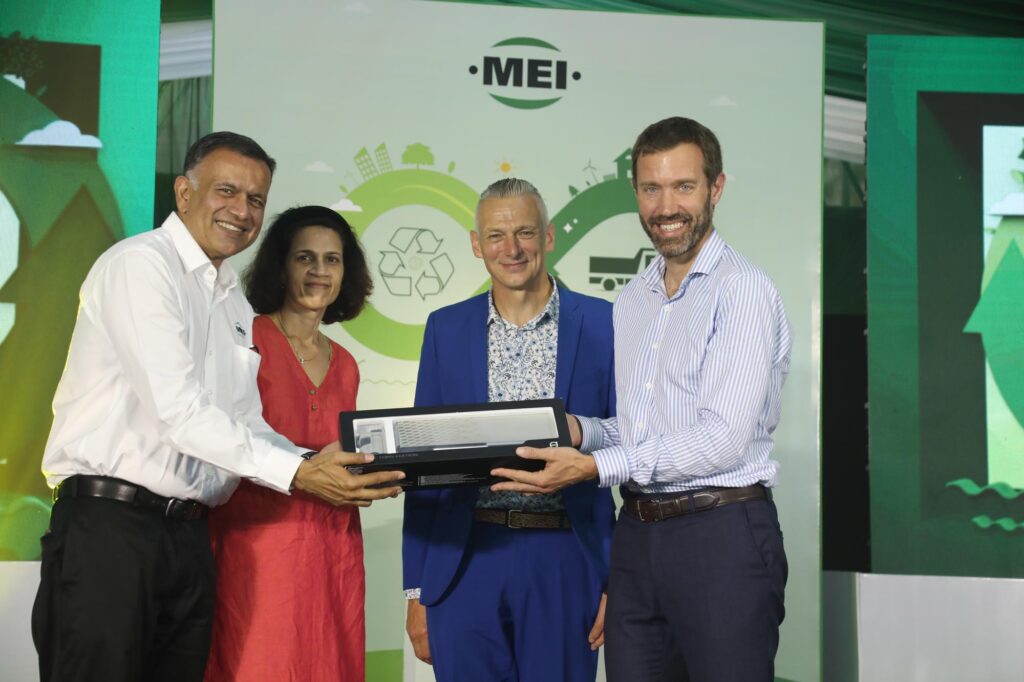
Madras Engineering Industries (MEI), the largest manufacturer of Slack Adjusters globally, had set up a ductile Iron Foundry during 2012 to meet its captive requirements. Over the past decade, MEI expanded its business by taking up supply of fully finished axle and chassis machined iron casting parts to Cummins {US, Mexico, Brazil and Europe}, Sisamex {Mexico} and Volvo {US and Europe}.
Considering the growth in the machined casting export business and the future opportunities with Volvo, MEI has taken up significant steps toward sustainability by partnering with Volvo Group to supply fossil-free ferrous castings for their trucks. As part of Volvo’s commitment to becoming a NET ZERO Company by 2040, this collaboration marks a milestone in their supply chain efforts, with MEI producing various critical components using > 90% renewable energy and 100% recycled materials. This partnership not only aims to reduce CO2 emissions by over 20,000 tons annually but also showcases MEI’s leadership in adopting sustainable practices and setting Industry standards for eco-friendly manufacturing. This article features insights from an interview by N. Balasubramanian and Subadra Anand with key representatives from MEI and Volvo, highlighting their thoughts on sustainability and innovation in manufacturing.
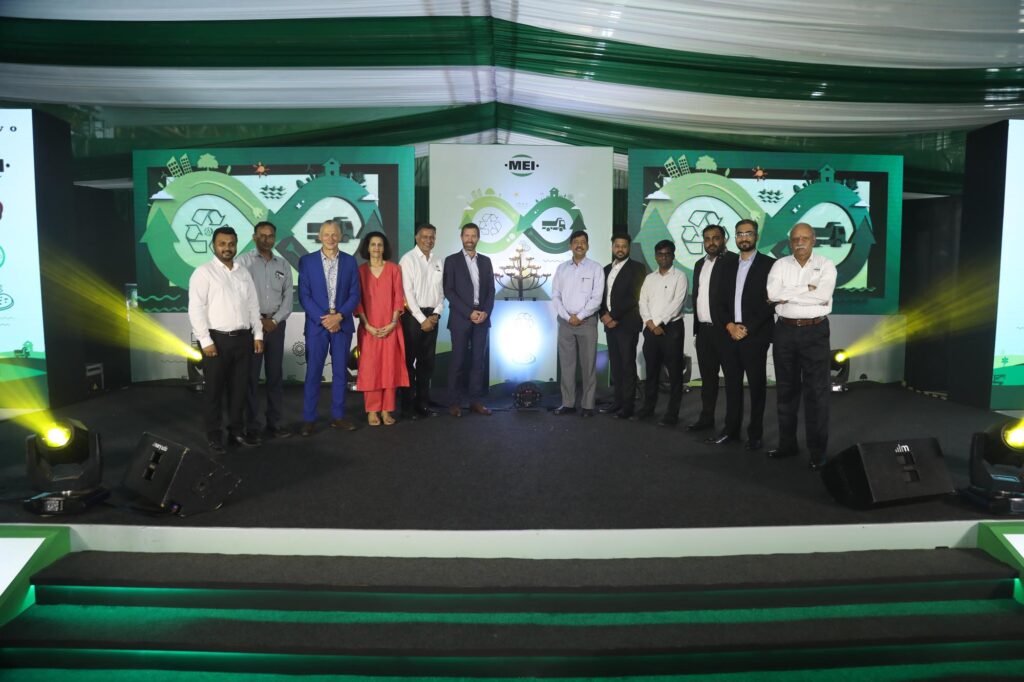
A Paradigm Shift: From Quality and Cost to Sustainability
For decades, metrics like quality (ppm), cost, and delivery times were paramount for manufacturers like Volvo when driving continuous improvement among their supply chain partners. However, as Sriram Sivaram, Joint Managing Director of MEI, pointed out, the conversation has shifted. Quoting Martin Lundstedt, CEO of Volvo Group, he stated that “Sustainability has to be profitable; profitability has to be sustainable,” highlighting the inseparable link between the two. MEI has integrated this philosophy into their core business strategy, allowing the company to embrace sustainability as a fundamental aspect of their operations.
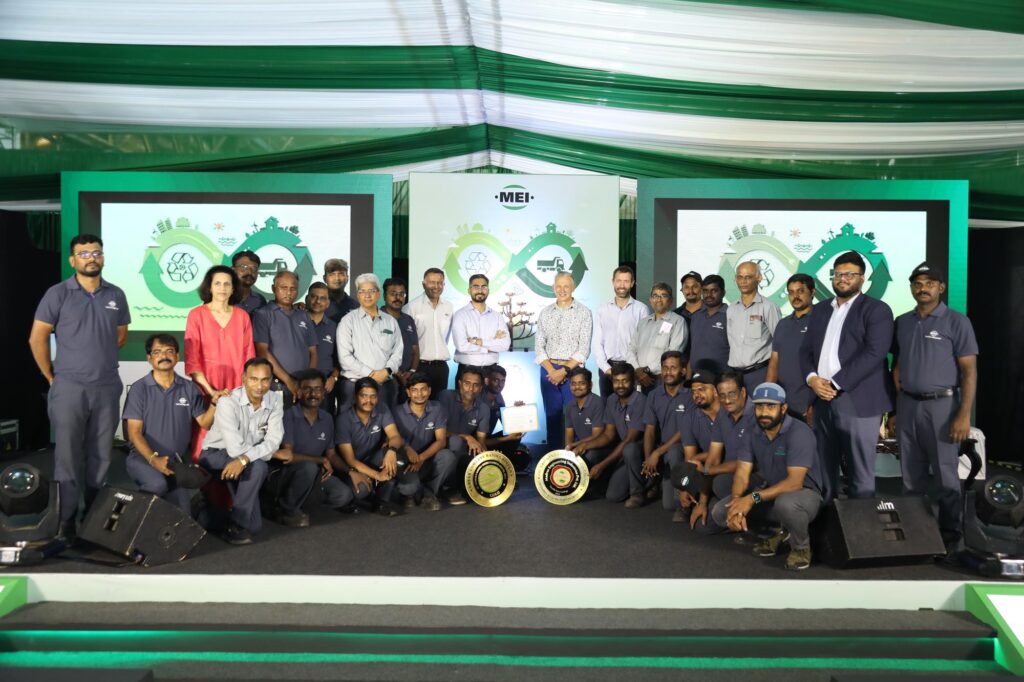
Mark Bamber, Head of Circularity and Remanufacturing, Volvo Group, echoed these sentiments. “It’s no longer just about quality or cost. Sustainability is now a critical factor when evaluating supply partners.” He acknowledged the complexities of implementing sustainable practices globally, given that different countries have varying regulations. Nonetheless, Volvo’s commitment to reducing its environmental impact through collaboration with suppliers like MEI has remained steadfast.
India’s Role in Sustainable Supply Chains
India’s growing prominence in global supply chains is reflected in the contributions of companies like MEI. As one of Volvo’s key partners, MEI has been instrumental in advancing the sustainability agenda. Recently, Volvo Group partnered with MEI to create fossil-free ferrous castings, a critical component in Volvo’s trucks. These fossil-free castings, which undergo high levels of stress and fatigue, are produced using > 90% renewable energy and 100% metallic scrap without the use of virgin materials like pig iron and Fossil fuels like Diesel. Sriram emphasized the importance of this initiative, stating, “By focusing on fossil-free production, we can significantly reduce our carbon footprint.”
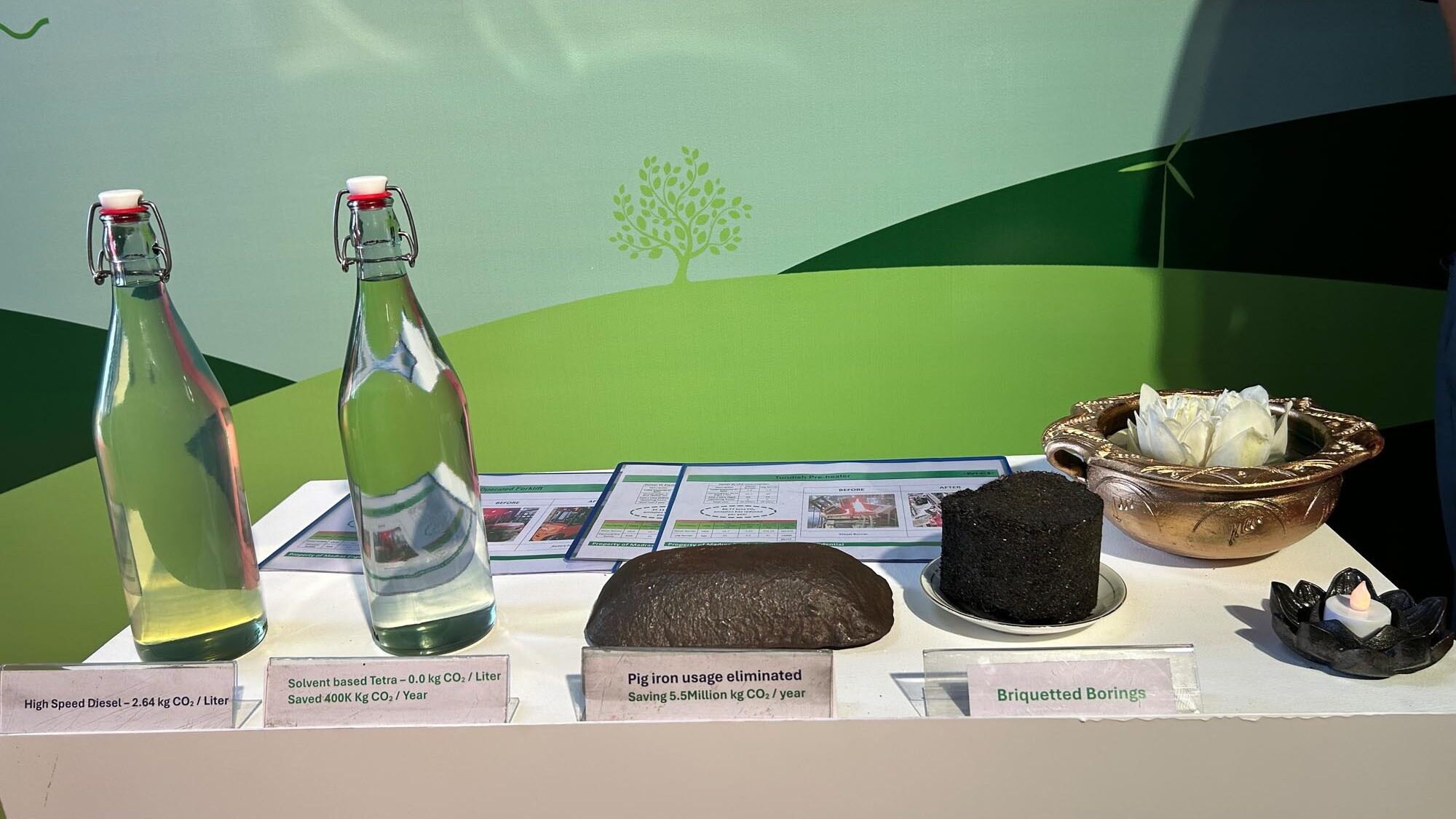
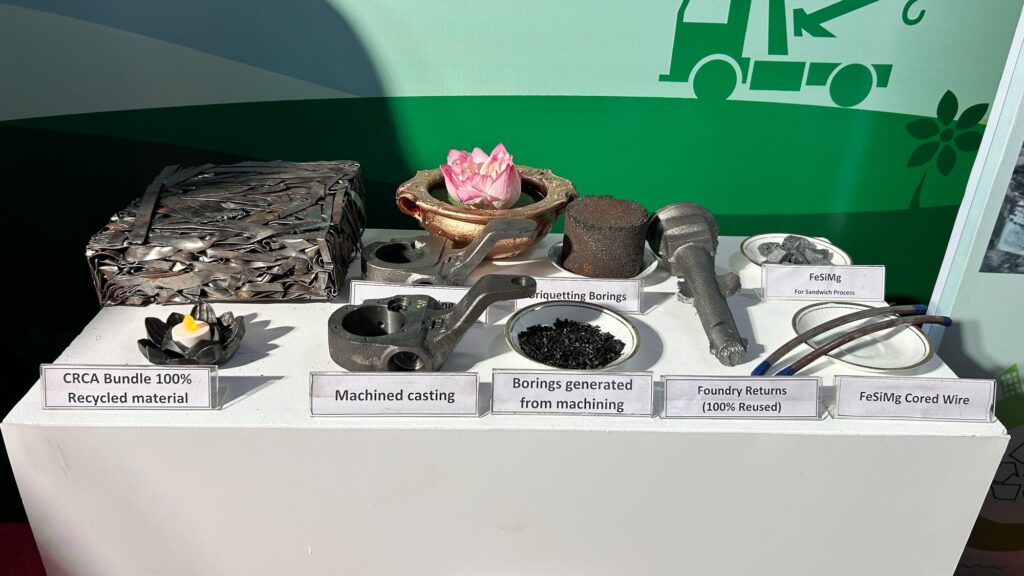
This collaboration is expected to reduce CO2 emissions by 20,000 tons annually for Volvo. Additionally, the castings produced by MEI are entirely landfill-free and devoid of toxic elements, making them 100% recyclable. These green certifications, earned through partnerships with Volvo and recognized by the Confederation of Indian Industry’s (CII) Green Products & Services Council, are a testament to MEI’s leadership in sustainable manufacturing.
By tackling Scope 1 and 2 emissions—reducing direct emissions from factory operations and increasing renewable energy usage—MEI has already achieved more than 90% renewable energy in their processes. Their target is to push this even further, aiming for carbon neutrality by 2030. Sriram underscored that this journey is only just beginning, stating, “Our goal is to be at the forefront of the fossil-free movement in manufacturing.”
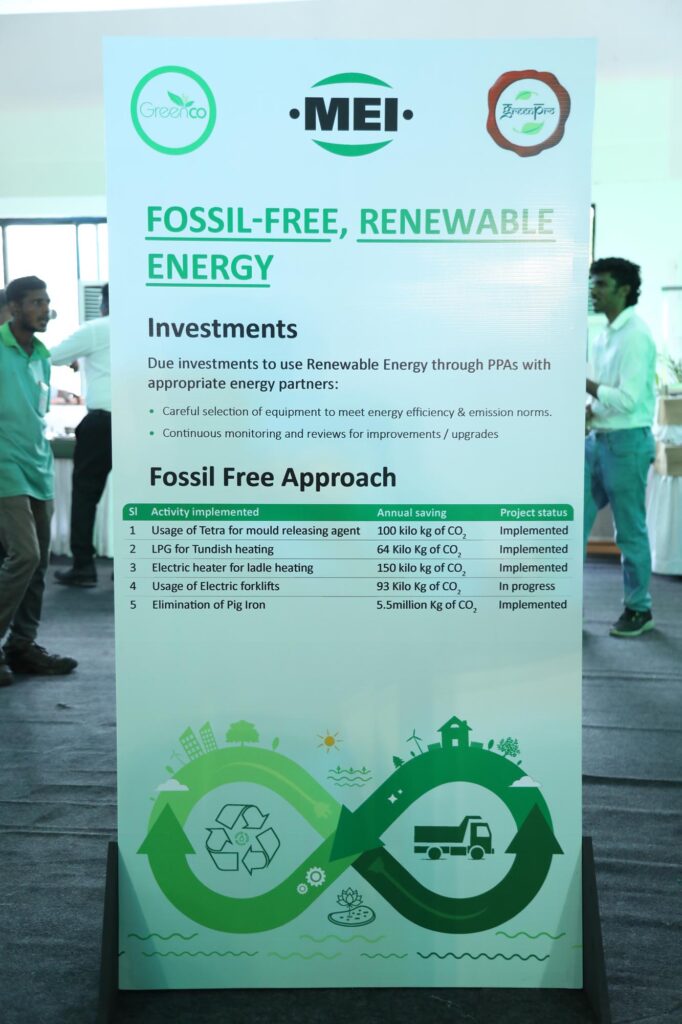
MEI has also made significant efforts for water conservation and recycling. Their Foundry at Pillaipakkam has 3 ponds to store up to 20 million litres of water, all dependent on internal rainwater harvesting. This caters to > 50% of plant water requirements currently.
Zero Defects: A Lesson from the Past
Volvo’s journey toward zero ppm (parts per million) offers a powerful analogy for their current sustainability push. Pierre Masclet, Head of Casting and Forging Purchasing, Volvo Group, recalled how suppliers once viewed zero ppm as an unattainable goal. “Today, it’s a reality. MEI, a key supplier for Volvo, has applied this same zero-defect mandate to their operations.”
Sriram discussed how this mandate extends to his Company’s commitment to producing fossil-free products. With their annual production of over 4.5 million machined casting parts, a ppm as low as one could translate into significant losses if issues arise. Therefore, his team focuses relentlessly on maintaining zero ppm. This dedication to quality is paralleled by their approach to sustainability, where global perspectives influence local strategies.
Growth and Innovation at MEI
MEI’s success story exemplifies how embracing sustainability can fuel growth. As the world’s largest manufacturer of Automatic Slack Adjusters, MEI is now expanding into the global Air Disc Brake market. Sriram noted that their next big challenge is developing advanced brake control systems. “We’re thinking of what the future generation wants, not what the past was,” he said, referring to MEI’s research collaboration with IIT Madras to develop Brake-By-Wire technology.
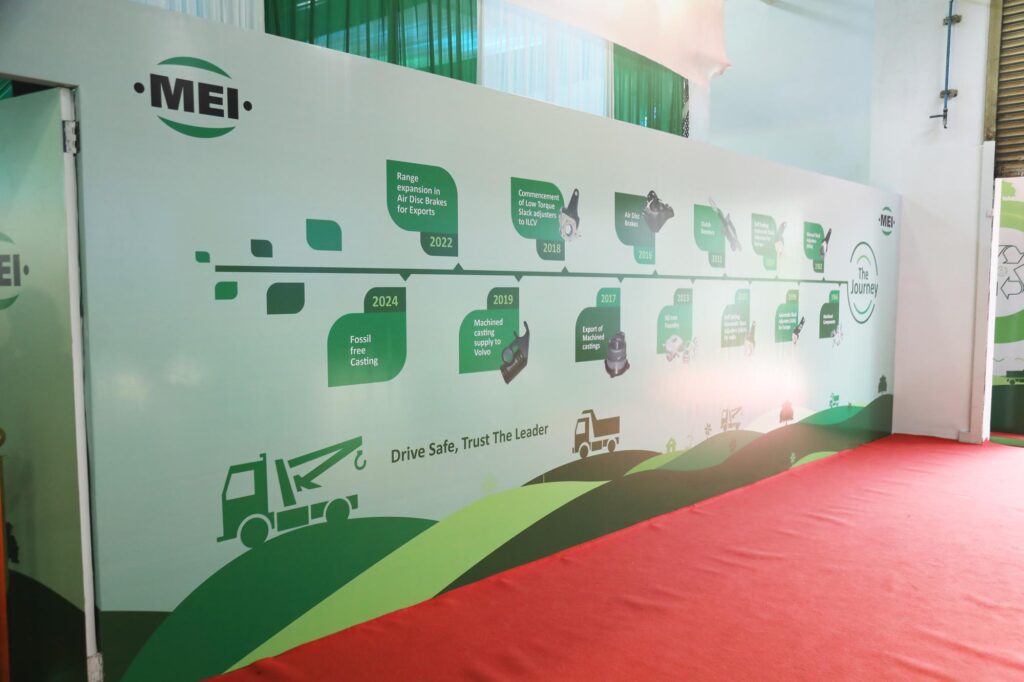
Looking ahead, MEI plans to certify all its products as green, expand its renewable energy use, and transition to electric vehicles for internal logistics. Their goal is to become carbon neutral by 2030. Sriram concluded, “We will continue to see growth, and our ambitious sustainability targets, including our commitment to fossil-free manufacturing, will make us a significantly large business house by 2028.”