– By Danilo Pasotti
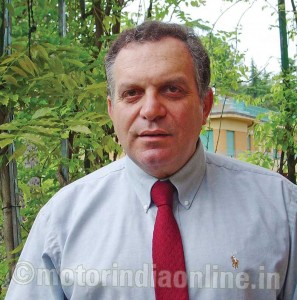
Do just acquisition and maintenance costs affect fleet tyre management? Reality and perception are quite different in tyre management. If we want to know the true tyres-related cost, we need to start with a complete cost analysis of the tyre system, right from basic acquisition numbers for new tyres and retreads.
But digging deeper, we’ll find additional costs for inventory management, disposal and unexpected downtime, not to mention the grey area known as administration. When we look at the big picture, we’ll see that while tyres constitute the number one expense, all the other costs put together represent 30-40 per cent of the total cost.
The cost can be split mainly into five areas:
• Product costs: New tyres, retreading tyres, casings, and disposal
• Service costs: External service (fitting, balancing, axle alignment), internal workers, location (in case of internal service), equipment and ancillary products, bolds, valves, caps and fitting paste
• System costs: Selection and purchase as well as administration
• Mismanagement costs: Low quality products, unbalance between use of new and retreading tyres, incorrect application matrix and inadequate pressure and wrong twinning
• Hidden costs: In-route failures, drivers and vehicles at standstill, electricity, heating, fuel for dealer service and eventual higher rolling resistance, and the cost of asset
In order to have a clear assessment of the above costs, it is necessary to undertake a thorough tyre inspection, including cost analysis
We start with the annual tyres consumption determined by initial inventory + annual purchases – final inventory (mm). It’s important to consider the vehicles’ annual replacement plan since they come always with new tyres.
After analyzing these data we need to make a fleet inspection so as to be able to figure out the mismanagement and hidden cost. This includes vehicle inspection as well as tyre and scrap tyre analysis. It is also important to identify the system costs, including procurement process analysis and administrative procedures.
The service cost analysis must consider internal service plus external service, including distance evaluation.
Finally no one considers the financial cost, namely, the value of the asset (all tyres fitted on the vehicles, tyres undergoing retreading and repairing, as well as those in stock.
A proper fleet inspection involves defining the scope and selection of representative vehicles to be inspected.
Although we should analyze the majority of the fleet vehicles, we do prefer a step-by-step approach. We should start with knowing the fleet problems, acquire knowledge and prepare ourselves for the best solution for the problems.
Once we have the complete information, we can start tackling the issues with the help of an expert.
The accuracy of the results is directly associated with the vehicles taken up for inspection:
• 10% of the fleet (accuracy 80%)
• 15% of the fleet (accuracy 85%)
• 20% of the fleet (accuracy 90%)
• 30% of the fleet (accuracy 93%)
• 50% of the fleet (accuracy 95%)
For inspection, the following information must be collected:
• Vehicle: Type, make, ID
• Tyre per position: Size, brand, pattern, new, retread, regrooved, pressure, tread depth
• Rims: Overall condition, missed valve caps, internal inaccessible valves, presence of rust and cracks
• Anomalies: Axle misalignments or mechanical organs damaged, tyre abnormality, irregular wear, object in tread, cut, bulges, broken cables, relocation needs and twining mismatches
• Scrap tyre analysis: Check waste reason, remaining tread depth and yard overview