Supplier of rubber components for the truck and bus industry, Polybond has carved a niche for itself in the automotive industry. Manufacturing rubber parts since 1978, Polybond’s product range includes rubber to metal and plastic bonded parts, silicone hoses as well as extruded hose. “We make built to print rubber components for engine mounts, radiator mounts, bump stops and a wide range of radiator hoses,” informs Adit Rathi, CEO, Polybond India Pvt. Ltd.
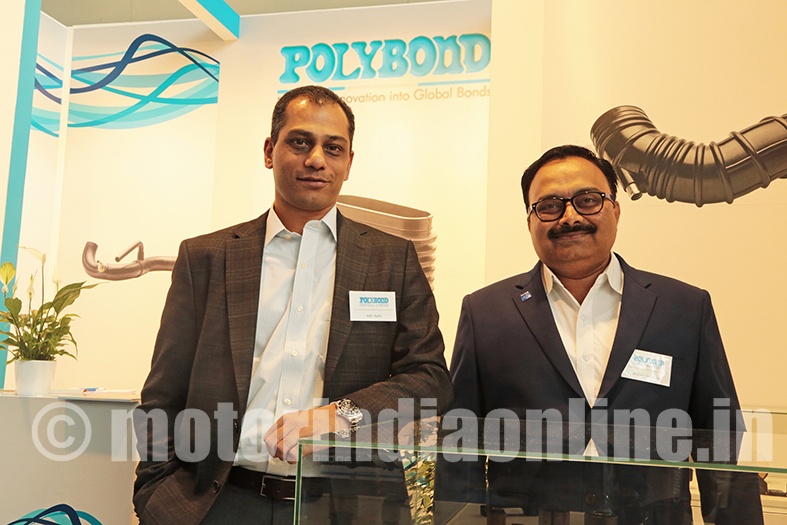
From the inception, Polybond has focused on rubber parts for trucks and buses. The company’s major business, approximately 70 per cent, comes from the export market. Even as the focus remains predominately on automotive, 70 per cent of Polybond’s business in automotive sector is from direct OEMs and 30 per cent from the Tier 1 suppliers. “However in the last one year the potential from Tier 1s is increasing and we have seen the business growing. Last year we grew by 14 per cent and this year we will be more than 25 per cent. We feel this growth is because of the new customers as well as our existing customers who have acquired new programmes,” reveals Rathi. To meet the growing demand, Polybond is constructing a greenfield facility in Madhya Pradesh. The company already have two state-of-the-art plant in Alandi and Sanaswadi, Pune, Maharashtra.
Advantage India
Polybond’s consistent growth is also attributed to global OEMs setting their eyes in India for not only its cost effective nature, but quality products. Adit Rathi says: “Component manufacturers over the years have improved tremendously on the operational side to become world class. It won’t be an understatement that our customers have literally improved us.”
India itself has gain prominence over the years and the ‘Make in India’ initiative has further helped the growth. Rathi affirms: “Ours is not a plastic or sheet metal component. Our products involve a lot of testing and interaction with engineering teams of customers. Communication over such subjects gives customers a comfort over other countries in aspects like language and transparency of processes. This help build trust. Since a lot of customers are not well equipped with rubber as a material so inherently there are a lot of project related discussions for months together before the project starts. Like fine tuning of design, rubber properties, endurance testing in our lab. The design can undergo changes after test. We have a technology center and we do all the endurance test at the lab in our plant. So all though it is made to print, without doing all the design and endurance tests we cannot start to supply.”