Since commencement of operations in 1961, TEXSPIN has achieved several milestones and is today amongst the top global bearing company with manufacturing facilities in India. Although the company specializes in manufacturing of clutch bearings in India, it has grown to innovate and spread its business verticals, implanting focus and dedication in several segments namely, Transmission, Steering, Wheel end & Taper, Suspension and Engine Bearings. We caught up with Mr. Dipen Makwana, Managing Director, at the company’s Ranpur office to understand the activities undertaken by them in various segments.
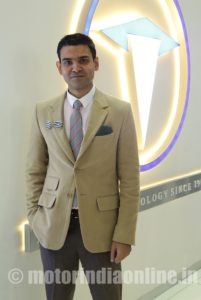
Focusing on value creation
Innovation is in the DNA of the company and it continuously strives towards innovative technological solution to address customers’ improved application requirements. By doing so the company tries to add value to the problem that the clients might be living with. Said Mr. Dipen Makwana: “Our core product has always been clutch release bearing and so when we thought of innovation, we went with the idea of forward integration on the clutch release bearing. The result was the concentric slave cylinders; some may even call it hydraulic clutch release bearings. It is one generation above the conventional mechanical bearings and operates through hydraulic system compared to the mechanical linkages.”
Manufacturing of Clutches is another forward integration and it is a completely new segment that TEXSPIN has ventured into. “We are seeing a lot of positive outcome in that. It has been one and half years that we have launched the clutches first in the aftermarket and within a year it has grown to reasonable figure in terms of business size. Also, more importantly, we are in the process of working with a lot of OEMs,” he informed.
Notably, TEXSPIN has a new plant adjacent to the present one, around 4 km away, with a build-up area of 46,000 sq.m. Apart from productionising various new technologies, the plant will incorporate further expansion into the present product segment to add capacities and new product lines.
Transmission synchronizer rings & wheel hub unit
It is extremely challenging to handle different segments, especially to create innovation in several product lines. TEXSPIN addresses this challenge with focused approach. “One of the key innovations that we have done in our transmission segment is the synchronizer rings. We have come up with stamped synchronizer rings for both Passenger Vehicles as well as the Commercial Vehicle segment. Changing from the forged part to the stamped part is not easy. Forging allows for a lot of machining allowances, while in the stamped synchronizer rings the required precision level is very high and involves a lot of complicated tools which demands a high degree of expertise,” he explained.
In the Wheel-end bearing segment, TEXSPIN has a range of unitized taper wheel end bearings which provides a lot of advantages to the customers. The company has developed a unique complete hub unit with unitized double row taper roller bearing which has maintenance free sealed for life and long enduring life features. It has optimized hub design and can be easily fitted directly into the axle.
“In the wheel end we have converted the standard ball or the taper bearing into the i-ball bearing. I ball bearing integrates the hub and the bearing outer intone unit and so, the hub is the integral part of the bearing. Earlier the hub used to be a separate component, and one had to fit the bearing. That is why we call it an integral ball bearing (that’s why named it as I -ball bearing),” beamed the MD.
Growth amid changing regulations
Since the company has proactively worked on innovation and changes, up till today and any material standard regulation or changes in emission norm has not affected them. “We have stayed ahead of norms and offered solutions that address client’s problem. We have a lineage of innovation. Regarding hazardous material, generally, in bearing, it is a combination of two or three material and we don’t have too many materials. We have got bearing steel, cages, which are stamped or are in plastic material and sealing are in rubber. These materials are again in use for quite sometimes. Even for coating, we do not have too many varieties and bearings are either coated for anti-rust or anti-friction. Those are either coated with anti-rust oil orphosphate and even over there the material that we use in coating are of International Material Data System (IMDS) certified,” he elaborated.
Demonetization did hit the industry, and TEXSPIN’S growth was marginally impacted during Q3 but overall the growth momentum is on track and working towards achieving the growth targets set for the company. “Demonetization hit our growth by a few per cent but we feel it would be compensated as we are experiencing a revival in the demand in the last quarter. Three months of slowdown effect in a twelve-month period is a lot to cover but we are confident that a substantial part of the gap will be covered by the time the year closes. Today we have a healthy portfolio of 60 per cent OEM customer and 40 per cent aftermarket. Our growth aspirations will be a combination of OEM, aftermarket and exports as we are working with a lot of European OEMs and ultimately will help us achieve our aspirations to grow at above the industry average to add value to all the stake holders,” concluded Mr. Makwana.