
With the introduction of new technology as well as different socio-cultural upheavals, the world has changed dramatically in the last few years. Businesses have had to constantly adapt to these changes. For manufacturing companies, this transformation begins at the shop floor, along with the board room, as the employees here are a vital cog in the wheel of change, reveals Amit Srivastava, Group Chief Executive Officer, Remsons Industries Limited, in an exclusive interview with Rajesh Rajgor
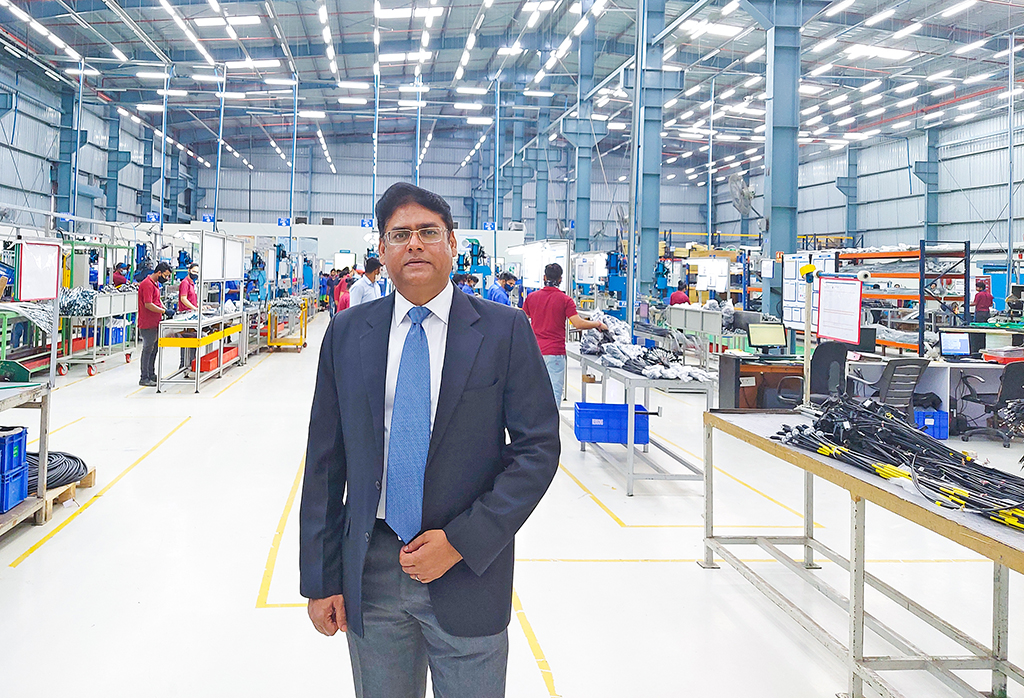
Let us start with the sprawling new facility you have set up in Pune. Could you share details on why you decided to build this new plant and move your operations from Daman to Pune?
Chakan, in Pune, is one of India’s major automotive centres, surrounded by Tier 2 and Tier 3 suppliers. We will be able to cut procurement lead times and delivery times by having a presence here. In terms of infrastructure, our Daman facility faced restrictions for future expansion. Because of the possibility for future expansion, we needed a much larger facility to meet industry demands. We are able to onboard workers who are being taught and groomed to accept more roles within the firm since we have access to a wider talent pool of human resources in Pune. Rather than focusing on building specific position skills, we are focusing on growing them in areas that correspond with business capabilities and values. We hope to materialise some future JVs in this unit, which has a larger and modern facility with good airport connectivity and is located in the centre of one of the automotive hubs. Customers will also be able to purchase products of our UK operation from this plant.
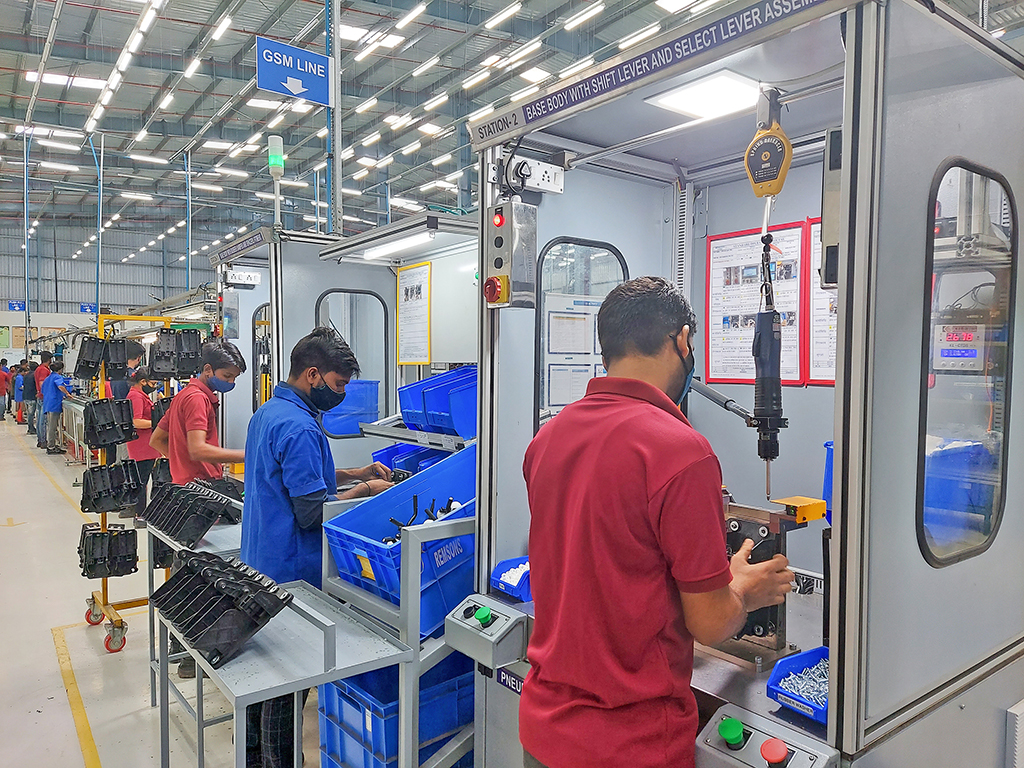
Could you give us a general overview of the products manufactured at the plant and the automotive applications to which they cater?
Light-duty vehicle cables, HVAC cables, seat cables, door lock cables, hood latch cables, choke cables and medium-duty cables will all be produced at the new site. It will also offer clutch cables, gear shift push-pull cables, accelerator and throttle cables and heavy-duty cables such as park brake, winch, axle retainer cable and jacks for all segments of the automotive industry, including passenger cars, light commercial vehicles, medium and heavy commercial vehicles, rear engine buses, agriculture, farm equipment, and even non-automotive segments.
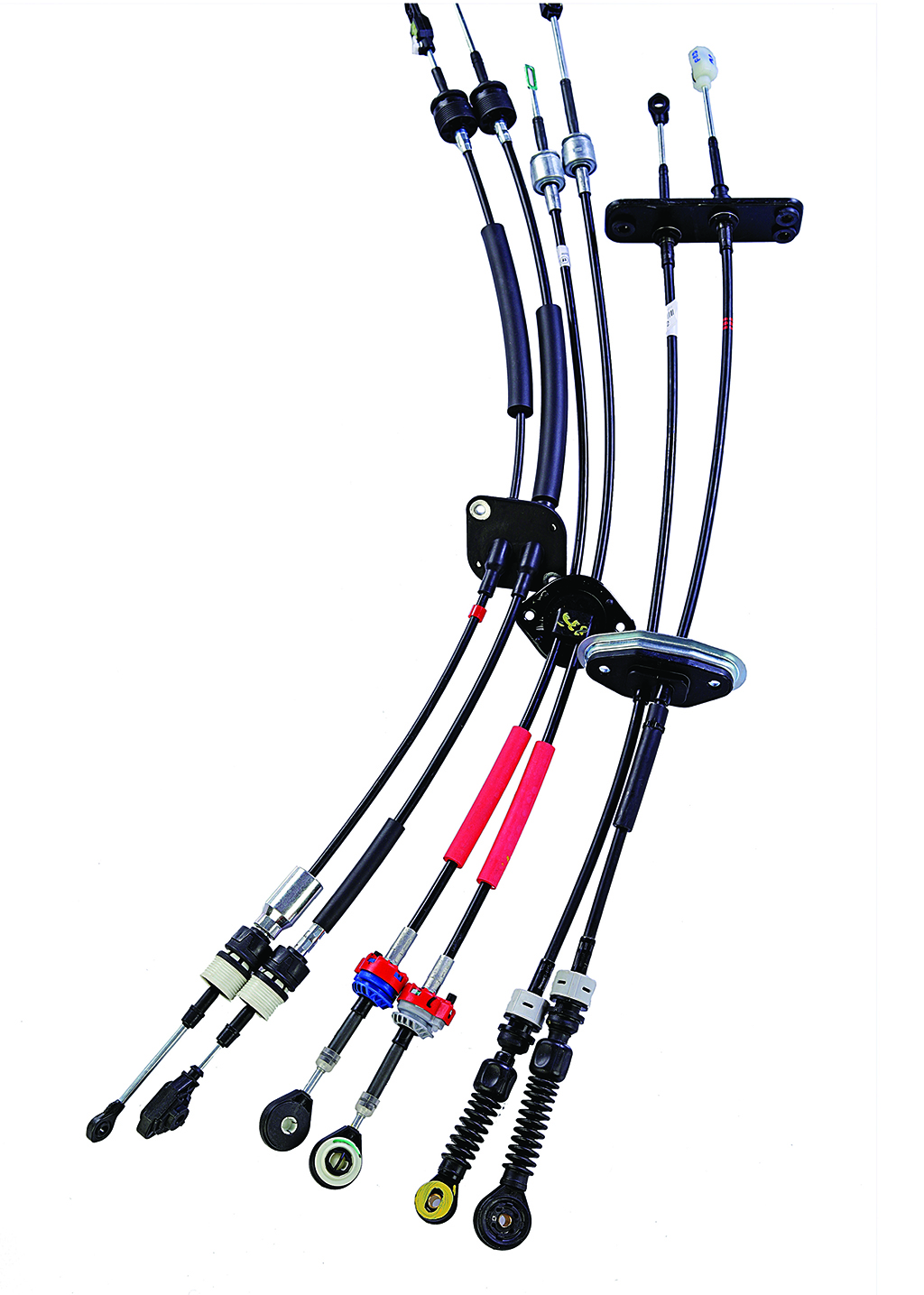
What impact would this new plant have on your overall production capability when combined with other products from your various factories in assisting Remsons’ in achieving its aim of becoming an Rs 500 crore company in 2-3 years?
Our new factory occupies 1,20,000 square feet of land. This facility is more than double the size of our previous one. We ended the previous fiscal year with group revenue of Rs 225 crore of which the Daman factory (now Pune facility) contributed 20%. We intend to double this amount in the next two years to reach our Rs 500 crore target. The extra capacity allows us to expand our product ranges and provide new products to our clients.
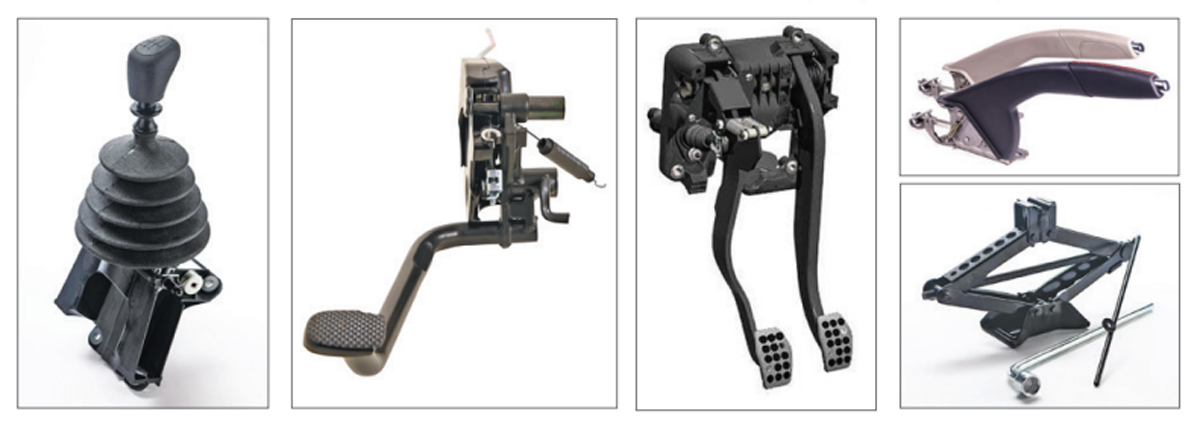
What relevance does the layout of the new factory have? What industry best practices have you used to increase manufacturing and what is the estimated cost of investment?
To achieve lean manufacturing, we enlisted the help of ACMA experts for layout design. We used this production procedure because we believe in increasing productivity while reducing waste in our manufacturing process. Reduced lead times and operating costs, as well as increased product quality, are all advantages of lean manufacturing. Despite the pandemic-related setbacks, the company has continued to develop capacity and Remsons has already invested around Rs 20 crore in this initiative. We put solar panels at our new plant as part of our ‘Go Green’ programme. Our goal is to protect against rising energy costs while also lowering carbon emissions. To improve quality and productivity, we installed conveyors on all manufacturing lines to assure single piece flow, as well as poka-yoke and failsafe. We have included modern amenities and facilities for shop floor workers such as a canteen, a medical room, a training room and a crèche. Apart from that, we encourage female employees to contribute to workplace diversity.
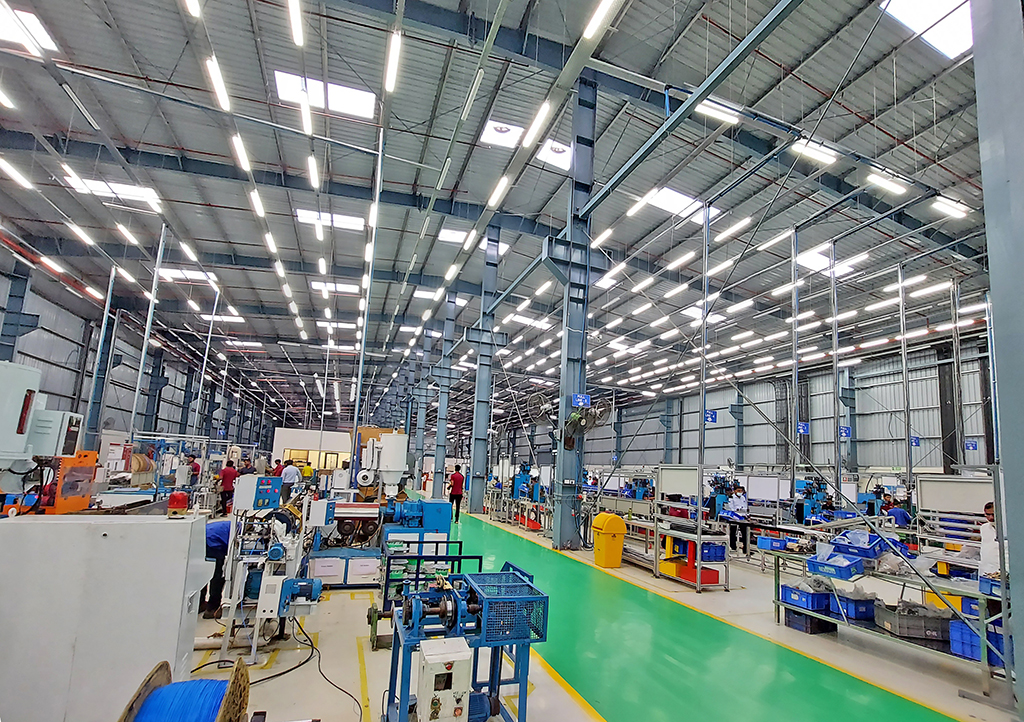
What steps have been taken to improve the company’s research and development infrastructure? Please elaborate if there has there been any unique learning from the acquisition of Magal Cable, which is situated in the United Kingdom?
We have decided to make a major investment in research and testing in light of the demanding global automotive safety policies and the growing customer validation requirements. This will be implemented over a two-year timeframe. A total of 5,000 square feet has been set aside for this purpose. This is in addition to our existing engineering centre. We have created the most modern cable characterisation rig in the industry, which is the first of its type. At the touch of a button, we can run several tests with excellent precision. With the help of acquisition of Magal Cable we were able to add various goods such as winches, jacks and pedal boxes. We are in the process of introducing them to our customers, who will be able to benefit from global technology produced in India.
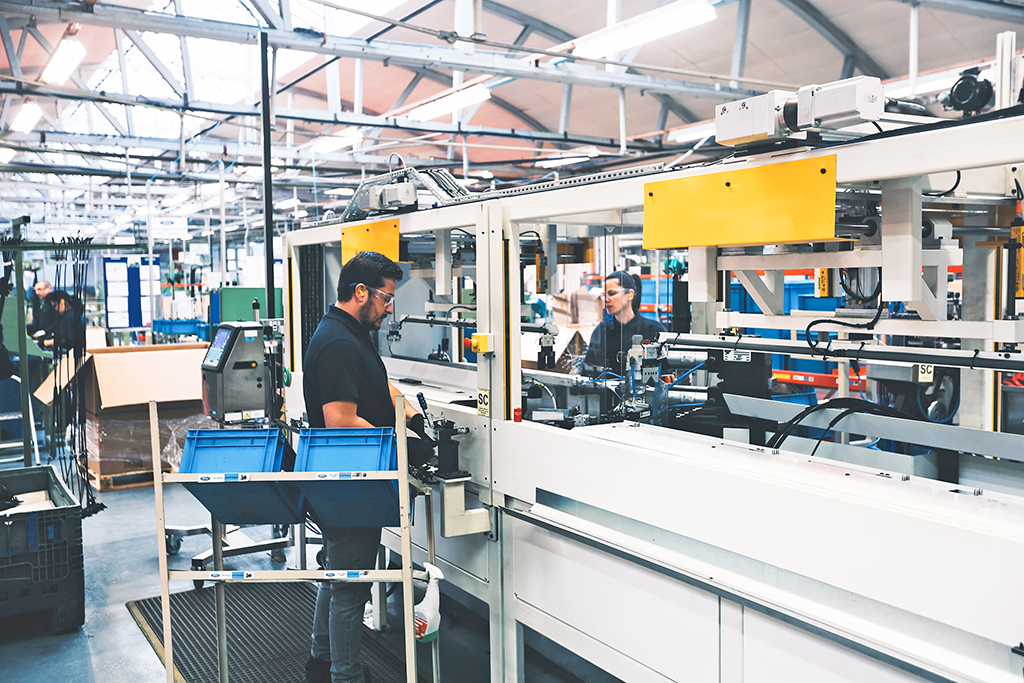
How would your research and development prepare for the growing number of electric vehicles that most OEMs are releasing?
We are developing a two-pronged strategy for the future electric vehicle segment. To begin with, we will develop a new product line that will be utilised in the majority of electric vehicles, while also working on a more dependable and economical parking brake mechanism using cables and body cables from our current product line. Winches, jacks, and pedal boxes are also EV-compliant and will continue to be in high demand in the near future. Our design team is collaborating with global OEMs on the design of a hood and charge port opening lever with cable controls.
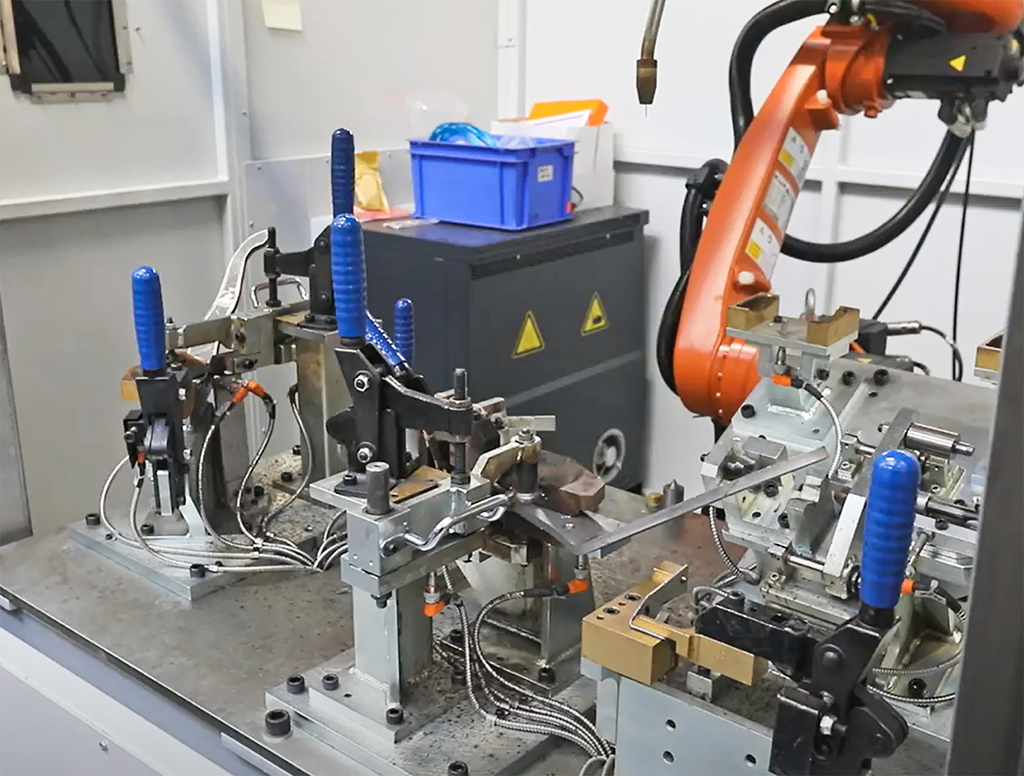
What is Remsons’ current CAGR and what are your projections for domestic clients and exports?
In comparison to the industry’s CAGR of 6%, our CAGR at the company level is 15%. We want to double our sales by doubling our exports and boosting our customer base in both areas as well. Our concentration would also be on acquiring international clients.
What is your idea for changing Remsons’ brand image and what kind of brand visibility and culture do you want to create?
Our driving force has been the desire to provide the finest quality products to our clients by always redefining our own goals, striving for the highest standards of engineering excellence and the highest ethical ideals. We wanted our brand’s inherent ethos to be reflected in its brand interface, logo and thought. We are certain that the new brand philosophy will serve as a rallying cry for teams across the organisation to re-energize our commitment to excellence. We want to build new vistas of cooperation with our customers and partners, as well as passionately serve the interests of society at large. This overriding intent will guide the organisation’s cultural imprint towards always striving for the best.
—
Remsons – new brand identity
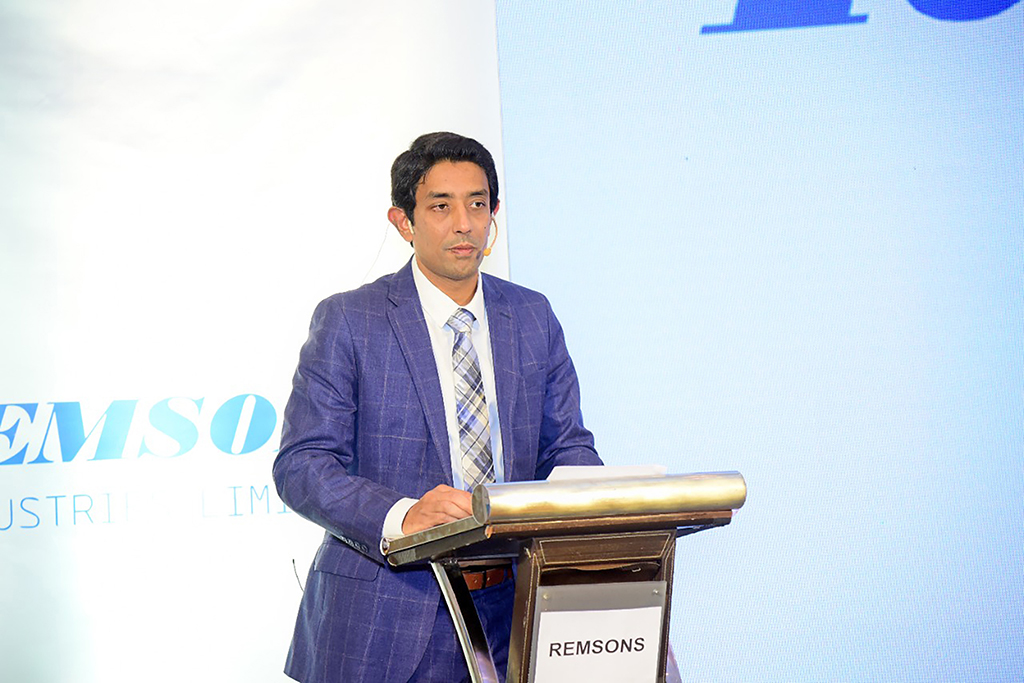
Remsons has updated its flagship brand’s logo in order to bolster its position in the automotive marketplace. According to the company, ‘the philosophy driving this re-branding initiative is built on the clarion call to collectively climb the next mountain of achievement. A call to keep striving. To keep moving ahead. A call to ‘LET’S MAKE GREAT.’
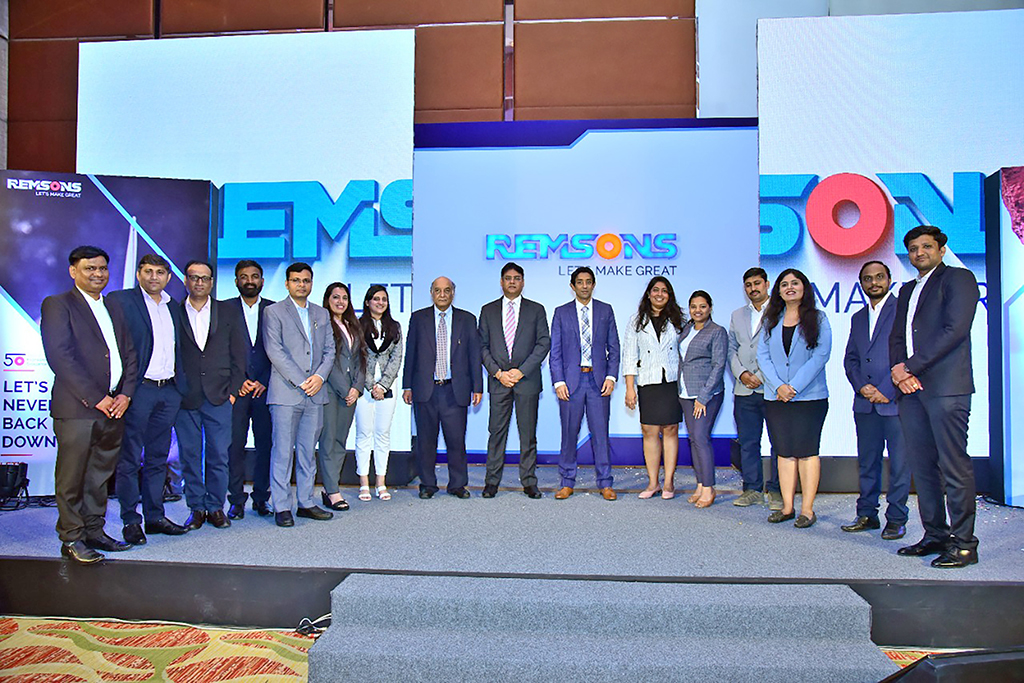
The new brand identity was revealed at a function at Marriott Chakan on 8th December, close to Remson’s new state-of-the-art production facility in Chakan, Pune, attended by the leadership team from around the country. The function was attended by Remsons’ leadership team from across the country who were in great spirits to witness the new identity and listen to the top management spell out the vision for the company for the coming years.