“Individual commitment to a group effort – that is what makes a team work, a company work, a society work, a civilisation work,” said Vince Lombardi, an American football player, coach and executive. He is best known as the head coach of the Green Bay Packers during the 1960s, where he led the team to three straight and five total National Football League (NFL) championships in seven years, in addition to winning the first two Super Bowls following the 1966 and 1967 NFL seasons.
Team MOTORINDIA discovered a similar zeal for team work, commitment to excellence, group effort and a dedicated civilisation helping a company flourish when it visited Gothenburg (known as the city of Volvo), Sweden. The Volvo Group (usually shortened to AB Volvo) is a Swedish multinational headquartered in Gothenburg whose core activity is production, distribution and sale of trucks, buses and construction equipment. It also supplies marine and industrial drive systems and financial services.
The Volvo Group, which employs about 100,000 people, has production facilities in 18 countries and sales of products in more than 190 markets. Quite an achievement for a company that was originally established in 1915, as a subsidiary of SKF, the ball bearing manufacturer. However, the Volvo Group and Volvo Cars consider themselves to have been officially founded in 1927 when the first car, the Volvo ÖV 4 series, affectionately known as ‘Jakob’, rolled out of the factory in Hisingen, Gothenburg, as a vehicle that could withstand the rigors of the country’s rough roads and cold temperatures. Assar Gabrielsson, an SKF sales manager, and engineer Gustav Larson, the two founders, are credited to have manufactured the sturdy ‘Jakob’ vehicle.
Cut to FY 2015-16 the group has sold a total of 2,07,475 units of trucks across Europe, North and South America, Asia and other markets. “Today, the majority of the Volvo Group’s customers are companies within the transportation or infrastructure industries. The reliability and productivity of the products are important and in many cases crucial to our customers’ success and profitability,” informed Rene Muller, Segment Manager, Construction Dept. Product Offer, Volvo Trucks, as he took us through the Volvo Group operations and the company’s history (read the accompanying box).
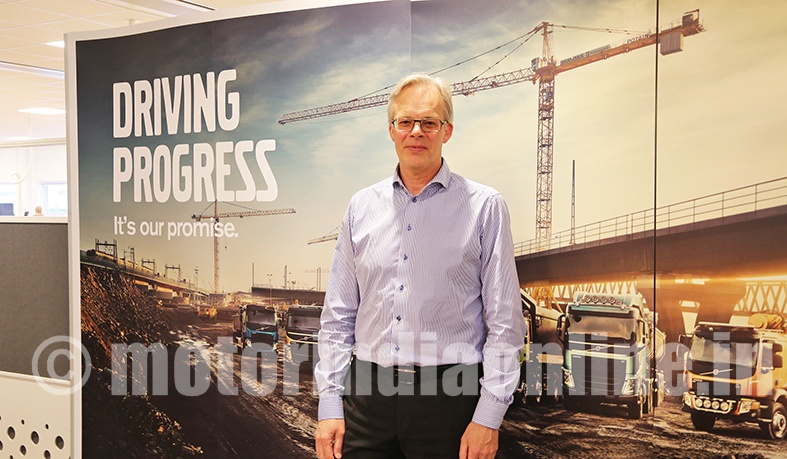
Sturdy, safe and reliable
Post the introductory presentations about the history, current operations of the company, we were introduced to key concepts that Volvo Trucks have developed in the recent years to enhance the safety of drivers. The important of them were the Volvo Dynamic Steering (VDS), Automatic Traction Control (ATC) and I-Shift with crawler gears. Before we get into the details of these applications in the following paragraphs, there is an important part (invention) of Volvo in all the vehicles that finds an honorary mention. It is the three-point seat belt invented in 1959. “This ingenious solution has saved more lives on the road than any other safety feature. Six out of ten truck drivers who are injured or killed in traffic would have suffered less severe injuries or no injuries if they had used a seat belt,” beamed Carl Johan Almqvist, Traffic and Product Safety Director, Volvo Trucks Global Brand.
“India is a very important and a strategic market for us at Volvo Trucks. Indian mining experience is a key input for many of the product innovations in the mining segment. At Volvo Trucks any new feature or innovation revolves around the customer. We believe in innovation with a purpose. Volvo Trucks enjoys a leadership position globally and with these new features added in the FMX for construction and mining will take it to the next level on performance and productivity,” said Mr. Ricard Fritz, Senior Vice President – Product and Vehicle Sales, Volvo Trucks HQ, Gothenburg, Sweden.
Volvo Dynamic Steering
“Volvo Trucks’ Volvo Dynamic Steering (VDS) improves the vehicle manoeuvrability as the whole system makes the driving experience more comfortable. VDS works through a precisely controlled electric motor which is mounted on the hydraulic steering gear. The motor is controlled 2000 times per second based on the inputs of the driver and on-board sensors. Its purpose is to provide precise steering control in every situation,” explained Goran Bojovic, Product Manager, Volvo Trucks Global Brand.

For all-wheel drive trucks like the 8X8, 4X4 and 6X6 that operate in tough conditions, Volvo has introduced Automatic Traction Control (ATC). It means the driven first axle is only used when needed which improves both fuel efficiency and driveablility. “It is a well-proven feature in the Volvo Construction Equipment, but Volvo is the first truck company to introduce this feature in a construction truck. ATC engages and disengages the front wheel drive automatically at the right time when driving on slippery road conditions. The system is very fast and it takes just half a second for the system to engage the dog clutch. This secures mobility and traction at all times,” disclosed Bojovic.
Today most drivers activate the front wheel drive before the terrain becomes difficult in order to avoid standstill. With ATC the driver benefits from better maneuverability right uptill the road condition gets worse. “When the sensors at one of the rear wheels detects that it is starting to lose traction, the all-wheel drive is instantly engaged. A dog clutch then transfers the power to the driven front axle and the truck continuous to run without dropping either torque or speed. The driven truck axle then remains activated until the driver releases the gas pedal,” beamed Bojovic.
Volvo I-Shift crawler gears
Another important feature that Volvo trucks have introduced is the I-Shift with crawler gears – a gear box with two additional crawler gears. The extra gears make it possible for the truck to be started from standstill. By adding two additional cock wheels the truck can be driven at a really slow speed, which is key for precision driving. “The crawler gears make it possible to drive as low as 0.5 km per hour. This gear thus helps a heavily loaded truck to climb uphill. It also enables reversing at really slow speed helping drivers who need to reverse with caution,” explained Bojovic.
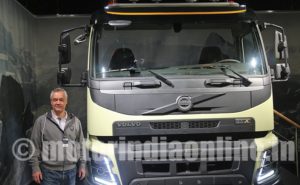
Experiencing Engineering Marvel
Post the presentations, it was time to experience the new technology in the Volvo FH and Volvo FMX off-road vehicles. We got behind the wheels and could understand, while discussing with the instructor, that VDS has four main benefits. First, it takes away the physical load of steering while even at low speeds. The driver controls the steering with very little effort regardless of how heavy the load is. Second, it improves directional stability at high speeds so that no small steering adjustments are needed. Third, it diminishes effects of road disturbances such as bumps and potholes. Fourth, we felt that it detects and balances out directional deviations like side winds too. In addition to this, the steering wheel returns to its original position perfectly even after reversing.
Even the I-Shift crawler gears in the FMX gave a feeling of driving two trucks in one. We could driver at low speed whenever needed and also optimize driveline on top speed. We were told that the gearbox achieves the same low fuel consumption as the regular i-shift. We also noticed bigger window and new rear view mirrors in two parts that help minimize blind spots.
Intelligent automation
After the driving experience, we got a glimpse of how the vehicles are made. While we sat in a super-comfortable Volvo-Road-Train that took us through the chassis plant at Tuve, we realised everything starts with a roll of steel sheet. The main chassis beams are made out of these sheets of steel by a series of pressing, bending and cutting processes. It is at this stage that the chassis beams are manufactured as per the customer’s orders, in terms of serial numbers, holes made, length, place to cut out, etc. Robotic machines carry these beams to the assembly area. They move and work with smooth precision throughout the duration of operation. Behind all the precision is an advanced computer programme that tells the robot what it has to do and exactly when. Be it welding, painting, cutting, pressing or assembling, each movement is carried out by these sophisticated robots that are otherwise difficult to achieve using conventional manual methods.
Here on, in the assembly area, each parameter of the chassis was carefully timed so that it remains efficient and doesn’t cause problem future down. The staff coordinates and keeps an eye on the television screen that depicts the countdown time left for that particular assembly.
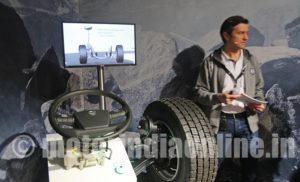
The operators work on the chassis putting nuts and bolts, wiring and harnesses and other electronic aggregates putting the chassis upside down, since it is easy to do it this way for operators. Operators ensure that everything is properly assembled as per the parameters given since all the electricals communicate to each other regarding speed, braking, steering wheels position, etc. In a nutshell, it takes approximately 4-5 days and a host of nuts, bolts and screws to transform sheet of steel and high-tech electrical into the state-of-the-art trucks. The factory also produces truck assembly kits that are shipped in another plant for assembly. After the nuts, bolts and electricals are fitted the chassis is tilted 180 degrees (from the previous upside down position) to be fitted with axles, suspensions and drive train.
Precision for Purpose
Next day we took a train from Gothenburg to Skovde for visiting the Volvo Group Truck Operations site covering 2,65,000 sq.ms. where heavy duty diesel engines are produced. Here the truck engines are cast, machined and assembled. The site houses two foundries, the G1 and the G2. The mercury shows 25 degrees in the foundry and around 1500 degress in the melting furnace. We saw the proceedings from a safe cordoned area. The G2 is the state-of-the-art foundry as the casting process has been refined and its environmental impact has been reduced. Water is used to cool down the casting moulds, which speeds up the solidification process and makes the iron stronger. The water is then recycled, and about 50 per cent of the energy generated from the casting is reused for heating. Almost 85 per cent of even the sand from the mould is recycled, which means the G2 facility has a very high recovery rate by international standard.
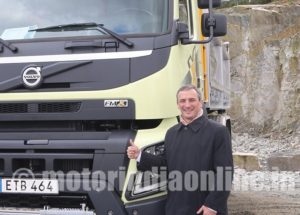
Before the casting process the mould has to be assembled. The co-packaged for cylinder heads is glued together by robots that perform the job in millimeter precision. It is then coated with a refractory fluid called the black wash which makes the surface flawless. The co-packaged is then put together, making the mould complete for the final process called casting.
We also came to know that all the parts that lead to the casting are first machined. The machinery process is highly automated and consists of a lot of steps, and it is under constant scrutiny by advanced machines that measure accuracy by 1000s of millimeters. The plant machines cylinder heads, engine blocks, cranks and camshafts plus flywheels and gears. The camshaft is assembled on the cylinder heads. “The plant assembles 13 liters and 16 liters engines, and in fact Volvo is the largest producer of above 9 liters engines in the world,” informed G.V. Rao, V.P. – Product Strategy, Brand and Marketing, Volvo Group Truck Sales, Volvo India Pvt. Ltd., who accompanied us throughout the two-day visit with his Indian colleague Yogesh Diwakar.
All engines manufactured adhere to strict environmental norms. To be able to compliant with Euro-6 emission norms, the engine has a selective catalytic reduction (SCR), exhaust gas recirculation (EGR) and diesel particulate filter (DPF) that produces nitrogen oxide by 77 per cent and particulate emission by 50 per cent compared with Euro V. After assembly, in a closed area, the engines are brought to life for the first time. The test lasts about two minutes. It is run without liquid in its cooling system, and during the two minutes important parameters are measured, monitored and saved. For instance, turbo pressure, sound and rpm are monitored thoroughly. When the engine passes all the parameters, it is moved to the paint shop which is the last step in the manufacturing process. The freshly painted engines are then ready to be fitted in the trucks.
Volvo Museum
After experiencing the technicalities of engine manufacturing and assembly, we were taken to the Volvo Museum. Located in the Arendal area on the island Hisingen at the sea, about 10 km west of Gothenburg city centre, the museum showcases development of the Volvo Group from its first car, other vintage models to the FH, FMX, Globetrotter and the first bus. It also contains the founder, Gabrielsson’s and Larson’s joint desk from the initial years. There are also displays of Volvo Aero and Volvo Penta products.
It was heartening to see how efforts of a focused generation could build world-class products. In the two days we could feel the commitment for excellence, precision for robust purpose and the hunger to strive hard for premium and reliable quality that Volvo and its customers worldwide vouch for. We bring you some exclusive pictures from the museum in a bid to make you part of the rich heritage.
Committed to excellence
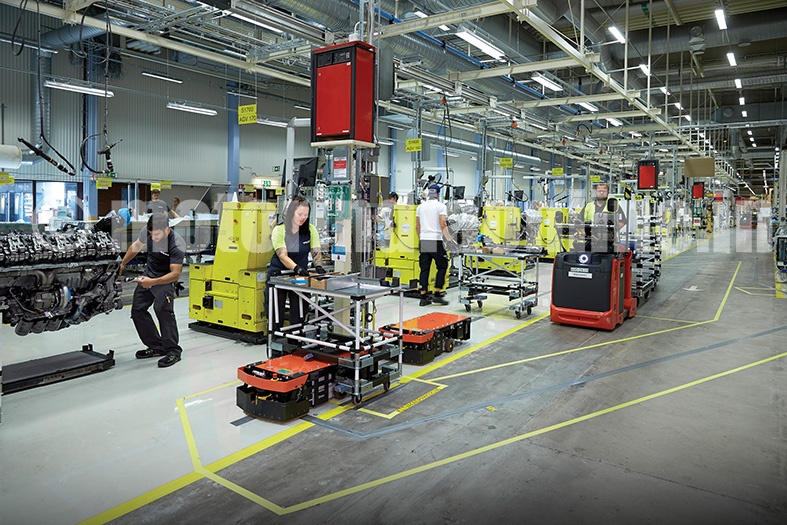
Today, Volvo Group operation includes Mack Trucks (light-duty trucks for close distribution and heavy-duty trucks for long-distance transportation, Founded in 1900, Mack Trucks is recognised around the world as (“The American Truck You Can Count On”) Renault Trucks (Heavy-duty trucks for regional transportations and heavy-duty trucks for the construction work segment Headquartered in France Renault Trucks supplies transport professionals with robust tools and robust relationships since 1894) Value Truck & JV’s (Designed to meet the specific needs of the Group’s truck customers in the value truck segment, with responsibility for the Value Truck business) UD Trucks (Established in Japan in 1935 UD Trucks markets heavy, medium and light duty trucks in Japan as well as in growth markets in Asia and around the world.) Volvo Buses (Involves production of city and intercity buses, coaches and chassis under the brands Volvo, UD, Sunwin, Prevost and Nova bus.) Volvo Construction Equipment (Manufactures a number of different types of equipment for construction applications and related industries under the brands Volvo, Terex Trucks and SDLG.) Volvo Financial Services (Delivers competitive financial solutions which strengthen long-term relationships with Volvo Group dealers and customers.) Governmental Sales (Selling trucks and buses to government agencies and organizations) Volvo Penta (Marine engine systems for leisure boats and commercial shipping, diesel engines and drive systems for industrial applications) Volvo Trucks (midsize-duty trucks for regional transportation and heavy-duty trucks for long distance transportation, as well as heavy-duty trucks for the construction work segment. Volvo Trucks is the second-largest heavy-duty truck brand in the world; with trucks sold and serviced in more than 140 countries.) Group Trucks Operations (Manufacturing of cabs and trucks for the Volvo, Renault Trucks, Mack and UD Trucks brands as well as production of the Group’s engines and transmissions. Spare part supply to the Group’s customers and logistics operations along with purchasing responsibility for Volvo Group.
It also has partnerships with Dongfeng Commercial Vehicles (DFCV) in China, together with Dongfeng Motor Group Company Ltd. Shandong Lingong Construction Machinery Co. Ltd. (SDLG) in China. Shanghai Sunwin Bus Corporation in Shanghai, together with Shanghai Automotive Industry Corporation (SAIC). Volvo Eicher Commercial Vehicles (VECV) a 50:50 JV with Eicher Motors Ltd. in India.
“We had an all-time-high vehicle sale in India in 2015”
Exclusive interview with Mr. G.V. Rao, Vice President – Product Strategy, Brand & Marketing, Volvo Group Truck Sales, Region India.
We have experienced VDS, I-Shift Crawler gears and Automatic Traction Control (ATC). These are futuristic technology and are pretty sophisticated. How do you think will these technologies fare in the deep mining trucks that Volvo has in India?
Volvo Trucks has always been in the forefront to bring in newer technologies to improve the vehicle as well the driver productivity for our customers. We have a leadership position in the mining and construction segment and some of the technologies like the VDS, I-Shift Crawler gears and ATC are such that they can take the vehicle productivity to the next level.
Coming to the features, in ATC the front wheel drive will automatically engage while the vehicle is negotiating a particular weight and gradient and also when the underfoot conditions are slippery. All this happens without driver intervention. This will consume less fuel and improve the vehicle performance. With fuel saving of upto two per cent it also improves the manoeuvrability at low speeds.
When it comes to Volvo Dynamic Steering (VDS) it is now available on dual front axles. Of course, it means effortless steering while improving the safety and productivity of the vehicle to a large extent.
I-shift we are already in leading position in automatic gear box and now it comes with crawler gears which improve the startability. In fact, in the heavy haulage vehicle we will also have ultra-low crawlers, in which the ratios can even go 32:1. Conventionally you have the first gear and the crawler ratios in the range of 14 to 16 while this goes up to 32. Thus, double the performance in vehicle start ability. We are open to exploring all these feature in our heavy haulage and mining segment.
We also saw the 13 litre and 16 litre engine assembly line. What are the synergies between the Bangalore and the Skovde plant in terms of the 13 litre engines used in India?
Yes, the 13 litre sophisticated engines that we use in our heavy duty trucks is manufactured in Skovde plant, one of the most advanced plants in the world. The same engines are used at our emission levels of BS-III in India. These engines are coming from the plant and they are assembled in India.
How was the performance in terms of units sold in India, in the last fiscal especially post the 10,000th vehicle that was produced in India?
We had an excellent 2015 in terms of vehicle performance. We had an all-time-high with sales of 1,222 vehicles, and the first quarter this year has also been extremely positive for us and we are expecting a growth over last year. We are optimistic because of positive initiatives taken by the current government both on the infrastructure and mining side.
By R.Natarajan, Managing Editor & Publisher and Rajesh Rajgor