Plant to support global sourcing operations
By Ritij Khurana
Commemorating its 100 years of existence, ZF Friedrichshafen AG, popularly known as ZF, has launched a new facility at Chakan near Pune with the aim of showcasing the company’s commitment towards India and to be a catalyst of growth in future. By setting up of the new plant, the company is aiming to expand its product portfolio and make India a global hub for sourcing in future.
“The new plant is an important investment in the centennial year of the ZF Group. It reinforces ZF’s role as a global player and its commitment to expanding in a growth region like India,” said Wilhelm Rehm, Board Member of ZF Friedrichshafen AG and Global Head of material management, at the launch of the facility.
The plant opening ceremony witnessed the presence of all ZF business partners, customers, overseas industry leaders and major internal stakeholders. The company wants to provide local production for local manufacturers wherever it has its presence, and its Chakan facility which it likes to call the ZF Business Park further confirms this claim in the Indian context.
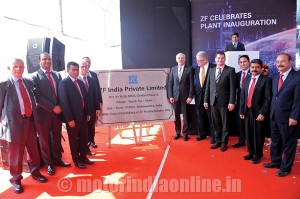
India is ZF’s second-most important market in Asia after China, and with the new facility becoming operational, the company will be looking towards reducing its dependence on China. It employs over 3,000 people in the country and remains committed towards India for the long term.
The new plant will initially be meeting the demand of Indian customers of the company, which is striving for higher localization of components to provide competitive pricing and good aftermarket support. But, while doing so, ZF has made it pretty clear that it won’t compromise on global quality standards. The facility was set up at an outlay of Rs. 150 crores.
Initially, the facility will begin with manufacturing transmission and clutch systems for various companies, in addition to chassis components for passenger as well as commercial vehicles. Mahindra and Ford are the initial customers for the clutch systems.
The areas the plant will be catering to are off-highway, windpower and marine. Employing about 200 persons, this is ZF’s eight plant in India. The group’s local presence is spread across Pune, Pantnagar, Gurgaon, Chennai, Coimbatore and Madurai. The new Chakan facility will be the headquarters of the after-market sales and services, engineering and administration divisions of the company which extends its support for the Centre’s ‘Make-in-India’ campaign and intends producing as much auto components as possible in India. The products would perfectly suit the Indian conditions.
State-of-the-art facility
We recently got a chance to visit the facility and were much impressed with what ZF does to ensure that the best quality products go to the OEMs which, in turn, reach the regular customers.
The factory visit started with the quality lab, where we were shown how the company strictly checks the quality of the parts received and those dispatched. Both 3-D modelling and 2-D are being adopted to fully analyze the quality and standard of components.
We were then taken to the division where chassis, clutch and transmission systems are manufactured. It was made clear that the factory doesn’t make any of the parts required for manufacturing these auto components but instead outsources them in view of the fact that it there are no adequate volumes to consider production of parts in-house.
The production line for the well-known ZF 9-speed transmission system came next. It was explained by the company technicians how the system of its packaging is done before being sent to the delivery area as a part of finished goods. But the most interesting aspect was the production line for the clutch plate system with a capacity of one million units per annum.
It was further explained how the various parts of the clutch plate system are put together and what goes into actual manufacturing. The clutch plate system passes through different automated stages before getting finally packed. Here, achieving the right balance of the metallic components is of utmost importance. So, just in case any of the clutch plate misses on the exact weight, it would be set right with the use of rivets, resulting in the right weight balance.
The company’s training centre is well equipped for development of technical skills of its employees and partners. The facility has different areas for both theoretical and practical training and also has a test bench, similar to the one in Bangalore, which is used to address the complaints from OEMs, dealers and customers. Further, the sophisticated system of manufacturing components is to ensure that only authorised dealers can attend to their repairs and maintenance.
Further, a team of professionals is always present within the facility to train dealers and employees of other OEMs for better use of ZF auto components.
The last leg of the tour was a visit to the packaging division where different parts are packed in accordance with the branding standards before being sent out of the factory.
It was further learnt that ZF is operating three shifts at the facility and is currently utilising two-thirds of the total area available. Thus, there is adequate scope for further expansion at a later date.