RMP Bearings has established a firm foothold in the competitive bearings industry, not only in India but globally, thanks to its high productivity and superior quality products. Miten Makwana, Managing Director, RMP Bearings Ltd., discusses how the company is utilising India’s growing acceptance and stature as a technology powerhouse to innovate and extend its product portfolio in this exclusive interaction with Rajesh Rajgor
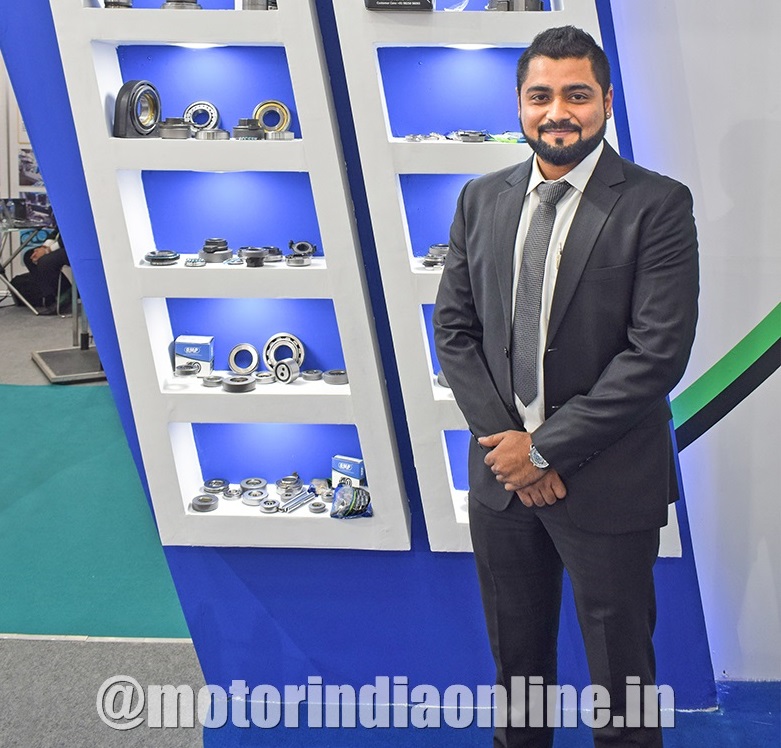
What products have you produced in the last three to four years that have acquired momentum in the automotive and textile space?
We at RMP Bearings offer a diverse range of products, all of which have been meticulously manufactured. Our clientele has demonstrated brand loyalty for some of our best-selling items. As India’s first maker of universal joints made of sheet metal, our stake yoke, bolt yoke, weld yoke, profile yoke and piped yoke have all been produced successfully. For manual steering, HPS and EPS we created stamping of machining. We have a tool room where we create and design universal joints, gauges and tools. For yokes we create special purpose machines according to our customers’ needs. We offer our yoke products to all the main OEMs across India as well as export them to France and the United States.
Further, to satisfy the rapid increase in demand for quality, diversity of standards and new types of bearings, RMP Bearings has developed the most advanced manufacturing and quality assurance processes. Precision ball bearings with bore diameters ranging from 6 mm to 160 mm are produced in our state-of-the-art manufacturing facility, which includes in-process and post-process gauging in grinding, as well as centrally air-conditioned assembly lines with auto gauging and testing equipment.
What advantages do Indian suppliers have at the moment considering the current domestic and global macro-economic factors and what areas should they focus on to keep scaling new heights? As a home-grown supplier with extensive experience, what is your take on the same?
As a bearing manufacturer we have the capability and capacity to serve vehicle manufacturers on every continent with the same extensive range of standard and custom bearing and ball products. Our organisation, which was founded in 1978, combines India’s significant strategic advantages and flexibility with high worldwide quality standards and documentation requirements. India is a fascinating market for foreign entrepreneurs and investors since it is a fast-growing country that also happens to be the world’s largest democracy.
In terms of technological innovation, India has emerged as a force to be reckoned with. Telecommunications, information technology, automobiles, textile and engineering companies are on par with their international counterparts in terms of sophistication and prominence. India, along with the United States and China, is increasingly considered as a major driver in global technology innovation. India has a large and healthy middle-class, making it an attractive consumer market. India is, without a doubt, the greatest market for manufactured goods and services in the world.
We have found good potential to develop our automotive and sheet metal components business in OEM, aftermarket and export divisions following the pandemic. In this recent worldwide uncertain environment, we have placed a greater emphasis on our export product categories. To capitalise on worldwide market prospects, we have expanded our product offering in the export and aftermarket segments. To boost our production capacity, we created new machinery. To fulfil our annual output objective, we intend to automate our manufacturing process.
Could you briefly describe changes in your company’s production infrastructure? What role does RMP Bearing’s research and development capability play in the development of newer products that different market segments demand on a regular basis?
We have a cutting-edge manufacturing facility in Gujarat, India’s commercial capital. Each function at our manufacturing floor is outfitted with the most up-to-date technology to ensure the highest level of quality. Before being released into the market, each bearing is meticulously made and put through a battery of testing. Our primary strength is our large reservoir of expertise and infrastructure, which has been established through time to provide clients with uncompromising performance and technology.
Our products and services include sheet metal, injection moulding, automatic temperature control heat treatment, finishing and super finishing all under one roof. We have auto gauging, auto ball pairing, automatic grease and seal insertion devices for our centrally air-conditioned manufacturing lines. At various stages of production, the entire equipment manufacturing process is subjected to rigorous inspection and testing, which reduces component rejection to practically nil and assures that the finished product meets international standards. Our tool specialists construct special-purpose production equipment, testing fixtures, injection moulding tools and press tools.
To develop a comprehensive production facility, this facility has a dedicated tool room. As customer loyalty is measured by our quality, we take very strict precautions to ensure that all of our goods are thoroughly inspected and tested at various stages of production, thus reducing component rejection to practically nil and ensuring that the end product meets international standards. We have a variety of high-tech inspection machines for profile and surface polish, case depth, complex geometry, carbon and sulphur analysers and other parameters, as well as measurement and metallurgical inspection.
How are you strengthening and increasing your presence in the aftermarket, which is one of your key business verticals?
The global automotive bearing aftermarket is benefiting greatly from the global expansion of the automobile industry. The demand for automotive bearings is continually increasing owing to the increased production of passenger, luxury, commercial and other types of vehicles. According to industry research, the worldwide automobile bearing aftermarket would increase at a 3.4% compound annual growth rate (CAGR) from 2020 to 2030. To fulfil the global needs of the vehicle industry, we are increasing our aftermarket product offering. We are constantly developing our manufacturing techniques in order to deliver OEM quality for the aftermarket industry.
What is the size of your export market? What is your plan for extending your global presence in terms of entering new areas, attracting new customers and increasing your brand portfolio?
Small and medium vehicle component companies were generally unscathed by the severe interruptions created by the numerous waves of the pandemic that began last year due to a constant flow of export orders and a resurgence in automobile sales following last year’s lockdown. We have a significant amount of business in the international business segment, which has supported and encouraged us to be positive, which is what we are currently pursuing. Despite global challenges, export orders have remained consistent and are expanding. On account of the recent ups and downs in global macro-economic factors, we are highly interested in accessing the global market.
That is because it provides us with the opportunity to get new consumers from East Europe and the Russian Federation as well as other European nations, including the Middle East. We provide premium quality items to our existing clients and adhere to the same quality standards when supplying to new consumers. In fact, we are receiving inquiries from the international market for new product lines. We are employing new and innovative ways in order to retain higher quality while keeping product costs down. This will help us to offer our new customers the best possible cost.