In line with its motto “Creative Systems – Globally”, Knorr-Bremse showcased innovative solutions that make for safe and efficient truck and trailer rigs in an increasingly mobile society.
“Knorr-Bremse commercial vehicle braking systems have proven their absolute reliability in multiple applications on roads around the globe,” said Hinrich J. Woebcken, Member of the Executive Board of Knorr-Bremse responsible for the Commercial Vehicle Systems division. “That said, our existing systems still offer unexploited potential, and we are out to pursue and leverage that potential systematically and creatively. As we do so, we are driven not only by the added value we can offer our customers but also by our sense of corporate responsibility. The shorter braking distance that we have now realized makes a significant contribution in this respect. As the global market leader, Knorr-Bremse offers new tailored solutions in the shape of highly integrated intelligent systems for the continuous overall improvement in tractor unit and trailer alike. The sale of more than 27 million disc brakes is an achievement that speaks for itself, as does winning the Trailer Innovation Award 2015.”
Worldwide investments
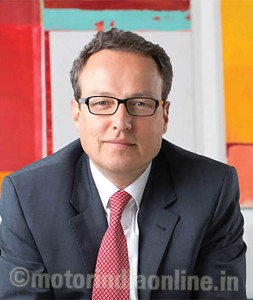
As technology leader in the worldwide commercial vehicle industry, Knorr-Bremse is constantly striving to strengthen its powers of innovation and focusing on the expansion of its research and development capacities in the world’s growth markets. Following on from an extensive €500 million program of investments in the expansion, modernization and maintenance of its production and development facilities over the past five years, Knorr-Bremse is currently building a state-of-the-art testing and development center in Munich, representing an investment of around €80 million.
On approximately 17,000 sq. mtrs. of built-over space, more than 100 test benches are to be set up for the technical testing and quality assurance of components for braking systems and their sub-systems for the rail and commercial vehicle industries. The center will create up to 350 attractive new workplaces for highly specialized engineers and technicians. In all, since August 2013 the group has opened no fewer than seven new production plants in the US, Brazil, Italy, Hungary, India and Australia. These new facilities meant an increase in capacity and efficiency as well as boosting the group’s powers of innovation, enabling Knorr-Bremse to offset the rising pressure on costs and provide its customers with exceptionally competitive systems.
Pre-development project: shorter braking distances
In the context of gradual progress toward automated driving, in a pre-development project Knorr-Bremse has looked into how a further reduction in commercial vehicle braking distances could be achieved. Through systematic component optimization across the entire braking system in tractor unit and trailer, the company’s development engineers achieved the desired improvement without having to increase maximum braking torque. Together with other measures, this led to a measurable reduction in the braking distance of a fully-loaden 40-tonne truck under emergency braking to standstill from a speed of 85 km/h – by exactly the length of compact car. This provides an impressive example of how Knorr-Bremse continues to make the targeted improvements in commercial vehicle systems in pursuit of greater road safety.
By combining the advantages of lighter weight, lower fuel consumption and a longer service life, Knorr-Bremse is constantly boosting the sustainability and economy of its products, creating new resource-efficient solutions – not least for hybrid and electric vehicles. The electrically driven screw-type compressor runs quietly and does not produce annoying operating noise when the engine is shut down. Its energy-efficient conversion of braking energy into compressed air enables annual savings of up to 1,700 litres of diesel fuel. With its high output capacity, this compressor is ideal for large urban buses. The first generation of this screw-type compressor is in series production and Knorr-Bremse is already working on the next generation.
The company’s conventional engine-driven compressors also help to conserve resources: In the compressor with clutch, which Knorr-Bremse has been successfully supplying for several years now, the Electronic Air Control system (EAC) shuts down the compressor by opening the clutch when higher engine performance is called for, such as on uphill stretches or when overtaking. When the engine is on the overrun, on downhill stretches for example, the vehicle’s surplus energy is used to produce compressed air by bringing the compressor back into play. This can lead to savings of up to 1,300 litres of fuel per year.
The new aluminum compressor housing also makes for greater efficiency. The new housing weighs as much as 35 per cent less than its predecessor. In addition, the water-jacket cooling integrated into the cylinder reduces temperatures by up to 50°C. This cuts oil carry-over, improves the air quality and prolongs the service life of the air dryer cartridge.
The EAC-based electronic parking brake (EPB) has entered volume production with the first truck manufacturer and is a role model of safety and comfort. When the vehicle is stationary, the EPB can either be activated manually – by simply pressing a button – or it cuts in automatically when the engine is switched off. Either way, it reliably prevents the vehicle rolling away. Knorr-Bremse offers the EPB integrated into the EAC 2.5 air control system. This not only makes for maximum synergies but also illustrates the company’s ability to develop innovative systems that add genuine value for customers, as the world’s first supplier to bring them reliably to series production readiness.
There is also a stand-alone version that can be supplied independently of the EAC as a flexible optional function. This is provided for customers who have chosen not to configure their system entirely to EAC 2.5. The experts at Knorr-Bremse regularly facilitate further improvements in customer benefits by enhancing existing, proven components and combining them in new ways.
With over 27 million disc brakes produced, Knorr-Bremse sets the standard here in terms of function and quality. With the newly introduced ST7 trailer brake and the next generation of heavy-duty disc brakes at the development stage, the group is set to extend its existing market leadership.
A mechatronic transmission control system newly developed by Knorr-Bremse will be brought to market in 2015 in the next generation of the world’s leading fully automated manual transmission (AMT). The electronic control unit keeps the engine in its optimum operating range, thereby cutting fuel consumption. The transmission control system features a modular design with an electronic control module, a pneumatic module and a sensor module that registers the gear selected as well as the temperature and speed of the transmission. The modular design makes for fuller integration into the transmission and cuts service costs. “With this transmission we provide impressive evidence of our outstanding ability to constantly improve established technologies,” says Bernd Spies, Chairman of the Executive Board of Knorr-Bremse Systeme für Nutzfahrzeuge GmbH.
Another newly developed product is the shifting module for the world’s first dual-clutch transmission in a heavy-duty truck. This makes for rapid shifting within the clutches and the transmission. The flow of power is now no longer interrupted during gearshifts, which means added comfort and convenience for the driver and fuel savings for the fleet operator. Market launch will begin at the end of this year.
The future belongs to scalable brake control systems
“With our modular ABS- or EBS-based brake control systems that are well established in the marketplace, for several years now we have been progressively adding functionalities to our systems and offering additional scalable applications for markets worldwide,” says Spies. “Building on the delivery of more than eight million electronic braking systems and our technology leadership, we offer our customers added value by enhancing the system architecture and reducing the number of different variants. Building on our market leadership, we will continue to integrate functions in the best possible way and further simplify their applications in order to offer increasingly powerful driver assistance systems, all the way to automated driving. We will be adopting this approach systematically in the next generation of our brake control systems, which are already at the development stage.”
At IAA, Knorr-Bremse also presented two new solutions specifically designed to meet market needs in the BRIC States. The specially developed global Air Processing Unit (APU) is a particularly compact modular unit comprising an air dryer and a multi-circuit protection valve. This unit is not only inexpensive but also easy to maintain. Another fully scalable product is the “BRIC TABS” ABS system for trailers, offering various mounting options and a correspondingly attractive price.
To enable more efficient trailer height adjustment, Knorr-Bremse has developed the Intelligent Leveling Control System (iLvl) for trailers. With the iLvl actuator built into the braking system, the system responds more rapidly, and raising and lowering the trailer is much faster now than in the past. The system also features pneumatic control buttons that enable the trailer height to be adjusted even when it is not connected to the tractor unit.
With the Intelligent Trailer Access Point iTAP from Knorr-Bremse, the driver’s smartphone acts not only as a remote control for the trailer but also as a data terminal. Key information such as tire pressures or vehicle weight can be accessed by the driver at any time. In addition, the trailer height can be adjusted or the lift axle raised or lowered at a swipe. In co-operation with TIP Trailer Services, Knorr-Bremse is endowing iTAP with FleetRemote functionality. With this WiFi-based telematics application, information on the vehicle location and the state of the trailer brakes are transmitted to fleet headquarters at regular intervals.
Also on show at the Knorr-Bremse booth was the new ST7 disc brake for trailers. This is currently the lightest two-piston brake for 22.5-inch wheels on the market. Modifications to the calipers, carrier and pads have brought a 10 per cent weight reduction compared to the predecessor model. The ST 7 disc brake was showcased not only at the Knorr-Bremse booth but also by various axle and vehicle manufacturers.
In the past, getting heavy trailers to turn within the prescribed radius called for steered axles. Now, in collaboration with Kässbohrer, Knorr-Bremse has developed an ingenious and low-cost alternative: the Steer-by-Brake system. In place of complex mechanical steering systems, Steer-by-Brake relies on partial load reduction and selective braking of the rear wheels. The driver has no need to switch anything on or off manually and is free to concentrate on the driving.
On the week-end of September 27-28, the reigning European Truck Racing Champion and three-time winner of the series, Jochen Hahn, signed autographs at the Knorr-Bremse booth. Hahn’s race truck was on show in the Knorr-Bremse outdoor area where there was also a truck driving simulator from Knorr-Bremse in which visitors could test their own driving skills.