
The team at Mahindra extensively uses simulation apps to accelerate their product design process and foster a culture of collaboration
Product design for modern-day automotive manufacturers is an iterative process that requires collaboration between computer-aided engineering (CAE) analysts, design engineers, the manufacturing team and the suppliers. As new vehicles are introduced at an accelerated pace, efficient collaboration is needed to streamline the iteration process and maintain a competitive edge in today’s consumer landscape. One of the main efforts for a company like Mahindra is to renovate their processes while ensuring the quality, safety and reliability their customers have come to expect. Instrumental to the team’s success are simulation apps used to make the design process more inclusive and robust.
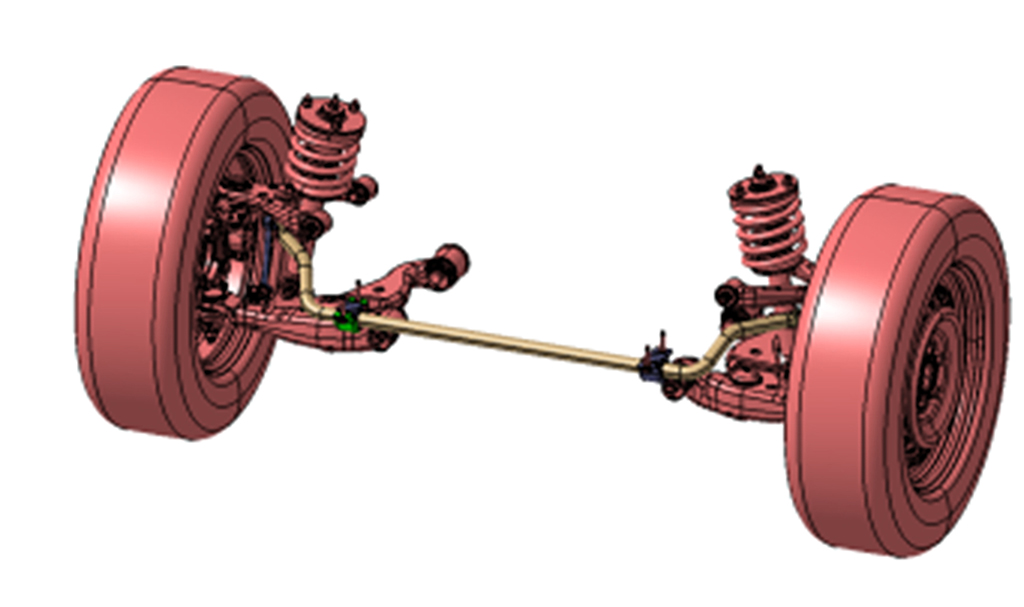
Challenges during Product Design
Collaboration can be a time-consuming process that requires different teams to consolidate their expertise in a meaningful and efficient manner. Design engineers demand evaluations of new concepts or adjustments to existing designs, which can be hard due to the complexity of the physics involved. CAE analysts, however, have the simulation expertise to manage high levels of complexity. They can provide assistance with concept evaluations through detailed CAE analysis. But with a limited number of analysts and an increasing volume of requests, these evaluations can be difficult to obtain in a timely manner. The design lead time for a particular vehicle component varies with the number of back-and-forth iterations required to finalise it and can take months in some cases.
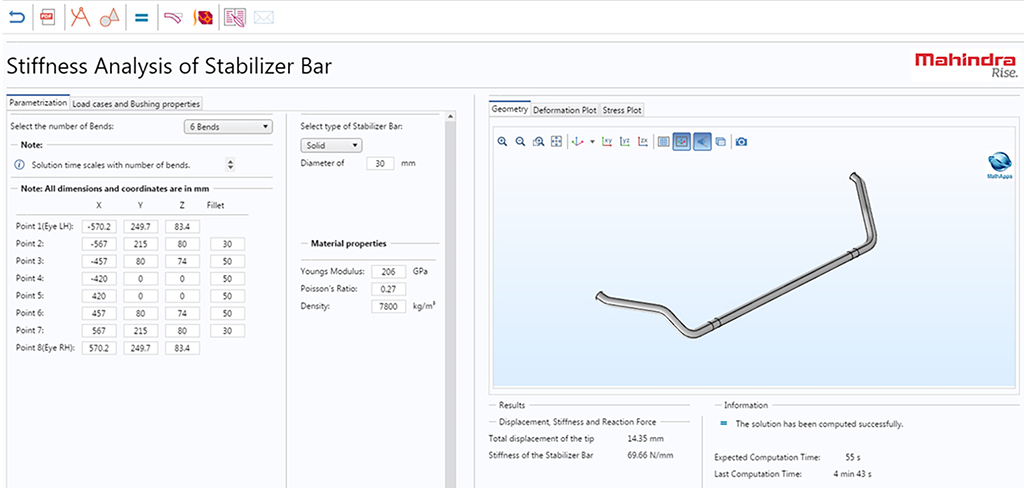
displacement of a stabilizer bar.
Depending on the design complexity of the proposal submitted, the CAE analysis alone can take weeks or months to complete. Based on the simulation results, the design team makes certain modifications and again awaits validation of the design by the CAE team. These iterations are crucial to the safety and reliability of the vehicle. To overcome the race against time, the methods team at Mahindra has explored the Application Builder tool available in COMSOL Multiphysics® software. The team looked at various options for the stabiliser bar and chassis designs via simulation apps. The adoption of apps resulted in substantial reductions in iteration times compared to the conventional approach.
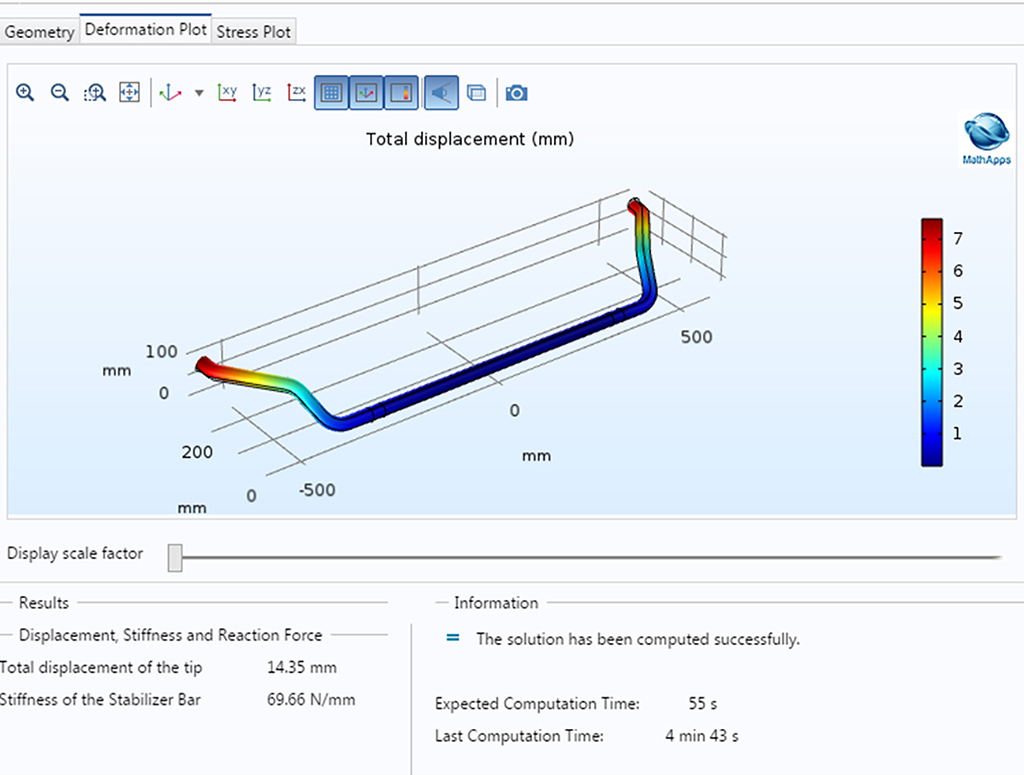
configuration of a stabilizer bar.
Innovative Approach for Designing Stabiliser Bar
A critical component of suspension used to limit the roll of a vehicle is the stabiliser bar, shown in Figure 1. The design is typically either a hollow or solid beam with multiple bends. To accurately model the deformations and stresses in such a component, the design team must ensure that the appropriate stiffness and stress levels are met, either by collaborating with the CAE analysts or requesting validation from their suppliers. Once the model was validated and the results were in good agreement with the experiments, a simulation app was created.
The simulation app of the stabiliser bar can accommodate a large variety of design configurations with up to 15 bends and the option of exploring either hollow or solid bars, with an example shown in Figure 2. The end user, typically a member of the design team, enters the coordinates of the bends to represent the geometry of the stabiliser bar and provides bearing location, bushing stiffness and cross-section parameters. The CAE analyst pre-defines the constraints within the app, making it simple and quick for the designer to run accurate simulations, compute the stiffness of the bar, and model the stresses for standard load cases, which can be seen in Figure 3.
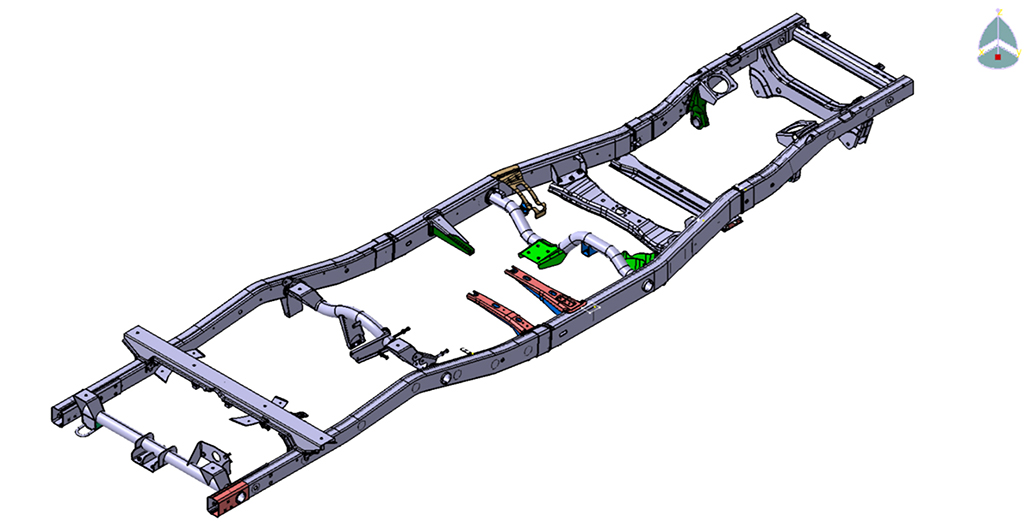
typical utility vehicle chassis
The typical run time of the application takes minutes, empowering the design team to run successive iterations and get immediate feedback on their designs. Knowing that the simulation app is based on a validated multiphysics model, the design team is confident in the results without requiring additional training in simulation. The team at Mahindra has found that the apps save significant amounts of time and encourage collaboration. Additionally, the new culture of collaboration has fostered a greater sense of ownership of the end product as the design can be generated in one or two days without depending on the supplier.
Reducing Iterations in Chassis Design
The chassis is another important load-bearing component that provides stiffness to the vehicle and acts as a base for mounting other components, such as the engine and transmission. One of the common architectures is a ladder frame with two long side members and a number of cross members as indicated in Figure 4. The number, size, position, and shape of the cross members are important parameters that are decided early in the design process.
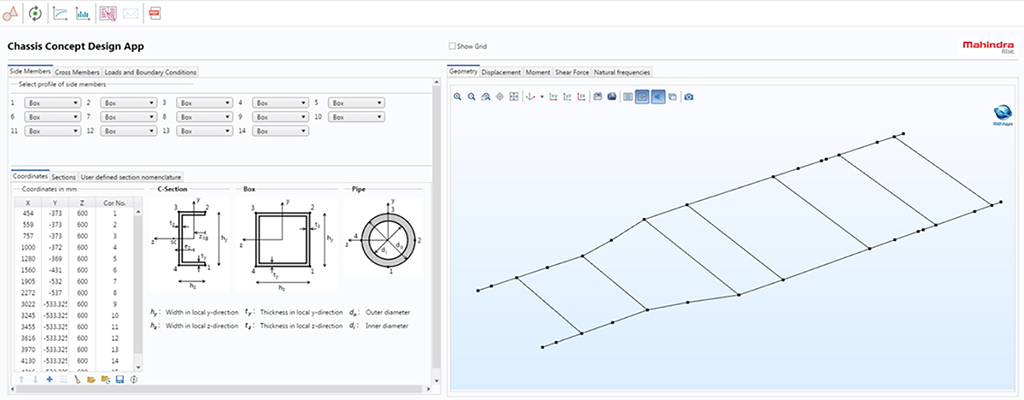
The load carried by the chassis results in combined bending and torsional loads for which no simple analytical solutions are available. The conventional approach to addressing this entails the evaluation of multiple chassis configurations based on the packaging requirements followed by numerous CAE iterations to finalise the design. The right packaging makes sure that all of the parts work together without any interference and with proper access for assembly and disassembly. The best design needs to be structurally sound and satisfy packaging requirements at the same time. While taking packaging considerations into account, each full CAE iteration involves three separate analyses: bending stiffness, torsional stiffness and modal.
This approach requires three to four full CAE iterations, each one typically taking two to three weeks. Using COMSOL Multiphysics, the team was able to combine the three separate analyses, resulting in only one or two full CAE iterations, saving precious time. They then went on to create a simulation app for the chassis design featuring a 1D beam model as shown in Figure 5 based on the Timoshenko beam theory. The end user doesn’t need to know the underlying mathematical model to benefit from the results offered by the app.
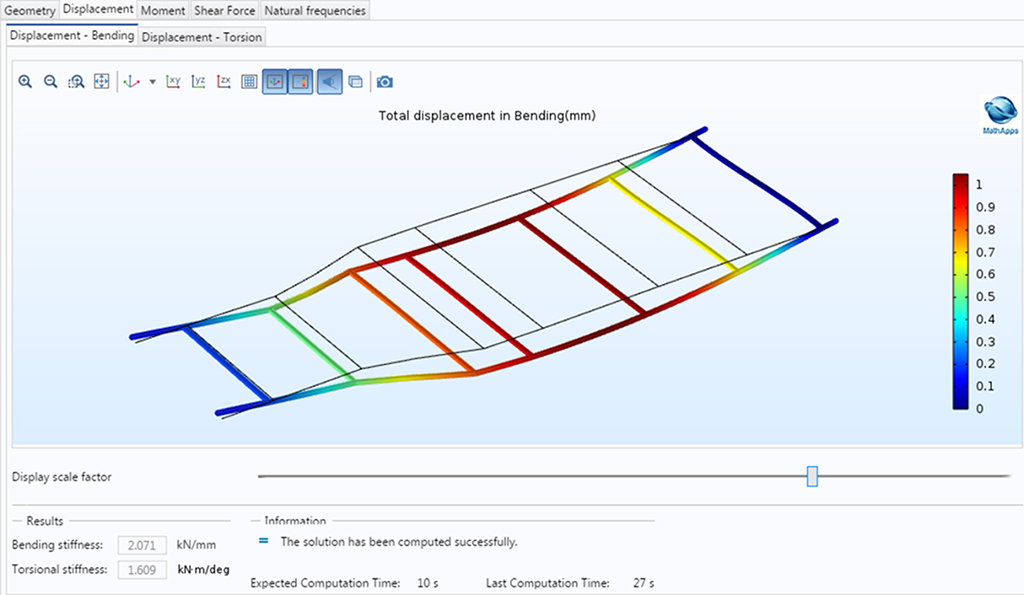
The simulation can be completed in a matter of seconds, even for a complicated chassis design with various cross-sections and members. The beam analysis provides fast and reliable results for a wide range of configurations and computes both torsional and bending stiffness and displacement, shown in Figure 6. The simulation app is used by the drive away chassis (DAC) suspension team, responsible for the design of the chassis and the stabiliser bar. The app offers the convenience of evaluating various design parameters through simple text fields rather than creating a CAD model for each configuration, which is a time-saver for both the CAE analyst and the DAC suspension team.
Simulation Apps and the Road Ahead
The uniqueness of the apps used at Mahindra lies in their ability to handle a wide range of parametric variations, physics and boundary conditions. This enabled the designers to explore various design options early into the product development phase, without the need to rely on the CAE analysts, or obtaining additional training in numerical modelling. The results of the parametric studies are presented within the design guidelines, enabling efficient and cost-effective products.
The simulation apps were developed based on detailed discussions with designers and CAE analysts before being deployed across various teams at Mahindra via a local installation of the COMSOL Server™. Complex design configurations that were previously under the guard of the CAE analysts became accessible to the designers in a convenient and easy-to-use platform. Multiphysics simulation and apps enabled Mahindra to expand their analysis capabilities to also include vibro-acoustics and thermo-structural analyses in their future simulation work.