigerated containers, the outer body was pre-painted galvanised iron sheet (GIPP) and interior with food grade stainless steel finish with MS frame structure. With the advent of new technologies and with an aim to offer lightweight solutions, they started to adopt innovative composite solution by providing GRP outer/inner body with marine ply reinforcement. “Upgrading to GRP ensured higher strength and lower weight of the body. The panels are processed with PU insulation by a vacuum process, to achieve high insulation characteristics. It is finished with aluminium cladding. We offer various options for the floor. The manufacturing process is integral,” asserts Mr. Patel.
Asked about his tie-ups with OEMs and contacts with fleet operator for acquiring business, he adds: “We have tie ups with the leading vehicle OEMs, to offer one-stop solution to their customers for total refrigeration containers. Recently we had executed large orders from the dealers of Isuzu Motors India Pvt. Ltd. and Eicher Motors Ltd. These OEMs have very good feedback from their customers and have seen high market acceptance. The business with vehicle OEMs is likely to grow upwards. Our observation is that these solutions are mutually beneficial to all stake-holders – vehicle OEMs, refrigeration unit suppliers (like Carrier, Thermo King and Hwasung Thermo) and mainly to the user / customers, due to the lower weight and higher load carrying capacity.”
Improving technology
Different technologies continue to have their impact on the transport refrigeration industry. At the recently held India Cold Chain Show we reported many alternate options available for future prospects of cold boxes and some that are adopted already by the industry. Some of them had a noticeable benefit, with respect to thermal energy storage plate, like the Eutectic’ Mobile Refrigeration.
On his company’s road map in upgrading to advancements, he informs: “Eutectic refrigeration offers significant noise reduction benefits as well as saving on fuel. The primary benefit by using Eutectic type refrigeration in containers is to eliminate the need for separate dedicated engine and thus eliminate additional fuel consumption and pollution to the environment. The technology we adapt straight away helps in lesser weight of the vehicle (ULW – unladen weight including container) which saves substantially on fuel for the same weight of goods carried by the normal GI/MS body containers. In other words, it can also help the transporter to load extra cargo by that weight that we save for them.”
While Ice Make has standardized models, the wide extent of applications’ demands customized solutions from the choice of material, uniform density to maintain optimum temperatures to hygiene and cleanliness. “At Ice Make we have full-fledged support team (design, production and service) which enables us to fully address the specific need of our customers. The final products we offer are top-notch with respect to the erosion, pitting and such kind of external and internal damages. Our intensive design and choice of material used in production ensures maximum thermal efficiency and lower operating costs. The seamless and uniform density (obtained by our vacuum press GRP panel process) ensures void-free all wall insulation, supported by aluminum structure absorbs vibration and reduces the cost of damage due to accidents. Further, the van can maintain the specified running temperature with fewer reefer system minutes. Another essential parameter for refrigerated container is its hygiene and cleanliness for transport of food products, pharma products and other perishable commodities. We make sure the all process, from raw material selecting to process of developing insulated box, will be tested by in-house laboratory and by third party to ensure meeting specific demands. Additionally, the external surface is smooth enabling unhindered branding for the customers for their products and services,” explains Mr. Patel.
In a bid to cater to the growing demand for top-notch products the company is geared up to scale up its operation. “Our system of manufacturing is such that we can easily scale up the production capacity based on future requirements. The Reefer business currently contributes to about 10% of our total revenue in 2018-19 and is seen to be increasing. We are also scouting for export orders, and as mentioned earlier, the market scenario, thanks to growing awareness and acceptability of fully built reefer trucks, would offer us scalability and the market a great potential to collaborate with OEMs to offer complete solution for refrigerated transportation,” he signs off.