Increasing customer variance, e-mobility, cyber security: smart factories are the automotive industry’s answer to current market challenges. Digitization of the production workflow with dedicated software solutions is key. At the heart of smart manufacturing are manufacturing execution systems (MES) that serve as the central data hub which makes the Industrial Internet of Things (IIoT) possible in the first place.
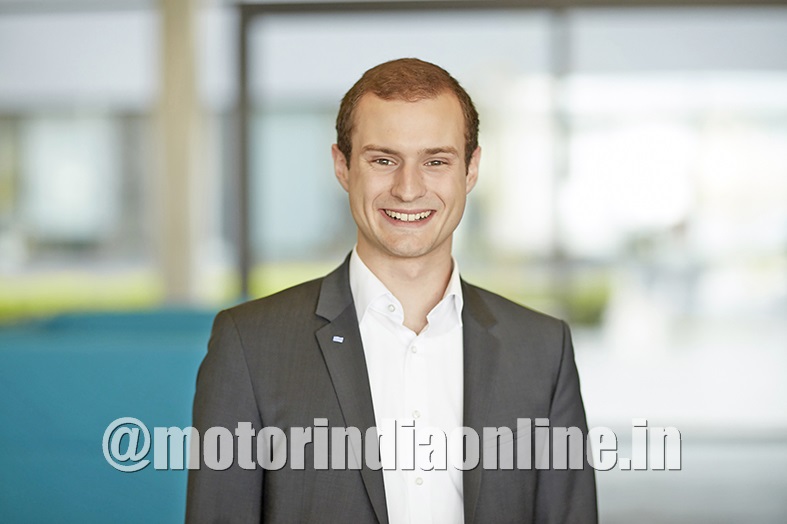
Mr. Felix Losch, a key account manager responsible for the iTAC.MES.Suite from Dürr, explains the benefits of the tailored MES solution for car manufacturers along the entire value chain.
Excerpts:
Mr. Losch, the digital transformation in the automotive industry is linked with buzz words like connected cars or autonomous driving. Looking at the digital transformation from the perspective of manufacturing rather than the end-products, what is the priority for manufacturers?
There is a clear focus on process automation. This is a market-driven innovation, pushed by increasing customization options and high customer expectations. The trend has long been towards lot-size-one – and not just in the luxury segment either. Thus efficiency and transparency become critical to manufacturing control. Convential MES solutions that only address individual functions do not make the cut.
What does a modern MES do?
An IIoT-capable MES covers the complex manufacturing process end to end – from the delivery of sheet metal to the fully functional vehicle that rolls of the production line. With mechanical engineering from Dürr and IT expertise from our software subsidiary iTAC, we developed an improved MES solution based on our proven EcoEMOS control technology. The iTAC.MES.Suite covers the complete production chain by incorporating OEMs and suppliers within one system. This includes, for example, components produced by third party suppliers. In the end, a single, centralized MES can provide the manufacturer with a powerful tool for monitoring, controlling and evaluating production performance. Additionally, the manufacturer can see the global supply chain by integrating several plants into the system in order to monitor and benchmark performance across sites. The first implementations of the iTAC.MES.Suite in the automotive sector are currently underway in several ongoing Dürr system projects in the European market.
How does the automotive industry benefit from a centralized MES?
A big benefit is the increased reactivity to changing production conditions, for example, to ensure better supply reliability to the customer. To achieve this, an Advanced Planning and Scheduling System (APS) was integrated in the iTAC.MES.Suite. The MES components provide direct feedback to the APS in order to create a production schedule that automatically adapts to the state of the production. Simply put, this means that sequences are no longer processed “dumbly”, but rather intelligently adapted to the actual circumstances, for example the unforeseen absence of an employee.
What is a typical application scenario?
Let’s look at the example of two spray booths, one of which unexpectedly malfunctions. In the past, the Enterprise Resource Planning system (ERP) would have known nothing about this and the production target would not have been reached at the end of the day. Since live data from manufacturing is incorporated into the iTAC.MES.Suite, it can perform recalculations in realtime. Thanks to this interaction, optimal production is possible despite the constraint imposed by the malfunction of one booth, for example by redirecting important high-demand bodies to the functioning spray booth. The interface between APS and MES is what really sets the iTAC.MES.Suite apart – a true step towards the digitization of logistics.
Future-oriented software technology needs a large quantity of data, which is generated in the networked factory. This quickly raises the question: how vulnerable is the system?
Software maintenance and support are becoming more and more important, because there are two aspects to the question of security for the automotive industry: secure, highly available plant operation and the protection against cyber attacks. For this reason we are expanding our headcount in the area of support, optimization and testing through globalization in the US and China. The experts who developed and implemented the projects are available via a 24/7 hotline. In addition, the support team continuously reviews the customer systems for security vulnerabilities, fixes them, implements hotfixes, and optimizes databases if the user behavior changes.
Are centralized control systems like the iTAC.MES.Suite only something for newly-built factories?
When Volkswagen in Wrzeœnia (Poland) built a new commercial vehicle factory, the company opted for an integrated MES system from the body shop through to the assembly. In contrast, many existing factories require a great deal of modernization in the area of software. This is also due to the fact that switching to e-mobility requires high investments and the existing factories have increased life expectancy. In the past, paint shops in the automotive industry had a lifetime of 10 to 15 years. Now, the target is at least 20 years. The analytical capability of modern control systems enables precise maintenance concepts and self-learning machines that identify deviations and optimize processes early on. The experience from 180 MES systems installed by Dürr worldwide in the past 20 years has been incorporated into the development of the iTAC.MES.Suite and will contribute in the future to extending the lifetime of technology and automotive factories even further through transparent, efficient control.