The bus body industry in the city of Karur in Tamil Nadu is one of the largest of its kind in south India. There are over 50 bus body builders of different scales, sizes and capacities in and out of the city that cater to the bus body building requirements of stage carriage, staff transportation and educational institute applications. Of the many players, there are some who have made contract carriage bodies, while only a handful have taken up the challenge of competing on the export front.
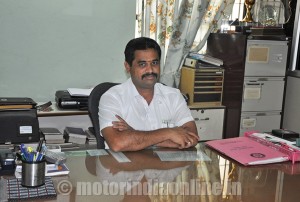
Karur bus body builders cater to a wide customer base right from the entire southern region, extending up to Orissa and even Andaman Islands. The bus bodies are known to be nimble, agile and easy to maintain and offer a wide choice of facias made out of steel and FRP, in addition to providing plenty of customizations in body length, width and seating capacities. It is a known fact that the base for most of the bus body manufacturers in the region is L.G. Balakrishnan and Brothers, a firm from which some employees moved out to set up their own works which have grown big today.
Road safety in India
We are aware that India has witnessed exponential growth in the number of automobiles. The rate of growth is manifold in personal vehicles as compared to public transport vehicles. Unfortunately, the number of roads and road space has not increased in tandem with the vehicular population growth. This has posed a serious challenge to road safety and environment. Road accidents have their negative impact on the economy, public health and the general welfare of the people, and a significant reduction in accident rates is possible only with improvements made in the design of vehicles, operating environment infrastructure, and enforcement of safety regulations and standards.
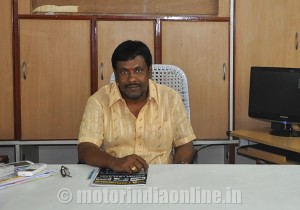
India’s motor vehicle population has grown at a CAGR of 10.5 per cent during 2002-2012 and, consequently, traffic risks and exposures have also gone up. During 2013, there were 4,86,476 road accidents in the country, which resulted in the death of 1,37,572 people and injury to 4,94,893 persons. These numbers translate into one road accident every minute and one road accident death every four minutes.
Incidentally, for the first time in two consecutive years, i.e., 2012 and 2013, there was a decline in the number of road accidents, the number of persons killed and the number of persons injured in road accidents. The total number of road accidents declined from 4,90,383 in 2012 to 4,86,476 in 2013. Not only was there a decline in the absolute number of road accidents in the country during 2013, as compared to 2012; there was also a decline in the number of accidents per lakh population from 39.9 in 2012 to 38.9 in 2013. The number of persons killed in road accidents too fell to 1,37,572 in 2013 in comparison to 1,38,258 in 2012. Still the numbers are far ahead of the normal.
During the last several years, efforts are on, under the aegis of the Ministry of Shipping, Road Transport & Highways, to bring in new regulations to enhance safety. To a greater extent, we are successful in enhancing the provisions in all categories of automobiles, except bus bodies and truck bodies built on drive-away chassis. We are aware that, bus body building and truck body building are carried out not only by a few well-organized sectors but also largely by small-scale industries and even roadside garages. There is a need to implement a Bus Body Code and Bus Body Building Accreditation System to ensure building of buses as per the stipulated safety norms. In order to implement the Bus Body Builders Accreditation System, there is a need to establish a proper system for its effective implementation.
Bus Body Code
The Code of Practice for Bus body Design and Approval – AIS 052 was first discussed in the 10th CMVR-Technical Standing Committee meeting held on July 5 and 6, 2001. The finalized standard was submitted to Ministry for further action and was published in September 2001. Further it has undergone changes with inputs from various stake-holders, including manufacturers, STUs and members of the sub-committee from ASRTU, ARAI, SIAM, CIRT and ACMA. The changes have been duly incorporated in the code and have been released as AIS-052 (Revision-1) – Code of Practice for Bus Body Design and Approval. This revised Code had the formal vetting of the CMVR-Technical Standing Committee, at its 24th meeting held on July 14, 2008.
With all the necessary revisions and changes done, the target date for implementing the code was April 1, 2015, for new design of bodies and October 1, 2015, for the existing design of bodies.
But implementation and the required changes in the existing designs were not so easy. It’s not exactly issues but is a giant leap forward for all the bus body builders to migrate to that level. The reason being, though the buses look jazzy and excellent in designs the industry was little more than unorganized. There are reputed body builders, but still this being more of fabrication industry there were equal and more of unorganized players as well.
When the code of practice was about to be implemented, it required several changes to be done in the design of the body, from the scratch. Structurally, each and every part – from seats to electrical, steel channels to floor materials – needs to be certified. Most importantly, the structure design is to be protected for roll-over protection.
Roll-over protection
The roll-over protection is one of the most important clauses which will rewrite the entire design of bus bodies. The physical representation of the bus (rather the ‘vehicle’ as defined in the Bus Body Code) with predefined requirements will be rolled over in specific test conditions. The bus will be lifted from a platform (subject to meeting various other preliminary test conditions) with angular velocity not exceeding 5 degree/sec. The bus, when lifted, shall not overturn till 28 deg from the horizontal. Post overturn, the subject bus will be ascertained on how the body section absorbs the impact and provides survival protection in the passenger compartment.
With this condition each and every body builder with their designs shall take approval for producing them. Sounds tedious, right? This further multiplies when individual design approval shall be taken for various manufacturers’ chassis and their variants. This now seems next to impossible. So, this being the magnitude of the problem, we spoke to two prominent bus body builders in Karur to know their plan and action to meet the regulation.
Mr. Muruganantham, Managing Director, Pee Tee Coach Builders, recollected a similar situation during 2008-2009 for getting the accreditation from CIRT for bus body building. A panic situation prevailed, and he was one of the forerunners to go deep into the issue, having understood what the actual scenario was and acted accordingly. “We have invested heavily during the times in various infrastructures like paint booth, shower test, min covered work area, etc., to get the accreditation. Likewise in today’s scenario it is not easy as the investment levels go to crores of rupees for design development”, says Mr. Muruganantham.
With these words one could easily understand what could be the situation of various other smaller bus body builders, many of whom are considering quitting the business.
If a company wants to develop a bus body design, it requires CAD images and various chassis details from the respective manufacturers for them to be integrated and checked for the roll-over protection. But it’s known that none of the manufacturers would be in a position to share their designs.
But Mr. Muruganantham is confident of a solution, wherein if the manufacturers come up with basic structural designs and share them along with the chassis, say, giving them the details in coach builders drawing, it will make them build an economically viable body. He also mentions that, with this option in hand, his own identity trademark in the industry can be protected without any compromise in the regulations. Instead, if a group of bodybuilders develops a design, then the bus bodies will look similar, making each player to lose his identity and his price negotiation skills in the market. Only if the manufacturers support them, can the problem be addressed easily, making it a win-win situation for both sides.
Mr. Soundararajan, Director, Maaruthi Coach Builders, echoed the thoughts of Mr. Muruganantham and shared other important points as well.
Mr. Soundararajan is currently speculating how the enforcement authorities will demonstrate their capabilities to check the actual conformance of designs of bus during registration. When there is no proper inspection methodology available at the end-user level, the entire purpose of providing safe transportation and making so much investment is likely to be misused. He wanted 100 per cent compliance across all levels, from certification authorities to implementation authorities, as this is a giant leap for everyone, moving in a new direction.
He also explained that they are planning to take forward the design approval of bus bodies through their association with the help from external agencies. “Economies of scale are very important today, and any further increase in the cost of bus bodies is likely to have negative impact on the business. Since the ticket price is completely controlled by the government, bus operators have a limited say in the matter and will have to deal with the existing fares. With the current on-road price of buses somewhere around Rs. 25 lakhs, any further increase in price due to implementation of regulation will not fetch any additional revenue to the operator, and hence will severely affect their operating economics, thereby having an adverse impact on the complete eco-system”.
His view of an economical solution is possible only if the different stakeholders join hands and that too with the inputs and participation of various bus operators.
The vision of providing safe transportation is encouraging and everyone to try his or her level best to take part in it. This was evident from our interactions. Safe transportation with approved designs is definitely possible, provided the required inputs are shared with bus body builders to arrive at a collaborative solution.