Company bullish on CV segment prospects
The Madhus name has been synonymous with quality and dedicated service in the garage equipment field in India. The company represents some of the world’s leading brands in the garage equipment space including Hunter, Ravaglioli, Telwin, Texa, Celette, Filcar, Romess, Capelec, Blowtherm and Hanmecson and has instrumental in driving the field’s evolution in India for the last 31 years.
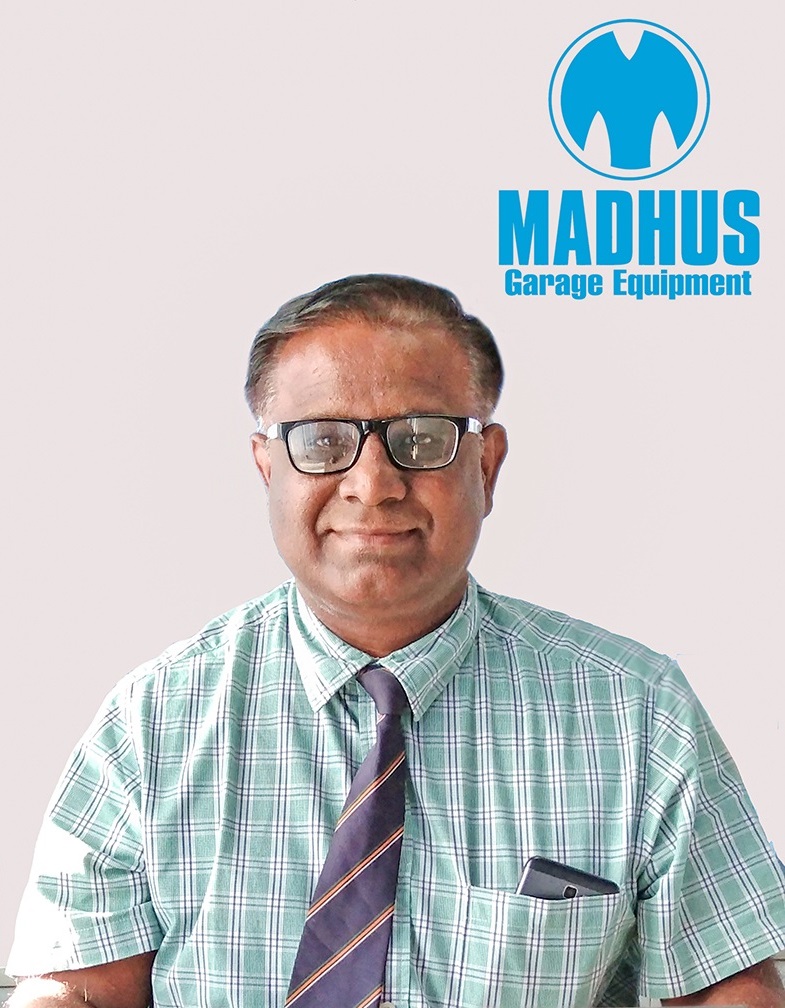
With the Indian commercial vehicle industry going through numerous changes in terms of regulations, product evolution and overall ecosystem, we wanted to understand Madhus’ preparedness for the road ahead and caught up with Mr. Mahesh Keshav, Vice President – Heavy Duty equipment, Madhus Garage Equipments, for an exclusive interaction.
Excerpts:
What are Madhus’ main focus areas when it comes to serving the CV segment? Please highlight the major product lines you offer for the truck & bus space.
Madhus has always been a pioneer in providing quality service and quality products. Our motto is to ‘Bridge the Technological Gap between international countries and India in the field of Garage Equipment.’ The products we choose are from international companies that are best in their segments across the world.
When it comes to the CV segment, our major focus is to improve and increase the tyre life of vehicles, provide efficient and safe equipment with respect to body shops and be prepared for new changes in the industry. For example, we are ready with an AC recharging system from Texa which is suitable for truck cabins and buses. We are also market-ready for other segments like test lanes for fitness centres. We were the pioneers who introduced truck wheel alignment in R&D centres of manufacturers in India way back in 2004.
Our bread & butter is our Hunter Wheel Aligner, made in the US for all trucks and buses. Approved by all major OEMs like Tata Motors, Mercedes-Benz, JK Tyre, Apollo Tyres and others, the product is the benchmark in the industry when it comes to reliability and accuracy. We have also invested in a strong team of service engineers to ensure our users face minimum breakdowns. We also have wheel balancers, tyre changers and nitrogen inflators for the truck and bus segment.
For the growing market of body shop in the CV segment, we have the Telwin Spot and MIG welders along with plasma cutters. We have conducted multiple demonstrations at truck workshops and the response has been phenomenal. The ease with which repairs can be performed is something that all workshops are impressed with.
We also have a range of testing equipment that can be used in Truck Fitness Centres in India – roller brake testers, speed testers, side slip testers, headlamp testers to name a few.
The passenger car industry in India is more advanced when it comes to adopting sophisticated garage equipment to ensure the vehicles are properly serviced and maintained. With more advanced trucks & buses plying on roads, are we seeing a parallel change in the use of superior equipment for maintaining CVs?
The CV segment is changing fast and automation seems to be the way forward. Tyre companies have preferred installing Ravaglioli truck wheel balancers and tyre changers to make their jobs easier. Madhus is also installing fully-automatic Texa AC rechargers at CV dealerships to prepare them for AC truck cabins which have been mandated from April 2019. The Indian CV industry is adopting new technology from Madhus as it helps them increase their productivity in the workshops.
What impact has the transition to BS-IV & the new axle load norms had on the service & maintenance side in the CV segment? How has Madhus helped make the transition smooth for customers? Moving forward, what kind of impact do you think the jump to BS-VI in 2020 would do to your field of business?
With the new axle norms, overloading may be reduced drastically and with the introduction of tubeless and radial tyres as a standard in OEM fitment, advanced garage equipment will have to be used for servicing which will also add to the productivity and profitability of the service centre. While the number of axles has been increased to improve the load capacity, alignment has been made compulsory which has benefitted the end-user to a great extent.
With the introduction of AC truck cabins, AC machines have been made mandatory. With increasing radialization and rotation of tyres becoming a standard service, tyre changers have also become essential in most workshops. BS-VI alone being implemented wouldn’t matter much to Madhus as it is more related to the exhaust emission of vehicles.
However, the overall quality of trucks and buses being manufactured has been going up and this means there is a much larger requirement for high-end quality equipment.
We at Madhus have made it easy for the industry as we are 100% ready with the latest equipment which are required for the Indian market. Dealing with the world’s best brands, we have access to the latest technology while many other companies are rushing to keep up with the changes in the industry. We have been prepared for this since many years and are well placed to make a smooth transition to the new norms.
Madhus has been one of the very few companies in the garage equipment field to try and go pan-India. What is your motive behind trying to be pan-India? How does your geographical presence across the country look like at present? Are you expanding into any new regions?
For a direct connection with the market and customers and to provide good quality products and services, we have developed a dedicated team for commercial vehicles and passenger cars in every region. This would also help us in understanding the requirements locally and provide better services. The users of our equipment are spread far and wide and we have to be close to them to offer prompt service when needed. This not only benefits our customers as they get the best service support but it helps us understand the regional variations across our vast country.
Apart from our Head Office in Bangalore, we have over 30 regional offices across all major cities in India. A dedicated training and demo centre for northern region customers is operational in New Delhi. To serve the OEMs and customers in the western region, we are coming up with a centre in Pune which will be operational in the next financial year. In addition, our Head Office and Training Centre in Bangalore has been revamped and continues to offer training and demonstrations for OEMs and customers.