Timken India Ltd. (Timken) has led the industry with significant breakthroughs in bearing technology offering friction management solutions that maximize performance, fuel-efficiency and equipment life. Wherever parts move and turn, Timken products and services have made things run a little smoother, safer and more efficient. We caught up with Mr. Sanjay Koul, Managing Director – India, Timken, to understand recent developments at the company.
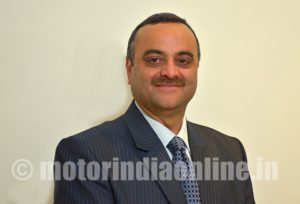
“We have had a double-digit growth and have been doing fairly well in the last one year. Apart from M&HCV segment, the general market sentiment was subdued, agriculture and off-highway segment have also showed signs of revival. We continue to grow at a CAGR of 10 per cent for the last three years and have managed to clock a turnover of Rs. 250 cr. in India through a large portfolio in commercial vehicle, railways and exports,” informed Mr. Koul.
Variations offered
Timken offers a growing portfolio of engineered bearings, mechanical power transmission products and industrial services to keep industries moving efficiently and reliably. Add to that the changing varieties as per new customer requirements. “We have had a wheel pack solution both for OE and aftermarket. For rolling motion bearing, we have fleet ultra, offering 500,000 km grease, first time in India. We also have designed an 8-inch bearing that can take similar power that a 10-inch bearing can take. It is a fuel-efficient bearing through power-density solutions,” beamed the MD.
To avoid any problems during the life-cycle of the bearings, Timken have invested in major rig-testing facility in India, Europe, China and the US. “All bearings are tested under load conditions to check if they can withstand the temperature. Lube film breaks down at high temp, so the metal-metal contact will kill the system. Speed, temperature, vibrations, life span are all tested,” he added.
Many advanced coatings- advance life, bring down vibrations, makes them clean. “We offer debris-resistant bearings, corrosion resistant bearings, advanced coatings to give true rolling motion. These will be effective when new BS-VI norms are implemented. We can also achieve lower weight, better load carrying, lessening shaft diameter by advanced material and metallurgy science. We are already doing a lot of application engineering in India. For light-weighting advanced heat treatment is a continuous process,” he revealed.
Talking about the company’s sustained Make-in-India drive, Mr. Koul concluded: “We want to contribute to PM Modi’s vision of ‘Make in India’, ensuring whatever is sold in India is made in India, will lead to a profitable growth. To be a global manufacturing hub and be a partner for Timken’s growth globally, we have a Tech centre in Bengaluru powered by efficient Timken India engineers. We can create an ecosystem that makes for the world”.