The Indian coach-building industry is still recovering from the disruption that came in the form of bus body codes, yet its spirit is indomitable. This is fairly apparent from the new crop of young entrants that have stepped into this segment of late, defying all the odds that the industry is still plagued with. The newest of the lot is Shatrunjay Coach Builders from Kolhapur. In an exclusive interview with Shivam Gautam, the company’s proprietor, Chintan Rathod, shares details about the venture and his strategy to occupy a niche place in this sector
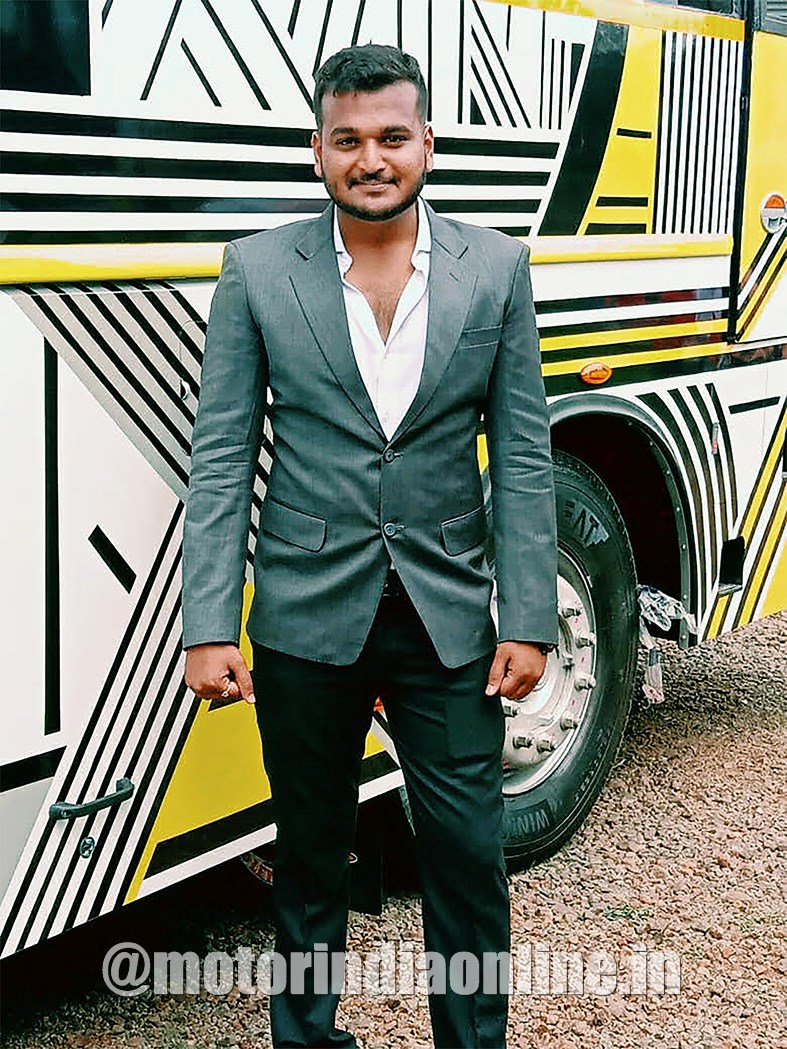
Launched in 2019, Shatrunjay Coach Builders is spearheaded by young and aspiring Chintan Rathod with the sole aim of providing a state-of-the-art bus body building facility in South Maharashtra. A bus operator himself, Rathod has been conversant with the modern consumers’ demand and is focused on building a bus body facility that takes into account every passenger requirement. Armed with the knowledge that he acquired under the tutelage of Srinivas Reddy, Managing Director, Veera Vahana Udyog (P) Ltd., Rathod has been successful in launching the first set of buses in September 2019 to warm response from the industry, fleet operators and bus enthusiasts alike.
Excerpts from the interview:
As a new entrant in such a competitive industry, what edge do you think can possibly work in your favour?
The bus body building industry is filled with veterans and we are just a few months old and therefore it is not going to be a cake-walk for us, especially in terms of trust and brand building. But what we can currently afford is to focus on having faith in ourselves and be confident of projecting this approach while making people understand about our products. My long-standing experience as a fleet provider definitely gives us an edge because I am very aware of the demands of the passengers of today as well as the drivers. We aim to be a market leader and not a follower in the coming future, and we want to achieve this by dint of innovation and technology both in our processes and our products.
Could you share details about your latest models and their salient features?
On September 29, 2019, we introduced our first model named Chetak that features immense innovation in both interiors and exteriors. The aesthetics are vastly different from what you normally see in the market as are the graphics. On our first consignment we have featured graphics that have never been seen before on Indian roads. The interiors are furnished with in-berth shoe racks, ambient lights, and the fabrics used are of top-notch quality. There is another feature that stands out in our buses. Normally, Indian buses have a lot of rear lights which tend to disturb drivers behind the vehicle.
To change that, we decided to feature only tail lamps and head marker on the rear – it sort of keeps it simple and elegant. In accessories, we advise USB sockets because there have been instances of lights and inverter or battery malfunctioning triggered by three-pin sockets. CCTV cameras should also be a must in every bus with regards to passenger safety, along with rear view cameras. Other than these, there are many devices available for safety, maintenance, tracking, etc., but it ultimately depends upon the client’s requirement and budget.
What is your approach to designing and what tools and technology do you bank on while designing your products?
We have designed our first model as per the codes and specifications laid down by the ARAI as well as considering every safety aspect possible. We are backed by a young and dynamic team of designers who are very focused on bringing out fresh and unique bus body models. As of now, AutoCAD is the basic software we are using but we are vying to try out other modern software that can aid us with both the interiors and exteriors of our buses.
Are there any new models that you are planning to release in the near future?
As of now, we are planning to modify the existing model and make it simpler to work on during breakdowns. Once we are done with it, only then we may consider launching new models. Honestly, this is a long procedure and it will take time.
Could you elaborate about your quality testing procedure?
Our company practices KAIZEN, which basically means continuous improvement or change for better. With this approach, our team is working with dedication to increase the overall productivity, and improved quality, that ensures value for money for our clients. Another quality system which we are practicing on a daily basis is ‘quality circle’ that enlists the help of employees in solving problems related to their jobs and to devise solutions for improvement. In addition, we also exercise strict traditional quality assurance processes and inspect our products at every stage of the production – right from job induction to pre-delivery inspection. There also is a feedback form given to the customers at every stage where they can suggest or ask for a change in material or quality.
What do you think about the current standing of the bus body building in India as a whole?
All the stakeholders have changed in this industry in recent years – right from fleet owners, bus body builders to the end consumer. Earlier, passengers were unaware about the fact that bus bodies are built by a different entity altogether, but now a radical shift has been witnessed. The modern passenger is a well-informed passenger, knows about bus body builders, and has immense demands. So, in line with it, I think that the bus body building industry is driven by a momentum that has been hitherto unseen. In the last few years, there has been a paradigm shift towards technology and innovation. Every brand is stepping up to making products that are superior, innovative, and unique enough to help them to stand out and emboss a name for themselves. It’s a welcome shift as it has helped the overall market to grow in the right direction.
As a stake holder, what do you think are the challenges that the bus body building industry in India is facing now?
The market is shaping up rapidly and it is very competitive. With various unorganised body building units in operation, the organised players of this industry face a lot of problems, mainly regarding labour. I also hold that some government norms, mainly bus codes, have been unsuitable and unnecessarily imposed on us. As a bus body builder, I would request the government to bring down the GST rate for the body builder. This would also be a beneficial move for fleet operators as well as the transport industry in India as a whole.
“I think that the bus body building industry is driven by a momentum that has been hitherto unseen. In the last few years, there has been a paradigm shift towards technology and innovation
– Chintan Rathod, Proprietor, Shatrunjay Coach Builders
Key facts
- Name of company: Shatrunjay Coach Builders
- Year of establishment: 2019
- Designation of spokesperson: Proprietor
- Headquarters: Kagal, MIDC, Kolhapur
- Location of manufacturing plants and size: 1 acre plot
- Certificates and accreditation: ARAI and ISO under process.
- No. of workers: 65
- Time required to complete one body: Non-luxury (50), luxury (60) and sleeper (75-90)
- Website: www.shatrunjaycoachbuilders.com