Sika is a market leader in the adhesives & sealants technology for the global bus markets, manufacturing and supplying products for bonding, sealing, damping, reinforcing and protecting in buses and coaches, apart from other applications. Sika has developed numerous products, specifically for the bus industry, and works with almost all leading OEMs and bus body builders in the Indian market as well.
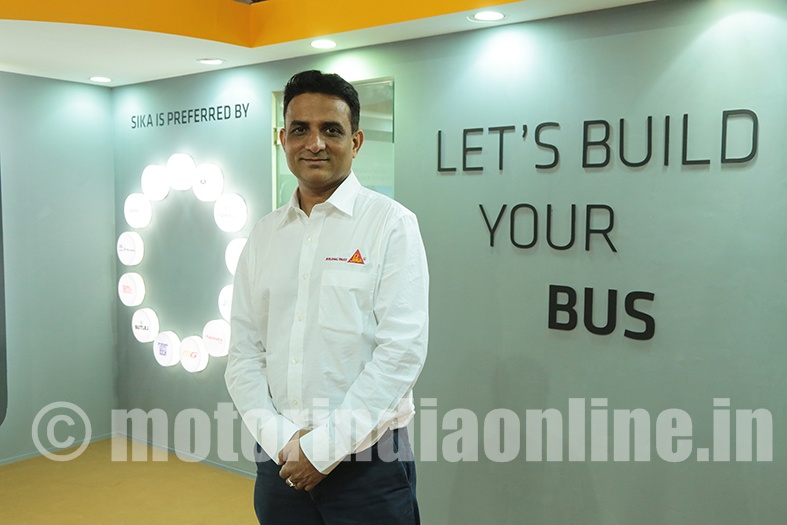
We spoke to Mr. Pankaj Sharma, National Business Development Head – Transportation and Marine, Sika India Pvt. Ltd., to know more about the company’s focus on safety.
Could you give us some insights on Sika’s focus on safety through your wide array of products and solutions?
There are safety regulations laid by the Automotive Research Association of India (ARAI) for conformity of production of critical components. For example, AIS 031 (Automotive Industry Standard) defines procedures for type approval and certification of vehicles & compliance to the standards of super structure roll over test which is critical for safety of passengers. Similarly Bureau of Indian Standards IS 13944 is to be followed for window retention and release system for buses, to meet the above regulations.
Sika has dedicated product range, namely, SikaPower, Sikaflex and SikaForce. For example, use of our adhesives and sealants in structural bonding application of buses and trucks provides the following advantages along with enhanced safety: large stress-bearing area, excellent fatigue strength, damps vibration and absorbs shock, minimizes or prevents galvanic corrosion between dissimilar metals, joins all shapes and thicknesses, provides smooth contours, seals joints, joins any combination of similar or dissimilar materials, often less expensive and faster than mechanical fastening, heat, if required, is too low to affect metal parts, provides attractive strength-to-weight ratio, greater torsional stiffness, better design possibilities, increased driving comfort, and noise reduction.
Stricter Fire & NVH norms can be met with Sika’s fire retardant products and under body coatings Sikagard.
Sika offers a number of bonding solutions where safety is a very critical parameter. Could you highlight some specific safety aspects of your adhesive solutions?
Like many other bus components, bonded windshields have also experienced a change in their function. In addition to their original task, that of protection from wind and water, dust and rain, directly glazed windshields in modern buses contribute greatly to torsional stiffness. This means the passenger compartment undergoes markedly less torsional movement under the same loads than with conventionally installed windscreens.
The resulting advantages, for example, lighter bodywork, better driving characteristics and less interior noise, are the hallmarks of modern buses.
In serial production, almost every bus is directly glazed using polyurethane adhesives. Advantages and benefits are: reduction of stresses in the glass, Increase in body stiffness, lower glass breakage, increased travelling comfort (interior noise), styling freedom, behaviour in a collision (Better results in crash test), increased safety requirements, assembly process more simpler (less installation effort), and automation possibilities.
Windshield bonded with adhesive provides one-third of the structural integrity for the roof of the vehicle. It’s there to keep the roof from crushing in during a rollover and in car bonded windscreen even helps the airbags on the passenger’s side to use it as a backboard.
Can you comment on the impact new and futuristic technology might have on the safety of the products you supply?
New Technology always comes with a lot of challenges. For example, fire-retardant adhesives and sealants fulfils the European fire regulation EN45545. However, such specific fire-retardant raw materials can have implications on other product properties also. For instance, the adhesion. Hence Sika ensures proper adhesion test with actual substrates prior to use of these products in the proto building.