The Gujarat-based Vasant Fabricators (VF) is into its third generation now. A fabricator of regular and tip bulkers and chemical tankers, VF is a market leader with its knowhow in making specialised heavy bodies. Twenty-seven-year-old Mr. Nikhil J. Panchal, the company’s Technical Director, is soft-spoken and unassuming, and has a legacy to carry on from his grandfather, Mr. Ganpatbhai Panchal, and his father, Mr. Jagdish Panchal.
Belonging to the village of Chhapi, nearly 130 km by road from Ahmedabad, VF started business by manufacturing cages, small tankers and vessels. The youngest Mr. Panchal shares: “Even today our main unit is in Chhapi. It was in 1983 when my grandfather came to Ahmedabad and set up the business. Then my father joined him, and they started making chemical machinery. And I joined the business in 2008.”
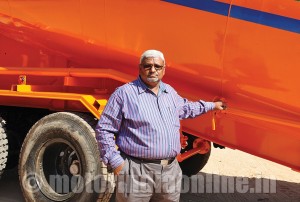
Even today his 84-year-old grandfather visits their unit in the village to oversee the work there. Neatly segregated work allows his father to manage operations and production in Chhapi, while Mr. Nikhil Panchal looks after technical aspect of the business. His younger brother, Mr. Vinit J. Panchal, is responsible for taxes and accounts. Currently, VF records an annual turnover of Rs. 18 crores.
The pioneers
It was in 1999 that VF received enquiries for cement bulkers. He says: “At that time, cement companies in India bought bulkers from Australia and Germany. With the growing demand in India they looked for locally made bulkers. But there were few manufacturers of cement bulkers. And we were only making chemical and storage tanks, and chemical equipment. My father studied the requirements of these companies for 5-6 months and then started making them.”
Since then, the journey became fast paced with the first chemical tank, measuring 12 cu.mt., which was made in 90 days becoming the first of the five bulkers ordered by Prem Goods Carrier. In the next four years, VF increased its capacity to make 45 tankers a month. With increased payloads, demand grew for bigger bulkers. VF continued to develop bulkers of different sizes as per the demand and went up to making 25 cu.mt., a first of its size in the industry for transporting cement and fly ash. In 2002, VF introduced a new element in its bulker design – a pneumatic compressor – aimed to eliminate external force to unload.
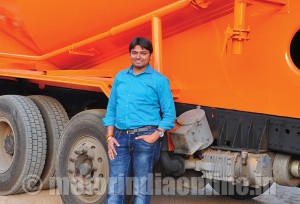
Mr. Panchal adds: “Going by the demands of the market, we made 27 cu.mt. bulker even when our competitor made only 24 cu.mt. At that time, only a 10-wheeler truck was available in the market with 25 GVW. In 2004-05, the 12-wheeler was introduced, for which we made 32 cu.mt. bulker.” The 32 cu.mt. bulker gave VF monopoly in the body building market.
VF uses aluminium and stainless steel for chemical tankers. Mr. Panchal says: “We have produced upto 900 units of 32 cu.mt. bulkers in the last four years which were all sold in Bilaspur, Himachal Pradesh. In the hilly areas, big trailers are unable to take sharp turns with heavy loads. We gave them a compact model of 32 cu.mt. bulker and it became a big success. We have captured 85 per cent of the market share in Himachal Pradesh. Pan-India, we have 30 per cent market share.”
Today VF supplies to companies like Chennai-based Ammayapper Roadways, Kolkata-based Naresh Kumar & Co. dealing in transportation and mining, Bangalore-based Aditya Auto Engineering and similar such companies in Rajasthan and Maharashtra.
Currently, VF is attracting orders from customers dealing in coal mining for the tipper segment.
Designer bodies
VF prides itself on its strong foundation of design. Mr. Panchal observes: “My father built our first tip bulker in 2008 in just four months after studying the products on display at an international exhibition in 2006. Presently, we are making nearly 7 tip bulkers a month with capacity of upto 58 cu.mt.”
The design genes have faithfully passed on to the youngest generation which has helped them cater to an impressive clientele, including JSW, Vizag Steel Plant, Tata Steel and SAIL for whom they supply rail bulkers. He adds: “We are dealing with Technimont ICB based in Mumbai, then with ONGC’s plant in Dahej for which we have been supplying special trolleys for two years now.” If not for VF, ONGC would have to procure them from Spain.
Whether it is V-shaped, tip or hopper type bulker, VF makes them all. He says: “We rolled out the first tip bulker in 2008 for hauling loose material like flour. We made hopper bulker measuring up to 62 cu.mt. in 2012 measuring 42 feet in length to carry up to 32 tonnes of low density fly ash.” VF has the knowhow to make a hopper bulker of up to 75 cu.mt. also.
It also helps today’s transporters, whether of new or old generation, opt for hassle-free transportation and best machinery. Hence VF has taken up the task of training the clients’ technicians, besides supporting them with AMC for bulkers bought from them. On a note of pride in his voice, Mr. Panchal says, “they have been running these bulkers for the last 12-13 years.”
The credit for all this surely goes to VF’s 50 different designs that cater to a range of models and application. With the current customer base transporting ingredients ranging from soda ash, bentonite sand, dolamine, melamine, purified Teraphatic acid or PTA, to lump lime, VF is more than happy to create and develop specialized heavy haulers. According to Mr. Panchal, it is currently the only manufacturer in India of tip bulkers made specially for soda ash.
VF has an installed capacity to produce 50 bulkers of different sizes a month though presently it is producing up to 35 units. The work floor is equipped with CNC profile machine, short blasting facility and paint booth, among other such machinery. Besides, it has built a residential colony for the outstation engineers and work hands.
Product portfolio
Convincing a customer to opt for quality over price is a challenge. Mr. Panchal shares: “Our conventional bulkers cost from Rs. 3.10 lakhs and V-shaped bulkers cost upto Rs. 22 lakhs, whereas tip bulkers are priced at Rs. 9 lakhs, and we have sold upto Rs. 28 lakhs. The hopper type bulker is an expensive product compared to the conventional one. Honestly, we have not sold as much as we would have liked. That is because hoppers need special application and not much awareness is there about them. They cost from Rs. 7 lakhs and goes up depending upon the capacity. We make them using hi-tensile steel and aluminium. In India there are very few who do aluminium fabrication.”
Soon to be added to the VF product range is the windmill trolley. With new stipulations from the Government, trailers carrying windmill blades must be flexible. Mr. Panchal says: “A trailer now should be able to fold down to a smaller size on its return journey. And they come with steerable axle at the rear, so they can turn into even extremely narrow spaces also.”
According to him, there is absolutely no competition in this segment, and the market is looking robust.
Another new trend is that of silos. If the world has been long using them, India is hesitant. Why is the uptake slow? Mr. Panchal answers: “Silos are new in our product portfolio. But the customers feel stealing of cement is easier from a silo because of the direct valve. Then, it is about the measurement, the material being used, and safety in narrow spaces.”
It is true that resistance is high when anything new is introduced into the society’s psyche. When bulkers made an appearance on the scene, they were not accepted readily, but now they are being made on demand.
Even if each of the above new products takes an year or two in the making, VF stands to benefit and hopes to double its current turnover in the next 3-4 years.
Being an ASME (American Society of Mechanical Engineering) compliant company, VF received its U, R and NB stamps in 2013 that enable it to produce vessels of 200 bar pressure capacity also. Mr. Panchal explains: “We are trained in production and maintenance of our technical documentation. Post training, the team leader from ASME comes to the shop and checks out the premises and performance on the demo vessel. Once you obtain a U stamp company, we have to follow all their quality controls for the raw material, pressure calculation and the like. This has given us confidence in designing our bulkers from 3 mm thickness even.”
The Vision
With 45 other manufacturers in the field, a downside is that the market is replete with supply overriding demand. Mr. Panchal is not worried though: “At this moment, the bulker market is going in excess. I feel the requirement will be steady for the next 4-5 years precisely because of this. And if Government rules change to mitigate the overload factor or if RTO gets stricter on the size of the bulker there will be a big boom in the bulker market. Already a few States have started working on the rated load, so we have orders for them in high tensile steel because it helps to reduce the bulker weight.”
While that may be a matter of pride, business requires either fresh or repeat orders for it to thrive. Mr. Panchal says: “Those that are old or have met with an accident, and hence cannot be repaired, need to be replaced. Then new cement companies have come too, so those who want bigger bulkers to replace their smaller ones are coming to us too.”
From being regular fabricators to making specialized bodies, Vasant Fabricators has become a name to be reckoned with in the industry.