BytEdge offers IoT-driven smart platform that uses digital twins with machine learning and AI for predicting product and component failures, providing a virtual connected design, simulation and optimisation capability
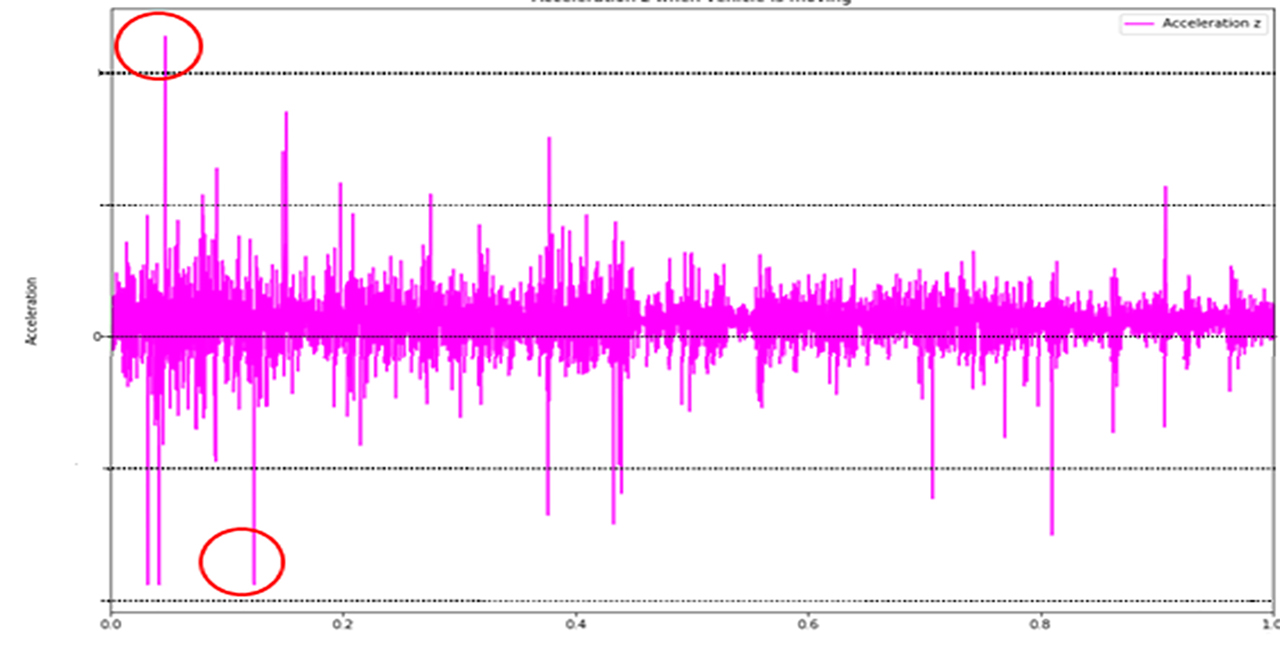
Earlier, if a detergent bar had to be validated for strength, it was physically shipped from one destination to the other and manually checked at its destination to see if any damages had occurred on the detergent bars during transportation. This process of course was time-consuming and took as many as three months. If breakages were detected, the product had to be re-designed and then the transit trials had to be conducted again. This manual and time-taking process has now been replaced with virtual simulation of the transit trials. Now design changes can be done with very high level of confidence.
In virtual transit trials the 3D CAD model of the detergent bar with packaging are applied with the actual loads coming during shipment. The results from these virtual computer models indicate whether the new design is capable of surviving shocks and vibrations faced during transportation. The most optimised model can be arrived at without actually building a physical prototype. This is where BytEdge steps into the picture. The company’s IoT-driven smart platform uses digital twins with machine learning and AI for predicting product and component failures, providing a virtual connected design, simulation and optimisation capability.
BytEdge has offices in USA, New Delhi, Pune and Hong Kong. It works in the automotive, logistics, ESG and industrial sectors. “We have undertaken and successfully implemented large design validation and design optimisation projects. Companies that have implemented our solutions have seen a design cycle time reduction of up to 95%. We have implemented our solution in one of the largest FMCG companies in India and they have managed to cut down their transit trial time from three months to three weeks for every design and shape change that they make to their product,” a press release states.
The accuracy of the results obtained from these virtual models depends on how accurately the company models the road load conditions. In order to measure these loads accurately, an IoT device was built where force transducers and accelerometers were placed within these boxes of detergent bars which were transported to different parts of India. The data of forces and vibrations collected in real time were sent to the platform for running the simulation models. This gives very accurate results from the simulation. The process of virtual transit trials allows the marketing team to check the strength of many different shapes and sizes of the product.
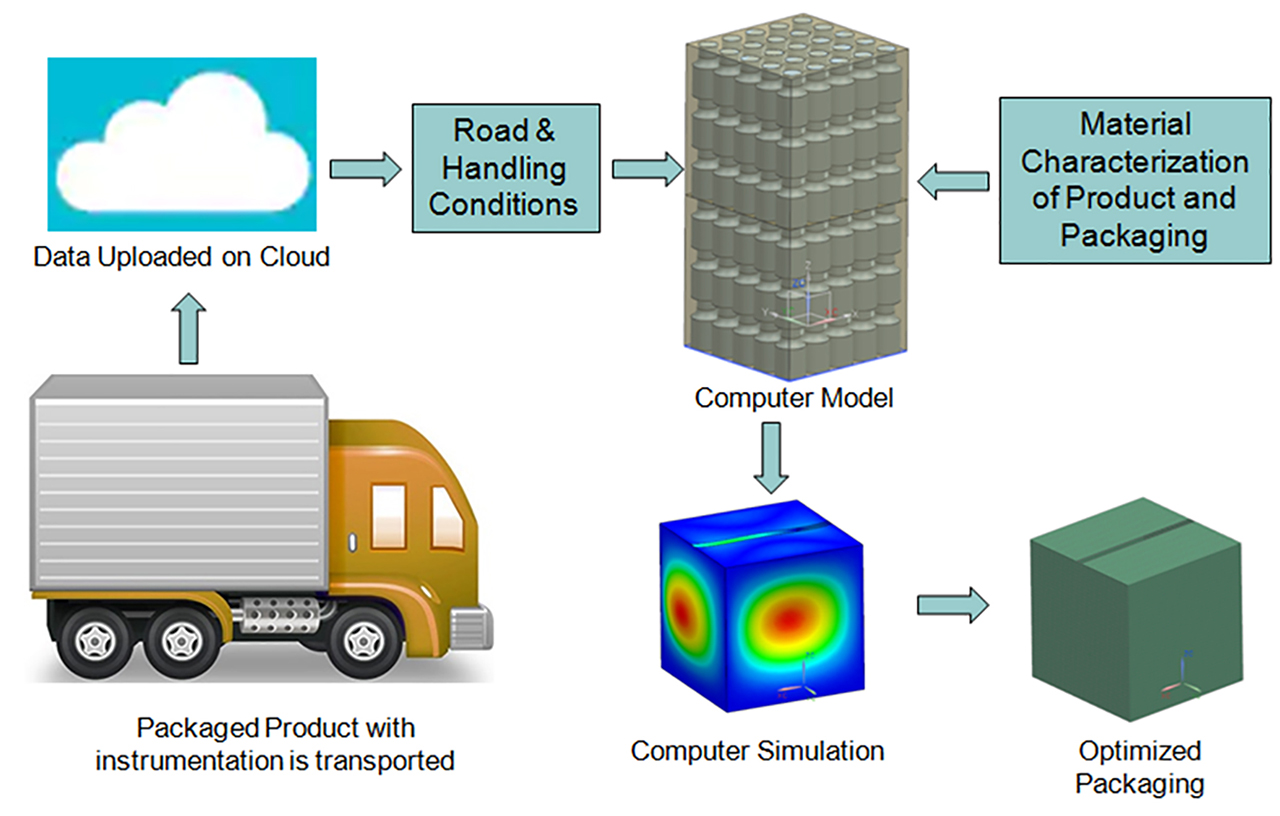
They can then arrive at the design of a product which looks appealing to their customers and also strong enough to survive the rigours of transportations through different routes. “This data is also being used by our customers to program their vibration shaker for physical testing of their products in the labs. With this process, the vibration shaker is able to replicate the road condition of different routes which are being used for transporting their products to different markets. After the vibration shaker is programmed with these specific road conditions, the physical samples are loaded on the shaker and subjected to the same vibration and shock as they would experience while in transit,” the release states.
After the tests are over, the physical samples are inspected to determine if the product has been damaged,” it adds. The vibration and shock data which is collected also gives an idea on the driving behaviour. It indicates whether there were hard accelerations and hard braking during the transit which would indicate aggressive driving. This increases the risk of product damage during transit. The driver of these vehicles can be then coached for safer driving behaviour. Another important aspect of these virtual tests is the material characterisation of the product. “Unless we define the material properties and the material behaviour correctly, the results and predictions that we get from these models are incorrect,” the company states.
“After extensive research and study, we have been successful in modelling the material properties and the material behaviour correctly,” the company adds. Incorporating these material properties and the material behaviour in such simulation models give a good correlation between the predicted simulated results and the observed behaviour of the physical samples in transit. With this solution the physical transit trials which took about three months to complete have been replaced with virtual transit trials which take about three weeks to complete, with the option of trying out many different shapes and sizes of the product.