“We have equipment operating in some 85 countries, we’ve had occasion to work with most chassis and prime mover manufacturers around the world. India is no different. However, with the haulage industry now using more and more prime movers, close co-ordination needs to occur in-terms of drawing (AutoCAD) and detailed specification sharing from the manufactures regarding items such as fifth wheel heights, electrical and service couplings, braking systems, so as to provide for a smooth and safe coupling between the prime mover and the trailer,” remarks Jeffrey M. Edwards, Director of Export Sales & Marketing, Heil Trailer Asia Ltd., on the subject topic.
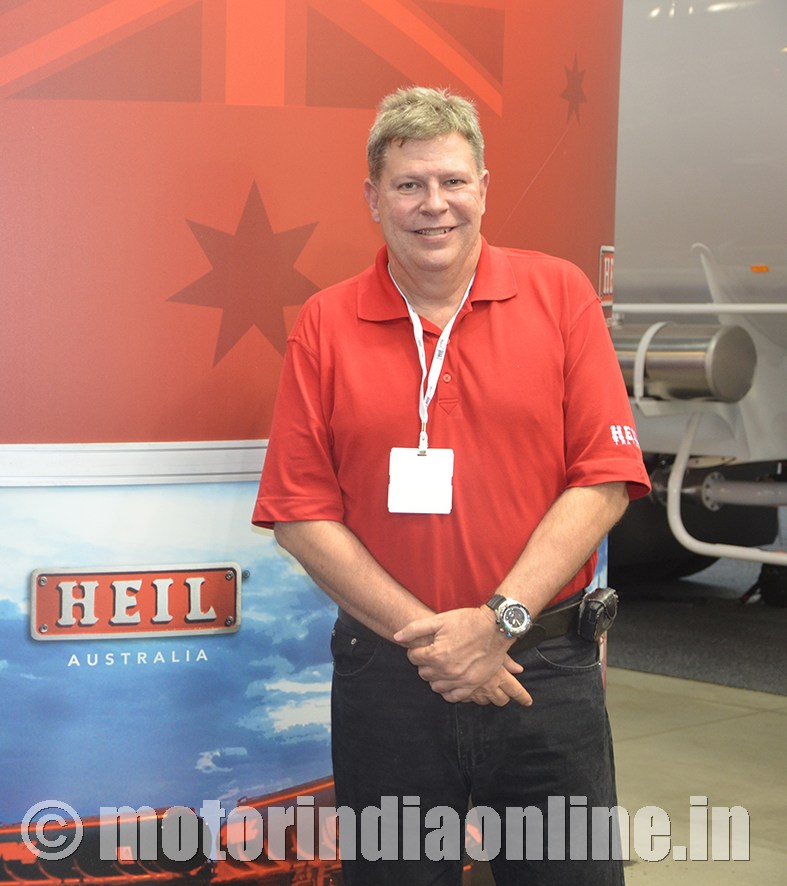
Excerpts:
Mandatory and other safety requirements
We have keenly been following the recent ARAI initiatives as they apply to our segment of the industry, and welcome them as a means of “raising the bar” for safe tanks and trailers, especially in the hazardous and dangerous goods sector. Aside from other CCOE, RTO, etc., directives, we also follow the UN-ADR code of manufacture for our tanks and trailers, which provide for additional safety through a prescribed manufacturing process that is used in many countries worldwide.
We have thus far provided both petroleum semi-trailers and pneumatic bulk trailers to the market, manufactured with aluminium. As a non-sparking, malleable material, aluminium offers a number of safety advantages in transport. Our company goes to great lengths to insure ergonomic efficiencies in the operation of our units, with items such as continuous access/non-slip handrails, working-at-height systems, pedestrian underruns, brake interlocks, emergency shut-offs and advanced lighting to help provide for greater driver and public safety.
Safety features and highlights in operations
On recent visits to India, we have been pleased to see an enhanced focus on training and curriculum, specifically as it relates to the haulage of hazardous and dangerous goods. This is a particular focus of most multinational oil companies who are now starting to enter the Indian market, bringing with them various systems that have been proven effective on a global level. When it comes to safe operation of our tanks or trailers, we provide comprehensive owner’s manuals, which provide both the owner and driver with a thorough operating knowledge of the unit, as well as clearly spelling-out various safety checks to be carried out in-order to insure the safe operation of the vehicle.
Figures indicate that human error accounts for as much as 90% of all road accidents. Obviously, this means that there needs to be a continual emphasis on driver training, with safety for the vehicle associated with such items as mandatory ABS and now EBS (electronic braking systems), coupled with RSS (roll stability systems), code enforcement of low centre of gravity requirements, mandatory underrun protection, hi-viz tapes and decals, consistent and enforced lighting standards, will all assist in making for a safer commercial vehicle.
Safety apprehensions at higher road speeds
Bear in-mind that while transit time is shortened, increased fuel usage will also result. The increase appears to be more geared to passenger and light commercial vehicles, while operators in the heavy, and in particular, hazardous and dangerous goods vehicle sector traditionally impose strict vehicle speed limits on their drivers for the basic reason of increasing response time in the event of critical situations relating to braking, exiting, lane changing, etc.
Technology impact on safety in the times ahead
I’ve personally been coming to India for almost three decades now, and I have seen tremendous positive changes over the years, particularly in the last decade. I believe that all of the technologies that you cite will be rolled out in the very near future to varying degrees. With specific regard to heavy vehicle transport, items such as electronic braking systems (EBS), GPS, multi-position cameras, mandatory cabin air conditioning, automatic transmissions, etc., will all soon be finding their place in the Indian commercial transport scene.
Light-weighting necessity and trend
Sometimes, “light” can go too far, and that’s why there are generally manufacturing codes in-place around the world, which dictate materials, material thicknesses, testing procedures, etc. It is apparent that India is now embracing standards and codes that will help guide the manufacturing industry in the direction of lighter and more efficient vehicles.
Our company built the first aluminium petroleum trailer in 1940, and has been introducing light-weighting options to the industry ever since. The highest cost in any haulage operation is fuel, and “real world” studies have shown that aluminium tanks/trailers can reduce fuel consumption by from 6% to 10% over similar mild steel units, which in-turn reduces the carbon footprint of the vehicle. Aside from fuel savings, additional savings are found in increased payload, greater tyre and less engine wear, as well as a high residual market value for the alloy tank/trailer.