The Indore-based company is a leading supplier of vacuum-formed (VF) ABS plastic components and interior trims to the commercial vehicle industry, whose speciality lies in robust fixture design and ease of customisation as desired by customers.
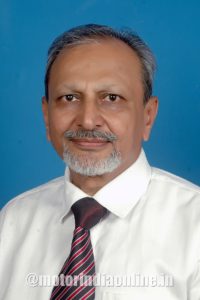
Plastics have made themselves indispensable for automotive manufacturing, finding their ways into every structural and functional aspect of automobiles, especially the interiors. Plastic moulding and trims not merely brighten up the passenger cabins but go beyond mere aesthetics and ergonomic comfort to occupants. Durable and scratch resistant, they limit noise and vibration and play a key role in safety innovation of cars and commercial vehicles.
In recent times, the advent of advanced thermoplastics and formed parts have made significant inroad into the interiors of buses and trucks in the country. They are now commercially viable, while also offering ease of design and manufacturing with seamless moulding and integration of plastic parts. The market standards and buyer awareness on aesthetic and safe interiors for heavy vehicles has also greatly improved.
Growing up in this milieu in leaps and bounds is Migma Packtron, a company that was once started to manufacture industrial plastic products but has later made a strong foundation in automotive interior solutions in the last decade as its mainstay business. Its Managing Director, Mr. Ashok Patankar, delineates his company’s rapid emergence. He said: “We began experimenting some small parts for Eicher, and in 2007, we entered fabricating plastic interior trims for Eicher Buses in a full-fledged manner. Today, we are among the top three suppliers of the OEM despite heavy competition”.
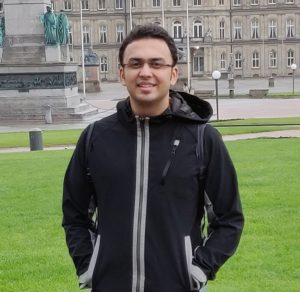
VECV apart, the company is also a prime-time supplier of ABS parts to Ashok Leyland, Azad Coaches, Olectra Greentech and Tata-Marcopolo (to commence shortly), among various other bus body builders in the country. The company specialises in vacuum formed products for buses such as dashboard, door and roof trims, seat back paddings, hat rack sections, interior domes, and so on. “Buses these days increasingly use these products, as they are ideal light-weight replacement to metal and FRP trims and are highly customisable as per the requirements of fabricators for aesthetic and enhanced passenger comfort”, he added.
Why vacuum forming?
Vacuum forming, by far, is the most suitable and cost-effective manufacturing process for the needs of the bus industry, according to Mr. Aditya Patankar, Director – Operations, Migma Packtron. This is because of two key reasons, he says. One, the ease of forming plastics in various profiles and shapes, even in large sizes, in a short span of time. This makes VF ideal for complex and variety of customisations aspired by different OEMs and bus fabricators. Second, quick development time for VF products adds great value to bus makers in a competitive market like that of India.
For the uninitiated, ABS plastic trims for automotive applications are largely made by the process of injection moulding, wherein molten thermoplastic granules are poured into dies of desired shape and design. However, in vacuum forming, ready-made sheet of plastic (made out of the same thermoplastic granules) is heated to a forming temperature and stretched onto a single surface mould and pressed against it by vacuum created.
Mr. Ashok Patankar explained: “VF is desired only in those product lines where demand is limited, and investing on die-casts for injection moulding can be expensive for producing limited volume. Beyond a certain threshold, VF becomes less desirable, and so interior trims for passenger cars and other high-volume applications are seldom made in this method”.
He pointed out that since the average demand for buses is not more than 1,000 units per month for an OEM and even less for body fabricators, along with a plethora of customisation, vacuum formed products are greatly sought after.
Further, Migma Packtron provides quality FRP to ABS conversions that come with light weight components and offer precision fit. The company has innovated ‘under-cut forming’ and has also developed a new concept of ‘snap fit’ components with unmatched benefits like instant fitting and removal, no visible hardware on surface, aesthetically attractive, and cost effective, which are highly desired by bus makers. For effective production, Migma has devised its own VF machines in-house, which are claimed to be state-of-the-art and can make a product as big as 3 metres by 1.7 metres, equipped with all latest technologies available in the field of vacuum forming.
Blue-sky future
“Aspiring to desired perfection in bus interiors, we have plans to deploy Robotic Arms in the process. We are already negotiating with some European companies in this regard”, Mr. Aditya said, while adding that the company has established a shop floor space of 25,000 sq. ft. to meet the increasing demand projected for the next 10 years. The company is also eyeing a massive expansion of production in the next two-three years. “We have secured an industrial land of 40,000 sq. ft. at a prime location in Indore for a second unit. Diversification in the field of injection molding will take place at the new plant”, he noted.
Speaking on the future prospects, the directors see their company growing with a lot of opportunities in the domestic bus industry. “With a growth of nearly 30 per cent in the last financial year, we are proving to be one of the emerging players in supply chain of the industry, and are now recognized as a vacuum forming expert. We are constantly enlarging our customer base, and our marketing team is working on a couple of proposals from overseas markets as well”, averred Mr. Aditya. “With expansion in product demand and customer base, we anticipate excellent opportunities in the aftermarket or replacement space as well”, he added.
The guiding force
The guiding force and brain behind Migma Packtron’s success is Mr. Nitin Raut. Known for his creativity and penchant for perfection, Mr. Raut has a vision and mission to take Migma to great heights in the global arena. Each and every machine functioning at Migma, be it for trimming or forming, has been made in-house by the veteran using his unparalleled intellectual skills and over 35 years of experience in the field.