The Advanced Application Summit held in Bangalore in June enabled Stratasys India, a subsidiary of Stratasys Ltd., a global leader in additive technology solutions, to push ahead further on what’s possible with 3D printed prototypes, empowering customers to deliver highly realistic, vibrantly-colored parts at speeds up to 5x – 10x faster and more cost effective than traditional manufacturing.
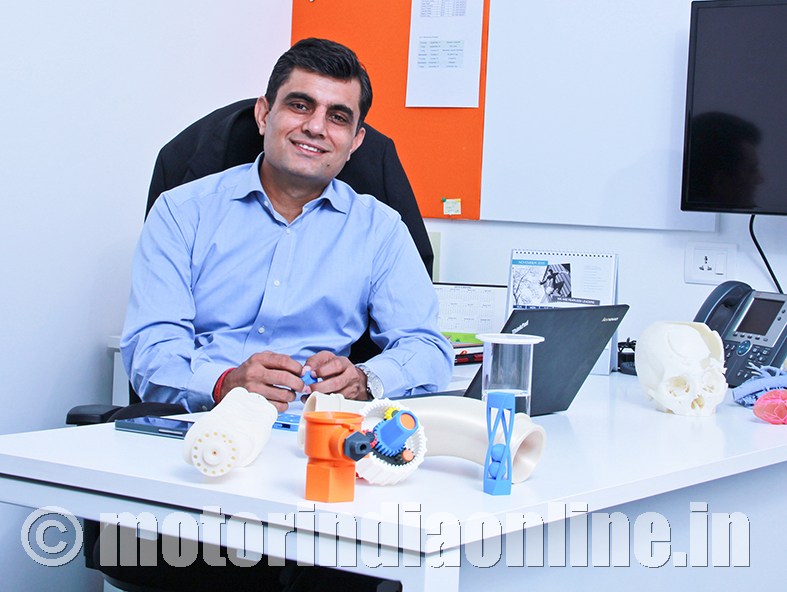
The focus of the summit was to provide a platform to introduce Carbon Fiber Filled Nylon 12 material and Vivid Colors to Stratasys end-users. Additionally, it brought together Stratasys experts to share first-hand information on the impact of the new addition of materials in today’s globally competitive manufacturing ecosystem.
“Today there is a vast market opportunity in product prototyping that we feel is not being addressed by current 3D printing systems. To keep pace with the fast-changing auto-tech industry and the evolving customer base requires new levels of innovation in 3D printing. The new introduction of Carbon Fiber Filled Nylon 12 material and Vivid Colors can transform the overall design, provide greater efficiencies and reduced time to market”, said Mr. Rajiv Bajaj, Managing Director, Stratasys India.
The newly-advanced J750 and J735 are engineered to power prototype creation in industries ranging from automotive and consumer goods to research and education. Additionally, two new materials – VeroYellowV and VeroMagentaV – deliver enhanced red/orange/yellow colors with next stage translucency, a perfect match for consumer goods and models used to represent automotive lights and housing. These advanced colors are available on both the J750 and J735 3D Printers, as also on the Connex3 3D Printer.
“With the new vivid colors solution on the J750 3D Printer, we can produce prototypes with incredible realism, such as the transparent multi-color covers for our tail lights. This can offer the texture and color-matching requirements to meet our design approval process,” said Mr. Reinhard Schiechel and Dr. Tim Spiering, Audi Model shop and 3D printing center.
“This ability to produce transparent multi-color prototypes that so closely mimic the final part, in a single print, might significantly reduce the time and cost required for each design process. Consequently, we could free capacities to run through more iterations and improve overall design, while accelerating our time-to-market,” they added.
Stratasys also featured its high-strength FDM material – Nylon 12CF – at the Advanced Application Summit. FDM Nylon 12CF is a chopped carbon fiber-filled (35% by weight) polyamide 12, available on compatible Fortus Production Systems. The material has a high strength-to-weight ratio and a tensile strength on par with other high-performance FDM materials.
Due to the unique directional orientation of carbon fibers, it enables parts to have a higher uniaxial stiffness than injection-molded parts of the same material. It opens unique design freedoms, not present in either traditional thermoplastic or additive manufacturing.
These characteristics make FDM Nylon 12CF a good fit in a variety of functional prototyping and tooling applications, namely, Aerospace (UAV components and tooling), Transportation and auto (bumpers, fixtures and brackets), Consumer (performance sporting goods) and general manufacturing (tooling, fixtures and other manufacturing aids).
Mr. S. Rajan, General Manager – Product Development, Ashok Leyland Ltd., one of the distinguished speakers at the summit, thanking the Stratasys team, said: “It was an exciting event to interact with OEMs and suppliers from various industries to share the experience and best practices in ‘3D Printing’. Let’s innovate and keep adding value to our customers consistently as ‘Customer is our Boss’ ”.
Mr. V. Sridharan, CEO, FIRST-TBI, Foundation for Innovation & Research at SASTRA Technology Business Incubator SASTRA Campus, said: “It was a well conducted event, and we got an opportunity to meet a number of experts from the industry and had knowledge exchange sessions to get an insight into Stratasys offerings and upcoming features for industry applications.”
“The session from Ashok Leyland was very useful to know how the automotive industry is leveraging the Additive Manufacturing technology. The kind of savings proven by Stratasys FDM machines at Ashok Leyland was a great testimony indeed. From the CAIR scientists’ presentations, we got an overview of the usage of 3D Printing in Robotics space. It was very impressive and informative”, he added.
Congratulating team Stratasys for arranging special theme-based events for the first time ever in India by any 3D Printing company, Mr. Sridharan expressed the need for more such sessions around healthcare and other industry verticals in future.