New plant coming up in Pune
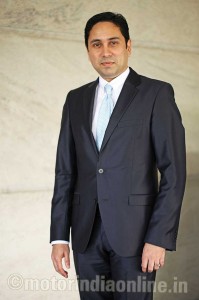
ZF Friedrichshafen AG, leading automotive supplier of driveline and chassis technology, is ramping up its commitment in India with the construction of a new plant in Pune. The location which is already under construction will unite the company’s Car Powertrain and Commercial Vehicle Technology business units as well as ZF Services in India under a single roof. Additionally, it will be home to the headquarters of the engineering and administration of ZF India Pvt. Ltd.
Earlier this year, the construction of the new building, on a plot size of 85,000 square meters (21 acres), started in the Chakan industrial park, roughly 20 kilometers north of Pune. After completion, scheduled for the turn of the year 2014/2015, approximately 350 employees will work at the location. ZF is investing nearly Euro 20 million (Rs. 150 crore) in the new facility. “For 30 years ZF has been present in the Indian market,” says Mr. Rudi von Meister, ZF’s President of Asia-Pacific. “In the years to come, we still see considerable potential in the Indian automotive industry. India will contribute to the growth of the ZF Group which will be strongly driven by the Region of Asia-Pacific.”
In accordance with the local-for-local concept, ZF wants to provide its customers with products from local production wherever possible. Equally, design-to-market considerations play an important role in this regard. Therefore, the ZF engineers from the R&D center in Pune will also be located in the new building in order to develop products specifically for the requirements of the Indian market.
For Mr. Piyush Munot, Managing Director, ZF India Pvt. Ltd., responsible for ZF Group operations in India, the new internal business park represents an excellent expansion of the company’s existing capacities in Pune. Says Mr. Munot: “In 2015, ZF will be completing 100 years of existence and a milestone for our Indian operations will be the integration of our commercial vehicle, passenger car and aftermarket operations under one roof at our new facility which we call the ‘ZF Business Park’. The new plant is a good starting point for further expansion of our business in India and is a clear commitment of the ZF Group to the Indian market and its future prospects.”
Focus on Asia Pacific
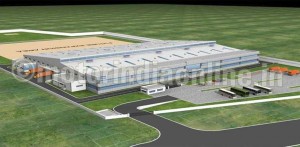
After North America, the region of Asia-Pacific is the largest international market for ZF Friedrichshafen AG. In 2013, the technology company generated sales of Euro 3 billion in the region. ZF employed around 7,500 employees at 36 production locations and 61 authorized service partners in the fast-growing region in 2013. One success factor in this respect is the early local presence as well as the close links between manufacturing operations and sales & service activities.
For instance, ZF has been operating businesses in India since 1984 and today produces directly for the local market in ten plants. “ZF has first-hand knowledge of the Indian market stretching back 30 years and is represented there with all divisions,” explains Dr. Stefan Sommer, CEO, ZF Friedrichshafen AG. “India’s strong population and economic growth calls for massive infrastructure expansion. Despite the not entirely easy situation at present, the Indian economy will continue to grow over the long term. We are well prepared for that.”
Pune is an excellent example of ZF’s long-term success in India. ZF has been producing – initially through a stake in a joint venture – at the location since 1984. After 2007, the Group continued to expand its involvement and production capacities in the growing metropolitan region and now has a new plant coming up in the region. Also the ZF Lenksysteme GmbH, a joint venture between ZF and Bosch, manufactures products for the local market in Pune.
After China, India is the second-largest sales market in the region of Asia-Pacific. For 30 years, the technology company has been operating a growing number of locations in this market region, which since then has become increasingly important and is today the most important international market for ZF after Europe and North America. In 2013, the Group invested nearly 84 million Euro in the Asia-Pacific region. Since March 2014, ZF is reinforcing its business in Asia-Pacific. In Shanghai, Mr. Rudi von Meister took over responsibility for the fast-growing international market in his role as ZF President Asia-Pacific.
System solutions
Mobility and driving pleasure can be combined with reduced fuel consumption, resource conservation, and additionally enhanced safety thanks to ZF technology. The technology company supplies driveline, chassis, and steering technology for all types of passenger cars and commercial vehicles worldwide. ZF components in the driveline and chassis – from clutches through control arms to shocks & dampers – constitute a mainstay in this respect. ZF is also established as an important systems supplier in many markets and assumes, for instance, responsibility for complete axle systems for its customers. In future, this systems expertise will be key to the Group’s success. After all, it is a decisive element in important future topics such as driveline electrification and automotive lightweight construction.
The provision of tried-and-trusted automotive technology in line with market requirements and at attractive costs – that remains a critical success factor for multinational supplier groups like ZF. Today, many automakers and commercial vehicle manufacturers worldwide turn to suppliers for suspension components or standard driveline technology. In this respect, they opt for suppliers in the particular country that are already working with them in other market regions so that they can rely on the quality and manufacturing expertise in the respective product group.
In addition to contracts for components, ZF is safeguarding its global market position with its systems business and is positioning itself as technological leader. In driveline technology, ZF’s portfolio comprises manual and automatic transmissions including clutch systems and torque converters for every vehicle segment. Added to which are dual clutch transmissions and modules for passenger cars. ZF’s driveline product range includes in particular dual-mass flywheels and axle drives, rear-axle differentials, and the commercial vehicle transmission brake known as Intarder.
When it comes to chassis technology, ZF offers complete axle systems for passenger cars and commercial vehicles including low-floor technology for buses. ZF also provides active and semi-active systems, which have become more and more prominent on the passenger car market in recent years. These adaptive damping systems including their control software and electronics enable driving dynamics and ride comfort to be increased in equal measure since the chassis damping can be adjusted in real time to the particular driving situation down to the level of individual wheel. The ZF system is only used on the rear axles of subcompact cars or vans in the CDC 1XL (i.e. one axle) version.
Ecomid
ZF launched the ZF-Ecomid manual commercial vehicle transmission in 1985 and has revised it several times since then several. The current version with nine gears is designed for medium-duty and heavy trucks with a torque range of 1,100 to 1,300 newton meters. The transmission has a particularly strong starting gear, the crawler, which enables fuel-saving and cost-effective driving. Optimum power transmission, short shift travel, a high level of operating smoothness, and the low curb weight of the ZF-Ecomid convince fleet owners and drivers worldwide. Additional functions like the pneumatic Servoshift shift support and the Intarder transmission brake, which can be integrated as an option, increase safety and operating comfort. Combined with a wide variety of PTOs, the Ecomid can tackle any task. This functional diversity and the fact that Ecomid works reliably, in a fuel-saving manner, and mostly without any need for maintenance are the reasons for the continuous worldwide success of the transmission.
The worldwide success of the ZF-Ecomid manual commercial vehicle transmission is proven by a number: So far, ZF has produced about 750,000 transmission systems of this type at its production locations in France (Bouthéon), India (Pune), Brazil (Sorocaba), and Russia (Naberezhnye Chelny).
AS Tronic
With the AS Tronic automatic transmission family, ZF covers a broad application range in the commercial vehicle sector. The AS Tronic for heavy trucks as well as the AS Tronic mid and lite for medium and light delivery vehicles are easy to handle, safe, and particularly economical. The same applies to the eTronic from ZF, an automatic transmission for vans, and the TC Tronic, which makes maneuvering with heavy goods vehicles of up to 250 tons significantly easier.
For manufacturers like Iveco, DAF, or MAN, Renault, and Volvo, the AS Tronic transmission range is the first choice for automatic shifting in commercial vehicles. Its advantages: easy handling, safety, and fuel savings. While the bigger members of the transmission family, like AS Tronic and TC Tronic, are suited for heavy trucks and construction vehicles, the AS Tronic lite and the AS Tronic mid relieves drivers of doing the shifting for smaller delivery trucks and medium-duty commercial vehicles. Vans are best equipped with the eTronic from ZF.
Ecolife
The formerly separated competence areas of bus driveline technology and bus axle systems have now been merged by ZF into a new business unit. This is also to the benefit of customers worldwide since they get key technologies for an efficient and comfortable bus operation from a single source now. This refers, amongst other things, to the EcoLife 6-speed automatic transmission that guarantees high driving and riding comfort for city buses with their frequent starting and stopping operations and keeps the engine speed at a low level at the same time – with a positive effect on fuel consumption and noise emissions. By means of the current low-floor technology by ZF, city buses can be operated in a particular cost-efficient and flexible way. For also enabling this in the future, ZF has already developed new bus axle system generations.
The EcoLife transmission from ZF makes public transport not only more fuel efficient but also quieter: The engine speed can be kept low thanks to the intelligent design, six fine-stepped gears, and the TopoDyn Life shift program. When setting off, a maximum speed reduction of about 700 revolutions per minute is possible compared to traditional automatic transmissions. Lower speeds mean lower engine noise emissions from which not only people living near bus stations or passers-by profit, but also passengers. In particular in the rear seats it is getting quite noisy at high engine speeds.
With regard to fuel efficiency, the ZF-EcoLife has set benchmarks since its market launch: Compared to the Ecomat predecessor transmission, ZF-EcoLife consumes ten percent less fuel due to the TopoDyn Life topography-dependent control software; the EcoLife hybrid version consumes even 25 percent less. Many technical details contribute to reducing fuel consumption, like for instance the demand-driven control of the hydraulic pump. It only provides full pump output if the bus is driven with full throttle. The control software does not only switch the transmission into neutral when standing still at a bus stop, but does that already when approaching it and when the speed is lower than 12 km/h. Like this, it is avoided in an early stage that engine and brake counteract with a negative effect on fuel consumption.
Off-road segment
The demands on small, self-propelled off-road vehicles are continually increasing. This is particularly true in inner-city areas were modern vehicles must in future be more mobile and maneuverable. This trend is also expected to continue with backhoe loaders. ZF offers a system for backhoe loaders consisting of a steerable driven front axle, the compact driven rear axle and a synchronized four-gear or power shift transmission. ZF’s WG-90 transmission, MULTISTEER MS-B 3000 and ZF MULTITRAC MT-B 3000 offer a comprehensive solution package for customers in the off-road segment.
ZF recently hosted a ‘Ride and Drive’ event at Pune to showcase its versatile range of solutions and unmatched technology capabiltiies across passenger car, commercial vehicle and construction equipment segments. The event included presentations on the company’s technologies by its experts along with a hands-on experience to highlight how ZF enhances the quality and comfort of vehicles. The occasion also presented an opportunity for the media to interact with the ZF team including Mr. Rudi Von Meister, Mr. Piyush Munot and Mr. Mandeep Bhalla among others, who were ready to respond to queries and clarifications on the technical front.
Rudi von Meister shares his views on how important the Indian market is for ZF
First of all, ZF has grown up, matured and become very successful in the European market which continues to be our cultural and technological home. We are definitely interested and need to diversify away from our focus on Europe and this has been in process for a number of years. The company, recognizing that Asia is going to be a sustained opportunity for growth over the foreseeable future, has placed great expectations on the region and on our activities here.
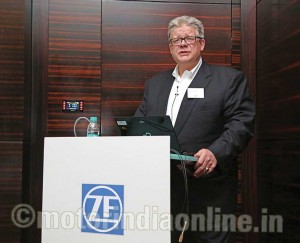
We have nearly 80 per cent of our business in Asia coming from China. So, the immediate observation is ‘shouldn’t we diversify?’ That is really what we are trying to do – balance, diversify away from Europe into other markets, inch away from China when it comes to Asia.
China is certainly our key market in Asia but we need other key markets and that is where the role of India comes in. The emerging powerhouses in the automotive industry over the next several decades will come from this country (India) and from China, more likely than anywhere else.
With our experience, we are now in a position to learn to do our business differently. Instead of being a traditional supplier of a component whose parameters and specifications are defined by our customers, we may be in a position to play more of a collaborative role. If we do that, and do it effectively, we should see significant growth in our business here (in India), but it requires an upfront investment and we need to be here. Yes we are here, but we need to be ‘more here’ and in a way that creates the umbrella that ties our different divisions together more effectively so that we can produce systems solutions rather than just component solutions. It is good for us and also good for our customers who manufacture vehicles indigenously.
To be successful in a market like India, we are working on training ourselves to be a more collaborative systems supplier. Another important focus area for us is to ’design-for-market’ and ‘develop-for-market’, ‘in market’, which is why we are enhancing our technological presence in the country.
ZF Lenksysteme develops new commercial vehicle steering system for the Indian market
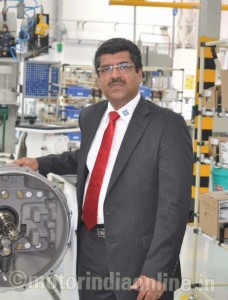
ZF Lenksysteme (ZFLS) has been the international market leader in the field of commercial vehicle steering systems for decades. The company develops and produces hydraulic and electrohydraulic steering systems for commercial vehicles as well as steering pumps and accessories. The ZF-Servocom® has been the benchmark in the field of ball-and-nut power steering systems for commercial vehicles for decades.
Due to the particular road conditions and logistics requirements, growth markets such as India place different requirements on commercial vehicles and their steering systems from markets in Europe or North America. Indian customers, for instance, are looking for lower costs and basic functions only. For this reason, ZF Lenksysteme has developed a variant of the ball-and-nut power steering system specifically for this market as part of collaboration between Corporate Headquarters in Germany and experts in India. Thanks to its weight-optimized modular design, the ZF-Servocom® 8007 has an improved power-to-weight ratio compared with the local competition, which translates into an increased payload for manufacturers and forwarding companies.
No compromises were made in terms of ruggedness, with key components designed to be larger than the local competition. The system is maintenance-free, requires less installation space, and offers the manufacturer the possibility of increasing ride comfort. The Servocom for the Indian market will be available in three model sizes: Servocom 8007 up to 6.5 tons steering axle load, Servocom 8006 up to 5.3 t steering axle load, and Servocom 8005 up to 3.2 t steering axle load.
The new steering model range will be produced from 2015 with approximately 80 per cent locally manufactured parts in the ZFLS plant in Pune which was opened in 2012. Says Mr. Mandeep Bhalla, CEO, ZF Lenksysteme India Pvt. Ltd.: “The Indian market deserves futuristic products and the idea of having a technology from Europe is exciting. But in India, the value-for-money proposition is important and it matters a lot to be cost-effective. We have tried to combine the strengths of our global technology with the capabilities of local suppliers and this has made these products evolve as products of India.”
ZFLS India Pvt. Ltd., the company’s Indian subsidiary, has some of the biggest auto manufacturers in the country like Tata Motors, Volvo-Eicher Commercial vehicles, Ashok Leyland, Volvo India, Daimler India Commercial Vehicles Ltd. and Force Motors, among others, as its customers. By 2018, ZF Lenksysteme India is targeting sales of around 100,000 steering systems annually, with nearly 20 per cent share of the total market.