India-specific transport refrigeration solutions take centre-stage
India Cold Chain Show 2017, one of the most renowned events in the country, held at the Bombay Exhibition Centre during December 12-14, attracted over 180 premium exhibitors and nearly 4,800 high-profile trade visitors.
Organised by Reed Manch Exhibitions, India Cold Chain Show, the 6th edition of the event, demonstrated a stirring range of both national and international companies from various sectors of the industry such as reefer transport, horticulture, material-handling, humidifier & dehumidifiers, freezing and chilling systems, air curtains, cold storage doors, compressors, packaging, data loggers, tracking devices, sensors and others.
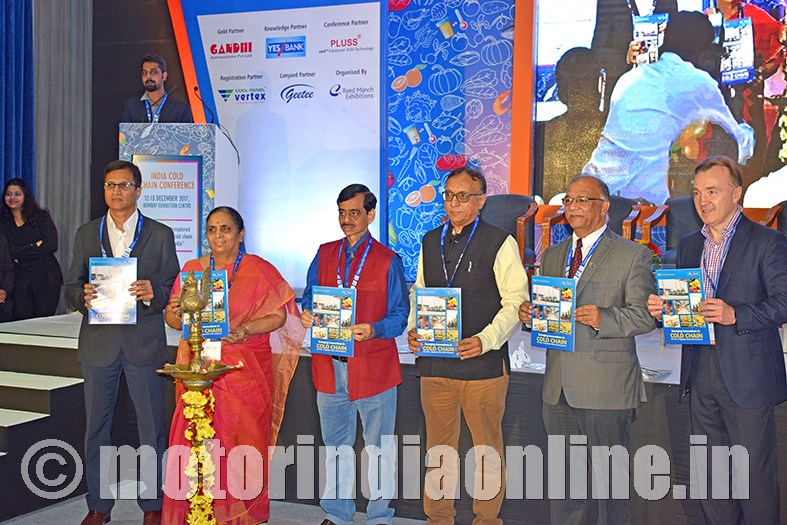
“I am elated to see how the India Cold Chain Show has turned up this time. With new visitors joining in, it is really delightful to see how the event is shaping up in bridging the gap between demand and supply requirements of the Indian cold chain sector. Our endeavour to make the India Cold Chain Show meaningful and fruitful for the participants is surely seeing results,” shared Anuj Mathur, Managing Director, Reed Manch Exhibitions.
Think-tankers’ talk
Keeping up to its promise of always bringing more for its participants, the event successfully held an inaugural conference on the theme ‘Tapping the unexplored opportunity in cold chain business in India’. It was inaugurated by R.R. Jadhav, Dairy Commissioner, Maharashtra, Mrs. Mandkini Eknathrao Khadse, Honarary Chairperson, (MRSDMM), Dilip Shinde, Chairman and Managing Director, Mahanand Dairy (MRSDMM), Ashish Guru, Senior Vice President, Federation of Cold Storage Association of India, and President, Gujarat Cold Storage Association, and Anil D. Gulanikar, President, Association of Ammonia Refrigeration (AAR). Leading speakers from Hindustan Unilever, Burger King, Allanasons, PescaFresh, Tessol, Amul Dairy, Mondelez India, CRISIL, MACCIA, etc., addressed the conference.
The conference emphasised the underlying trends of the cold chain industry and brought together suggestions, ideas and well-debated solutions. Mr. Mithun Appaiah, CEO, Innovative Foods Ltd., who moderated the panel, said: “In India we have approximately 90,000 crores of food wasted a year. This is because most of the cold storage are near the manufacturer and not near the end user. There is lot of scope towards improving last-mile delivery.”
Echoing his sentiments, Mr. Sangram Sawant, Founder & CEO, Pesca Fresh, India’s leading sea food brand, said: “Last-mile delivery special vehicles are needed. Since the delivery silos are big, one company cannot reach everywhere.
Taking the narrative towards a doable solution, Mr. Shaukat Ali Farooki, Director Logistics, Process Foods Division, observed: “QSRs and pharma companies should push this (last-mile delivery) change and bring the technology they use in other countries to India. A lot depends on manufacturing companies too. They should promote physical audits of the reefer fleet to give the right direction to the sector.”
Ms. Binaifer Jehani, Director, Crisil Research, acknowledged: “We realise that cold storages are only in the main States and there is a lot of supply-demand gap. On the agriculture side, around 25 per cent of produce is lost and that is huge for a country like India. We have studied the geographies and seen that most of the warehouses and cold storages are also near the produce and not on the way or towards the end user. There is a need to address this lack of cold storages and have them wherever is required.”
Brianza Plastica focus on Indian cold chain sector
Brianza Plastica, founded in 1962, produces fiberglass laminates for both the industrial and commercial sectors. It keeps expanding production, operating mainly in the construction and cold chain sectors. “Important know-how and expertise acquired over the years and the demand for laminates with better characteristics have made its fiberglass laminates suitable for recreational and temperature-controlled vehicles,” said Dr. Cosima Klinger-Paul, Managing Director, Klinger Composite Solutions Pvt. Ltd., the sole agent of Brianza Plastica in India.
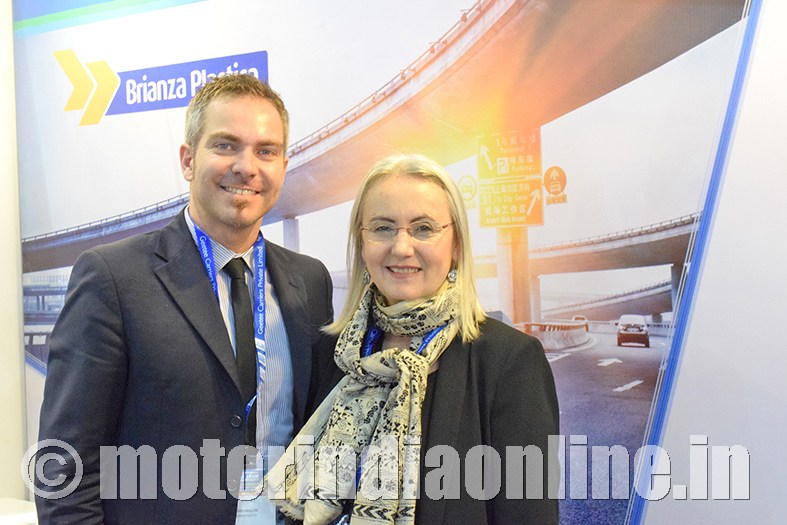
During 2006-2008, the company built two new production facilities equipped with discontinuous laminating technologies and expanded the main production site of Carate Brianza with the introduction of a continuous laminating production line. Brianza Plastica is currently one of the largest European manufacturers of fiberglass. It offers flat laminates made with two production technologies: continuous hot laminating and discontinuous cold laminating. In 2014, it opened the commercial-logistics centre of Elkhart to serve the entire US market and to strengthen its presence in the territory. In summer 2016 a third production site for discontinuous laminates was established in Rovigo, together with a new continuous plant in Carate Brianza. These investments have increased the production capacity by 40 per cent.
Elaborating on the USP of the company’s material, Ms. Klinger said: “Our USP is FRP with the potential of replacing steel used in the cold chain industry. Our sandwich panel technology which is light weight and has corrosion resistance is the right product for the Indian reefer containers. The sandwich panel material can outlive the trucks. We are looking at truck body manufacturers who seek glass fiber reinforce plastic material as compared to steel. One sq metre of steel weighs 7.8 kg whereas one sq metre of FRP weighs 1.34 kg. So the difference is 40 per cent lighter and enables higher payload and saves diesel.”
Clearly a win-win situation for customers who can save a lot on repair and maintenance. “The impact (or a dent) on FRP doesn’t shatter the whole panel unlike the steel panel. It is easy to cut and replace the panel by pasting it with another. We are training our customers so that the they can take care of their customers, as we believe supporting the customers in using and handling the material is also of utmost importance,” concluded Ms. Klinger.
Geete Carriers with Subzero’s Double Deck solution
Sub Zero Insulation Tech Pvt. Ltd., known for its knack of understanding the customer requirements and proposing customized solutions based on specified inputs, showcased a double-deck container for Geete Carriers Pvt. Ltd.
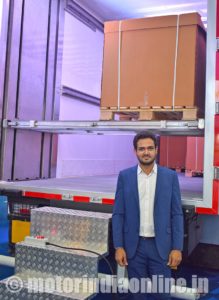
Mr. Nipun Goyal, Director – Business Development Cold Chain, Geete Carriers, disclosed: “When I entered the family business of transportation, particularly the cold chain sector, I realised that to command value in the industry we need to do something unique. While we load the truck there is always space on top, and in terms of the weight it was half filled. Taking cue from the car carrier, we decided to introduce double decker pallet assimilation in the container. We realized it was already popular in Europe and the UK. The customers enjoy the benefit of utilizing the same truck and save on an extra truck and get almost 25-30 per cent saving. The double-deck container is easy to operate and offers 67 per cent more loading space at 30 per cent less transport cost, and 50 per cent less CO2 emission. It can load 22 pallets instead of 12 pallets in standard trucks.”
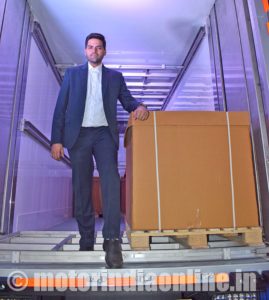
Mr. Deep Khira, CEO, Sub Zero, said: “We are happy to showcase our potential as a unique solution provider and believe that the high quality and the innovative products and offerings are the way forward for the Indian cold chain industry. In the past too, we have proven our metal through projects executed over the last few years, be it light-weight multi-temperature boxes or standard boxes. We are pleased to see growing awareness amongst transporters of product quality and reject anything sub-standard.”
Reefer India adds value with thermal testing solutions
Reefer India which provides multi-level options for the transportation industry and complete cold chain solution presented a host of solutions for the complete cold chain process from walk in cold rooms, multi-level cold storages, refrigerated vehicles, multi-temperature reefer vehicles, insulated porta cabins and other customized solutions as required by the industry.
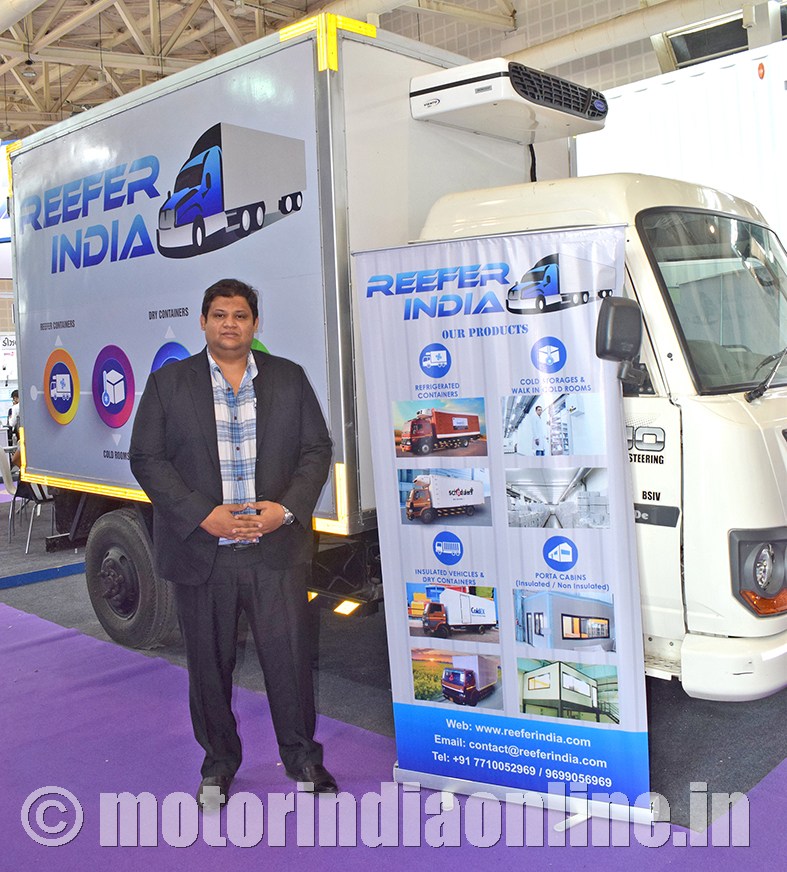
Mr. Swarup Bose, Proprietor, Reefer India, whom we interacted with at the Truck Trailer and Tyre Expo in Gandhinagar, said: “We manufacture 300-400 containers per year at the Taloja facility. This would double to around 800 containers a year once we move to a new facility at Panvel.”
The company showcased a vehicle designed for the pharma sector with multiple sensors in it. “The container has got, three temperature sensors, two door sensors and one GPS sensor. All these sensors are linked to single software, reports of which are displayed on a screen. The idea is to show the output on a single screen as pharma companies really like this owing to its accountability depicting the movement of the truck,” said Mr. Bose.
Reefer India is an expert offering a variety of cold chain solutions and also supports with thermal testing reports. Elaborating on the methodology of the thermal testing, Mr. Bose observed: “We provide thermal images of the containers. If there is any problem with the container like inadequate maintenance of temperature, we get to know whether it is seeping through the roof or the walls. Ideally thermal testing is done in two steps – one by pouring chemicals into the container to check if there are any leakages or any hot spots, and the second is the pre-delivery inspection not given by anybody in India. It saves cost on maintenance with little or no downtime owing to the care taken during the installation of the reefer body. Apart from this, we give 3 years warranty on the container and we encourage them to come every year to have the thermal testing done, so as to further avoid problems if any.”
Trackster Technologies’ ‘tracking’ mechanism
One of the companies that caught our attention was the tracking solution provider, Trackster Technologies. Using the Internet of Things, the company aids in providing on-board vehicle diagnostics, GPS tracking, alerts and diversified reports. “Our 100 per cent web-based vehicle tracking platform provides round-the-clock visibility and control of your mobile workforce by monitoring the status and current location of vehicles, enhanced safety and protection of vehicles and drivers, identification of the nearby vehicle to a current location, historical record and reports of trips, routes, speeds, deviation from routes, driver’s driving behaviour, etc.”, said Mr. Sudhir Bakshi, CEO, Trackster Technologies.
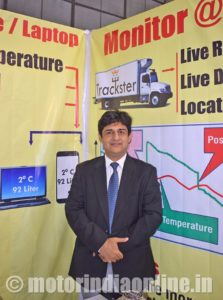
Trackster’s Real Time Vehicle Tracking System is designed to help customers reduce operating costs and enhance business revenues by improving productivity and efficiency. Temperature tracking systems in a cold chain vehicle can help monitor, fuel, freshness of food, vaccines and serums. “Our GPS provides real-time alters during route deviation, zone intrusion and temperature change due to factors such as breakdown. When any temperature difference occurs, the cold temperature tracking system sends alerts, and you can do the needful immediately by finding out the real cause. Reasons such as taking wrong route, bad maintenance or lack of equipments can cause breakdown of trucks. This may result in huge loss. Hence it is imperative to monitor the perfect transportation of goods. This is possible only by installing the cold chain temperature tracking system,” beamed Mr. Bakshi.