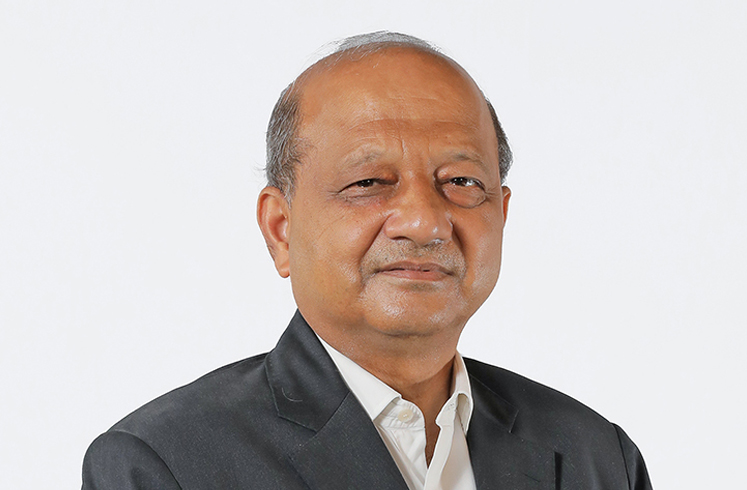
The Automobile Skill Development Council (ASDC) has been engaged in spearheading the process of providing training modules for those working in the automotive industry. In this interview with Rajesh Rajgor, ASDC President Vinod Aggarwal elaborates about how factors like 5S, safety, the environment, quality, teamwork, discipline, communications, IT and many more are covered in their courses and also how the association is upgrading itself to cater to the changing needs of the industry
The Automobile Skill Development Council (ASDC) was established with the goal of improving the abilities of those who work in the automotive industry. The improvement of occupational standards for workers in research and development, manufacturing, sales, service and driving is being promoted by the organisation. The Society of Indian Automobile Manufacturers (SIAM), Automotive Component Manufacturers Association (ACMA), Federation of Automobile Dealers Association (FADA) and Government of India represented by the Department of Heavy Industry and National Skill Development Corporation (NSDC) support and promote ASDC. Excerpts from the interview:
The automotive industry underwent a transition from BS IV to BS VI in 2020. How have the service and maintenance technicians, dealers and OEMs coped with the change and are there any courses that ASDC offers for them?
We have courses for everyone and specifically for new technologies like BS VI. The portfolio is wide and the courses are designed for companies, shop floor technicians, workshop labourers, drivers, etc. We offer courses in artificial intelligence (AI) and digitalisation and areas like Industry 4.0. There are also courses for upskilling on various fundamental technologies like machining technology, welding technology, etc. Much before the transition happened from BS IV to BS VI we encouraged technicians, dealers and OEMs to train the technicians so that they would be ready on the day of implementation of the new emission norms. We are working with various companies like Hero, Royal Enfield, VECV, Toyota, MG Motor, Maruti Suzuki and others to train technicians, workshop managers and shop floor mechanics.
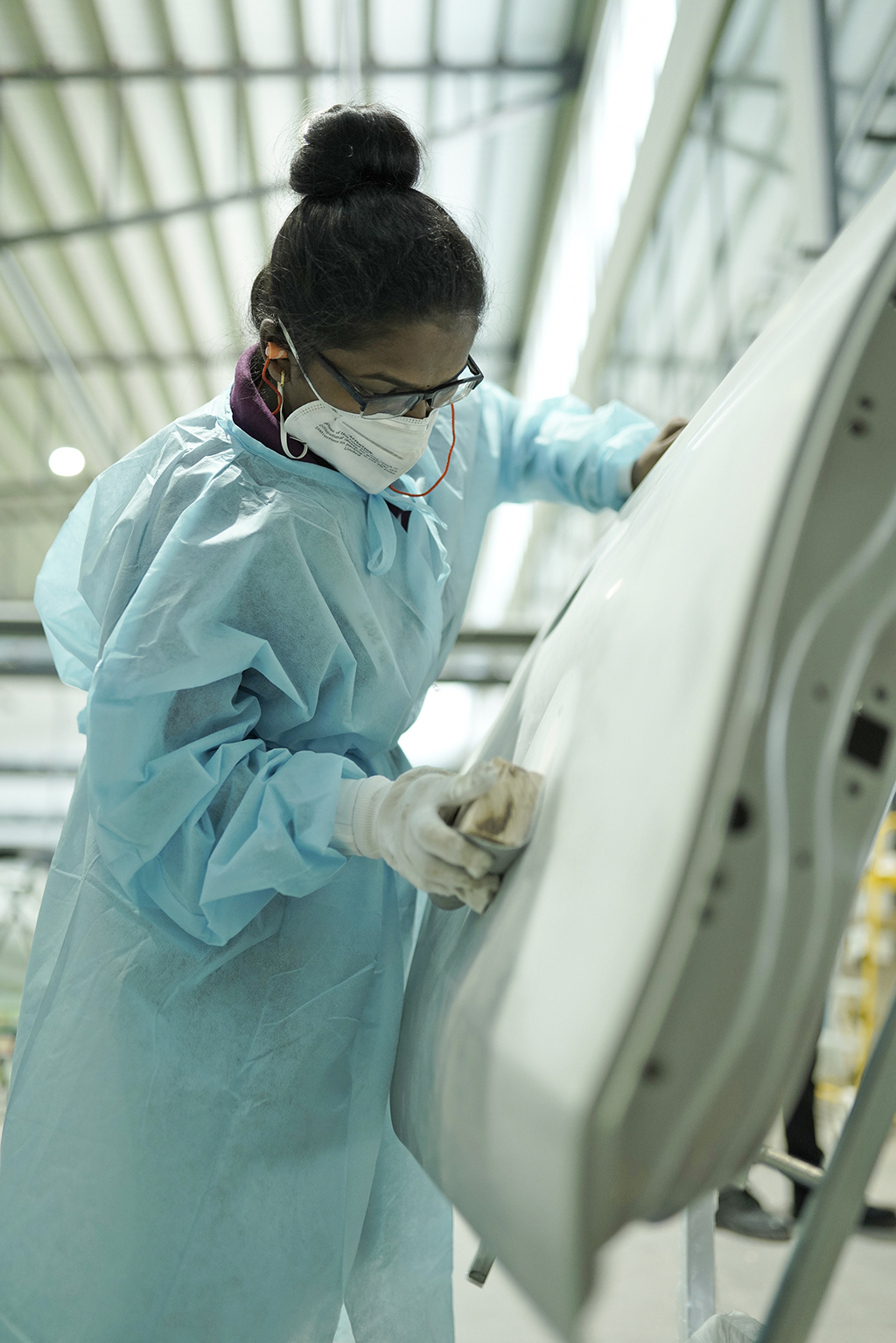
How are you creating these courses? Could you share a few examples?
There is so much upgradation which has happened on the shop floors because of Industry 4.0 and everything can be traced back. For example, if there is a defect in the vehicle you can absolutely trace it back to find its root cause. Many companies are adapting to Industry 4.0 and the Manufacturing Execution System (MES) that is getting implemented in most of the organisations. A majority of the organisations are implementing Enterprise Resource Planning (ERP). All these requirements will need retraining of the workforce.
Of course, organisations are themselves responsible for upskilling their employees but ASDC facilitates the training process so that it can take place with speed. We also help them in getting the right material, right course content and training programmes. We also certify their apprentices, thus guaranteeing their fitness for employment. Based on that certification, the industry can just pick up those people and put them on the job. They are ready for employment immediately. We have 114 approved curriculums and qualifications on the national qualification register website based on industry requirements.
How big is ASDC how do you plan and manage your workforce to design these courses?
We have 20+ employees and our corporate office is in New Delhi. We also have a few full time in-house subject matter experts and based on project requirements they engage with external freelancers or take help from industry resources. There are people working on content development and then there are those working on specific projects. We have a very competent team that is running the show. While we do all this, we have to be self-sufficient. Hence, we are trying to become self-sufficient even though we are not a profit-making body. Hence, tie-ups with companies and state governments as well as industry bodies are important.
Since you have been working with different organisations in the automotive industry, what is your observation about the most pressing skill gaps?
With BS VI there is a lot of electronics in any vehicle and when there is a significant change in technology, the implication is that everyone down the line has to learn these new technologies. Otherwise, technicians working with dealers will not be able to carry out repair and service tasks. Unless we are able to train everyone associated with the automotive industry, customers will not get the right service. The crucial fact is that this training is mandatory since there is now a complete change in the fundamentals of automotive engineering.
For example, if you are going from ICE engines to electric vehicles, the technology is totally different. The engine is replaced with an electric motor and batteries along with sophisticated software like the battery management system. These are new things for most people. Hence, we have to prepare a specific curriculum and collaborate with experts to take care of this change. It also implies that we have to work with a lot of agencies, including state and central government bodies.
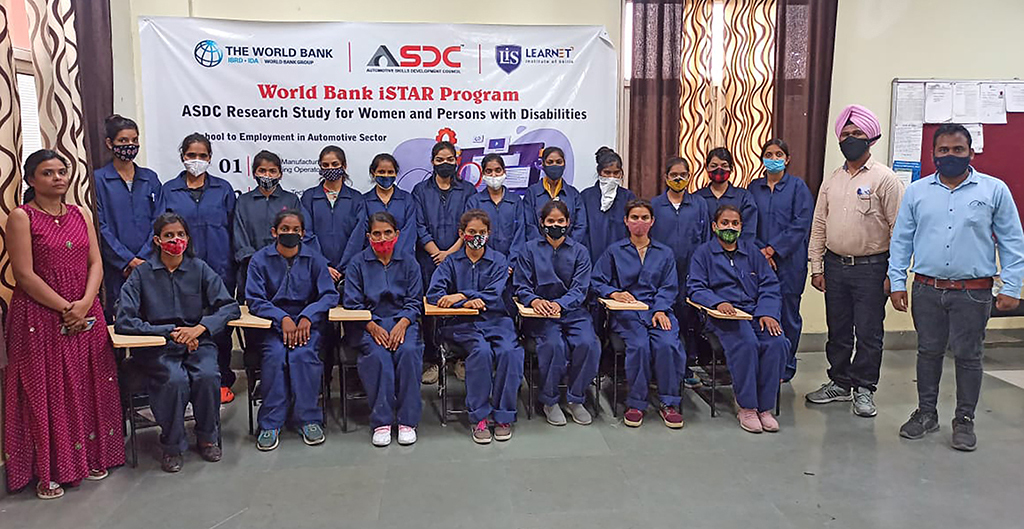
Could you please list down the opportunities and challenges that the Indian automotive OEMs are facing currently? How should they prepare for them?
There are opportunities in the areas of cutting down the greenhouse gases and if we have to move towards cleaner and greener technologies then we have to move towards alternate fuels. This may be in the form of electric vehicles, fuel cells and so on. It implies learning new technologies. We are an active participant providing the right training and courses suitable for this change in the automotive industry. As far as challenges are concerned, any kind of change management has to be handled very carefully. We have to understand all the nuances, pitfalls and prepare the right material which will help in creating the right competencies in the industry. ASDC therefore engages the right skill-sets who help us with the curriculum. We are in pursuit of creating synergy with companies to identify common programmes.
How has your experience been with the world skill competition? What are the key lessons that ASDC has derived from such competitions?
It’s a very big motivating factor for the concerned people when you participate in any competition. It helps upgrade one’s skills because then you are competing with the best and this is especially true when you go on to the world stage. We become aware of what is happening in the field of any technology and this helps us prepare for the change as sooner or later all such technologies will get implemented in India.