The EcoPaintJet, initially introduced for overspray-free paint application in industrial vehicle painting, is now benefiting other industries. Refrigeration manufacturer PAN-DUR insulates glazing for commercial refrigeration equipment and has been using Dürr’s innovative applicator to paint glass surfaces for several months. This technology saves time and materials by eliminating the need for individual screens in the screen printing process.
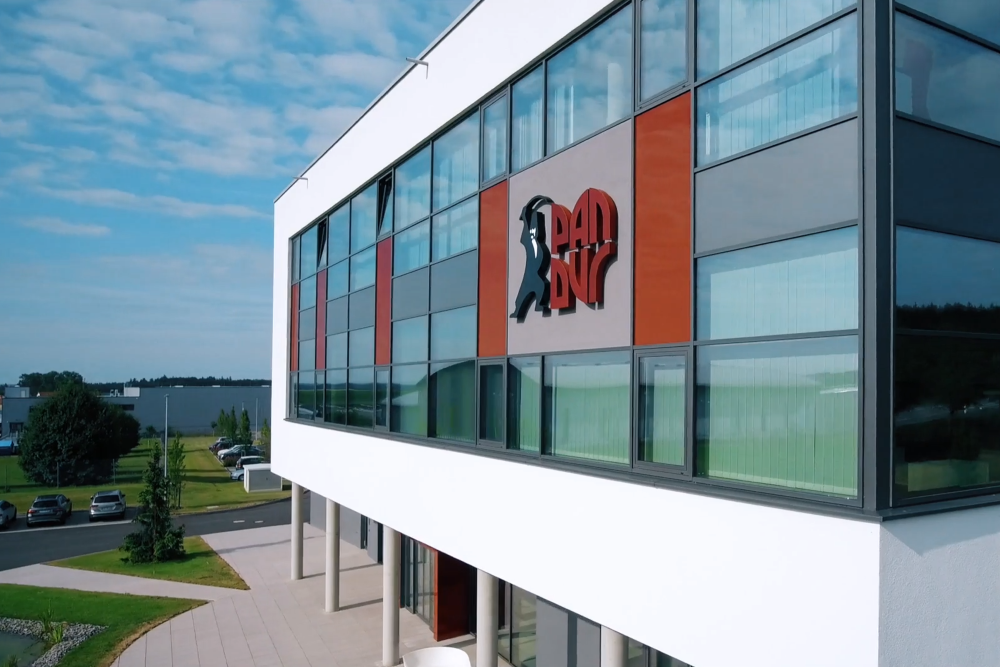
We are all familiar with large refrigeration units from supermarkets: wall shelving, cabinets, or counters, behind whose glass or plastic panels a wide range of foodstuffs are stored. PAN-DUR uses enhanced safety glass (ESG) for its glass elements. Opaque decorative stripes are applied to obscure the unsightly bonded and sealed seams at the edges of the glass and the refrigeration technology behind them. Until now, PAN-DUR used a screen printing process for this, which required a new screen or template for every color, size, or design variation.
More flexibility, lower costs
The EcoPaintJet’s high edge definition paint application without overspray allows PAN-DUR to avoid the complex screen printing process, increasing flexibility and speed in production while reducing paint costs. Each contour is simply programmed and applied in the desired color to the corresponding predefined area without having to mask the glass surfaces first, eliminating the complex and costly manufacture of individual templates as well as the need to devote valuable space to storing them.

One-stop shop for the full range of process technology
Dürr not only supplied PAN-DUR with the paint applicator but also provided all process technology, from the system for extracting paint from the containers to the system for supplying it to the applicator. The installed components include the Fluid Board color dosing and color changing system, the applicator cleaner, and the EcoAUC control unit. PAN-DUR developed a multi-axis portal to mount the EcoPaintJet’s swiveling and height-adjustable application head seamlessly integrating the process technology. “We linked the Dürr process technology with our system’s interfaces. The implementation couldn’t have gone any more smoothly,” explains Jens Verhoef, Head of Development of Electrical and Automation Technology at PAN-DUR. The biggest challenge was finding the right paint for use on glass surfaces. Specialist paint company Votteler, a long-standing partner of PAN-DUR, was also involved in the development. Project manager Uwe Schmidt explains: “Painting glass surfaces is extremely challenging. You need specially developed paints whose rheological properties, coverage, and particle distribution are perfectly tailored to the system. This paint system can also be used on other substrates. So, we needed a few practice rounds until we found the right paint.”
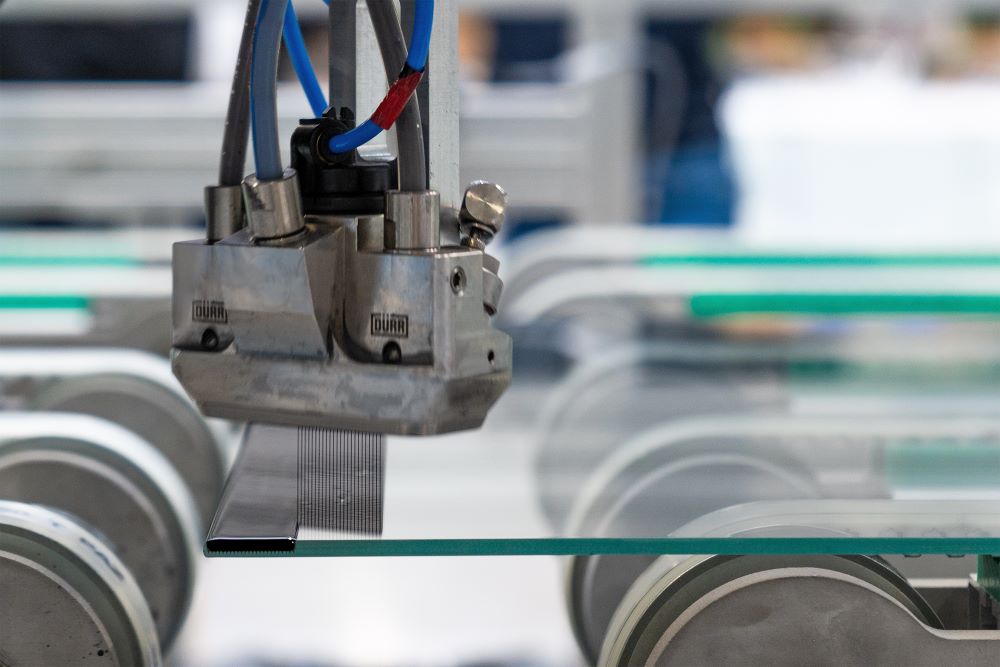
Other industrial uses possible
Other industrial applications are also possible for the EcoPaintJet, for example, in the timber industry, in window or kitchen building, and in the field of painting railway vehicles. “There is potential everywhere that straight stripes are applied to flat surfaces and that type of painting still requires masking right now. We’re getting many inquiries from different industries,” says Fabian Schilt, Head of the European Industrial Sales Team at Dürr. An additional advantage that makes the whole system attractive for other uses is that all components are ready to integrate into existing production systems.