Windal Precision Pvt. Ltd., a prominent manufacturer of two-wheel drive axle assemblies, rear axle housings for HCV / LCV popularly called banjo housings, tag axle, grader axle assemblies and various components for the farm equipment, commercial vehicle, construction and material handling industry is showing considerable growth across all its verticals.
Over the past few years it has successfully acquired business with leading OEMs and Tier-1 suppliers in India. The company that already has achieved recognition as a leading manufacturer of two-wheel drive axle assembly in India, by catering to customers like M&M, John Deere, Eicher Tractors, Escorts, CNH, among others is making deep inroads with its growing finesse in the field of banjo axle housings, tag axle assembly and its newest vertical of lift axle assembly.
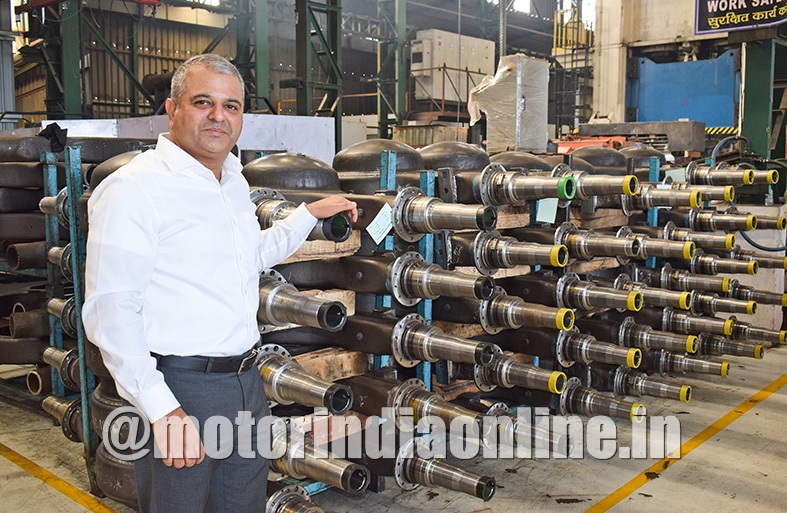
In an exclusive interview with MOTORINDIA, Mr. Vaibhav Vinzanekar, Director, Windal Precision, said: “We have been in the axle assembly business since 1997. Over the years we have grown from being a single product, single customer company to a multiple product and multiple customer company with specialized manufacturing capabilities in axle parts and assemblies. We were looking at diversification and the opportunity in 2014 in the axle space owing to the backward integrated plant we have, we were able to offer that as a competitive advantage to our customers. The existing capacity crunch in the Banjo housings also worked in our favour and we were able to establish a fully integrated banjo housing plant in a short span of two years. We have been able to manage this, with relentless focus on process improvements which leads to quality improvements along with support from our esteemed customers like Dana India, American Axle, Axle Tech, M&M and Ashok Leyland.”
In the field since 2015, the banjo housing line is, according to Mr. Udaykumar Vinzanekar, Managing Director, Windal Precision, “the first and only fully integrated line in India with forging, hot forming, friction welding and all machining under one roof.”
Mr. Vaibhav Vinzanekar seconded him and observed: “We had started the project implementation in January 2014 and, after various processes, the first batch was delivered by May 2015 under the able leadership of Mr. Vijay Kumar Ananthpur, General Manager – Projects & Developments. The team ensured tight project management despite the set-up being under process. We successfully manufactured first time right for all variants that were tested in the lab in the US and for 5 lakh km on road. Since 2015 we now have over 18 variants and models’ live-in production.”
The road ahead
Windal Precision has a dedicated banjo housing manufacturing facility in Pune and Rudrapur and also has plants at Nagpur and Bhopal. Rudrapur and Pune are also for two-wheel drive axles. “The Pune plant remains the central engineering kitchen for all plants. Majority of the banjo housing manufacturing happens at the Pune facility and only last few processes of child part assembly and painting happens from our Rudrapur plant. From Pune we supply to Chennai and Rudrapur where as Rudrapur plant is specifically for the requirements of our customer located there. Our current capacity is approximately 6,500 units per month which we are looking at scaling up to 10,000 housings a month from 2020,” asserted Mr. Vinzanekar.
Apart from the bulking up of capacities, what the company could achieve during the process was becoming proficient in organizing deliverables. “These learning happened quite naturally while dealing with key MNCs that are Tier-1 suppliers to most of the OEMs in India. The entire setting-up of new lines was a huge project management lesson as well as reinforced our focus and commitment towards systems, automation and improvements of the existing technologies. For instance, the setting up of hot forming on a 2,500 tonnes press with an induction heating equipment and friction welding which is a 100 tonnes along with large CNCs and VMCs, our operating force has become highly formidable which has remained our core strength,” he added. The company is looking at getting more talent for the journey ahead and is also investing extensively for learning and development. Continuous improvement and agility towards change is a mantra in the organization that every member of the Windal Precision family has embraced.
Clearly, the association with OEMs and Tier-1s has ramped up Windal’s growth road map both on the product front and the impact on the company’s overall culture. In just three years the company has added four clients in the form of leading axle manufacturers as well as added 18 variants. In line with its growing product portfolio, the company is also looking at manufacturing dead lift-axles and trailer axles. This development will be keeping in mind the WIN2020 – Windal vision that aims at diversification and collaborative growth.
Asked where the focus lies given the huge multi-product component portfolio, Mr. Vinzanekar explained: “Our vision WIN2020 has given us the direction of change, helping us set a target of being a Rs. 1,000 crore-listed company by 2020. This simply means that we not only grow organically on our old expertise of two-wheel drive tractor axles, but also add variants in banjo axle housing, lift & tag axles and other components along with in-organic growth that we are working towards. While this is merely a start, over the past 3-4 years we have become even more focused, efficient to run the business professionally. We have very good products, the best of customers and a very experienced and technically good team on board. We are ahead of our roadmap and have surpassed our yearly targets within nine months. We are confident of achieving the vision and road map we set for ourselves in 2012.”
Closer to the target
In 2012, when the company decided to give a realistic number to its WIN2020 road map target of being a Rs. 1,000-crore listed company by 2020, it was an approximately Rs. 100-crore company. Mr. Vinzanekar elaborated: “In April last year, we had an order book of Rs. 127 crores worth from the banjo housings business and close to Rs. 300 crores from tractor axles. Add other component business to it we had an orderbook of Rs. 558 crore-order estimates in 2018 itself when we are talking about Rs. 600 crores by 2020. Even if there is a dip in off-take around the BS-VI transition phase, we should close at least Rs. 450 crores by March 2019. We believe that due to the efficient project management our projection scenario has become a lot sharper. De-risking our business has also ensured that we are able to manage the industry lows a lot better.”
The company’s optimistic projection is on the back of two important factors – things, market dynamics and the investment made in state-of-the-art facilities. “As per the BDB research report conducted in 2016, out of the overall tractor front axle market 46 per cent was yet held by captive. Of the 54 per cent outsourced we held majority market capitalization, three times to our closest competitor, with 26 per cent market share which was 38 per cent the previous year. The same has grown to 47.73 per cent as on November 2018. In axle housings, although a late entrant, we could easily supply around 60,000 housings annually and can more than easily fill the ever-existing supply gap in the segment,” revealed Mr. Vinzanekar.
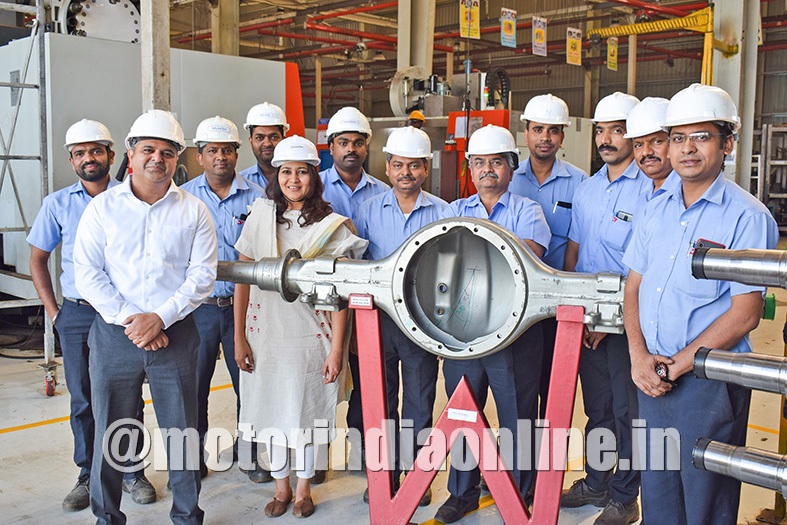
On the finer details of the operational front that makes the company get closer to the target are the Banjo Axle housing for HCVs, LCVs and ICVs that the company has entered into with two key global players. The firm is also exploring possible opportunity of supplying to the aftermarket for tag axles in India. It is in talks with a leading OEM and two leading Tier-1 MNCs globally and are looking at adding it to its business portfolio at the start of the next financial year. Also, as part of the WIN2020 is the company’s vision to build in-house design capabilities.
“We took our first step towards designing with an in-house tag axle for leading Indian OEM. We would in the future look at strengthening the same through a technical partnership. Our vision is also to do backward integration with respect to casting, currently as things are, we would focus on sheet metal and forging and stabilize in terms of the existing business. There are huge opportunities also in spindles and axle shafts, and we are already in talks with a few key players for technical partnership”, concluded the Director.
The journey from manufacturing a single part to a single customer, from a single location to becoming a complete solutions provider with multi-capability plants catering to multiple customers and becoming the first and only fully integrated line worldwide with forging, hot forming, friction welding and all machining under one roof, Windal Precision has come a long way from the time the company was founded by Mr. Udaykumar Vinzanekar to consolidating its presence in the axle eco-system.