Though incorporated in 1983 in California, Velodyne became the most sought-after brand name for its LiDAR technology systems a few years later, in 2005. These real-time sensors were founded by David Hall who was a contender at the first driverless car race challenge organized in 2004 by the Defense Advanced Research Projects Agency (DARPA). It so happened that the following year the organizers wanted Mr. Hall to develop these sensors for other participants because for the first time these sensors offered three-dimensional information that enabled autonomous driving.
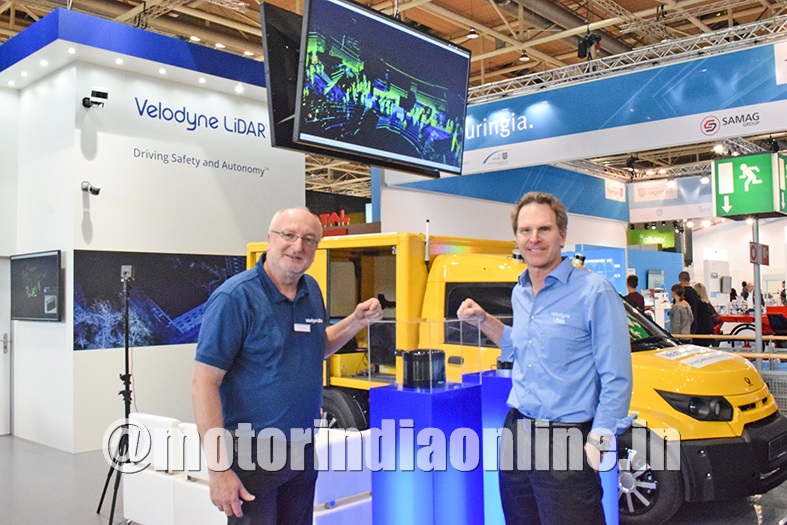
Velodyne LIDAR
To understand the definition of LiDAR and what the sensors do, a brief official explanation says – ‘Light Detection and Ranging or LiDAR is a surveying method that measures distance to a target by illuminating it with pulsed laser light and measuring the reflected pulses with a sensor. Differences in laser return times and wavelengths or intensities can then be used to make digital three-dimensional representations of the target’.
Mr. Hall developed the HDL-64 solid-state hybrid LiDAR sensor, and with it Velodyne established itself as a pioneering company in self-driving that develops, manufactures and supplies real-time LiDAR sensors. Over the years, the company’s foray into laser distance measurement made history.
Mr. Erich Smidt, Executive Director – Europe, says: “The company’s latest generation of sensors are used in autonomous vehicles, vehicle safety systems, 3D mobile mapping, 3D terrain measurement and security systems. And we develop our own R&D processes.”
Mr. Dieter Gabriel, Marketing Manager – EMEA, adds: “Velodyne has huge expertise in analysing and transferring data generated by the sensors to be used by the customers, and that is the basic foundation of our company in the LiDAR business.”
LiDARs are used for perception, landscaping and localization to let the vehicle know where it is so that it can intuitively gauge the free space around it, be safe, avoid obstacles and send warning signals or even stop itself in time.
Mr. Smidt shares: “The data thus generated is utilized by our customers who can then put it into their algorithms to provide actions, stop the vehicle or turn it or do anything else that they need to do. And, since we realized there are other applications for LiDAR, we have started downsizing it so that we can make it less expensive but maintain its higher resolution. That is why we have created the Puck family of sensors which are smaller LiDARs that can also be used for a huge variety of autonomous applications.”
The latest solution to be offered is the all-new VLS-128 which delivers real-time three-dimensional data up to a vertical and horizontal resolution of 0.1 degrees and a range of up to 300 meters at 360°.
Mr. Smidt adds: “The VLS-128 is the culmination of 10 years of LiDAR development and experience of ours coming from driving millions of road kilometres with LiDAR sensors. The sensor is built for advanced safety demands such as for autonomously controlled trucks driving at high speeds. VLS-128 offers a much clearer image than all its predecessors owing to the 128 laser channels. As a smart city application, this basically allows mapping for security at small intersections where the customer can monitor what is happening at the intersection and provide data from the infrastructure to the vehicles. Or, if it is a government agency using it, then they can glean information such as how much traffic flow is happening or look at the safety zones with regard to people.”
Mr. Gabriel observes: “Our sensors have to be reliable in use for highly congested streets and lanes in the middle of the city because for safe autonomous driving vehicles must always have excellent vision.”
Agrees Mr. Smidt and says: “The vehicles need a three-dimensional view that measures and eventually generates one billion data points in real time at the speed of light. This technology enables them to assess the speed of other vehicles, determine pedestrian locations and also assess safety relevant situations.” Another great example: a novel ‘follow me’ function may allow the driver of the vehicle, for example of an e-commerce company, to walk down to the destination to deliver packages and the vehicle follows him.
Currently, VLS-128 is being utilized by their customers for conducting tests on long haul trucks in Europe and the US and the officials foresee its suitability for India as well.
Now, Velodyne is going one step ahead with the Velarray sensor which no longer requires any moving laser components and can be used in highly reliable driver assistance systems.
Mr. Smidt expands on its unique features: “The Velarray detects areas with a horizontal angle of 120 degrees, a vertical angle of 35 and a range of 200 meters. It also detects objects with particularly low reflections – for example, even at 10 per cent reflectivity – it means we can see dark objects. And this is the first time when the compact three-dimensional laser sensors combine autonomous driving with modern automobile design.”
Mr. Gabriel shares: “Velarray sensors are basically for hidden applications which the automotive manufacturers embed them in the vehicle, say, behind the grill, the glass or the truck window.”
Velodyne’s LiDAR sensors are used by most industries, including those into navigation who use LiDAR data to create high definition maps. Mr. Gabriel adds: “Drones for mapping use LiDAR because they can get highly accurate information when they create a three-dimensional model. And robotic companies use LiDAR for two purposes – one to guide it around an area and secondly, to monitor what is around it. And there are others who use LiDAR for autonomous loading and unloading of cargo at warehouses.”
With multiple manufacturing sites, including its huge San Jose mega-factory, Velodyne is preparing for the increasing industry demand through advanced and streamlined manufacturing techniques for its full range of lidar sensors.
Mr. Smidt says: “Our sensors have long range, high resolution, are highly robust for the vehicle – whether it is a passenger vehicle or a commercial vehicle. And we make them consume less power because that is a crucial feature with the e-vehicles nowadays.”
Velodyne is now working on coming up with a million units a year by means of automated manufacturing and is aiming to reach the series production level for autonomous driving at the earliest. Its sustainable technology is enabling Velodyne LiDAR to help its customers develop their autonomous vehicle prototypes faster.
The future of autonomous driving with Velodyne LiDAR sure is electrifying.